Введение и краткий обзор оборудования карьеров
Известно, что значительную долю строительных материалов (различные сыпучие фракции, известковая мука, известь, асфальтовые наполнители, щебень и т.д.) для нужд строительной индустрии поставляют многочисленные известковые карьеры, имеющие в своём составе дробильно-сортировочные фабрики (ДСФ), представляющие собой единый технологический комплекс специального оборудования для переработки добываемого известкового камня. Типовой набор оборудования включает дробильные агрегаты, просеивающие устройства (грохоты), конвейерные системы, краны-перегружатели, заборные и приёмные узлы, отвальные механизмы. К этому необходимо присовокупить системы электроснабжения и безопасности как неотъемлемые элементы нормальной эксплуатации технологического оборудования ДСФ. Что характерно для установленного оборудования и условий эксплуатации?Во-первых, жёсткая функциональная связь между отдельными агрегатами технологического комплекса, обусловленная определёнными особенностями реализации процесса переработки исходного материала (известкового камня).
Во-вторых, невероятно тяжёлые условия эксплуатации всего электротехнического оборудования ДСФ: приводных электродвигателей, различных датчиков, концевых выключателей, шкафов управления, силовых распределительных сборок, устройств контроля и безопасности. Это, как правило, значительная запылённость, перепады температур, ударные механические нагрузки, влажность и т.д.
В-третьих, постоянно присутствующая потенциальная опасность для обслуживающего персонала, несмотря на все меры безопасности, предпринимаемые соответствующими техническими службами. Это обусловлено наличием большого количества вращающихся и движущихся механизмов со значительной степенью потенциальной доступности для эксплуатационного персонала ДСФ.
И, наконец, неизбежно высокий уровень потребления электроэнергии, так как суммарная установленная мощность приводных электродвигателей даже для минимальной конфигурации оборудования ДСФ превышает 1000 кВт.
Проведённые осмотры электрооборудования на ряде известковых карьеров в Тульской и Липецкой областях в рамках работ по оптимизации потребления электроэнергии позволили обозначить конкретный круг инженерных задач по модернизации электрооборудования, средств управления и визуализации, решение которых позволит значительно повысить эффективность и безопасность производственных процессов на большинстве ДСФ в Российской Федерации. Исходя из опыта работы с карьерами центрального региона России и активного общения со специалистами из числа эксплуатационного персонала, следует отметить их высокий профессионализм и умение работать с электрооборудованием, часто достигшим пределов морального и физического износа. Поэтому данная статья не преследует цель научить персонал ДСФ «как надо», а лишь достаточно деликатно ориентирует и указывает направления для конструктивных размышлений.
О целях автоматизации ДСФ
Учитывая характерные особенности технологического процесса и условий эксплуатации оборудования ДСФ, автоматизация призвана обеспечить:- максимальную визуализацию фрагментов процесса запуска, работы и останова всех агрегатов ДСФ;
- контроль режимов работы силового электрооборудования агрегатов ДСФ: роторных, щековых, конусных, молотковых дробилок, грохотов, сортировочного оборудования и т.д.;
- фиксацию и отображение сбойных (аварийных) ситуаций в работе оборудования ДСФ во время запуска, рабочего режима и останова;
- контроль наличия исходного состояния элементов оборудования ДСФ, представляющих наибольшую опасность для эксплуатационного персонала;
- первичную обработку, запись, хранение и наглядную визуализацию текущих и архивных данных о работе технологических агрегатов ДСФ: времени работы и простоя, количества и причин сбойных, аварийных ситуаций и других параметров, которые позволяют оценивать эффективность производственного процесса и проводить ретроспективный анализ производства в целом;
- учёт, накопление и архивирование информации о показателях наработки и технического состояния оборудования ДСФ, данных о режимах потребления электрической энергии по временам года;
- реализацию передачи статистической информации о работе ДСФ на более высокий уровень управления горным производством для планирования профилактического, текущего и капитального ремонта технологического оборудования, а также для интеграции в общую информационную систему производства.
