Введение
На некоторых доменных печах (ДП), установленных на Западно-Сибирском металлургическом комбинате (ЗСМК, Россия), Бхилайском металлургическом заводе (БМЗ) и заводе Джиндал (Jindal, Индия), используется роторное загрузочное устройство (РЗУ) [1, 2], разработанное НПКЦ «Тотем». На ЗСМК и БМЗ применяется загрузочное устройство конусного типа, а на заводах Jindal – бесконусного. Основным элементом РЗУ является ротор, распределяющий шихтовые материалы на колошнике ДП (рис. 1).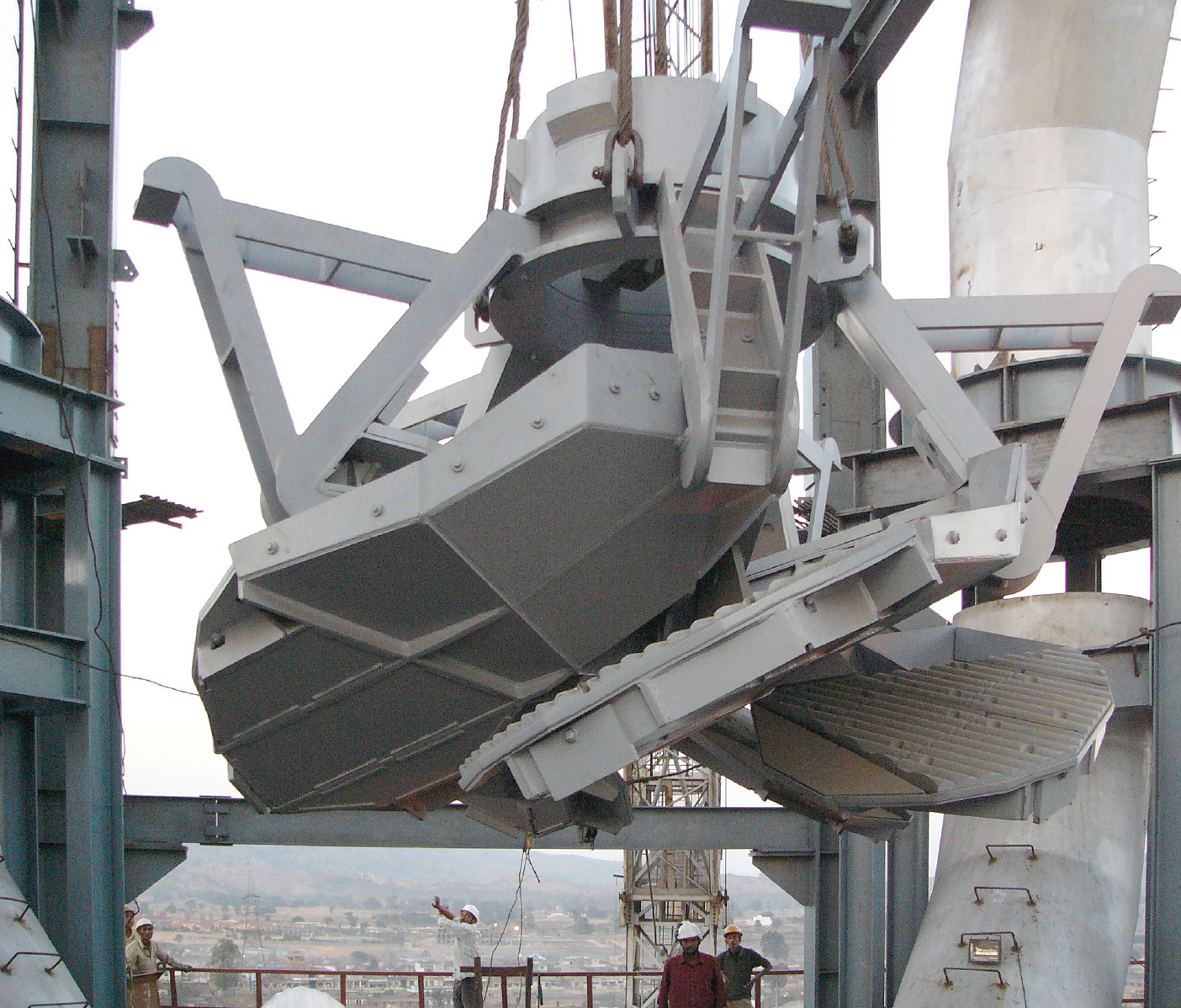
Для управления загрузкой ДП с РЗУ в НПКЦ «Тотем» разработан аппаратно-программный комплекс, включающий три подсистемы:
- система управления механизмами верхней загрузки ДП с РЗУ (АСУ «Ротор»);
- имитационная модель загрузки;
- система контроля профиля шихты.
АСУ «Ротор»
Назначение системы
АСУ «Ротор» предназначена для управления механизмами роторного загрузочного устройства с целью обеспечения заданного распределения шихтовых материалов на колошнике доменной печи и создана с использованием современных высокопроизводительных программируемых логических контроллеров (ПЛК) с расширяемой модульной архитектурой. АСУ «Ротор» может быть включена как составная часть в существующую автоматизированную систему управления доменной печью. Далее описана АСУ «Ротор» бесконусного роторного загрузочного устройства (БРЗУ) как наиболее перспективного и в настоящее время повсеместно устанавливаемого вместо конусного, как при строительстве новых, так и при капитальной реконструкции действующих доменных печей.Принципы управления ротором в печах с конусным загрузочным устройством аналогичны, отличие в том, что до роторного распределителя в тракте выгрузки осуществляется управление конусами (электроприводом лебёдки конусов) вместо блоков клапанов. Вращающийся распределитель шихты при установке ротора в конусных аппаратах не используется и может быть демонтирован.
Характеристика объекта автоматизации
В комплект поставки БРЗУ НПКЦ «Тотем» входят следующие основные узлы и агрегаты:- приёмная воронка и верхний блок клапанов (ВБК);
- промежуточный бункер и нижний блок клапанов (НБК);
- привод роторного распределителя с ротором лопастного типа;
- гидронасосная станция (ГНС);
- станция густой смазки (СГС).
- ВБК;
- НБК;
- клапаны системы выравнивания давления;
- клапаны подачи азота;
- ротор;
- ГНС;
- СГС.
Для безаварийной работы БРЗУ предусмотрены системы охлаждения водой и азотом центрального редуктора, а также система густой смазки. СГС обеспечивает смазку подшипника, зубчатой передачи редуктора, уплотнительных колец камеры редуктора, а также узлов блоков клапанов. Каждый блок клапанов состоит из шихтового затвора и расположенного под ним газоуплотнительного клапана тарельчатого типа, управляемых с помощью гидропривода. Конструкции ВБК и НБК идентичны. Газоуплотнительный клапан и шихтовый затворы оборудованы гидроцилиндрами, каждый из которых управляется АСУ «Ротор».
Для предоставления информации о значениях эксплуатационных параметров и состоянии механизмов загрузки обслуживающему персоналу и программам ПЛК, управляющим процессом загрузки, БРЗУ оснащено необходимыми датчиками.
Технология загрузки доменной печи шихтовыми материалами с помощью БРЗУ
Загрузка доменной печи осуществляется повторяющимися циклами, состоящими из подач, которые, в свою очередь, включают раздельные порции рудной и коксовой части. Таким образом, каждая подача состоит из двух порций материалов. Под порцией подразумевается количество шихтовых материалов, однократно выгружаемых из приёмной воронки и промежуточного бункера БРЗУ в печь. Цикл загрузки считается законченным, когда вид и состав подач начинает повторяться. Наименьшей и неделимой частью цикла является порция одного вида материалов. Загрузку ДП принято оценивать по величине рудной нагрузки на кокс (отношение руда/кокс) и газового потока по радиусам и окружности колошника.Колошник доменной печи условно разбит на 6 равновеликих по площади кольцевых зон (КЗ). Регулирование распределения рудных нагрузок и газового потока по радиусу колошника достигается изменением режима работы роторного распределителя, при этом материал может поступать по окружности в любую область колошника, от стенок печи до оси включительно, в виде:
- однокольцевой загрузки (гребень засыпи расположен на одной КЗ);
- многокольцевой загрузки (гребень засыпи формируется на нескольких КЗ путём скачкообразного изменения скорости вращения ротора);
- спиральной загрузки (порция распределяется в заданных смежных КЗ путём непрерывного изменения скорости вращения ротора).
Основные функции системы управления
Основными функциями АСУ «Ротор» являются:- управление по заданной программе скоростью и направлением вращения ротора при выгрузке в печь каждой порции шихтовых материалов, с возможностью обеспечения в широком диапазоне однокольцевой, многокольцевой, спиральной загрузки материалов;
- управление работой ВБК и НБК;
- управление работой клапанов выравнивания давления;
- взаимная синхронизация работы перечисленных систем и их синхронизация с работой скипового подъёмника (загрузочного конвейера) и зондами (механическими, при их наличии);
- управление СГС, ГНС и системами охлаждения, обеспечивающими нормальное функционирование узлов БРЗУ;
- сбор, обработка и хранение информации о работе АСУ «Ротор»;
- выдача предупреждающих и аварийных сообщений при выходе контролируемых параметров за допустимые пределы;
- протоколирование аварийных и предупреждающих сообщений, возникающих в ходе процесса загрузки печи;
- ввод и передача в контроллер АСУ «Ротор» управляющих инициатив оператора (дистанционное управление);
- представление эксплуатационному персоналу на экране монитора информации о процессе загрузки печи;
- редактирование и хранение программ загрузки;
- проверка корректности ввода оператором программы загрузки на этапе её отработки;
- настройка параметров системы управления через настроечные экраны;
- архивирование значений технологических параметров, характеризующих процесс загрузки;
- самодиагностика ПЛК и модулей ввода-вывода.
Программы загрузки доменной печи
Программа загрузки доменной печи представляет собой организацию работы БРЗУ для реализации конкретного цикла загрузки шихты. В АСУ «Ротор» может быть представлено несколько программ (циклов) загрузки.Программы загрузки включают следующие данные:
- вес и вид материалов загружаемой шихты в подачу;
- число и порядок чередования коксовых, рудных и смешанных порций;
- дополнительные выгрузки;
- уровень засыпи (для левого и правого зонда).
- тип загрузки;
- начальная и конечная кольцевые зоны загрузки;
- распределение материала по кольцевым зонам.
Выгрузка материалов в печь производится согласно заданной программе в режимах однокольцевой, многокольцевой и спиральной загрузки. В последних двух режимах можно установить как равномерное распределение порции по заданным кольцевым зонам, так и неравномерное – путём указания в процентах массовой доли порции, выгружаемой в каждую кольцевую зону.
Спиральные загрузки порций материалов могут производиться как от центра печи к периферии (ротор ускоряется), так и от периферии к центру (ротор замедляется).
Вид экрана программ загрузки показан на рис. 2.
