Особенности современных вызовов
В автоматизированных системах управления упрощённо различают системы комплексной автоматизации производства любых масштабов (роботизированный комплекс), конвейерные автоматизированные линии сборки (в том числе розлива) и управление бизнес-процессами BPN. С учётом некогда отлаженных связей с зарубежными поставщиками мы имеем технологический и научный фундамент для прорывного скачка в развитии отечественной электроники. Если об опережении уровня стран с ведущими экономиками мира в сложной ситуации говорить неуместно, то в ряде сфер, включая радиоэлектронику и, в частности, радиационно-стойкий её сектор, производство некоторых материалов, химическую, металлургическую промышленность, военпром, куда направлено достойное государственное обеспечение, и, конечно же, бытовой промышленный сектор, включая лёгкую и пищевую промышленность, – в этих (и других) сферах российские производители и предприятия конкурентоспособны. Всё это позволяет замещать прежних партнёров новыми, «держать удар санкций» и перспективно работать в области «параллельной» электронной индустрии с использованием инновационных материалов, таких как Si, SiC, GaN (и др.), создавая собственные производственные линии и модули для замены линий, ранее поставленных из-за рубежа. Автоматизация производственных процессов идёт рядом с развитием робототехники. По сути, эти понятия во многом аналогичны. На российском рынке роботизированной автоматизации процессов насчитывается два десятка вендоров. Среди них уже значительно выделяются несколько компаний. В ближайшие 3–4 года рынок консолидируется и получит крупных российских вендоров, уверенно развивающихся в фазе масштабирования.Автоматизация бизнес-процессов, ПО и документооборота, или Робот в ящике
Что касается автоматизации бизнес-процессов и в целом роботизации, после условного спада 2022 года эти сегменты на российском рынке зависят от быстрого заместительного импорта, в том числе параллельного, и роста сотрудничества с КНР. Чем быстрее появятся значительные результаты взаимодействия, тем скорее состоится замена прежних RPA-решений (Robotic process automation – технологии, сочетающие использование программных роботов и машинный интеллект) с оптимизацией под требуемую инфраструктуру. Если изначально среди потребителей программных роботов числились предприятия банковской сферы, теперь роботизацией активно занимаются крупные промышленные холдинги, нефтеперерабатывающие компании, военная промышленность и структуры государственного сектора управления – все они вовлечены в роботизацию процессов. Один из примеров – платформа Robin RPA, масштабируемая внутри организаций и холдингов, поддерживающая кластеры и массовое развёртывание роботизации производства. Robin RPA характеризуется условно двумя режимами разработки роботов: No-Code и Low-code. Уникальный No-Code позволяет создавать элементы, модули и в целом электронных роботов из «конструкторов», без системного программирования, а потому такая система доступна, легко адаптируется на производстве и перспективна для отечественных специалистов-разработчиков в области автоматизации [3]. Сия модульная система устойчива, так как модули можно заменять, а их производство осуществлять на территории России, что даёт дополнительную экономическую и техническую безопасность. То же касается инструментальных и программных приложений на любом языке программирования – Java, Python или NET Framework с библиотеками приложений. Так создаётся «цифровой сотрудник» – программный робот, решающий многие задачи не хуже человека, не подверженный при этом пресловутому «человеческому фактору». В рейтинге российских платформ CNews роботизация при помощи ROBIN RPA выигрывает премию Global CIO – развивающееся направление c облачной фабрикой программных роботов по автоматизации процессов для «РЖД-Технологии» [4].С замещением деятельности человека-сотрудника роботом в сфере логическо-производственных задач открылись перспективы организованного электронного документооборота. Налицо не робот как таковой с типичными представлениями о нём – металлический каркас, человекоподобная голова, «стреляющая» яркими световыми вспышками – индикаторами решений ИИ… По сути, робот – это «ящик» с электронной начинкой, умеющий обрабатывать большие массивы данных по заданной программе, и этим зачастую заменяющий целый отдел из 10–20 сотрудников, с той разницей, что робот не ошибается и не отвлекается на перекур и кофе-брейк. Именно тот «состав» попытки «взятия власти» самообучаемой электронной системой, против которого поднялась волна (Илон Маск и др.) аргументированного протеста, чтобы искусственный интеллект (ИИ) не подчинил себе все сферы жизни бесконтрольно для человека. Но пока до этого не дошло, мы можем дискутировать и вырабатывать новые решения, анализировать уже существующие. Если говорить о рынке роботизированной автоматизации процессов в целом, то все вендоры (в разных странах) в 2021–2022 гг. показали рост уверенными темпами. В среднем сегмент RPA прибавляет в качестве инноваций и развитии по 40% в год [4].
Рисковый фактор в том, что пусть RPA универсальная и в принципе привлекательная для разработчиков технология, однако в этой связи надо понимать и опыт, и перспективу: как с любым делом с претензией на инновацию, ИИ и роботы обывателям кажутся выгодными, и вложения в отрасль уже напоминают «звёздный дождь» инвесторов. Но выигрывают всегда только первые. Правильные предсказания на основе «умной» аналитики, всё то, что приписывают, к примеру, ChatGPT, напоминают «магов» на скачках. Допустим, условно, что аналитика и возможности роботов будут доступны. Инструмент ИИ у многих будет только один, и результат будет – один на всех. Тогда, используя «секрет Полишинеля», люди захотят выиграть и поставят, говоря аллегорией, на одну «призовую лошадь», и она придёт первой; без изменений фонда условно выиграют все, но чуть-чуть. Вот здесь и «собака порылась»: перспективно использует возможности ИИ и соберёт дивиденды тот (или группа лиц, компаний), кто проведёт собственную аналитику на основе данных робота-помощника с ИИ и поставит на перспективную, но неизвестную «тёмную лошадку». Потому что робот с ИИ не ищет лазейки и ошибки, а всего лишь анализирует большой поток данных. Пока реально так. «Выключать» свои человеческие мозги, полагаясь только на робота, право, ещё рано, до тех пор пока искусственный разум научится не только анализировать имеющиеся массивы, по которым самообучен, но ещё и творить новое, не на основе старого, а именно инновации. Вот тогда действительно наступит другая интеллектуальная эра, и опасность приблизится к людям. А пока – жить ещё можно...