Разработка типовой структуры программно-технических средств управления оборудованием ДСФ
Решение разработать типовую структуру программно-технических средств основывалось на результатах проведённых обследований комплекса технологического оборудования ДСФ в центральном регионе РФ, в ходе которых были проанализированы состав задействованного оборудования, используемые технологические схемы, существующий уровень автоматизации производства, номенклатура работающих программно-технических средств управления, необходимость или отсутствие потребности в организации системы сбора и обработки информации о состоянии эксплуатируемого оборудования. Инициирующим фактором в создании надлежащей конфигурации системы управления наряду с коммерческим интересом являлось наличие по состоянию на осень 2014 года широкой гаммы различных модулей (функциональных, коммуникационных, интерфейсных) в продуктовых линейках ряда известных производителей, использование которых, несомненно, обеспечит удачное решение производственных задач. Кроме этого, можно было учесть определённый опыт разработки программно-технологических средств управления отдельными агрегатами и различными структурами ДСФ. Что должно отличать систему управления как типовой комплекс программно-технических средств?- Безусловно, высокая надёжность для далеко не тепличных условий эксплуатации (пыль, колебания температур и вибрация для некоторых элементов системы).
- Возможность размещения аппаратных фрагментов системы (особенно силовой составляющей) в стандартных малогабаритных строительных конструкциях с использованием новейших вариантов щитового и модульного оборудования.
- Обеспечение высокой ремонтопригодности и минимального времени восстановления работоспособности системы управления применительно к условиям производственного процесса.