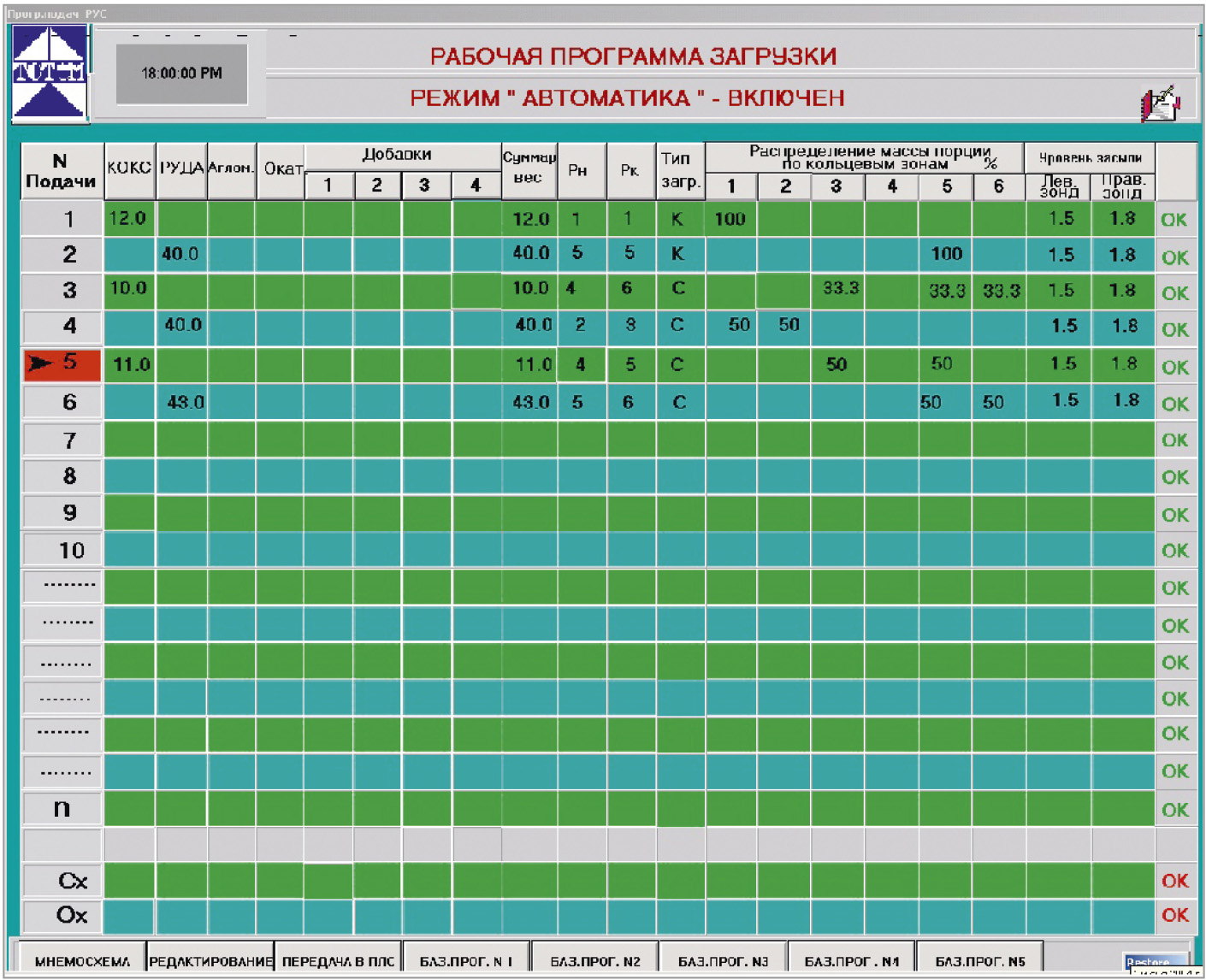
Алгоритм слежения
Алгоритм слежения осуществляет слежение за продвижением порции по тракту загрузки и последовательностью работы механизмов загрузочного устройства. В основе алгоритма слежения – перезапись данных о порции материала из базы данных (БД), относящейся к определённому механизму тракта загрузки, в БД следующего по ходу тракта загрузки механизма. Данные о порции по мере обнаружения её в БД определённого механизма последовательно переписываются в следующем порядке: скип 1/скип 2 (конвей-ер), приёмная воронка (ПВ), промбункер (ПБ), ротор.Структура данных в БД всех механизмов одинакова и включает поля:
- номер цикла;
- номер порции в цикле;
- вид порции материала;
- её вес;
- начальная КЗ;
- конечная КЗ;
- тип распределения;
- доли выгрузки на КЗ.
Дальнейшее отслеживание наличия порции в ПВ, ПБ и выгрузки её в печь, а также выдача управляющих сигналов работы клапанов, шихтовых затворов, разрешения работы зондов, предварительной раскрутки ротора производится по данным уровнемеров в шихтовых бункерах (при их наличии) и сигналам положения шихтовых затворов.
Вид экрана мнемосхемы верхней загрузки показан на рис. 3.
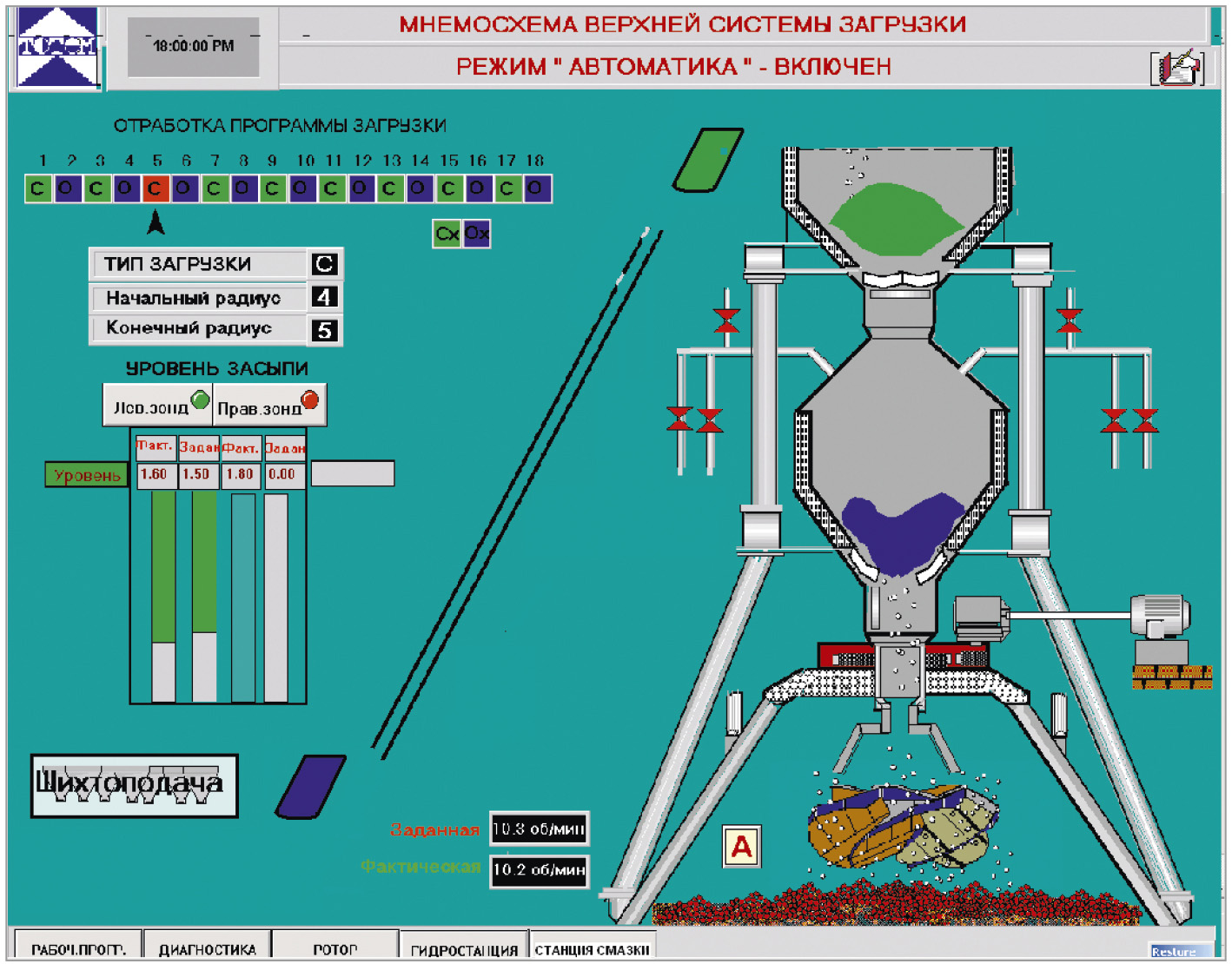
Алгоритм распределения материалов ротором
Алгоритм роторного распределения шихты предполагает постоянство скорости истечения материалов (т/с) через шихтовые затворы. Зная её и вес порции, которую надо выгрузить (распределить), можно рассчитать необходимое время выгрузки (время работы электропривода ротора с частотой, необходимой для выгрузки на данную кольцевую зону – КЗ).Скорость истечения каждого вида материала – величина постоянная, как и скорость вращения ротора для укладки материалов в определённую КЗ (на фиксированном условно нулевом уровне). Эти скорости определяются в процессе испытаний ротора во время холодной загрузки шихты и являются настроечными параметрами.
Для кольцевых загрузок алгоритм работы ротора простой. При однокольцевой загрузке на одну КЗ выгружается вся порция, то есть ротор в течение всего рассчитанного времени выгрузки работает на одной скорости. При многокольцевой загрузке время работы ротора на каждой КЗ пропорционально весу части порции материала, загружаемой на соответствующую КЗ. В случае спиральной загрузки скорость вращения ротора должна плавно изменяться от минимальной до максимальной (или от максимальной до минимальной в случае распределения от периферии к центру) за период времени полного истечения материала. Алгоритм работы электропривода ротора для спиральной загрузки выглядит следующим образом.
- Предварительно (до распределения) производится расчёт необходимой периодичности (с) изменения скорости ротора для каждой i-й КЗ по формуле: Ti = Tвыгр i ∙ ΔTi / (Vмакс i – Vмин i), где Tвыгр i – время выгрузки для данной КЗ; Vмакс i, Vмин i – минимальная и максимальная скорости для данной КЗ (об./с); ΔTi – шаг изменения скорости на данной КЗ (об./с).
- Устанавливается минимальная (при распределении от центра к периферии) или максимальная (при распределении от периферии к центру) скорость вращения ротора для начальной КЗ.
- Запускается таймер на период Т, рассчитанный для начальной КЗ, в течение этого периода ротор вращается со скоростью, установленной в п. 2.
- По истечении периода Т таймер останавливается, проверяется, достигло ли значение заданной текущей скорости максимального (минимального) для конечной КЗ, если достигло, то распределение завершено, если нет, скорость на фиксированное значение (шаг – настроечный параметр) увеличивается (распределение от центра к периферии) или уменьшается (распределение от периферии к центру).
- Далее проверяется, достигло ли значение заданной текущей скорости максимального (минимального) для начальной КЗ, если не достигло – процесс повторяется с тем же периодом, если достигло – устанавливается период для следующей КЗ и последовательность п. 3–5 повторяется для следующей КЗ.
Так как данные по скорости вращения ротора для определённого материала и КЗ являются для данного ротора и печи фиксированными настроечными параметрами для определённого условно нулевого уровня засыпи, при другом текущем уровне для загрузки на нужную КЗ скорость ротора корректируется добавлением поправки, определяемой выражением:
2∙(H0 – Hi),
где Hi – текущий уровень засыпи; H0 – условный нулевой уровень засыпи.
Экран параметров ротора и его электропривода показан на рис. 4.