Особенности и тренды автоматизации современного производства
Обращая внимание на сектор автоматизации производства, необходимо отметить его особенности на примере действующих конвейерных линий.В ближайшие годы, когда время холдингов – производств «всего», от заклёпки до локомотива, подошло к концу, перед отечественной промышленностью актуализируются несколько связанных между собой вызовов.
- Встраивание конкурентного произ-водства в глобальные цепочки поста-вок и развития рынка – без высокотехнологичных автоматизированных линий не обойтись.
- Уже определилась тенденция потребности в персонализированной, «заказной» продукции, собранной под потребителя – от цвета до формы и функциональности. Для этого нужно мелкосерийное адаптированное и быстро настраиваемое производство: обратим внимание на китайскую промышленность – она работает именно по такому принципу и снабжает… весь мир. Один и тот же небольшой завод относительно быстро может изменить ассортимент – от кастрюли до условно танкового прицела ночного видения. И это совсем не аналог условной ручной сборки автомобилей в Швеции (Volvo) и Финляндии (Sisu) во второй половине ХХ века.
- Ещё один тренд – оптимизация и сокращение сотрудников при нехватке квалифицированного персонала. В психологическом плане современный человек всё больше желает блистать и влиять, он уже был рабом потребления, а теперь его интересует не столько гедонизм общества, сколько культура особо ориентированного потребления, консюмеризм. Пока большие неповоротливые производства перестраиваются, малые предприятия с автоматизированными линиями завоюют свою рыночную нишу. Сотрудникам захочется проявить элементы компартментализации – повышать уровень образования в соответствии со своими целями и участвовать в миссии производства, а не просто обслуживать конвейер. Таким образом, меняется не только производственная сфера, но и человек – главный потребитель всего, формирующий в современной повестке социальный запрос на экологичное и рациональное, социально-ориентированное производство. Такие компании будут популярны.
Автоматизированные линии розлива для производственных процессов
Среди автоматизированных произ-водственных линий в разных сферах можно встретить решения разных производителей. Линия ЛР-5-1000 производства ЗАО «Кропоткинский завод МиССП» предназначается для автома-тического розлива растительного масла, питьевой или минеральной негазированной воды, технических фильтрованных жидкостей неядовитых, неагрессивных по отношению к контактирующим с ними материалам в бутылки объёмом 3–5 литров, автоматического укупоривания бутылок пластмассовыми резьбовыми или забивными пробками и наклеивания самоклеящейся этикетки. В линии ЛР-5-1000 применяется пневматическое оборудование фирм «Festo» или «Camozzi», электронные контроллеры приводы фирмы «Omron». Линия настраивается под определённые типоразмеры бутылок, пробок и этикеток. На рис. 1 представлена потоковая автоматизированная линия ЛР-5-1000 в действии.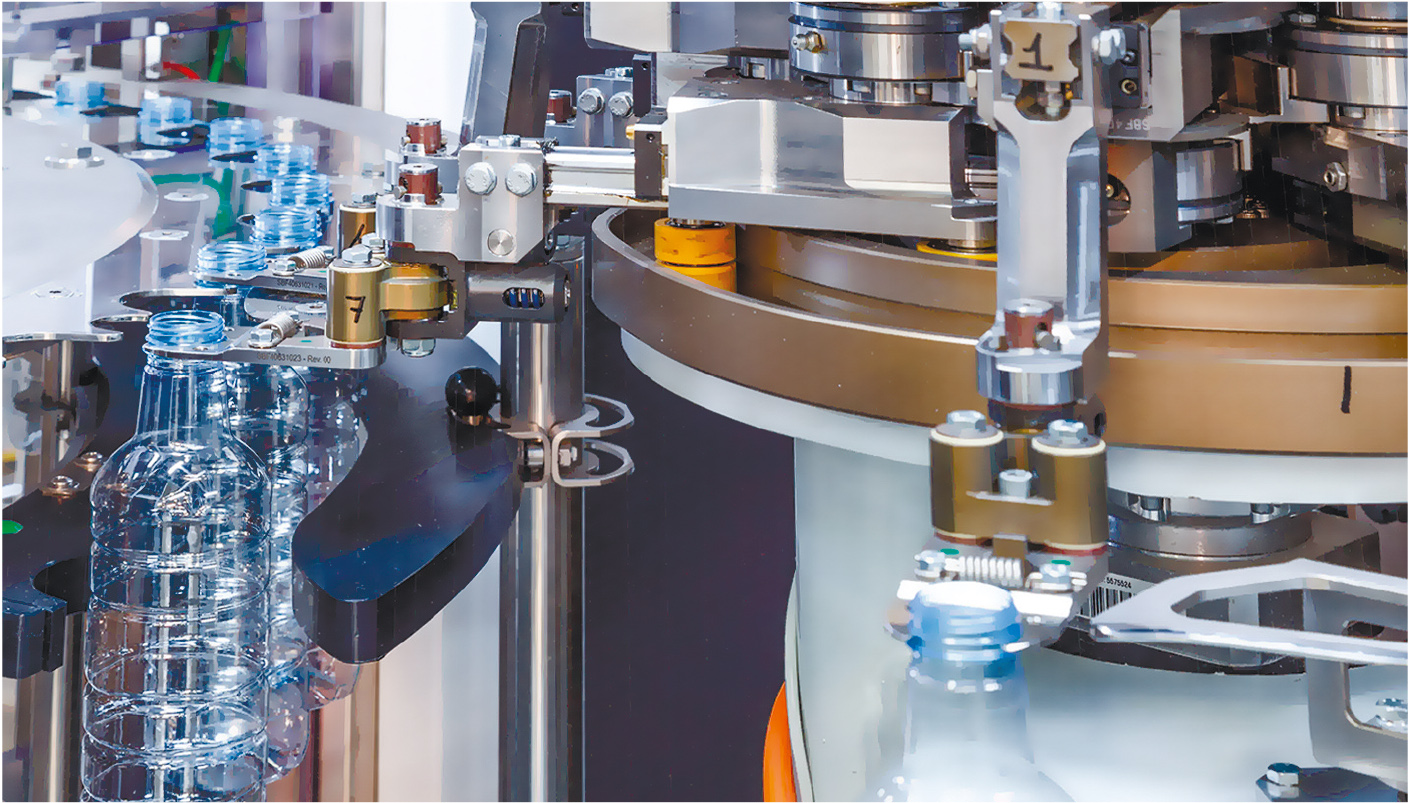
На рис. 2 представлен вид пневматического блока с электронным управлением для крышек ПЭТ (полиэтиленовой тары) линии ЛР-5-1000.
