Введение
Современное пищевое производство невозможно представить без автоматических линий упаковки и отгрузки готовой продукции. Наличие автоматики позволяет решить сразу несколько проблем: уменьшить отбраковку продукции из-за нарушения целостности упаковки, повысить безопасность производства, снизить издержки за счёт уменьшения количества персонала. Одной из компаний, выполняющих проекты по автоматизации процессов упаковки и отгрузки готовой продукции, является ООО «ГринХилл Груп».Компания работает на рынке автоматических производственных линий и упаковки готовой продукции с 2010 года и является официальным системным интегратором ряда европейских производителей конвейерного оборудования. Область поставляемых решений охватывает системы и средства перемещения продукции в первичной или вторичной упаковке, её сортировку и учёт.
Заказчиками подобных систем были как международные компании, такие как Nestle Purina PetCare, K-Rauta, Rockwool, Harry’s (Barilla Group), так и ряд российских предприятий, занятых в пищевой промышленности, производстве бытовой химии, косметики, а также строительных материалов.
Задача укладки упаковок на палету
Один из недавних проектов был связан с поставкой, монтажом и пусконаладкой на предприятии Harry’s (Barilla Group) комплекта из двух палетайзеров – оборудования для послойной укладки на палету упаковок готовой продукции.Необходимость внедрения была обусловлена несколькими причинами:
- повышение производительности труда персонала, занятого на упаковке, – обилие ручного труда снижает производительность сотрудников к концу смены;
- повышение качества упаковки – при ручной укладке упаковок слои деформировались и выступали за границы палеты;
- снижение издержек за счёт уменьшения количества персонала, занятого на упаковке.