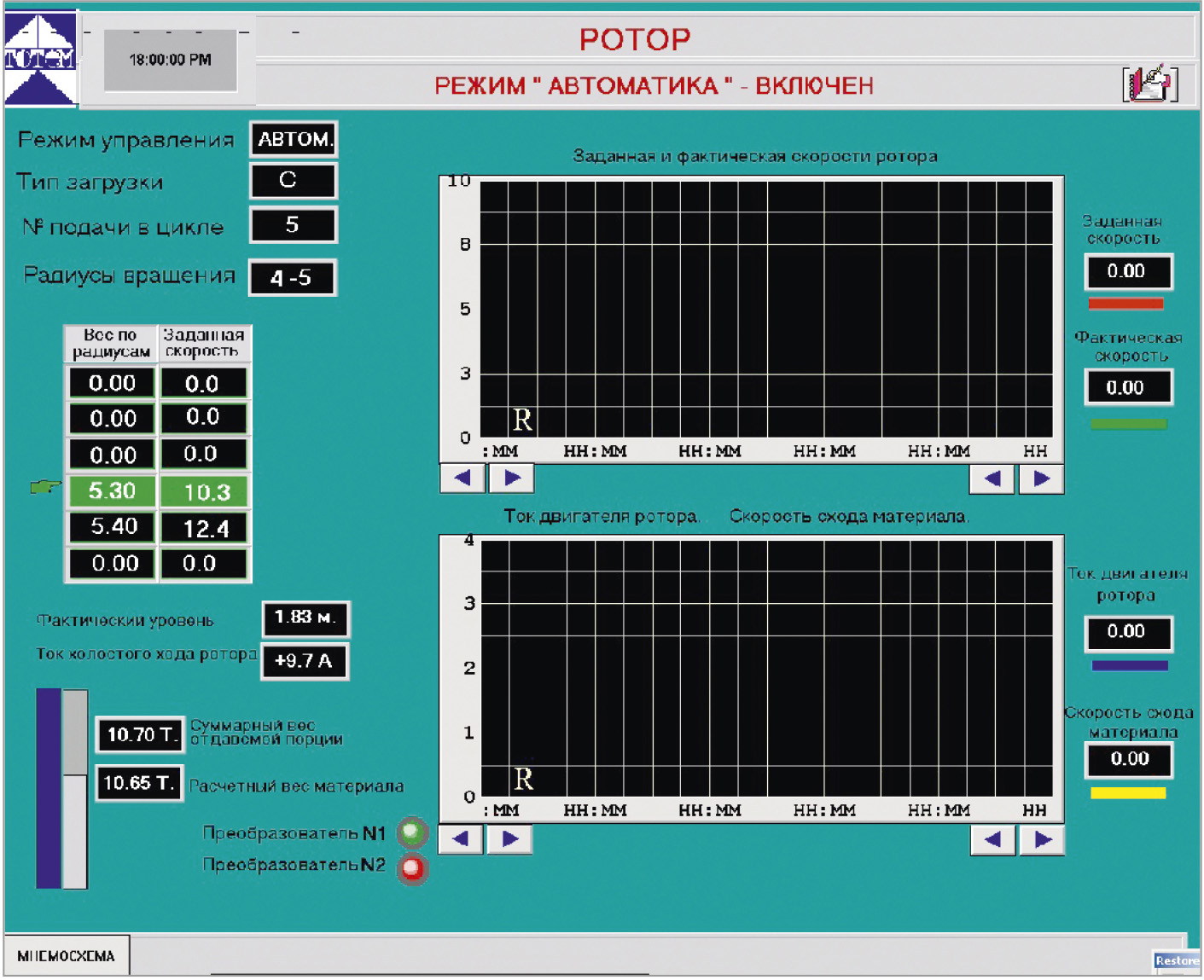
Управление системой гидравлики
Система гидравлики БРЗУ предназначена для управления работой гидроцилиндров шихтовых затворов, газоуплотнительных клапанов, листовой задвижки, а также клапанов системы выравнивания давления и подавления выбросов. Управление соответствующими электромагнитными распределителями (выдача необходимых сигналов) осуществляется ПЛК в программе слежения за продвижением порции материала по тракту загрузки. В ГНС контролируются значения давления в напорных трубопроводах и аккумуляторе, загрязнения фильтров – по сигнализаторам перепада давления на фильтрах, уровни и температура жидкости в баке – сигнализаторами уровня и температуры соответственно. Все перечисленные сигналы – дискретные с датчиков-реле.Мнемосхема ГНС с индикацией состояний параметров отображается на отдельном экране. Индикация положений гидроцилиндров (связанных с ними устройств) показана на экране «Мнемосхема верхней системы загрузки».
Управление системой смазки
Централизованная густая смазка узлов БРЗУ осуществляется из автоматической смазочной станции, расположенной в специальном помещении на колошниковой площадке. Смазка производится автоматически в два смазочных цикла: короткий (каждые 2–3 часа) для точек смазки центрального и углового редукторов и длинный (каждые8 часов) для остальных точек смазки. ПЛК управляет соответствующими распределительными клапанами. Давление на напорных линиях контуров (работа насоса) контролируется концевыми реле давления. Работу системы можно наблюдать на соответствующем экране операторской станции АСУ «Ротор».
Управление системой охлаждения
Для охлаждения узлов БРЗУ применяются азот и вода. Азот подаётся в камеру центрального редуктора привода распределителя. Охлаждающая вода подаётся в рубашки центрального редуктора и циркулирует в замкнутом контуре. Температура узлов редуктора и охлаждающей воды контролируется датчиками температуры.В камеру редуктора привода распределителя азот подаётся постоянно, сброс азота производится в рабочее пространство печи. При повышении температуры любого из указанных датчиков выше заданной (+60…+70°C) автоматически увеличивается подача азота. Также контролируется температура внутри блоков клапанов. Внутрь корпуса нижнего блока клапанов азот подаётся в автоматическом режиме для охлаждения при повышении температуры среды внутри корпуса сверх установленного предела (+100…+150°C).
Работа БРЗУ без подачи азота разрешается в течение 30 минут при условии, что температура контролируемых узлов редуктора не более +90°C. При превышении значения +90°C либо при отсутствии азота более 30 минут происходит автоматическая остановка ротора БРЗУ.
Работу и параметры механизмов системы можно наблюдать на мониторе рабочей станции (рис. 5).
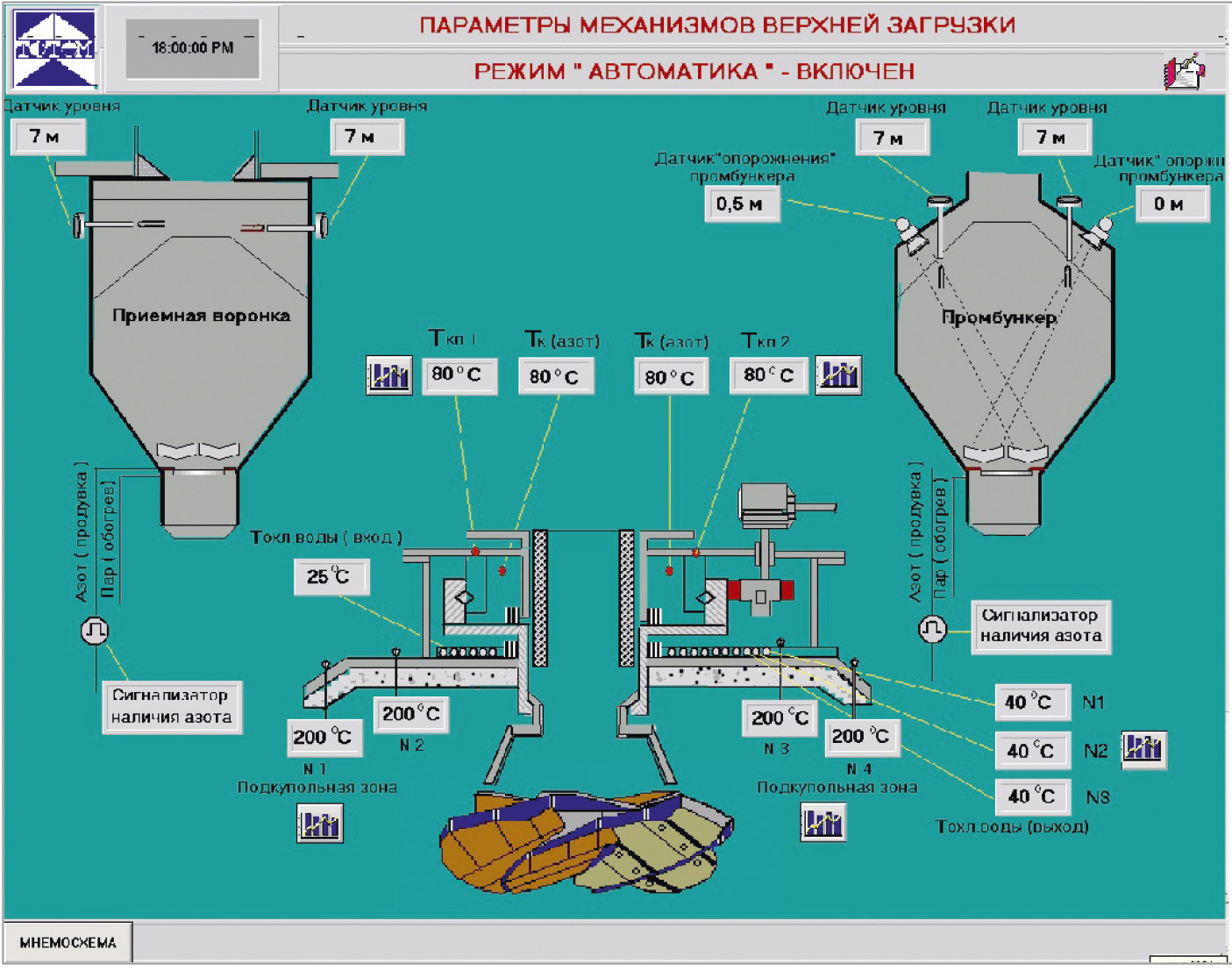
Значения параметров, вышедшие за допустимые пределы, высвечиваются на мнемосхеме жёлтым (предупреждение) и красным (авария) цветами, а также протоколируются значения параметров и время их выхода за допустимые пределы.
Техническое обеспечение
Структура комплекса технических средств АСУ «Ротор» разработана по принятой в современных системах управления с ПЛК трёхуровневой схеме. По характеру выполняемых функций могут быть выделены следующие уровни контроля и управления:- верхний уровень – система хранения, представления информации и операторского управления (операторская станция), выполненная на базе современного персонального компьютера (ПК) промышленного исполнения, подключённого к сети Ethernet;
- средний уровень – система контроля и управления, выполненная на базе ПЛК и удалённых модулей ввода-вывода в станциях распределённой периферии, использует схему распределённого ввода-вывода, основанную на сетевых технологиях;
- нижний уровень – датчики КИП, электрифицированные исполнительные механизмы и устройства управления электродвигателем ротора (управление ГНС и СГС осуществляется через их шкафы управления).
На рис. 6 приведена структурная схема технических средств АСУ «Ротор» на базе ПЛК SIMATIC S7-400 фирмы SIEMENS.