- управление предприятием и производственным комплексом (диспетчер ДСФ);
- управление техпроцессом переработки исходного сырья (оператор технологического комплекса ДСФ);
- контроль технологических параметров, непосредственное управление исполнительными устройствами.
Назначение и функции системы
Нижний уровень (рис. 1) – уровень станционного и полевого оборудования.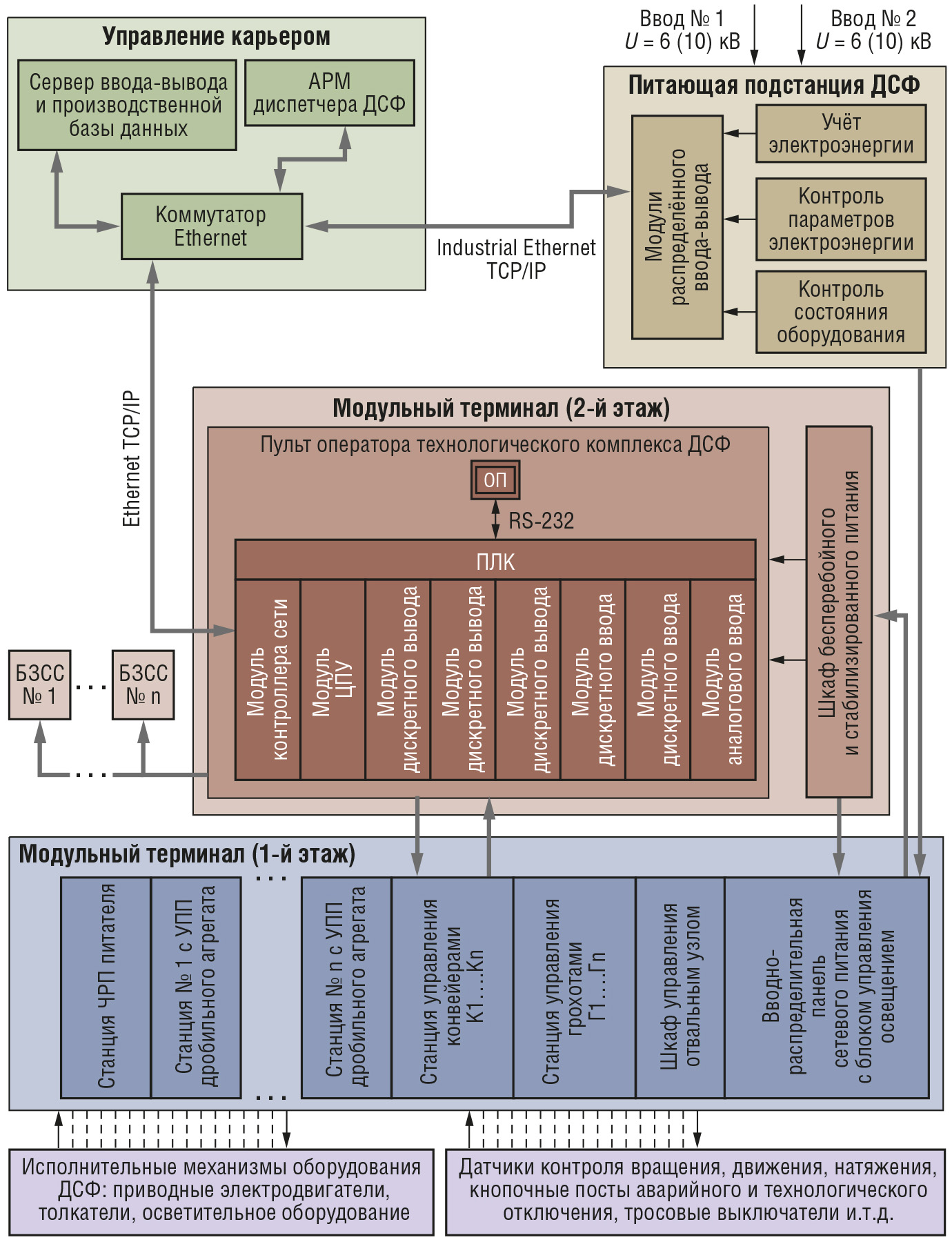
Условные обозначения: ЧРП – частотно-регулируемый привод; УПП – устройство плавного пуска; ОП – операторская панель; ПЛК – программируемый логический контроллер; БЗСС – блок звуковой и световой сигнализации.
Станционный комплекс оборудования конструктивно представлен в виде модульного терминала (рис. 2), на первом этаже которого размещены станции управления отдельными агрегатами ДСФ, на втором этаже – пульт оператора технологического комплекса со шкафом бесперебойного питания.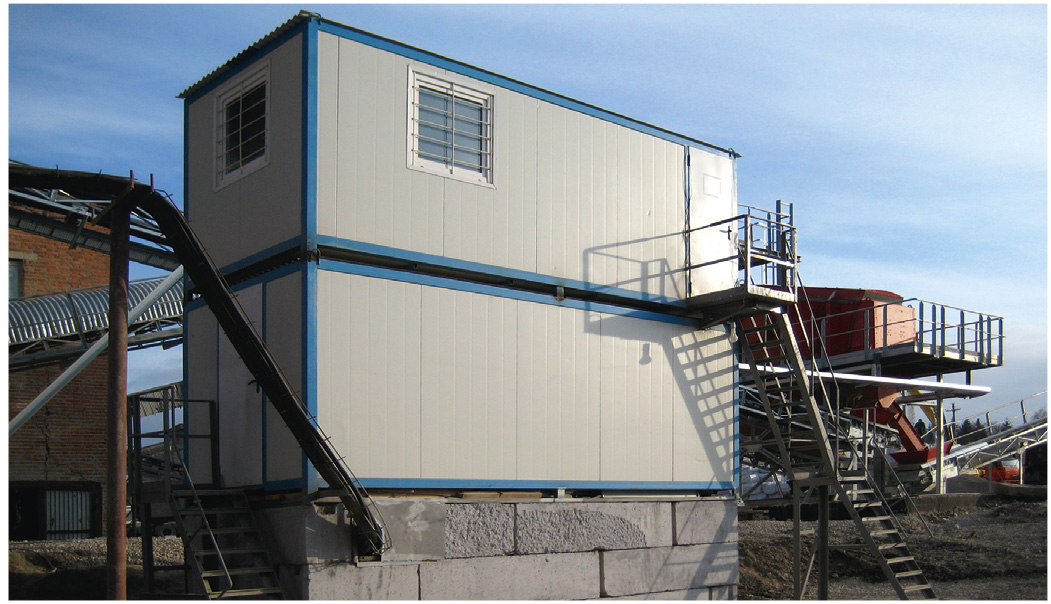
Приводные электродвигатели, толкатели, осветительное оборудование, датчики контроля вращения, движения и натяжения, кнопочные посты аварийного и технологического отключения, тросовые выключатели – всё, что составляет полевое электрооборудование, расположенное на удалении от 200 до 400 м, подключается к станциям управления модульного терминала с помощью линий силовых и контрольных кабелей. Таким образом реализована структура централизованного управления оборудованием, распределённым по территории ДСФ и находящимся непосредственно в зоне переработки известковых фракций, что даёт очевидный выигрыш в эксплуатационных затратах на техническое обслуживание, капитальных вложениях и в повышении надёжности работы силового электрооборудования станций управления.