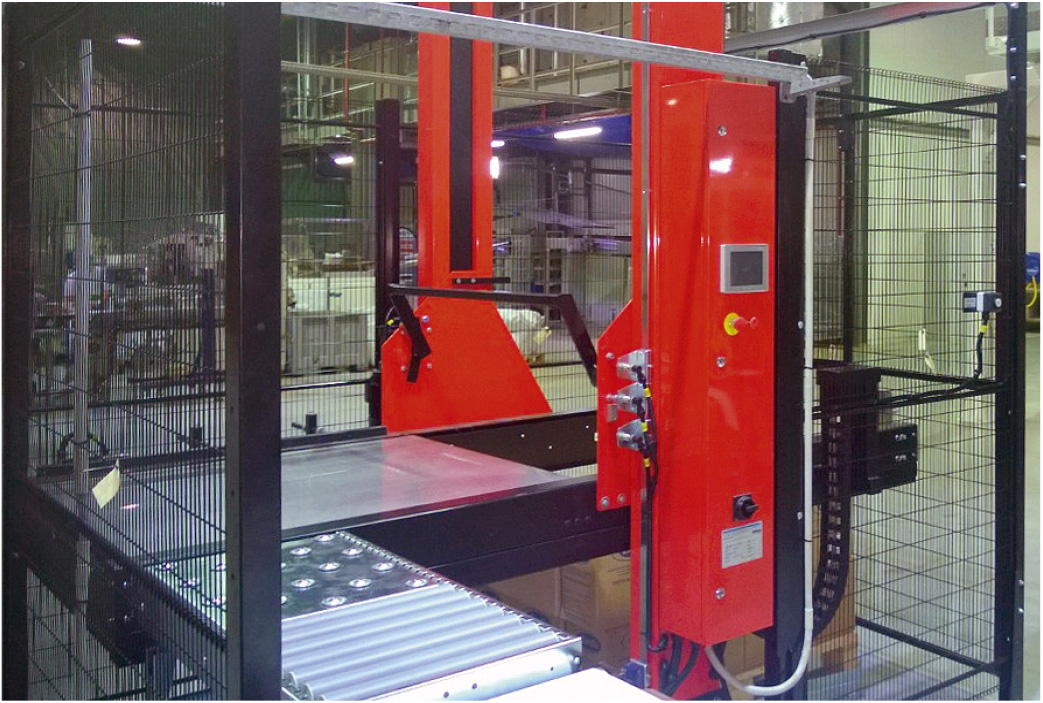
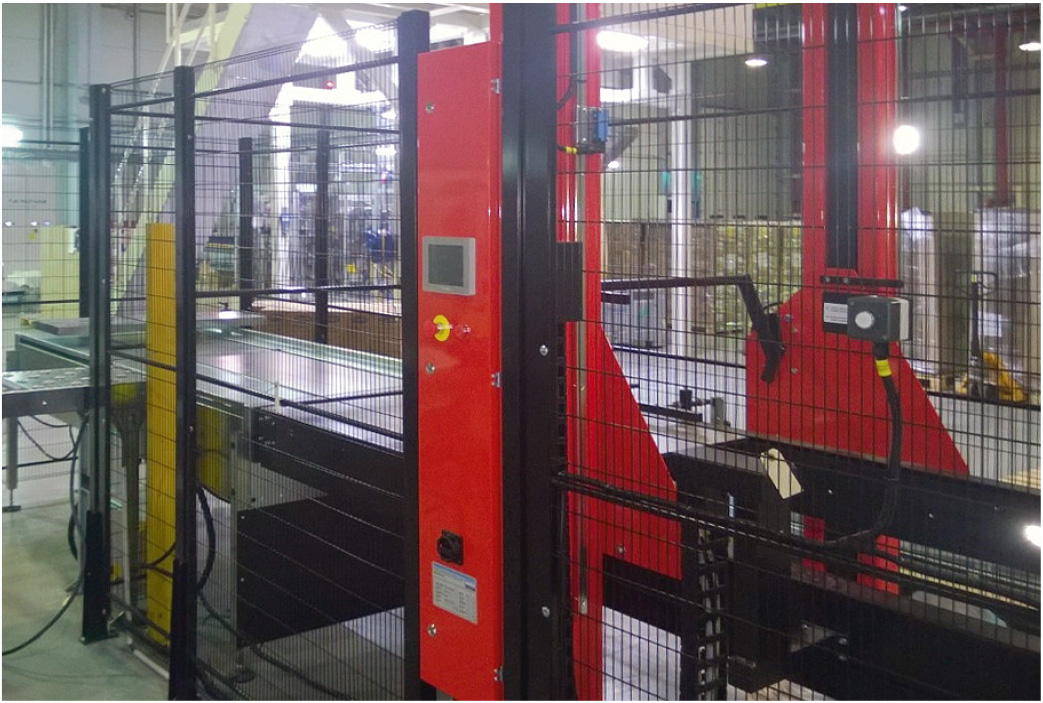
Состав оборудования
Палетайзер представляет собой комплексную систему, имеющую в своём составе как металлоконструкцию, так и электромеханические элементы (двигатели, редукторы), различные датчики, устройства безопасности, управления и визуализации.Оба палетайзера включают в свой состав:
- платформу для погрузки;
- раму для платформы с установленным электродвигателем для горизонтальных перемещений платформы;
- башенный модуль с электродвигателем для вертикальных перемещений рамы платформы;
- механизм съёма упаковок с платформы, оснащённый электродвигателем;
- шкаф управления для компонентов управления с сенсорной панелью (рис. 3), выключателем питания, кнопками остановки и аварийной остановки;
- сканер безопасности для контроля зоны безопасности (рис. 4);
- кнопочный пост для контроля доступа в зону погрузки палеты;
- фотоэлектрические и индукционные датчики, концевые выключатели для определения положения движущихся механизмов и обеспечения безопасности.
- столом с толкателем для перемещения слоя упаковок на платформу для погрузки;
- световым барьером (рис. 5) для предотвращения травм персонала при работе погрузочного механизма;
- кнопочным постом для запуска процесса загрузки и кнопочным постом аварийной остановки.
В качестве ПЛК используется SIEMENS S7-1200 1214C (рис. 6).
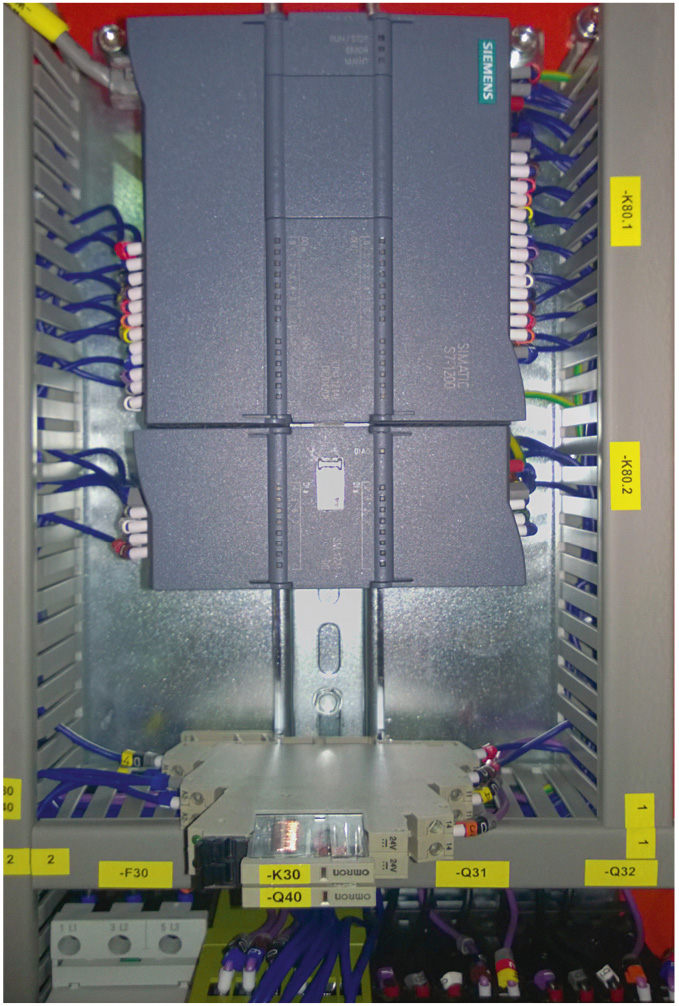
Центральный процессор S7-1200 оснащён встро-енным интерфейсом Ethernet, который может применяться для программирования и диагностики, обмена данными с другими системами автоматизации, устройствами и системами человеко-машинного интерфейса. Для организации обмена данными могут использоваться транспортные протоколы TCP/IP, ISO на TCP и S7-функции связи (S7-сервер или S7-клиент). Блок