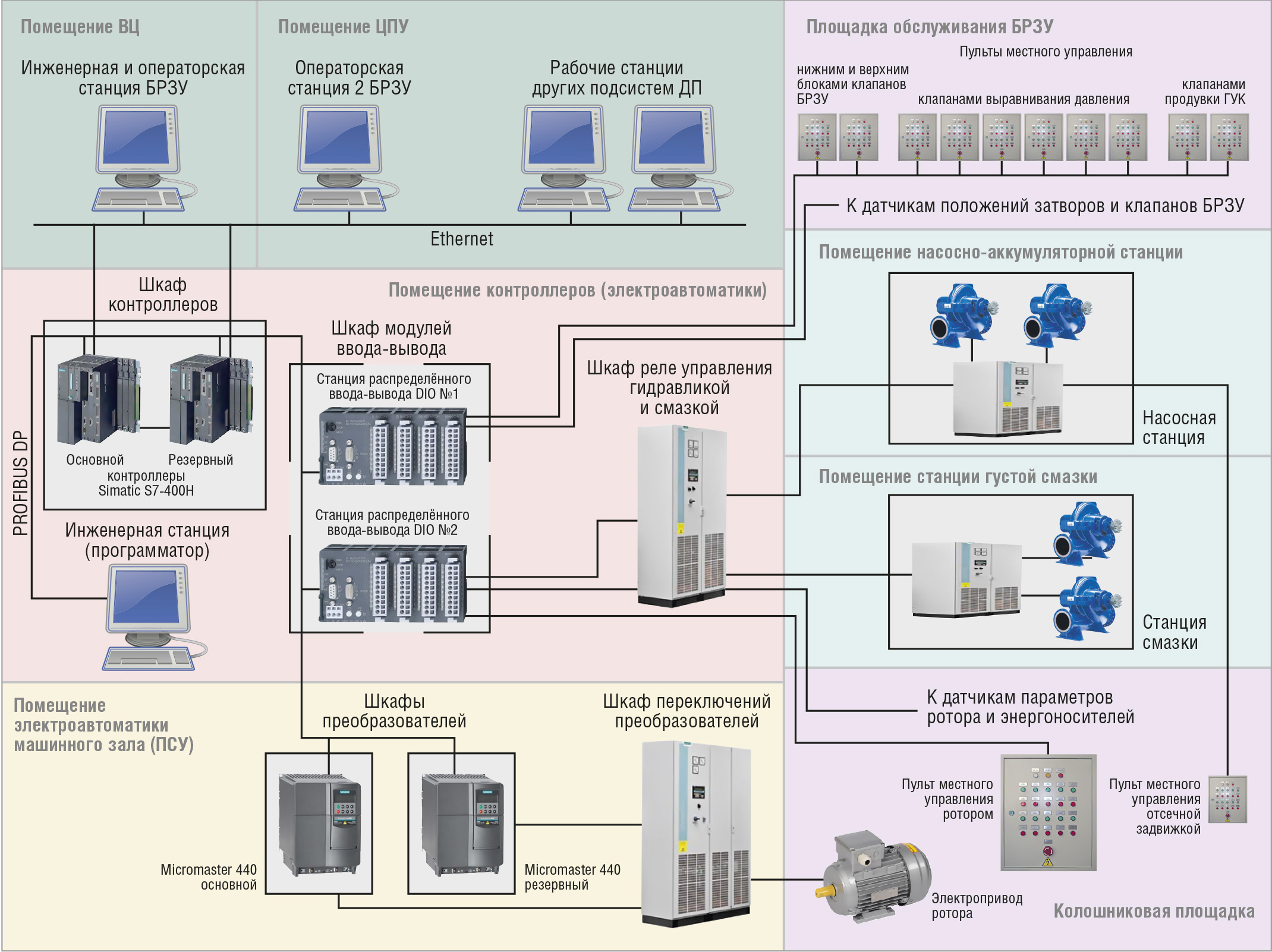
Программное обеспечение
Прикладное программное обеспечение (ППО) АСУ «Ротор», реализующее алгоритмы, описанные в предыдущем разделе, включает в себя:- ППО контроллера управления;
- ППО операторской станции.
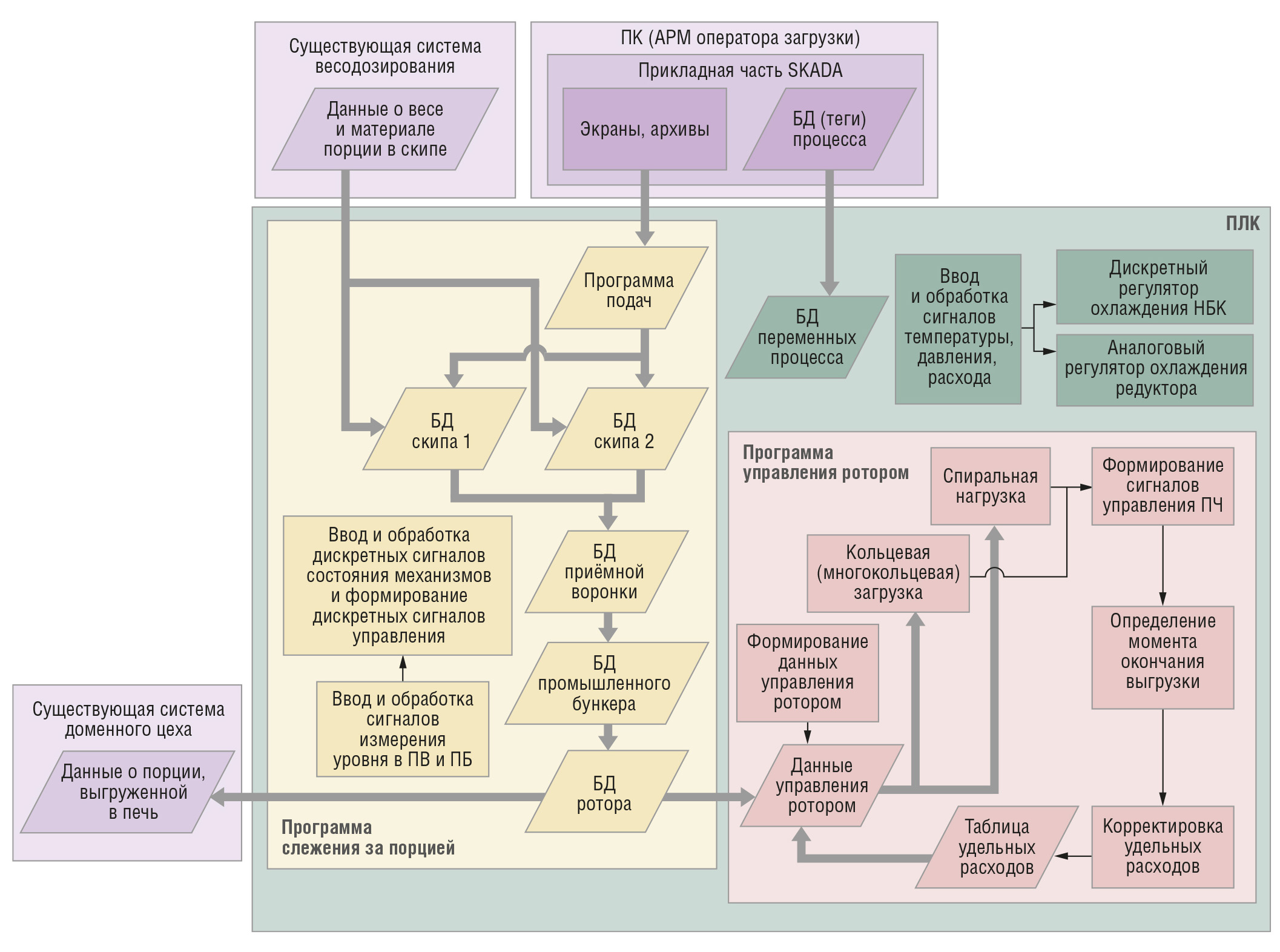
На рис. 8 показан шкаф полигона НПКЦ «ТОТЕМ» с оборудованием SIMATIC S7 для разработки и отладки технического и программного обеспечения АСУ «Ротор».
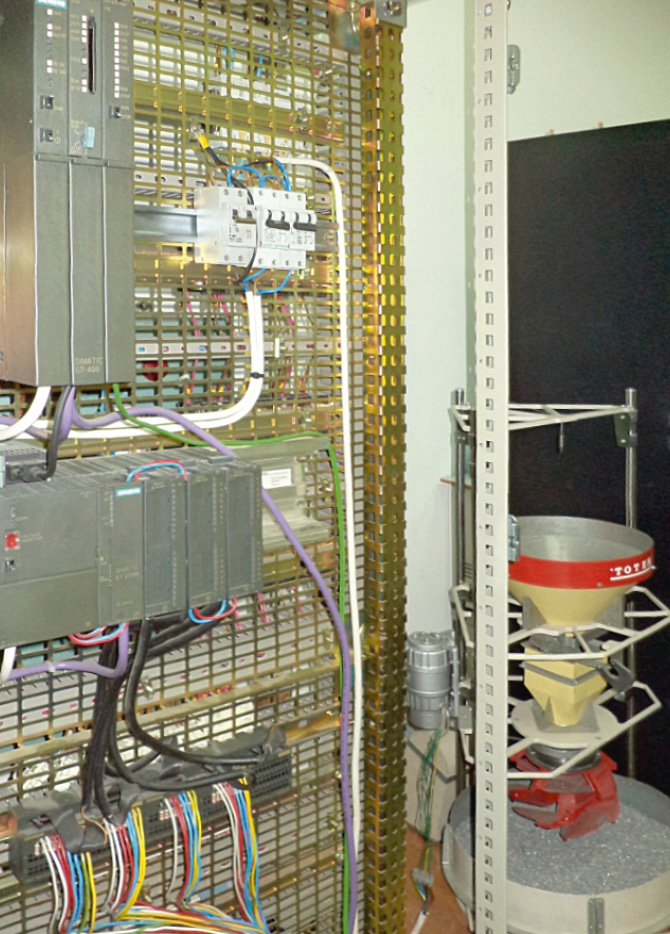
На рис. 9 представлен резервированный контроллер S7-400 в шкафу ПЛК АСУ «Ротор» БМЗ (Индия).
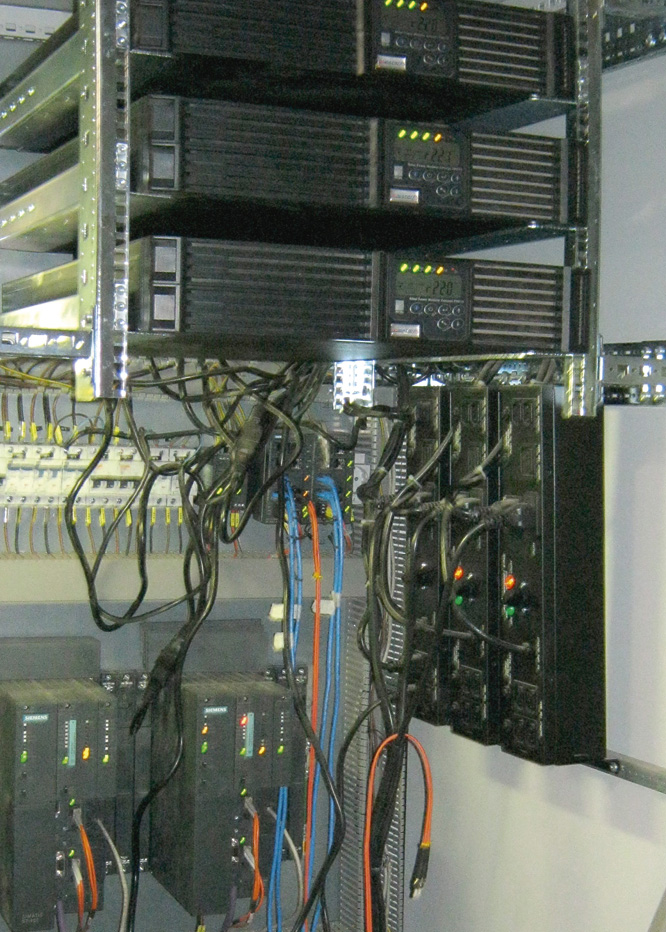
Аналогичные структуры имеют КТС и ППО, созданные на контроллерах и SCADA-системах других типов и производителей с использованием соответствующих средств программирования и конфигурирования, например, АСУ «Ротор» ДП завода Jindal в Индии создана на базе ПЛК Control Logix 5000 и SCADA-системы фирмы Allen Bradley.