Заметим, что на начальном этапе проектирования управляющего комплекса рассматривался распределённый вариант архитектуры системы, в котором станции управления размещались бы в непосредственной близости от соответствующего агрегата, а связь с контроллером пульта агрегата осуществлялась бы через систему распределённого ввода-вывода с помощью полевых шин PROFIBUS DP или Modbus RTU. Несмотря на очевидные достоинства такого варианта в части значительного сокращения количества контрольных и силовых кабелей, стоимость станций управления и, соответственно, требования к их исполнению существенно возрастали, так как необходимо учитывать:
- обеспечение степени защиты оболочек до уровня IP65;
- оборудование шкафов вентиляцией с очисткой воздуха, кондиционированием и термостатированием, при этом затраты на кабели для подачи силового питания от питающей подстанции к станциям даже могут увеличиваться.
Пульт оператора находится на втором этаже модульного терминала и выполнен на базе унифицированного корпуса (рис. 3).
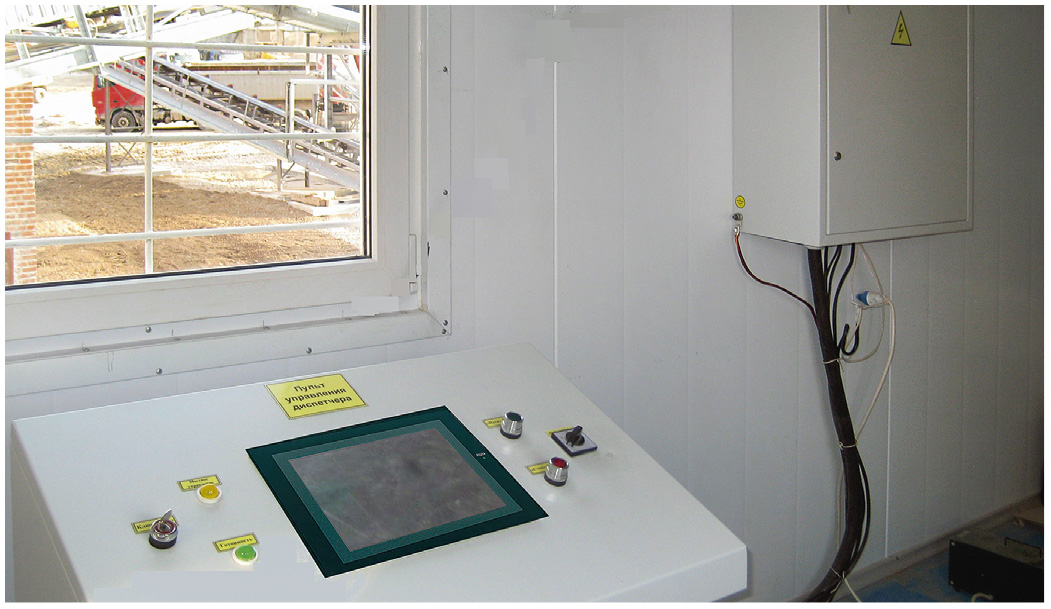
Функции пульта оператора включают:
- управление оборудованием ДСФ в ручном (местном), полуавтоматическом и автоматическом режимах работы;
- формирование внешнего звукового и светового оповещения перед запуском ДСФ во всех режимах управления через блоки звуковой и световой сигнализации (БЗСС);
- инициализацию и последующий контроль запуска электроприводов дробильных агрегатов с помощью станций управления с устройствами плавного пуска (УПП);
- отображение мнемосхемы оборудования ДСФ в статическом и динамическом (запуск/останов) режимах работы;
- визуальный контроль наличия или отсутствия движения лент конвейеров;
- фиксацию останова оборудования ДСФ с выдачей соответствующих сообщений в нормальном и аварийном режимах работы;
- обеспечение системы взаимных блокировок агрегатов ДСФ в соответствии с технологической схемой;
- контроль работы частотно-регулируемого электропривода питателя и синхронизацию режима его работы с общим технологическим ритмом ДСФ в режиме автоматического управления;
- ведение архива рабочих и аварийных остановов оборудования ДСФ;
- поддержку коммуникационной связи с АРМ диспетчера ДСФ и сервером производственной базы данных по сети Industrial Ethernet TCP/IP.