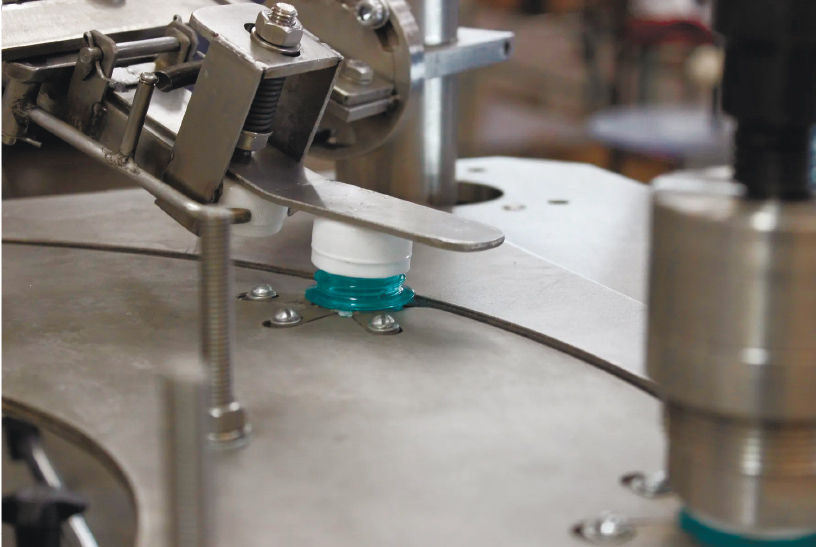
Некоторые технические характеристики ЛР-5-1000:
- максимальная производительность 1200 бутылок в час;
- мин/макс объём тары – 3/5 литров;
- диаметр бутылки 120…160 мм;
- высота бутылки 300…380 мм;
- точность дозирования ±1%;
- давление напитка на входе 0,01…0,1 МПа;
- рабочее давление сжатого воздуха 0,6…1 МПа;
- напряжение питания 380 В, трёхфазная электрическая сеть.
На рис. 3 представлен элемент ЛР-5-2, тоже Кропоткинского завода. Это оборудование по сравнению с высокоскоростными АЛР напоминает анахронизм эпохи – много металла и крупных элементов в отсутствие условно точных деталей и контрольных датчиков.
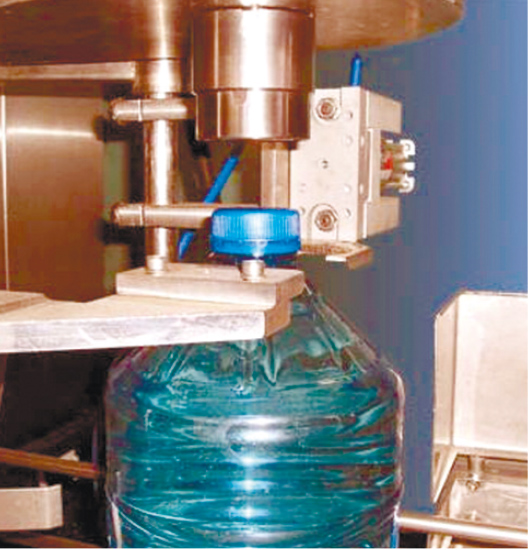
Практические примеры автоматизации производства
Особый сегмент автоматизации производства – линии розлива. В принципе, они могут работать с жидкими или вязкими продуктами (кремы, соусы и джемы), в том числе содержащими твёрдые частицы – как йогурты с печеньем. Автоматические линии объёмного наполнения (АЛОН или АЛР) оснащены пневматическими клапанами, обеспечивающими точную и постоянную производительность. На рис. 4 представлен схематичный вид универсальной линии розлива жидких и вязких неагрессивных продуктов в тару.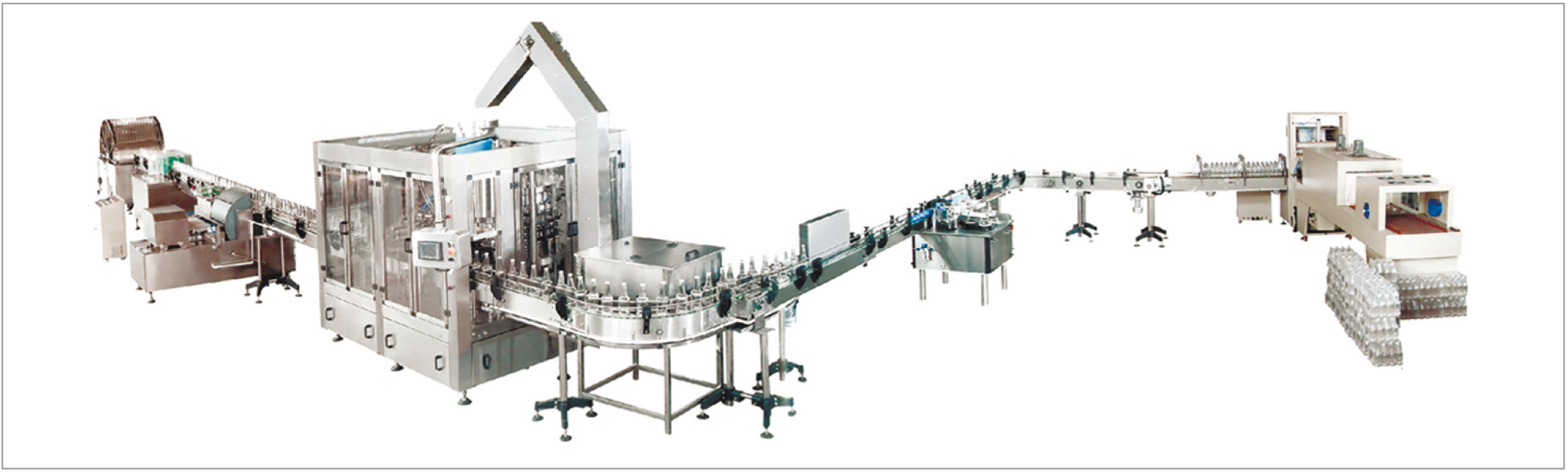
Дозирование выполняется благодаря управляющему ПО, разработанному в России и настраиваемому на местах, в том числе для одновременного заполнения больших резервуаров с различными параметрами. Автоматические линии розлива оснащаются автоматическим циклом мойки, укупорки, этикетировки и маркировки с централизованным управлением с сенсорной панели управления. АЛР предназначены для компаний, работающих в отраслях пищевой промышленности, косметической индустрии, фармацевтической и химической индустрии. Как правило, производители АЛР учитывают специфические требования заказчика. В электронных системах с пневмоприводами для автоматизированного розлива жидкостей в тару используется прецизионные электронные устройства и контроллеры для точного управления объёмом наполнения в зависимости от расхода продукта. На рис. 5 представлен вид ЛРС-6-150.