Имитационная модель загрузки
Для оптимизации режима загрузки оператор-технолог может использовать имитационную модель (ИМ) формирования структуры столба шихты в печи. ИМ разработана на основе результатов физического моделирования распределения шихты ротором.В экспериментах на физической модели РЗУ определялось распределение материалов по радиусу колошника в зависимости от следующих параметров режима загрузки: скорость вращения ротора, высота уровня засыпи, общее количество и вид материала, расход (скорость истечения) материала, поступающего на ротор.
В ИМ учитываются также распределение скоростей опускания шихты по радиусу печи, углы естественного откоса различных материалов, профиль предыдущего слоя шихты, на который осуществляется загрузка материала, объём и вид загружаемого материала.
Исследования проводились на физических моделях РЗУ масштаба 1:20 применительно к печам соответствующего объёма. Для получения математических моделей, описывающих поведение системы, был использован метод планирования экспериментов [1]. Уровни факторов в экспериментах бы-ли нормированы. В качестве примера в [1] представлены для печи объёмом 2000 м3 завода ЗСМК уровни факторов и матрица планирования экспериментов, а также полученные после обработки экспериментальных данных уравнения регрессии, использованные в ИМ.
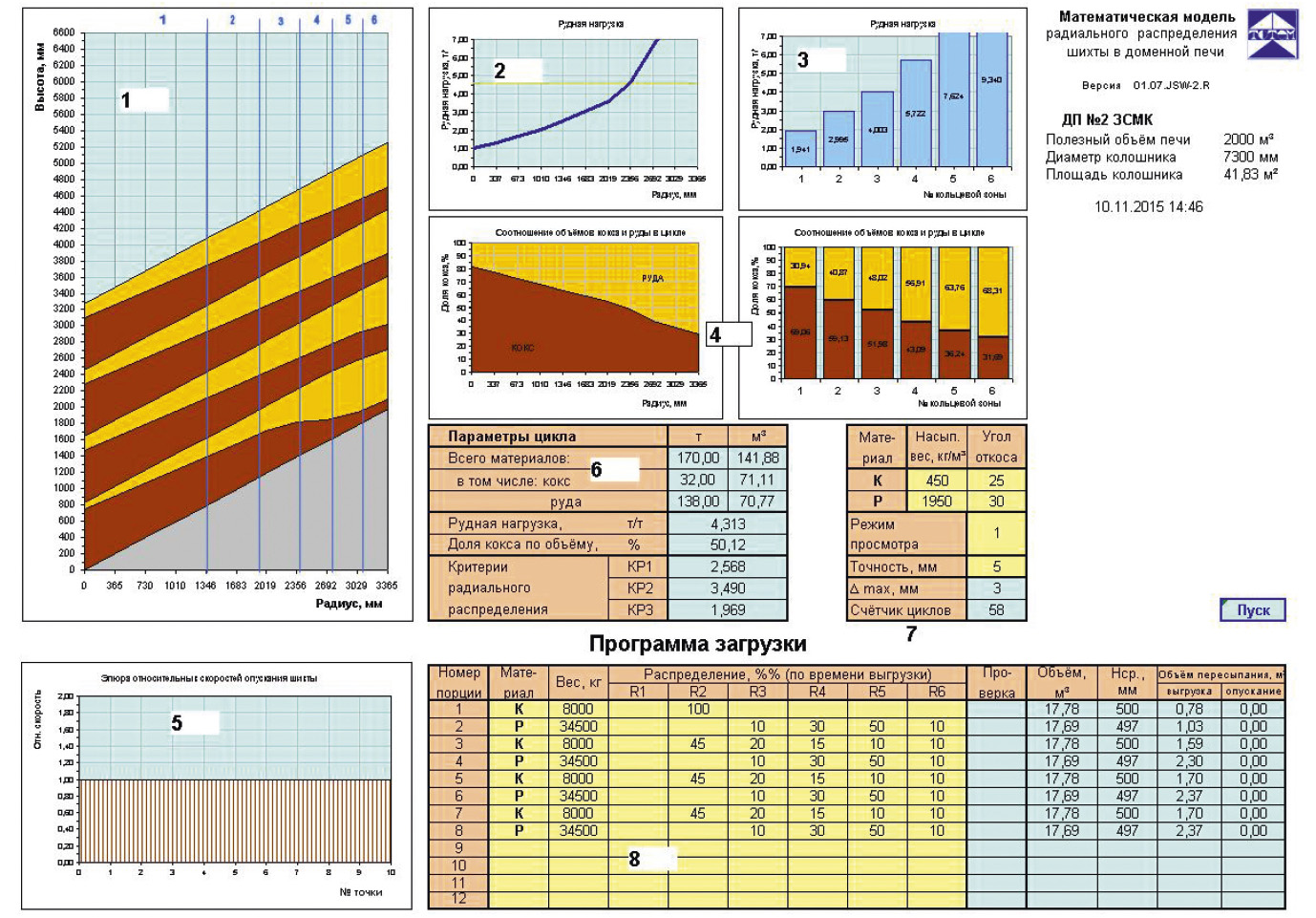
Интерфейс ИМ для цикла, состоящего из 8 подач, показан на примере ДП2 ЗСМК (рис. 10) и содержит диаграммы, на которых представлены:
- расположение и форма слоёв шихты на колошнике после выгрузки одного цикла подач из восьми порций материалов (1);
- изменение рудной нагрузки за цикл подач по радиусу печи (2);
- распределение рудной нагрузки за цикл подач по кольцевым зонам (3);
- относительная высота слоёв кокса и рудных материалов по радиусу (4);
- эпюра скоростей опускания материалов по радиусу печи (в данном примере скорость опускания материалов принята равномерной по всему радиусу) (5);
- характеристики подач, насыпные массы материалов, условия выгрузки их в печь и количественные критерии оценки распределения рудной нагрузки по радиусу (6);
- режимы выгрузки материалов с ротора для каждой порции цикла (7).
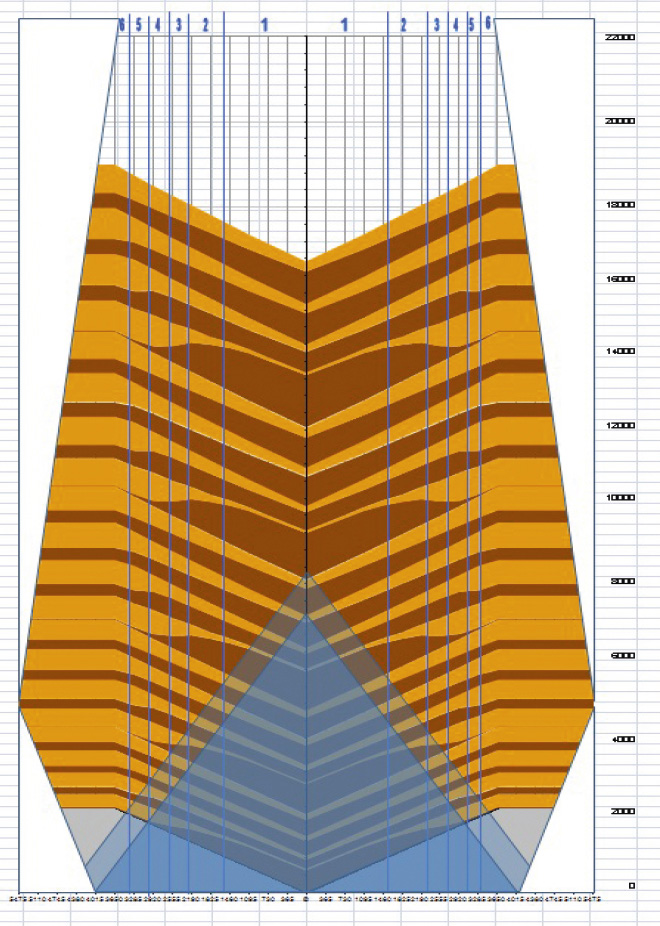
Таким образом, на основе задания режима работы ротора и определения условий укладки материалов на поверхность шихты ИМ позволяет получать послойную структуру шихты на колошнике доменной печи и изменение рудной нагрузки по ее радиусу.
Критерии оценки распределения рудной нагрузки по радиусу печи
В ИМ рассчитываются численные критерии для количественной оценки распределения рудной нагрузки (РН) по радиусу печи. Расчёт осуществляется по формулам:CRD1=РН4–6 / РН1–3;
CRD2=РН5–6 / РН1;
CRD3=РН2–4 / РН1,
где CRD1, CRD2 и CRD3 – критерии радиального распределения рудных нагрузок по радиусу печи; PH4–6; РН1–3; РН5–6; РН2–4; РН1 – рудная нагрузка соответственно в зонах от четвёртого кольца до шестого, от первого до третьего, от пятого до шестого, от второго до четвёртого и в зоне первого кольца.
Предложенные критерии позволяют количественно оценить асимметричность распределения рудных нагрузок в радиальном направлении и степень загруженности периферийной (CRD1 и CRD2) и промежуточной (CRD3) зон печи железорудными материалами. Эти критерии могут использоваться как при обычном, так и при автоматизированном управлении процессом загрузки доменной печи.
ИМ выполнена в Microsoft Excel и предназначена для работы в режиме советчика оператора-технолога. В принципе, полученные модели благодаря нормированию уровней факторов могут быть использованы в качестве составной части алгоритма управления ротором в АСУ ТП «Ротор». Программа ИМ в настоящее время используется на всех ДП, где установлено РЗУ.
Система контроля профиля поверхности засыпи шихты
Назначение системы
Для РЗУ разработана система контроля профиля засыпи шихты (СКПШ) [3], предназначенная для автоматического непрерывного бесконтактного измерения уровня в нескольких точках поверхности колошника, построения и визуализации по этим данным профилей засыпи, скоростей движения шихты и загрузки и последующей оценки критериев распределения шихтовых материалов в доменной печи и стабильности её хода.Устройство СКПШ
Измерение уровня и профиля засыпи шихты осуществляется с помощью радарных измерителей уровня (РИУ) путём зондирования поверхности шихты импульсным СВЧ-радиосигналом с одновременным приёмом, обработкой и анализом отражённого сигнала. При этом используется перископический принцип измерения. СВЧ-излучение от приёмо-передающей антенны РИУ поступает на поверхность шихты через отражательный элемент (отражатель) в виде пластины, жёстко закреплённой на нижней поверхности лопасти ротора под постоянным (фиксированным) углом к продольной оси антенны РИУ. Величина этого угла определяется точкой поверхности, в которой надо измерять уровень. Использование такого принципа измерения позволило полностью вынести радар из подкупольного пространства печи, предохранив его тем самым от воздействия высоких температур, агрессивных газов и пыли, что повышает надёжность электронной части радара.РИУ является основной частью измерительного блока (ИБ). Поставляемое в комплекте с ИБ программное обеспечение (ПО) позволяет строить профили засыпи шихты, скоростей её движения и загрузки и отображать их на экране АРМ оператора. Также данные о профилях могут быть сохранены в файлах для последующей обработки данных в системе оценки критериев распределения шихты, которая также входит в состав СКПШ.
Основным элементом СКПШ является уровнемер на базе радарного дальномера УЛМ-11 (далее по тексту – радар). В этом устройстве используется частотный метод определения расстояния до поверхности объекта, характеризующийся высокой рабочей частотой и узким углом луча радара (4 градуса), что позволяет производить высокоточные измерения на небольших участках поверхности засыпи в среде колошниковой зоны доменной печи, для которой характерны запылённость и высокие температуры. Структурная схема СКПШ представлена на рис. 12 .