Основные функции:
- питание ПЛК, операторской панели;
- формирование стабилизированных напряжений переменного тока для питания оперативных цепей станций управления, вводно-распределительной панели, блока управления освещением ДСФ;
- обеспечение бесперебойного питания оборудования пульта оператора.
- блоки управления агрегатами;
- диспетчер координации процесса запуска и останова технологической линии ДСФ;
- модуль системы безопасности и формирования звукового сопровождения в соответствии с требованиями «Единых правил безопасности при разработке месторождений полезных ископаемых открытым способом» 2003 года и положений инструкции ПОТ Р М-016-2001;
- программу тестирования и контроля исходного состояния оборудования ДСФ.
Программное обеспечение уровня управления ДСФ состоит из набора программ АРМ диспетчера и сервера ввода-вывода. Информационное обеспечение АРМ диспетчера включает наборы видеокадров для организации пользовательского интерфейса и наглядного отображения информации о ходе производственно-хозяйственной деятельности карьера, журналы событий в системе управления, блок учёта количества нарабатываемой продукции и ресурсов, программу дистанционного мониторинга параметров и количества потреблённой электроэнергии, а также состояния электрооборудования питающей подстанции (рис. 1). Сервер ввода-вывода и производственной базы данных в соответствии с проектом выполнен в конструктиве одного дублированного системного блока (фактически два системных блока, в каждом из них сервер ввода-вывода и сервер базы данных), в котором содержится архив системы управления ДСФ. Кроме этого, сервер ввода-вывода хранит информацию о конфигурации (топологии) существующей сети для реализации связи сервера с ПЛК пульта управления, АРМ диспетчера и модулями распределённого ввода-вывода питающей подстанции. Следует отметить то обстоятельство, что технологическое управление агрегатами ДСФ в автоматическом режиме производится без переноса даже части алгоритмов на верхний уровень, то есть на АРМ диспетчера. Это позволяет обеспечить надёжное функционирование комплекса программно-технических средств управления оборудованием ДСФ в случаях, когда по каким-то причинам происходит сбой в работе подсистемы уровня управления предприятием.