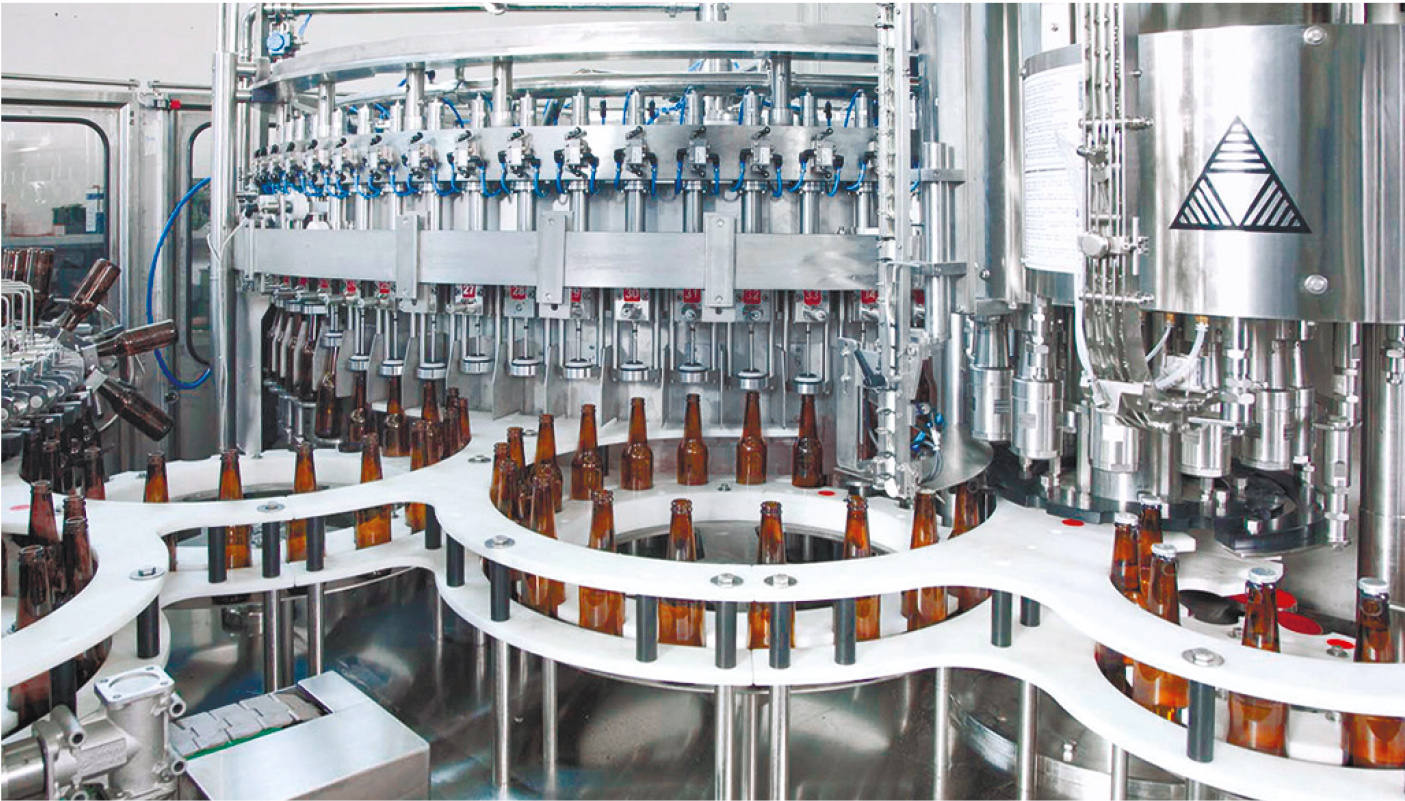
Ключевые преимущества автоматизированного оборудования для розлива:
- условно простой монтаж установки исключает необходимость в дорого-стоящих сменных деталях;
- эргономичный дизайн обеспечивает доступ для быстрого переключения и очистки;
- настройка параметров дозирования выполняется на многофункциональном сенсорном дисплее;
- подходит для работы с тарой разных форм и размеров;
- не требует высококвалифицированных операторов (кроме наладчиков), а потому проста в использовании и обслуживании.