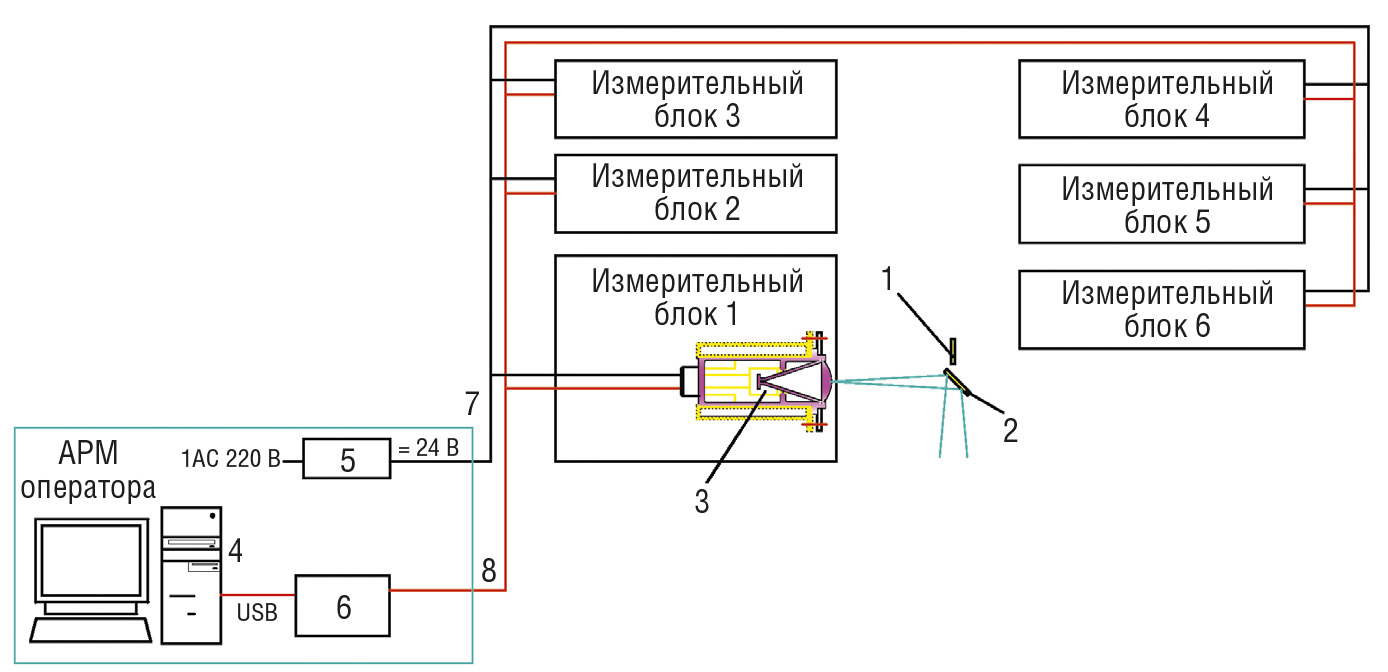
Условные обозначения: 1 – отражатель – датчик положения блока отражателей; 2 – основной отражатель блока отражателей; 3 – радарный измеритель уровня; 4 – персональный компьютер с ПО расчёта и отображения профиля и оценки критериев распределения шихты; 5 – источник питания РИУ; 6 – преобразователь интерфейса RS-485–USB; 7 – шлейф (кабель) питания РИУ; 8 – шлейф (кабель) передачи информации.
Принцип измерения профиля
Измерение уровня надо производить в момент, когда отражательный элемент (отражатель) на роторе находится напротив радара. Для определения этого момента необходим датчик положения, который должен выдать сигнал о том, что надо начинать измерение уровня.В качестве такого датчика используется специальный отражатель (отметчик), установленный под прямым углом перед парой основных отражателей по ходу вращения ротора. Расстояние от радара до отметчика всегда постоянно и известно. Фиксация этого расстояния является сигналом начала измерения профиля в двух соседних точках поверхности шихты. Величина угла наклона основных отражательных элементов определяется точками поверхности, в которой надо мерить уровень. Отметчик и два основных отражателя образуют блок отражателей. Количество блоков отражателей равно пяти, по количеству лопастей РЗУ. Каждый блок отражателей предназначен для измерения профиля в двух соседних точках поверхности засыпи, таким образом, общее количество точек измерения одним радаром по одному радиусу при полном обороте ротора – 10. Для упрощения идентификации пары точек (блока отражателей), в которых измеряется уровень, расстояния от радара до отметчика различные для каждого блока отражателей. Механическая часть СКПШ показана на рис. 13.
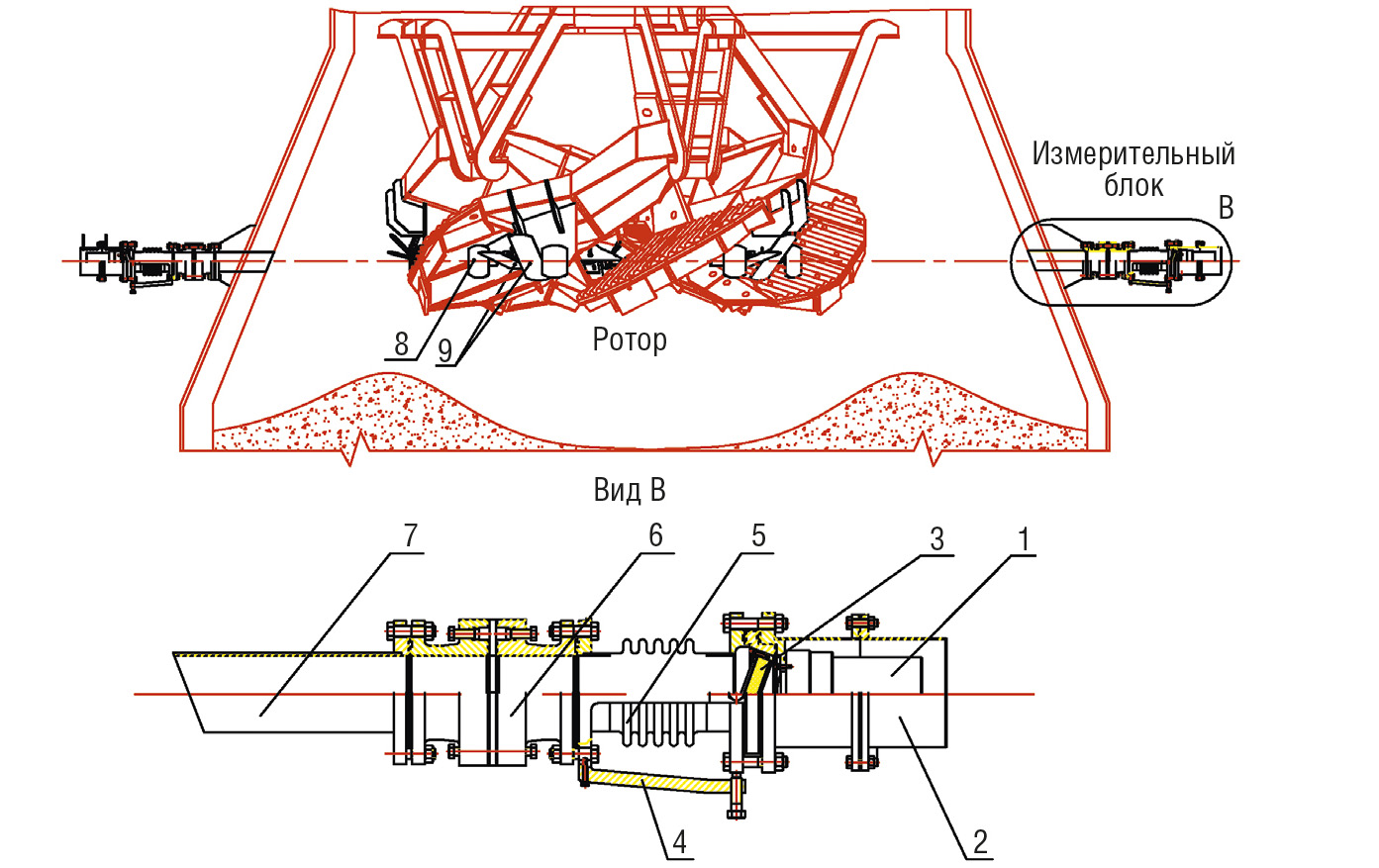
Условные обозначения: 1 – радарный измеритель уровня; 2 – кожух; 3 – защитная перегородка из радиопрозрачного материала (кварцевое стекло); 4 – центрирующее устройство; 5 – компенсатор; 6 – отсекающая задвижка; 7 – патрубок крепления в кожухе ДП; 8 – отражатель-отметчик; 9 – основной отражатель.
Расположение измерительных блоков профилемера по окружности колошника и формируемые по информации от них профили по шести радиусам (трём диаметрам) колошника показаны на рис. 14.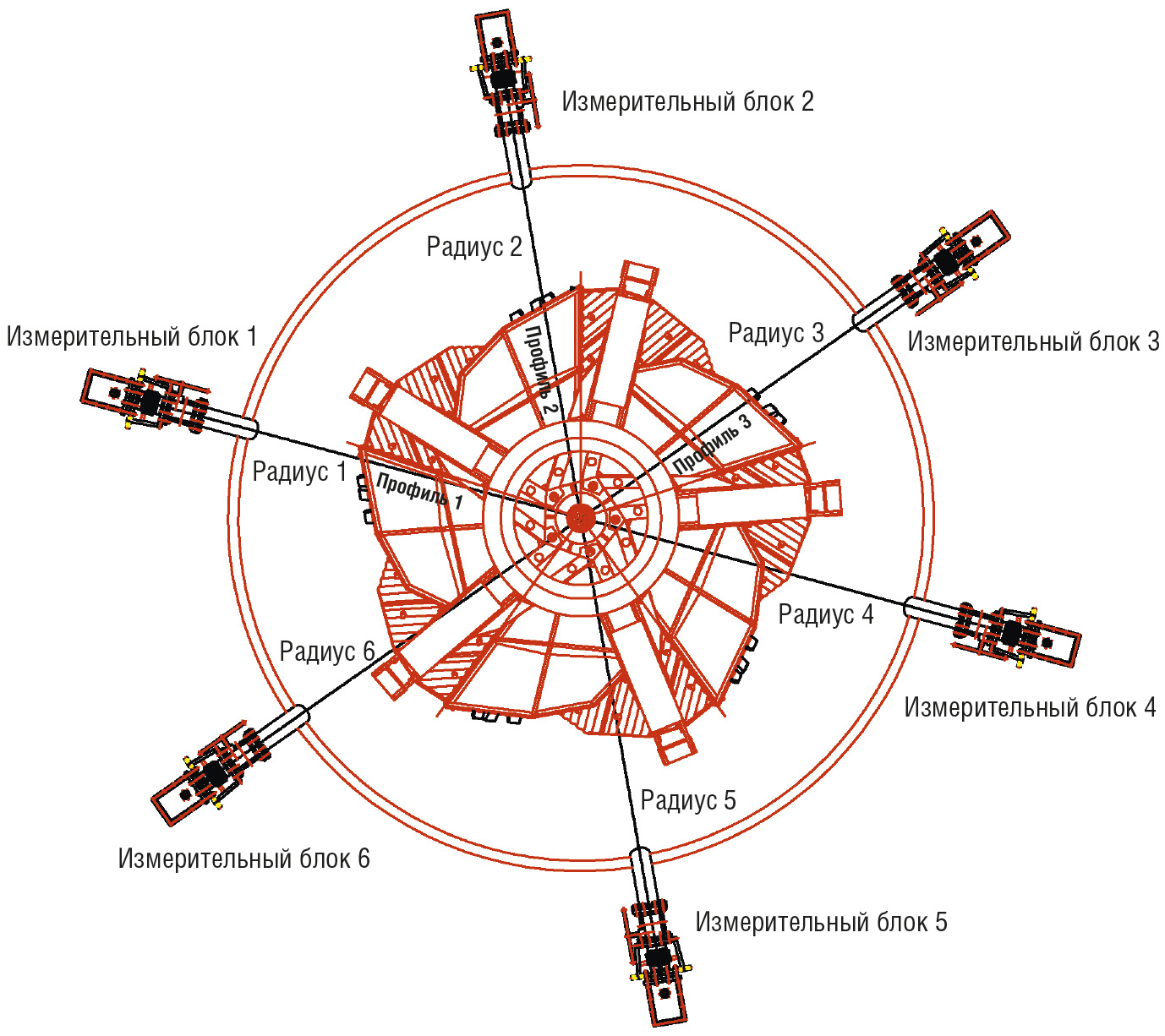
Программа расчётов и построения профилей
В СКПШ программой расчётов и построения профилей (ПРПП) для шести радиусов (трёх диаметров) поверхности колошника формируются следующие профили:- текущий (реальный);
- нормированный – для фиксированных точек, что необходимо для построения профилей скоростей опускания шихтовых материалов и профилей загрузки;
- скоростей опускания шихтовых материалов в виде графика поля скоростей;
- загрузок.