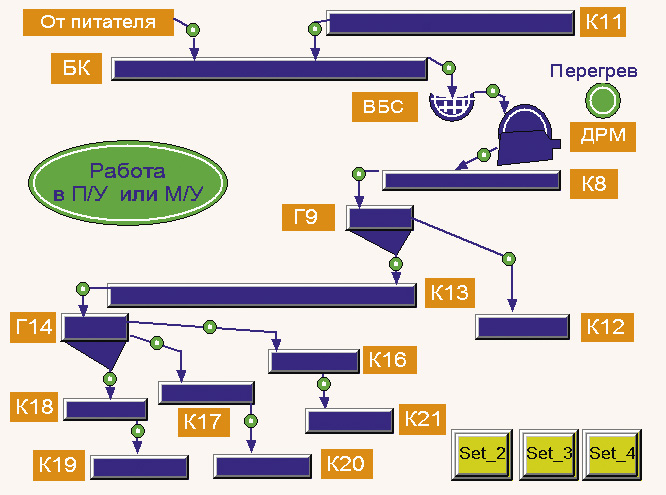
Условные обозначения: ДРМ – дробильная машина; К8, К11, К12, К13, К16, К17, К18, К19, К20, К21 – конвейеры технологических линий; Г9, Г14 – грохоты; БК – бутовый конвейер; Set_2, Set_3, Set_4 – кнопки перехода к служебным экранам; ВБС – вибростол.
В качестве примера на рисунке 4 приведён вид основного рабочего экрана пульта оператора Гуровского карьера, который появляется после включения системы с помощью ключа-бирки и отражает:- мнемосхему ДСФ, близкую по мнемонике к реальной технологической схеме, описанной в руководстве по эксплуатации системы управления;
- состояние агрегатов ДСФ (включено, выключено, авария).
Используемые технические и программные средства
Прежде чем перейти к изложению информации об используемых программно-технических средствах, стоит сказать, что по различным объективным причинам (в основном из-за отсутствия средств для финансирования программ модернизации) пилотный проект был реализован пока только на двух карьерах в Тульской и Липецкой областях, при этом значительная часть комплектующих использовалась, исходя из наличия их на складе. В частности, пульт оператора выполнен на базе семейства модулей ПЛК серии CJ1 фирмы Omron: ЦПУ CJ1M-CPU23, модуль дискретного ввода постоянного тока CJ1W-INT01 – 3 шт., модуль дискретного вывода («сухой» контакт) CJ1W-OC211 – 2 шт.,модуль аналогового ввода CJ1W-AD081-V1 – 1 шт., модуль контроллера сети с портом 1×100Base-TX CJ1W-ETN21 – 1 шт. В качестве операторской панели используется программируемый терминал (сенсорная панель) NS10 с цветным экраном TFT 10″.
Разработка программы управления технологическим комплексом ДСФ производилась в среде интегрирован-ного пакета CX-One c помощью фирменных инструментальных программ CX-Programmer для ПЛК и NS Designer для операторской панели.
В настоящее время рассматривается возможность корректировки проектно-конструкторской документации по переводу пульта управления на ПЛК FASTWEL I/O c использованием сенсорных панелей Weintek. Побудительными факторами к проведению такой модернизации служат следующие особенности указанного оборудования [2, 3].
- Контроллеры FASTWEL I/O – продукция отечественного производства, что в современных условиях упрощает решение целого ряда вопросов, связанных с поставкой, гарантийным обслуживанием, ремонтом, заменой и т.д.
- Наличие исчерпывающей эксплуатационной документации на русском языке.
- В комплект поставки контроллера включаются адаптированная среда CoDeSys 2.3 и необходимые аксессуары программирования ПЛК.
- Наличие модулей дискретного ввода с контролем целостности цепей подключённых датчиков, а также модулей приёма сигналов термометров сопротивления с функцией обнаружения обрыва и короткого замыкания в измерительных цепях.
- Существование для некоторых модификаций ПЛК (CPM 711, CPM 712, CPM 713) поддержки интеграции с GSM- и GPS-приёмниками за счёт обновлённого системного программного обеспечения и пакета адаптации CoDeSys 2.3 для FASTWEL I/O.