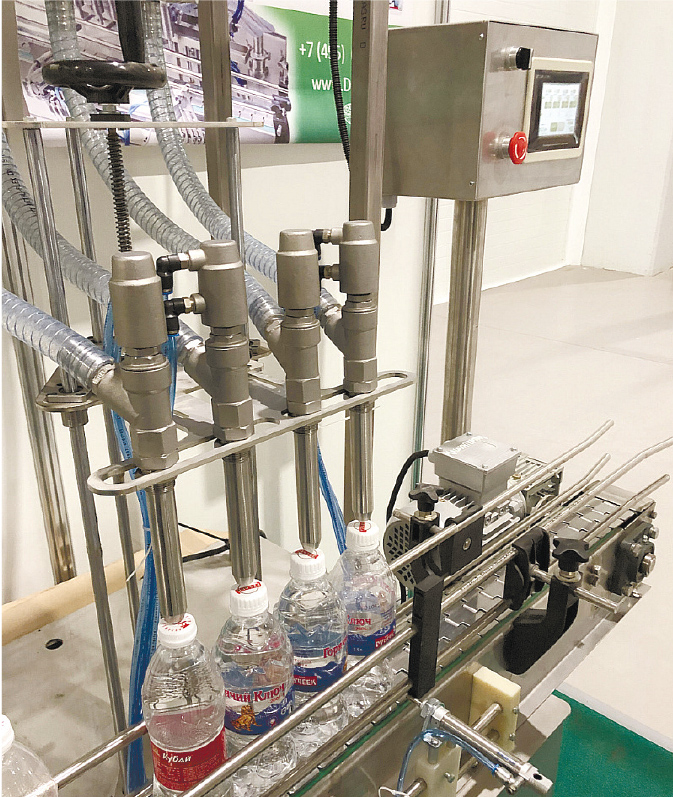
Технические характеристики:
- количество головок: 4;
- объёмы дозирования: 100…1300 мл;
- скорость розлива: до 25 бутылок/банок в минуту;
- точность заполнения: ±0,5%.
Элементы оборудования, контактирующие с разливаемым продуктом, изготовлены из нержавеющей стали. Состав автоматической линии розлива: узел подачи тары и накопления тары состоит из нержавеющего стола или комплексной установки – «позиционер». Подача тары на конвейер для розлива может производиться как оператором-контролёром вручную (в устаревших линиях), так и полностью в автоматическом режиме (современное оборудование). Затем тара поступает к узлу наполнения, состоящему из 4-канального перистальтического дозатора, системы опускания патрубков для наполнения тары. Подача продукта к узлу наполнения осуществляется по силиконовым армированным шлангам.
В современной АЛР многоканальный розлив во флаконы, пробирки, пузырьки и неустойчивую тару невозможен без настройки и функционального информативного дисплея с сенсорным управлением. Вид автоматизированного рабочего места для выбора режима дозированного розлива жидкостей с производительностью от 1500 до 3000 флаконов в час представлен на рис. 7.
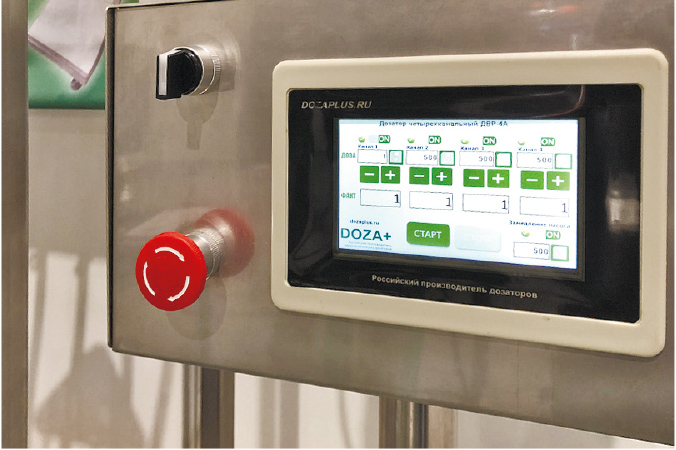
Автоматический 4-канальный асептический дозатор, внешний вид которого представлен на рис. 8, применяют в АЛР небольшого форм-фактора тары и производительности; модуль розлива, который может использоваться самостоятельно или входить в состав линии розлива.
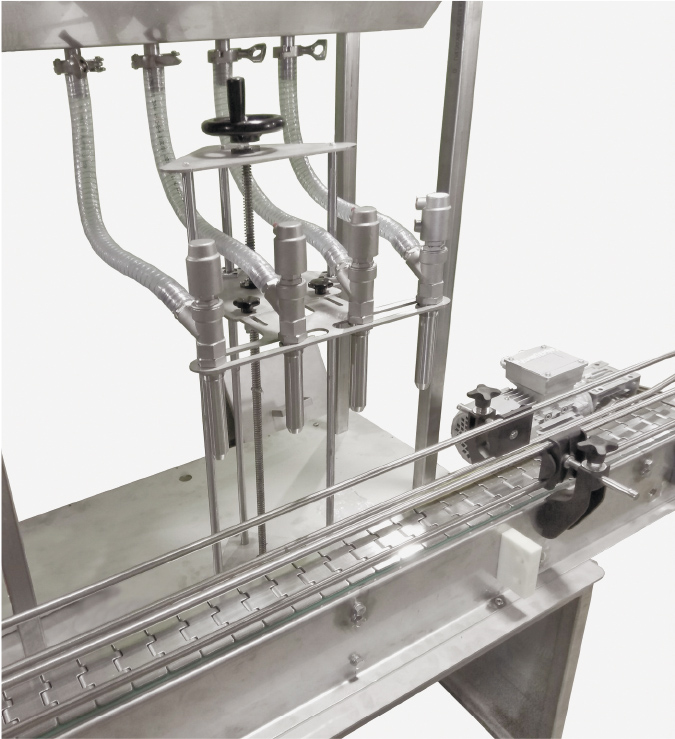
Автоматический 4-канальный настольный асептический дозатор представляет собой модуль под электронно-пневматическим управлением с диапазоном дозированного розлива 10…1000 мл на каждый канал. Настольный, полностью автоматический дозатор эффективен при розливе средних доз с высокой производительностью. Он широко используется в медицине, фармации, пищевой, химической и других отраслях.
Установка для автоматизированного розлива жидкостей использует прецизионное электронное управление для точного управления объёмом наполнения в зависимости от расхода продукта. Эргономичный дизайн обеспечивает лёгкий доступ для быстрого переключения и очистки. Настройка параметров дозирования выполняется на сенсорном экране.