На первом экране осуществляются основные настройки программы: необходимые для описанных расчётов геометрические размеры колошниковой зоны ДП, элементов СКПШ и расстояний между ними, параметры работы и логические адреса радаров, переменные первичной обработки измерений (фильтрация) и т.п. Для исключения случайного изменения большая часть настраиваемых параметров скрыта от оператора, для доступа к ним надо ввести пароль.
На втором экране производится запуск опроса радаров и построение на соответствующем графике в реальном времени первичного профиля по данному радиусу. Профили могут строиться по любым (от 1 до 6) радиусам колошника по выбору оператора одновременно. Пример этого экрана показан на рис. 15.
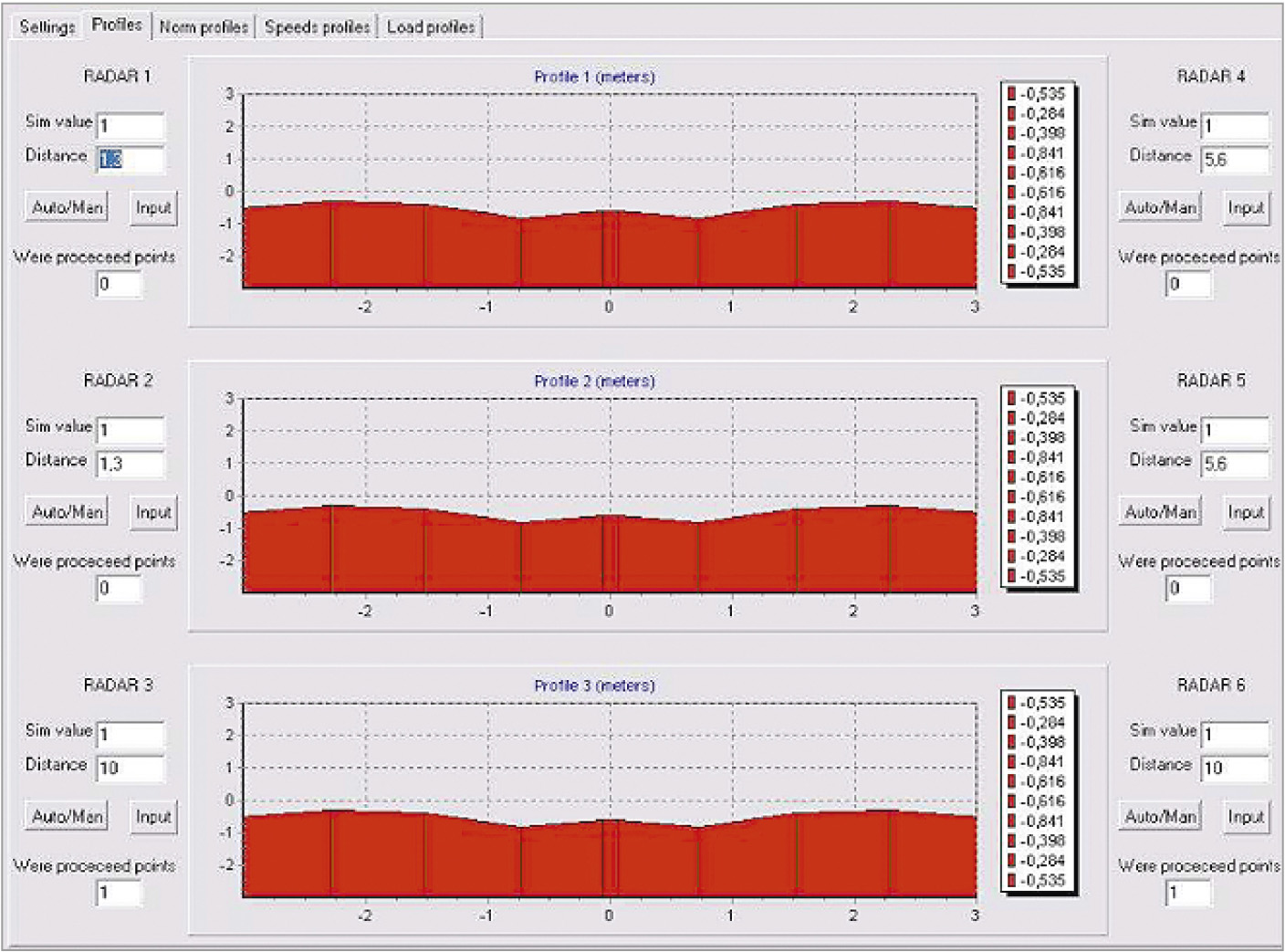
На третьем экране отображаются профили загрузки в реальном времени для фиксированных по радиусу шихты точек, расстояние которых от центра печи и количество задаётся в окне настроек, – нормированные профили. Вид этого экрана аналогичен показанному на рис 15.
На четвёртом экране визуализируются в реальном времени в виде столбчатых диаграмм векторы и поля скоростей движения шихты для фиксированных по радиусу шихты точек. Представленные на графиках данные могут быть записаны в файлы в табличном виде при нажатии оператором соответствующей кнопки. Пример этого экрана приведён на рис. 16.
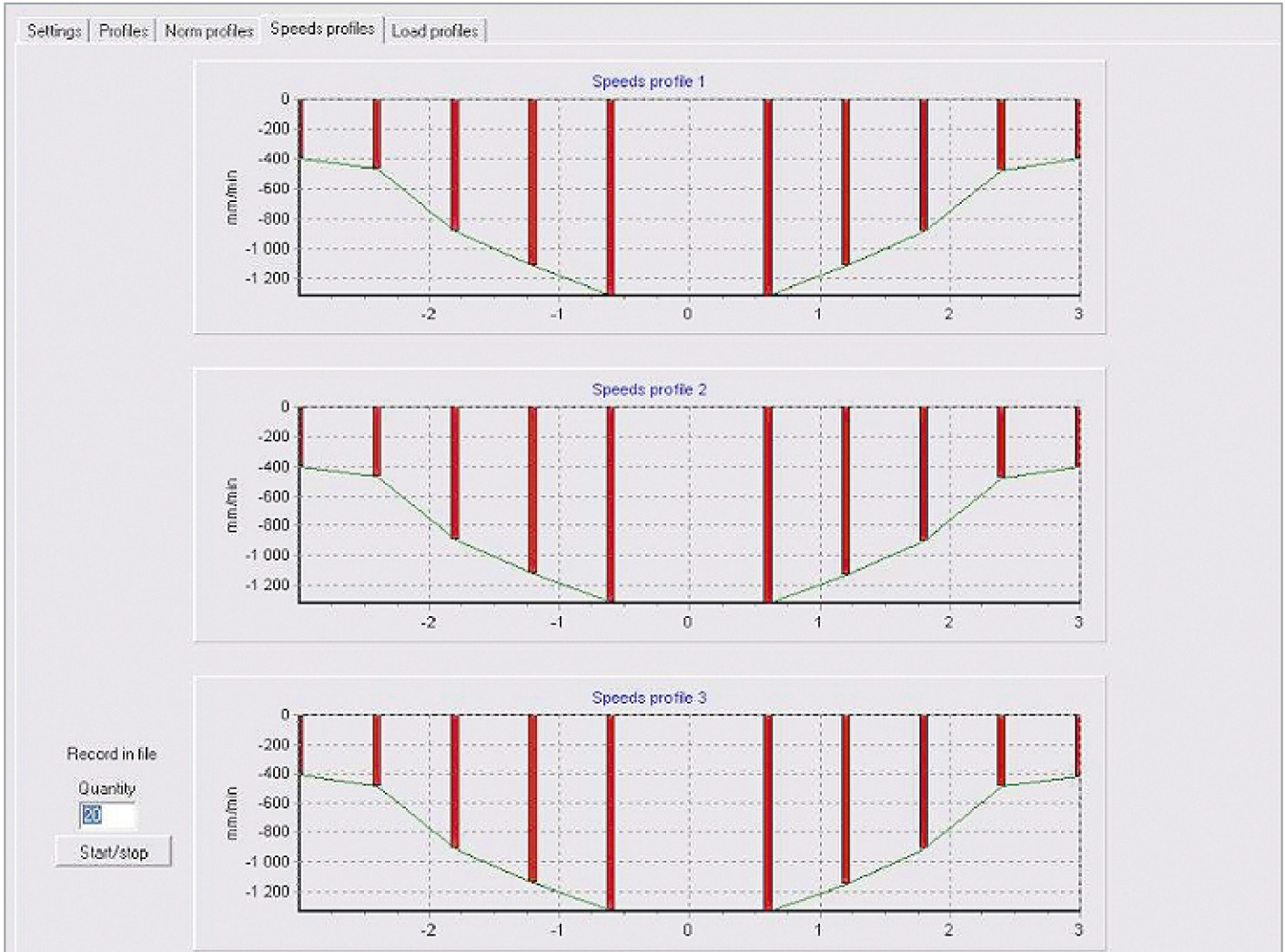
На пятом экране отображаются в реальном времени профили загрузки (слои материала) для равномерно распределённых по радиусу шихты точек. Представленные на графиках данные также могут быть записаны в файлы в табличном виде при нажатии специальной кнопки. Пример этого экрана для четырёх порций (две – агломерат, две – кокс) показан на рис. 17.