центрального процессора имеет 14 дискретных входов, 10 дискретных выходов и 2 аналоговых входа, это позволяет уменьшить количество модулей расширения и снизить стоимость оборудования. Помимо этого в шкафу управления установлены модули рас-ширения SM 1221 на 8 дискретных входов, а также SM 1223 на 8 дискретных входов и 8 дискретных выходов. Подключение к внутренней шине контроллера выполняется с помощью выдвижных штекеров, вмонтированных в каждый модуль SM. Подключение внешних цепей производится через съёмные терминальные блоки с контактами под винт.
Силовое оборудование шкафа (рис. 7) включает в свой состав автоматические выключатели SIEMENS SIRIUS серии 3RV1011, которые выполняют функцию защиты от перегрузки и короткого замыкания двигателей, а также контакторы SIEMENS 3RT1015 для коммутации питания электродвигателей.
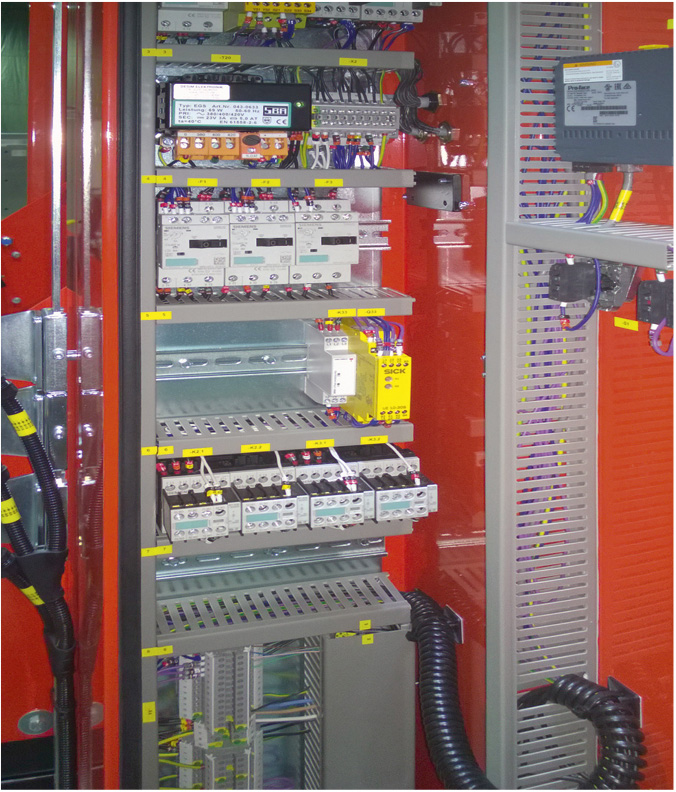
Поскольку палетайзер является подъёмно-погрузочным оборудованием, то крайне важно соблюдение норм безопасности персонала. Безопасность обеспечивается за счёт многоступенчатого (отдельно контроль датчиков и кнопок аварийного останова) и многократного (контролируются два выхода с датчиков и кнопок) контроля состояния датчиков безопасности и кнопок аварийного останова.
Эти функции в шкафу управления выполняют реле безопасности SICK UE10-30S и реле безопасности PILZ PNOZ-X3. Первое реле принимает сигналы от датчиков безопасности (сканер и световой барьер) и передаёт на внутренние контакты, которые последовательно подключены к кнопкам аварийного останова. Далее полученная цепь подключается ко второму реле, которое в случае нарушения безопасности блокирует включение двигателей оборудования. Оба реле также выполняют диагностику и показывают состояние системы безопасности посредством светодиодных индикаторов.