Автоматический дозатор может работать как отдельное устройство, так и в составе линии розлива. Дозатор позволяет фасовать жидкие, пастообразные, в том числе пенящиеся продукты дозами от 50 до 3000 мл. Процесс дозирования и укупорки происходит в автоматическом режиме. Подача тары на наполнение осуществляется с помощью подающего конвейера. Съём расфасованной продукции осуществляется в автоматическом режиме в приёмный бункер с производительностью 1000…3000 бутылок/час, в зависимости от количества дозирующих модулей. Ротационный укупор для пластиковой и стеклянной тары с резьбой представляет собой мультиголовочный пневмопривод для установки крышек и распылителей на флаконы, бутылки и иную тару после розлива, с гарантией герметичного уплотнения тары и целостности продукции. Другое совместимое оборудование – автоматический укупор на пробки от 15 до 70 мм может работать как отдельно, так и в составе автоматизированной линии.
Для производственных условий в фармакологии применяется автоматическая линия розлива, укупорки и этикетировки во флаконы и пузырьки диаметром 20–500 мл. К этому сегменту оборудования предъявляют требования повышенной санитарной чистоты, безопасности, связанной со стеклянной тарой и отсутствием сколов при фасовке, а также экологичности. Автоматическая линия АЛ-4 розлива и укупорки ПЭТ пузырьков предназначена для дозирования удобрений, средств от комаров, прикормок для растений, инсектицидов, фунгицидов, гербицидов, «прилипателей» и «растекателей». Конструктивные элементы оборудования, соприкасающиеся с продуктом, выполнены из нержавеющей стали и силикона. Автоматический этикетировщик для круглой тары модели YTK-150 позволяет работать с заготовками и образцами диаметром 10…550 мм. Для розлива и фасовки жидкостей и паст на производстве применяют перистальтические и многоканальные, в том числе поршневые дозаторы ЮНАП и CRpump, весовые дозаторы жидкостей, OEM-перистальтические насосы, рабочие головки, расходники и комплектующие. Надёжность автоматических линий и её основные показатели описаны в [2].
Автоматизация малых форм розлива
Есть примеры малого форм-фактора, определяющие перспективное развитие розничной продажи напитков с автоматическим розливом. Таков условно новый формат продаж разливного пива – вендинговые автоматы (beerboks, бирбоксы) c автоматической системой SmartTap (умный кран), появившиеся с 2020 года в торговых сетях в Москве, Ростове-на-Дону, Санкт-Петербурге, Анапе, Геленджике и Сочи, а также в локальных торговых сетях других городов. Это миниатюрные линии розлива, прообразом которых когда-то в ХХ веке были автоматы газированной воды. Главное преимущество автоматических «раздатчиков» в том, что они управляемы, безупречны с санитарной стороны и безопасны, работают по установленному ПО алгоритму, и в принципе лишены участия пресловутого человеческого фактора; тут соки, воды или пиво не разбавят, со сдачей не обманут, даже если вы утеряли контроль в качественном арифметическом счёте, и ещё автомат не умеет… хамить. Недолив, как и перелив, исключён, поскольку все функциональные процессы контролируются современной электроникой. Программирование позволяет настроить таймер работы бирбокса для соответствия разрешённому времени продажи тех или иных напитков.Самое простое решение для мониторинга пролива в любых (больших и малых – розничных) точках продаж состоит из электронного счётчика потока Digmesa и контроллера с АЦП для сбора данных модели BC-30. Подходит для вендиговых аппаратов (бирбоксов), кафе и баров. Счётчик потока представлен на рис. 9.
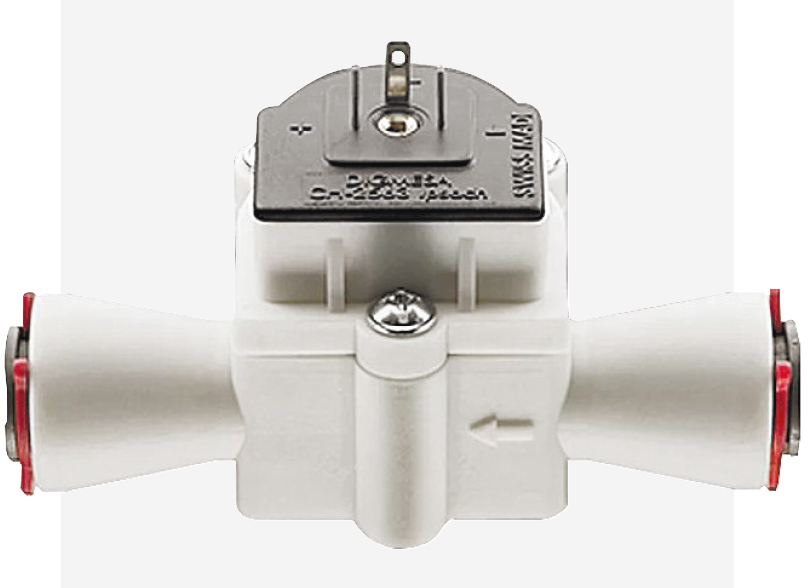
Встроенный принтер этикеток дополняет конструкцию, расширяя её возможности: таким образом можно выбирать под конкретную задачу – расплачиваться ли банковской картой, кэшем с помощью электронного купюроприёмника или предъявлять тару с наклеенным штрих-кодом при выходе из торгового центра – на кассе. Штрих-код на липкой основе содержит RFID-метку для исключения несанкционированного выноса неоплаченного продукта (кражи в формате набирающего популярность шоплифтинга). Бирбоксы снабжены системой регулируемого охлаждения жидкости до +5°С так, чтобы даже «в летний жаркий день “приотдохнуть” от трудов в саду под кронами “тенистых дерев”» с прохладительным напитком в руках, и при этом, согласно Н.В. Гоголю («Мёртвые души»), граждане умилялись и струили «потоки слез в знак признательности [о заботе] к господину градоначальнику». Широкие перспективы такие аппараты открывают во всём спектре напитков. Места под арендуемую площадь требуется мало, энергопотребление не более 60 Вт в активном режиме (как старая лампа накаливания), затраты на регламентные работы, в том числе по очистке, невелики – как и во всем вендинговом бизнесе, и могут быть совмещаемы со сменой расходных частей – непосредственно заменой герметично закрытых на заводе пивных кег или иной подобной тары. В современных бирбоксах можно продавать до четырёх сортов разных напитков. Таким образом, речь идёт об отвечающем современным требованиям и даже перспективам торговом продукте (системе), который в принципе может «не приходить» за зарплатой и не станет выяснять отношения с работодателем при обоснованном увольнении за грехи. Основным критерием выбора покупателя жидкой продукции бирбокса является свежесть, высокий и отслеживаемый маркетингом стандарт качества напитка и сам процесс розлива в формате «здесь и сейчас». Спрос пользователей растёт. По открытой статистике за три года в России установлено более двух тысяч бирбоксов фирмы NPM Group, бóльшая часть – в Москве и др. мегаполисах. Таков показательный пример «малой автоматизации», которая так же пропорционально соотносится к типичной автоматизированной производственной линии розлива, как малая авиация к большой авиации. Пионерами в продвижении в России являются FMCG-компании. Так, пивоваренная компания, являющаяся частью международной корпорации Carlsberg Group, автоматизировала работу 18 линий на территории России с помощью WMS – усовершенствованной маркетинго-логистической цепи системы LEAD. Внедрение электронной WMS повысило скорость упаковки готовой продукции на 43% и позволило стабилизировать работу АЛР без технических ошибок.