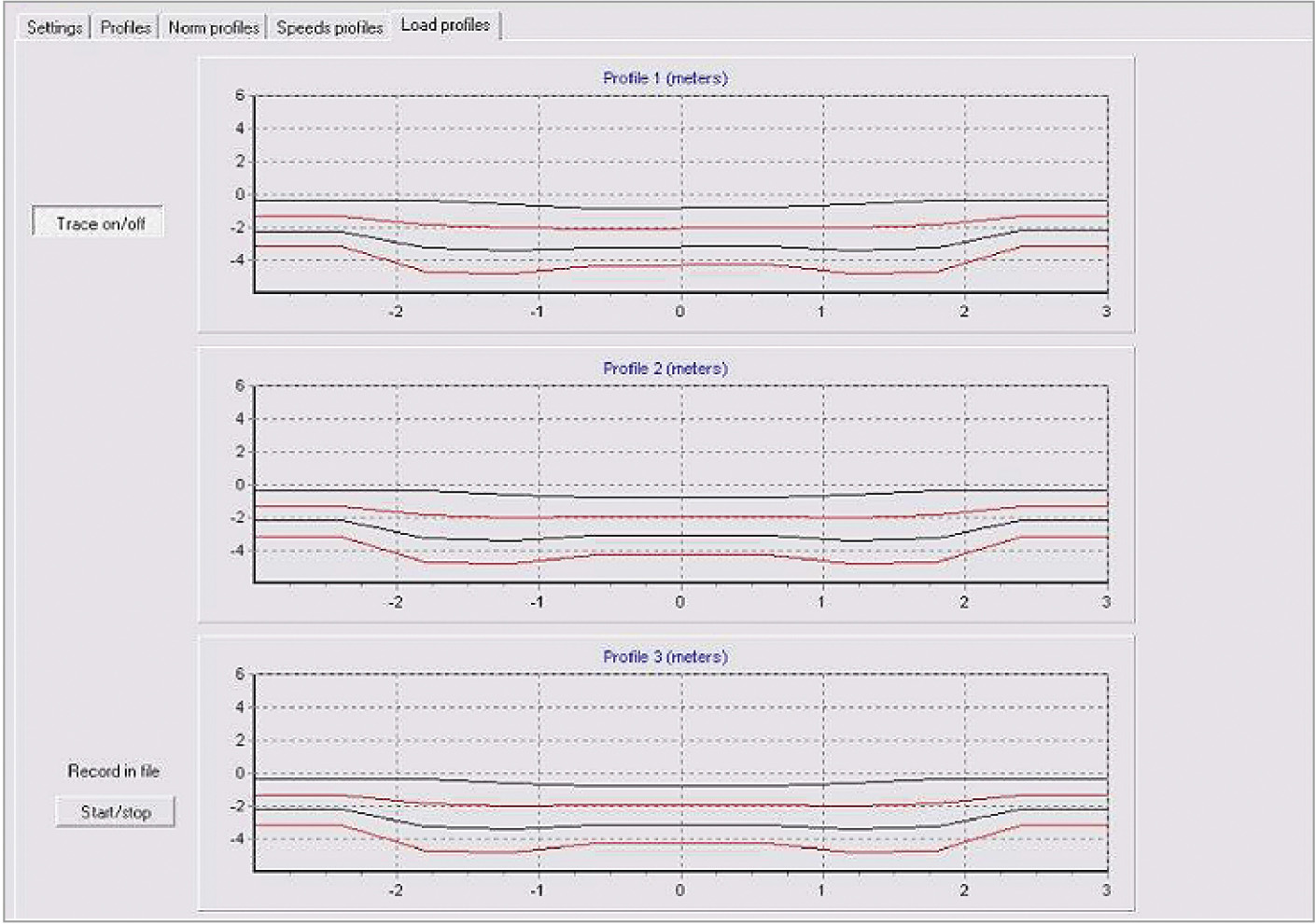
Шестой экран – дополнительные настройки. Они используются для указания и подключения файлов, в которых сохраняются данные для последующего анализа и расчёта критериев распределения рудных нагрузок и стабильности хода ДП (см. далее) и подключения интерфейса OPC для получения данных из АСУ доменной печи при построении профилей загрузки. Настройки интерфейса OPC доступны только после ввода пароля на 1-й странице.
Программа расчёта критериев радиального распределения рудных нагрузок и стабильности хода доменной печи
Алгоритмы и формулы расчёта критериев радиального распределения рудных нагрузок (CR) и стабильности хода ДП (WR) также приведены в [3]. Критерии распределения рудных нагрузок определяются в СКПШ аналогично описанным ранее в программе ИМ, с той разницей, что берутся реальные данные из файлов профилей загрузки, сформированных описанной в статье программой расчёта и построения профилей.Программа расчёта критериев распределения рудной нагрузки и стабильности хода доменной печи (далее по тексту – программа) по исходным данным о профилях загрузки (толщине слоёв материала) и профилях скоростей опускания шихты в заданных нормированных точках по шести радиусам колошника осуществляет расчёт радиального распределения рудных нагрузок на кокс и на их основе расчёт критериев радиального распределения материалов и оценку стабильности хода ДП по алгоритмам, описанным ранее.
Исходные данные формируются ПРПП и хранятся в файлах, имена и расположение которых могут быть заданы оператором (см. выше). Интерфейс программы представляет собой три экрана (вкладки), по которым оператор может выбрать необходимую функцию.
Первый экран – «Настройки». На этой странице осуществляются все настройки программы. Задаются геометрические параметры колошника, КЗ, группы зон для расчёта критериев, плотности шихтовых материалов, имена и расположение файлов, из которых читаются данные о профилях загрузок (слоёв) и скоростей опускания шихты, формируемые программой расчёта и построения профилей.
Второй экран – «Рудная нагрузка». На этом экране на основе данных о профилях загрузок производится расчёт критериев распределения (CR) по рудным нагрузкам определённых кольцевых зон и строятся графики рудных нагрузок для заданного количества циклов загрузки (руда–кокс). Пример этого окна показан на рис. 18.
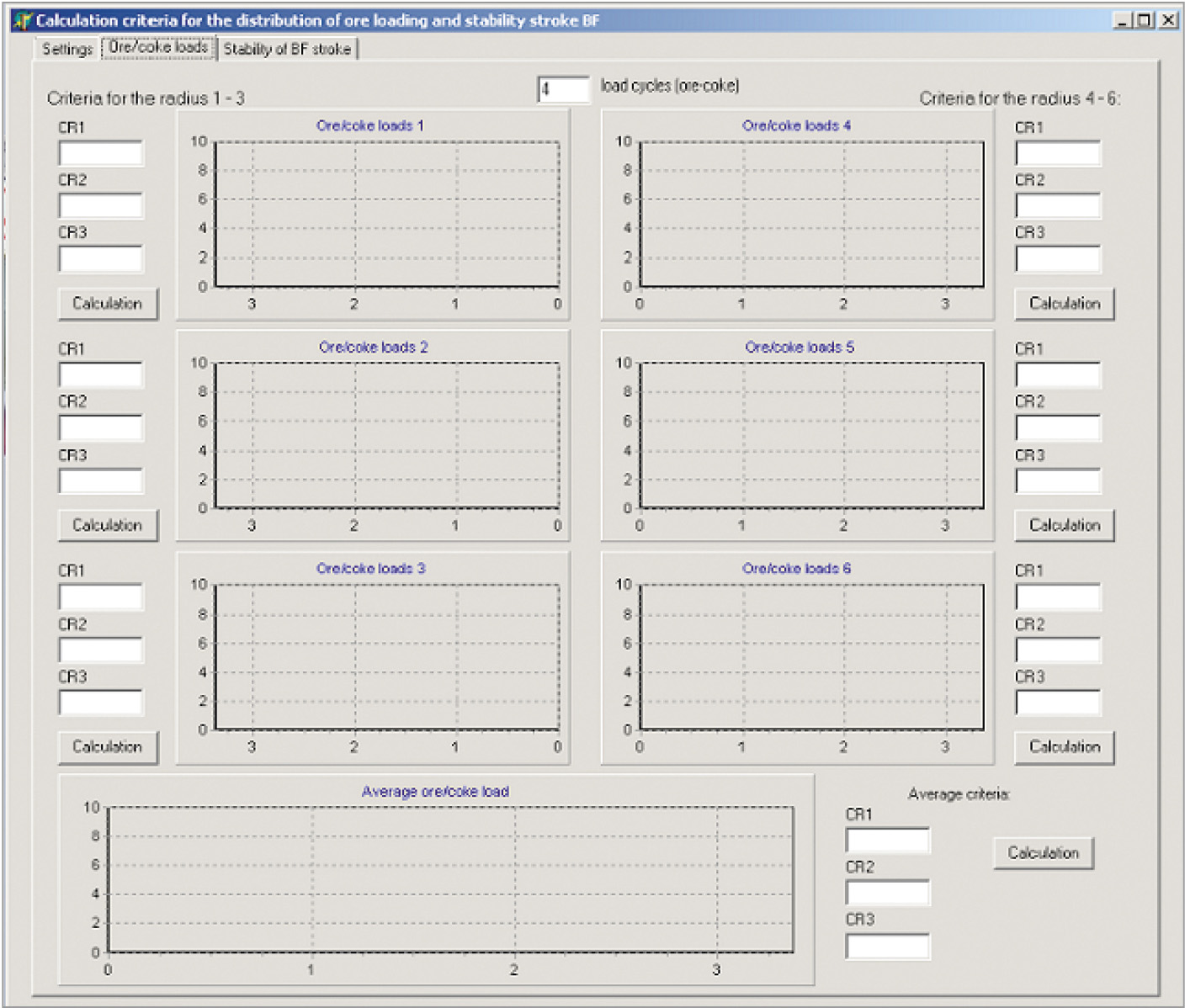
Третий экран – «Стабильность хода доменной печи». На этом экране на основе данных о профилях скоростей опускания шихты для определённых кольцевых зон рассчитываются для заданной выборки (количества профилей) и отображаются в соответствующих окнах критерии (WR), по которым оценивается стабильность хода ДП.
Запуск процедур расчёта на 2-й и 3-й страницах осуществляется нажатием кнопок «Расчёт» для любого выбранного оператором радиуса колошника и для средних значений по всем радиусам.
СКПШ является новой разработкой и проходит опытную эксплуатацию на доменной печи 2 завода Jindal в Райгархе (Индия), поэтому операторский интерфейс имеет надписи на английском языке. Эксплуатация показала такие преимущества СКПШ, как малое количество РИУ для измерения большого числа точек колошника (6 радаров – 60 точек), вынесение РИУ за пределы пространства доменной печи и связанное с этим облегчение условий их работы и простоту обслуживания. В то же время СКПШ требует большого объёма квалифицированных пусконаладочных работ, связанных с необходимостью точного позиционирования отражательных пластин и надёжного их крепления на блоках отражателей и самих блоков отражателей, чтобы исключить их смещение в процессе работы под потоком шихты, ссыпающейся с пластин ротора.
Предполагаются следующие направления дальнейшего совершенствования СКПШ:
- отработка методики позиционирования отражателей на этапе пусконаладочных работ с применением лазерных указателей-дальномеров, разработка необходимой оснастки для этих целей;
- создание конструкции отражателей как жёстких элементов конструкции ротора, возможно, образующих с ним единое целое;
- доработка измерительных блоков: по возможности применение РИУ с более тонким лучом, доработка антенны РИУ для уменьшения угла распространения радиолуча, создание методики подбора РИУ с минимальным отклонением радиолуча от вертикали;
- разработка программы более наглядного объёмного (3D) изображения профиля загрузки. •
Литература
- Абрамин Г.В., Боранбаев Б.М., Кошельников А.В., Янковский Д.А. Новая концепция загрузки доменной печи // Сталь. – 1999. – № 3.
- Боранбаев Б.М., Вакулин В.Н., Глазер Ю.М., Сиркар А. Бесконусное роторное загрузочное устройство – совершенная технология загрузки шихты // Металлург. – 2009. – № 7.
- Ткаченко В.Ф., Дятлов А.М. Система контроля профиля шихты доменных печей с роторным загрузочным устройством // Приборы и системы. Управление, контроль, диагностика. – 2016. – № 6.
Если вам понравился материал, кликните значок - вы поможете нам узнать, каким статьям и новостям следует отдавать предпочтение. Если вы хотите обсудить материал - не стесняйтесь оставлять свои комментарии : возможно, они будут полезны другим нашим читателям!