Управление палетайзером осуществляется через сенсорную панель Pro-face PFXGM4301 TAD. Также для управления возможна установка кнопочных постов.
Описание алгоритма управления
Процесс работы с палетайзером построен следующим образом:- после включения палетайзера система переводится в автоматический режим, который выбирается на панели управления;
- через настройки задаётся количество слоёв на палете;
- персонал укладывает на платформу слой коробок с продукцией;
- после выхода из зоны работы погрузочных механизмов работник нажимает кнопку «Загрузка» на панели управления;
- механизмами палетайзера выполняется укладка слоя на палету;
- после возврата платформы в исходное положение персонал может войти в зону работы и продолжить погрузку;
- если уложено заданное количество слоёв, разрешается доступ в зону погрузки палеты для вывоза продукции и установки пустой палеты.
- после включения палетайзера система переводится в автоматический режим, который выбирается на панели управления;
- через настройки задаётся количество слоёв на палете;
- персонал укладывает на стол с толкателем слой коробок с продукцией;
- после выхода из зоны работы толкателя работник нажимает кнопку «Загрузка» на панели управления или аналогичную кнопку на кнопочном посту;
- толкатель выполняет перемещение слоя на платформу;
- после возврата толкателя назад в исходное положение персонал может сразу войти в зону работы толкателя и продолжить погрузку, не дожидаясь окончания цикла укладки слоя;
- механизмами палетайзера выполняется укладка слоя на палету;
- если уложено заданное количество слоёв, разрешается доступ в зону погрузки палеты для вывоза продукции и установки пустой палеты.
На палетайзере с толкателем дополнительно для повышения безопасности установлен световой барьер (SICK C2C-SA03030A10000 – передатчик, SICK C2C-EA03030A10000 – приёмник) на выходе стола для погрузки. Разрешение светового барьера позволяет контролировать случайное попадание руки сотрудника в зону работы погрузочного механизма. Такая потенциальная опасность существует, поскольку укладка персоналом нового слоя на стол производится до окончания цикла работы палетайзера. Одновременное срабатывание сканера безопасности и светового барьера проверяется схемотехнически с использованием реле безопасности. Это позволяет исключить ложное срабатывание светового барьера при перемещении толкателем слоя коробок на погрузочную платформу.
Также для безопасности предусмотрен замок с концевым выключателем на дверцах в зоне погрузки палеты. При открытии дверцы во время работы палетайзера происходит аварийный останов системы. В то же время, если система разрешила открытие дверцы, то срабатывание концевого выключателя не приводит к аварии.
В случае использования нестандартных палет или не предусмотренных техническим заданием размеров упаковок в палетайзерах предусматривается настройка через сенсорную панель начального положения платформы для погрузки и смещение слоя относительно положения палеты. Для отстройки отступа по высоте между платформой и палетой, а также максимальной высоты слоёв на палете предусмотрена регулировка положения концевых выключателей на башенном модуле.
Результаты внедрения
Был успешно выполнен полный комплекс монтажных и пусконаладочных работ по вводу палетайзеров в эксплуатацию. Тем не менее, стоит отметить и несколько важных замечаний, которые выяснились в ходе пусконаладочных работ:- при настройке сканеров безопасности необходимо обратить внимание на цвет спецодежды персонала: дело в том, что тёмная одежда поглощает часть излучения и происходит незначительное сужение зоны безопасности; в то же время в случае использования белой одежды зона безопасности незначительно увеличится, поскольку белая поверхность отражает излучение гораздо лучше;
- штатный замок на дверцах в зоне погрузки палеты довольно слабый и открывается от любой вибрации – для устранения этого недостатка на дверцах были дополнительно установлены магниты для их более прочной фиксации;
- к сожалению, отсутствуют какие-либо штатные средства и инструкции по настройке скорости работы палетайзера, в результате при увеличении производительности конвейера на палетайзере возникает скопление упаковок готовой продукции и требуется их буферизация;
- необходима жёсткая фиксация всех промежуточных конвейеров, устанавливаемых для транспортировки упаковок с основного конвейера до палетайзера, в противном случае при случайных смещениях данных конвейеров они могут попасть в контролируемую зону безопасности, что приведёт к аварийному останову системы.
E-mail: ssa-company@rambler.ru
Если вам понравился материал, кликните значок - вы поможете нам узнать, каким статьям и новостям следует отдавать предпочтение. Если вы хотите обсудить материал - не стесняйтесь оставлять свои комментарии : возможно, они будут полезны другим нашим читателям!