В описываемых примерах компании, работающие в России, реализуют не только проекты импортозамещения, а внедряют средства автоматизации и роботизации на основе современных российских разработок. В сложившейся ситуации, связанной с ограничениями по санкциям, стало затруднительно, почти невозможно получить готовые производственные линии из-за рубежа. Речь может идти только о поставках модулями с монтажом на месте, да и это стало затруднительным. Наиболее выигрышное положение (относительно) занимают компании со сложившимся пулом заказчиков и поставщиков оборудования с международными связями, основанными на вхождении в корпорацию или промышленную группу привилегированных акционеров международного состава. К примеру, ПК «Балтика» с корпоративными зарубежными связями условно имеет более выигрышное положение, чем пивоваренный завод в Челябинске. Ещё одна актуальная проблема – поставка ЗИП, модулей и запчастей к производственным линиям. Несмотря на всю позиционируемую разработчиками универсальность электронных и силовых модулей, полной унификации не существует и в этой области, иначе бы все производственные линии были бы похожи, как будто у них один «папа»-производитель.
Пример автоматизации производства на Новочеркасском электродном заводе
Российская компания BFG Group Robo-tics специализируется на комплексной автоматизации производства разных масштабов [1]. АО «ЭПМ – Новочеркасский электродный завод», имеющий собственную инженерно-конструкторскую площадку – один из крупных в России и в Восточной Европе производителей графитированных электродов. Основные потребители продукции – сталелитейные производства, среди которых Челябинский металлургический комбинат, «Красный Октябрь», Магнитогорский металлургический комбинат, Оскольский электрометаллургический завод. Экспортная продукция (до 40%) НЭЗ до введения санкций пользовалась большим спросом за рубежом, в том числе у производителей стали на Ближнем Востоке, в Северной и Южной Америке, Азии и Австралии. В 2023 году производство переориентировано в основном на государственный заказ. Графитированные электроды используются в том числе в производстве стали: для подвода электроэнергии к сталеплавильным печам. Из-за высокой термостойкости графита материал устойчив в габаритных характеристиках при экстремальных температурах. При плавлении стали электроды расходуются, а для их компенсации (длины) применяют конусообразные или цилиндрические ниппели, ввинчивающиеся с концов электродов и тем продлевающие срок эксплуатации. Реализованный проект BFG Robotics способствовал автоматизации производства графитовых ниппелей. Внешний вид автоматизированной линии представлен на рис. 10.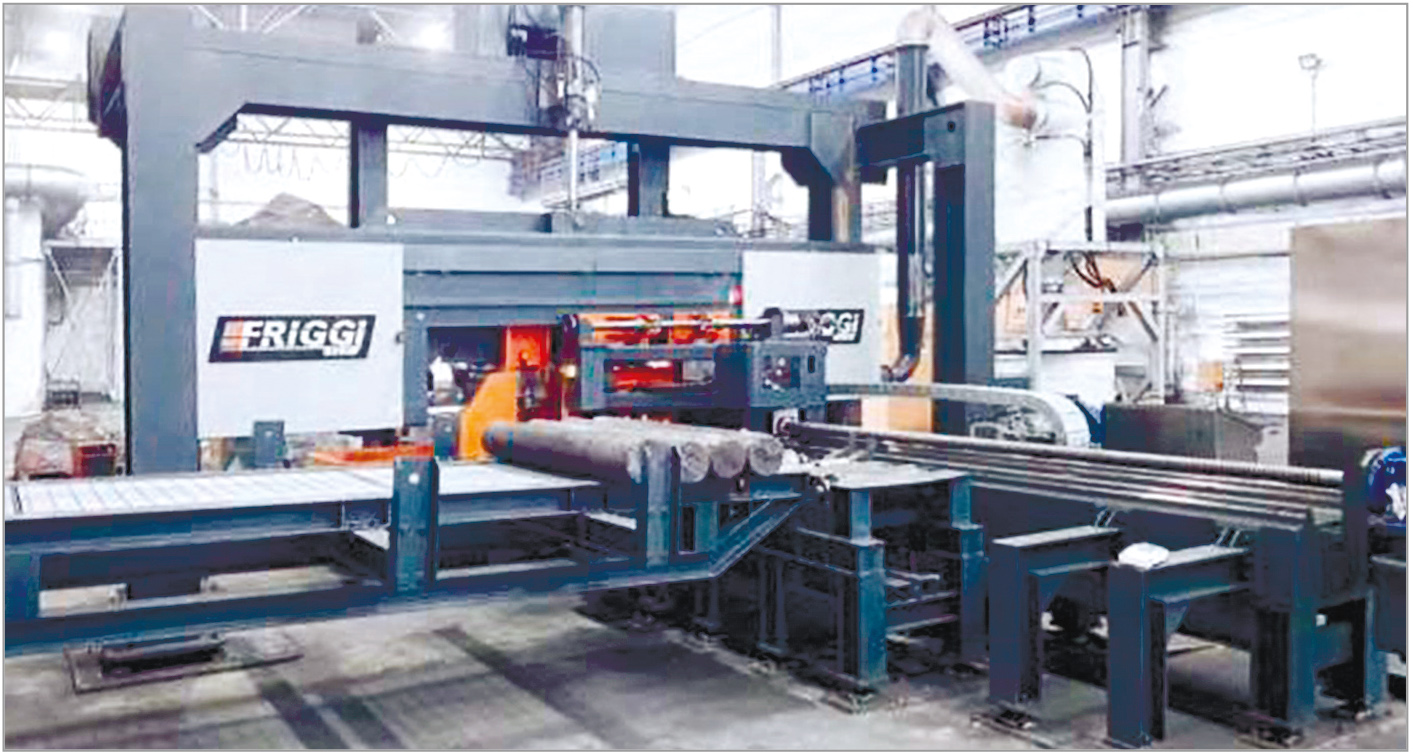
Ранее действовавшая на НЭЗ автоматизированная линия для производства ниппелей к электродам не удовлетворяла руководство компании по качеству и затратам на обслуживание, оставляла желать лучшего и её пылезащита. Когда недавно возросли требования к точности нарезки резьбы ниппелей, стало понятно, что старая линия напоминает анахронизм эпохи. Вместо неё, следуя разумной политике развития на конкурентном, в том числе международном, рынке НЭЗ нашли возможность заказать проектные работы, создание на российской элементной базе и монтаж современной автоматизированной системы, запущенной в 2022 году. На проектирование комплекса с нуля и на заказ необходимого оборудования у разработчиков отечественной компании BFG Robotics ушло 4 месяца.
Особенности внедрения робототехнического комплекса