- Коммуникационные возможности последних модификаций контроллеров, например CPM 713, позволяют создавать распределённые системы сбора данных и управления без центрального (главного) компьютера, в качестве которого обычно используется промышленная вычислительная система. Это позволит подключать удалённые узлы управления и сбора информации при расширении числа технологического оборудования ДСФ без радикальных мероприятий по модернизации системы.
APM диспетчера ДСФ является клиентской рабочей станцией для сервера, на котором в качестве приложения визуализации и сбора данных установлен программный пакет SIMATIC WinCC 6.0. Набор возможностей, представленных системой WinCC, традиционен для современных SCADA-систем: визуализация технологического процесса и его параметров, оповещение диспетчера ДСФ об аварийных и нештатных ситуациях на работающем оборудовании, архивирование текущих данных о работе карьера, сбор данных об уровне энергопотребления и состоянии силовой схемы питающей подстанции.
Отметим, что в рамках модернизации комплекса управляющих средств планируется разработка проекта АСУ карьера на основе SCADA-системы GENESIS32, так как пакет служит наиболее приемлемым вариантом для этого приложения, являясь простой в применении системой, основанной на использовании открытых стандартов и адаптированной для работы на базе ОС Microsoft Windows.
Учёт электроэнергии, контроль параметров системы электроснабжения и состояния оборудования питающей подстанции реализуются на АРМ диспетчера ДСФ по сети Ethernet с помощью системы распределённого ввода-вывода, выполненной на основе модулей сбора данных фирмы Advantech серии ADAM-6000:
- ADAM-6151E1 – модуль дискретного ввода с 16 каналами с гальванической изоляцией для сетей реального времени;
- ADAM-6117E1 – модуль изолированного аналогового ввода на 8 каналов.
Одни из самых ресурсоёмких элементов системы – станции управления агрегатами ДСФ. Станция питателя, важнейший элемент системы управления, выполнена на базе преобразователя частоты (ПЧ) CIMR-E7Z40750B фирмы Omron мощностью 75 кВт в стандартной оболочке напольной конструкции (рис. 5, 6).
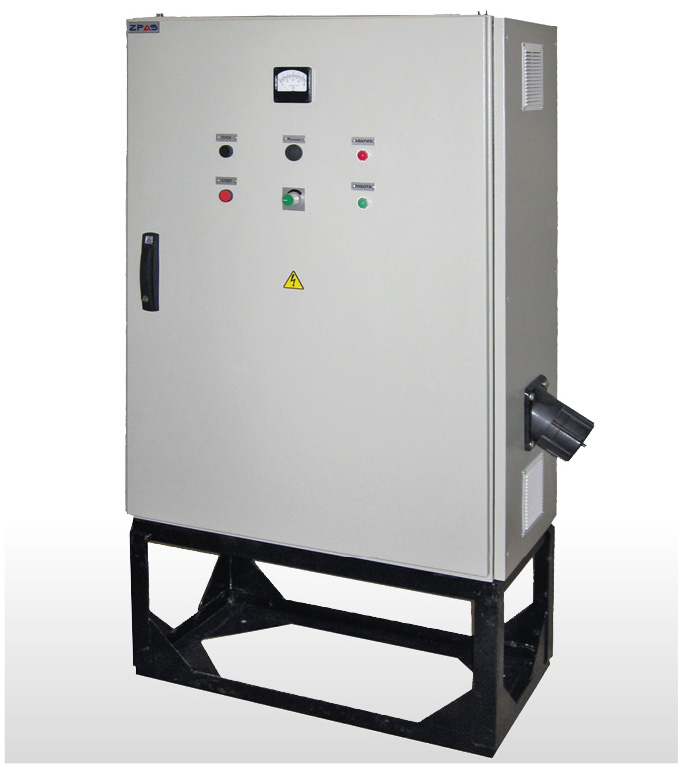
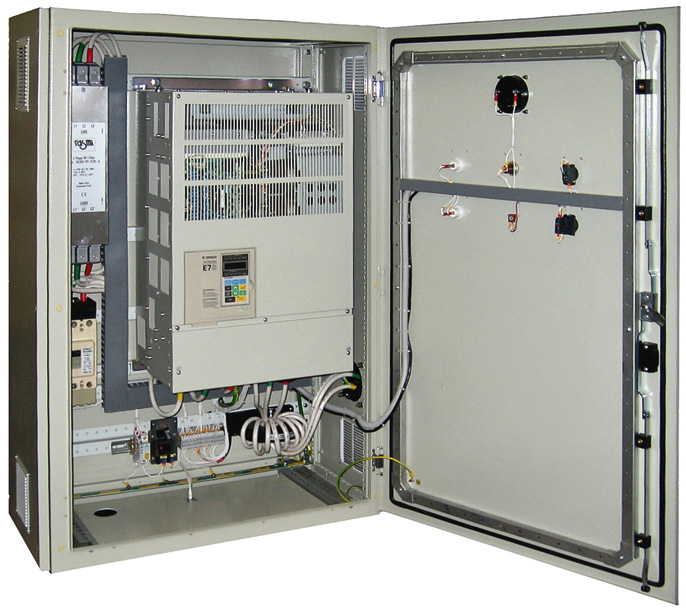
В связи со снятием с производства серии Е7 последующие станции будут изготавливаться на основе серии А1000 Omron либо аналогичных по возможностям ПЧ фирмы SIEMENS, например, известной серии MIDI MASTER 440.