Не обойтись без автоматизации процесса и тогда, когда масса заготовки может достигать 400 кг, при этом её нужно установить в захват станка с точностью до 1 мм. Ни кран-балка, ни группа людей быстро и точно установить деталь с таким весом не может. В ситуации для решения подобных задач выбирают или роботизированную систему, или систему портальную, стоимостью в пять раз дороже… и сложнее в эксплуатации и регламентном обслуживании. Автоматизированная линия подходит и там, где требуется работа с большим ассортиментом заготовок разного размера; на НЭЗ это 31 типоразмер. Необходимо захватывать и малые, и условно большие заготовки. Автоматизированная линия, смонтированная в НЭЗ, отличается особенностями разработки: теперь с помощью инженерной мысли на производстве применяются два типа захвата с переналадкой не более 5 минут. Переналадка всей линии-робота, станков, ленточной пилы для разделки больших заготовок на части, управление двумя станками и системой измерения и дополнительного защищённого от агрессивной окружающей среды (графитовой пыли) оборудования не более 15 минут [1]. В процессе работы автоматизированной линии оцифрованная информация о состоянии каждой единицы оборудования и маркированных деталях в режиме реального времени передаётся на OPC-сервер завода. Технологические операции происходят в полностью автоматическом режиме: оператору нужно загрузить заготовки, выбрать на панели управления нужный типоразмер и дождаться готового продукта. На производство каждой детали затрачивается 2–5 минут в зависимости от диаметра. Автоматизированная загрузка исключает человеческий фактор, таким образом, уменьшаются риски травм и повышается безопасность производственного процесса. На последнем этапе данные измерений в цифровом виде зашиваются в штрих-код, этикетка с которым распечатывается на принтере с липкой лентой. Перед отправкой на конвейер оператор помещает этикетку на деталь. Функции единственного оператора сводятся к наклеиванию этикеток и визуальному контролю ниппелей на отсутствие брака. Эти процессы пока не автоматизированы, однако нет пределов совершенству. В результатах также исключение травмоопасного физического труда из-за относительно тяжёлых заготовок. Итак, в НЭЗ освоили автоматизированную систему производственной линии под управлением и контролем только одного человека-оператора, тогда как старой линии требовалось 5 человек. Процесс производства достоверно описан в [1]. Роботизированная линия по выпуску графитовых ниппелей на НЭЗ единственная в России. Аналогичную продукцию выпускают лишь несколько заводов в КНР и США.Выводы
Автоматизированные линии на предприятиях и заводах в России действуют не первый год. Чтобы сохранить конкурентоспособность и повысить производительность производства, расширить функционал без потери качества и безопасности, необходимы разработки новых модулей автоматизации, технологий, что приведёт к запуску нового оборудования взамен устаревшего. На примерах в статье мы показали, что это вполне возможно. Как показала практика, в сложное время санкционных ограничений вполне возможна результативная кооперация между разработчиками, заказчиками и монтажниками оборудования и автоматизированных производственных линий с объединением всех составляющих на территории России. Такой государственный подход поможет решить насущные вопросы национального суверенитета, экономической независимости государства и промышленности, параллельного импорта, замены комплектующих уже действующих АЛ зарубежного производства и в целом приведёт к созданию параллельной электронной индустрии с опережением зарубежного уровня. ●Литература
- Автоматизированная производственная линия на Новочеркасском электродном заводе // URL: https://www.tadviser.ru/a/606365.
- Надёжность автоматизированных производственных линий, выдержки, общие понятия, расчёты // URL: https://cyberpedia.su/4x50d1.html.
- Облачная фабрика программных роботов (ОФР) для транспортно-логистической отрасли // URL: https://www.tadviser.ru/a/707014.
- Рейтинг RPA-платформ 2022 // URL: https:// www.cnews.ru/reviews/rpa_2022.
Если вам понравился материал, кликните значок - вы поможете нам узнать, каким статьям и новостям следует отдавать предпочтение. Если вы хотите обсудить материал - не стесняйтесь оставлять свои комментарии : возможно, они будут полезны другим нашим читателям!