Кроме этого, в связи с высокими требованиями по надёжности, предъявляемыми к станциям управления, около 90% используемой пускорегулирующей и защитной аппаратуры относится к изделиям фирмы SIEMENS: автоматические выключатели, контакторы, реле серии SIRIUS (3RA1/3RA7, 3RB, 3RE, 3RF2, 3RH, 3RN, 3RP и т.д.), компактные пускатели SIRIUS 3RA6, аппараты контроля и управления, элементы системы SIEMENS Safety Integrated, устройства плавного пуска SIRIUS 3RW и SIMOCODE 3UP. Несмотря на несколько завышенные затраты на комплектующие изделия, почти двухгодичный период эксплуатации станций на Гуровском карьере подтвердил целесообразность использования элементной базы фирмы SIEMENS при сборке устанавливаемого в шкаф электрооборудования для достаточно жёстких условий эксплуатации.
Заключение
По результатам опыта проектирования и эксплуатации комплекса программно-технических средств на двух карьерах по добыче и переработке известкового камня необходимо:- рассмотреть целесообразность и возможность частичной децентрализации управления некоторыми наиболее удалёнными агрегатами ДСФ на основе использования систем беспроводной связи и полевых шин;
- упростить процедуру изменения порядка включения агрегатов в программе ПЛК пульта управления силами оперативного персонала в случае вынужденных и внезапных ротаций технологической схемы с сенсорной панели терминала через специальную функцию с административным паролем;
- разработать комплекс мер по повышению эффективности диагностики повреждений и сокращению времени на локализацию и ликвидацию аварийных ситуаций;
- продолжать работу по совершенствованию алгоритмов и программ управления оборудованием ДСФ с целью оптимизации уровня потребляемой электроэнергии. ●
Литература
- И. Лопухов. Коммуникационные технологии умного предприятия в рамках концепции Индустрия 4.0 и Интернета вещей // Современные технологии автоматизации. – 2015. – № 2.
- А. Локотков. FASTWEL I/O: развитие продуктовой линейки. Часть 1 // Современные технологии автоматизации. – 2014. – № 3.
- А. Локотков. FASTWEL I/0: Развитие продуктовой линейки. Часть 2 // Современные технологии автоматизации. – 2014. – № 4.
Если вам понравился материал, кликните значок - вы поможете нам узнать, каким статьям и новостям следует отдавать предпочтение. Если вы хотите обсудить материал - не стесняйтесь оставлять свои комментарии : возможно, они будут полезны другим нашим читателям!