Введение
Условия, возникающие вследствие образования шва, указывают на деформацию шва (рис. 1), к примеру, это нагревание, остывание, внутреннее напряжение и т.д.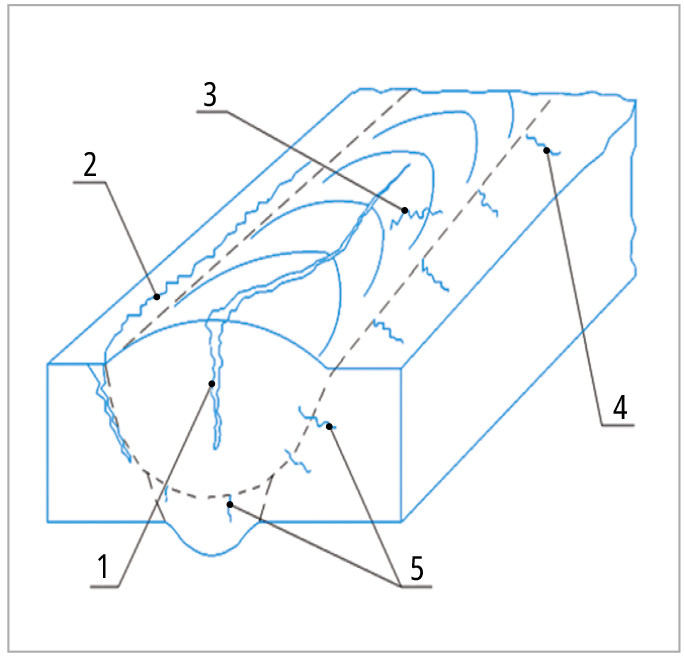
По размещению сварные трещины делятся на несколько видов:
- в самом шве: продольные – зачастую длинные (1); поперечные – обычно короткие (3);
- в околошовной зоне: продольные – тонкие и длинные (2); поперечные (4);
- внутри материала – поперечные (обычно короткие) (5).
Наиболее трудным фактором считается выявление внутренних трещин, так как протяжённость этих трещин может быть небольшой, и зачастую они могут образовываться как на поверхности, так и внутри металла.
С помощью внедрения автоматизации в производство можно исключить возможные варианты образования трещин посредством:
- визуального обследования – проис-ходит совместно с использованием увеличительных устройств;
- цветной дефектоскопии;
- магнитного метода – измерение иска-жения магнитных волн;
- ультразвукового метода;
- радиационного метода.
Существуют устройства, которые работают без участия человека, они делятся на два класса: сварочные автоматы и автоматические системы (регуляторы).
Автоматические системы могут изменять физические величины по заданным законам в технических приборах или процессе без участия оператора-сварщика или не изменять вовсе.
Авторы пришли к выводу, что внедрение автоматизации сварных процессов способствует улучшению качества продукции (снижение образования трещин), наиболее экономичному потреблению материала, а также возможности расширения производства.
Активно применяются методы контроля автоматизации, введённые в производство: магнитный, ультразвуковой, радиационный и т.д.
Например, радиационный метод позволяет определить дефекты небольшого размера, а ультразвуковой – наоборот. Практика доказывает, что определённый метод автоматизации позволяет более надёжно выяснить качество сварного соединения и предотвращает образование дефектов.
Виды радиационного контроля:
- рентгеновская дефектоскопия (рент-геновские лучи);
- гамма-дефектоскопия (гамма-лучи). Недостатком является наименьшая чувствительность выявления дефектов в швах тоньше 50 мм.
- Обнаружение дефектов в паяных соединениях.
- Определение плотности сплавов.
- Проведение контроля соответствия изделий нормативным требованиям.
Тем не менее дефекты сварных швов на полученных рентгеновских снимках проявляются в виде тёмных пятен. То есть, проходя через снимки, рентгеновские лучи теряют первоначальную интенсивность.
Исходя из всего этого, необходимо учесть некоторые аспекты:
- рентгеновский контроль не применяется при наличии жидкой среды в резервуаре;
- во время контроля необходимо приостановить производственный процесс и освободить площадку от посторонних людей;
- рентгеновский контроль осуществляется только при двустороннем доступе к исследуемому объекту.
- определить качественно-количественную оценку всех видов дефектов, определяя степень угрозы этих дефектов;
- установить соответствие объекта обследования требованиям нормативно-технической документации;
- обеспечить безопасную эксплуатацию ответственных трубопроводов и предотвратить вероятные аварии.
- вред для здоровья человека (облучение);
- плохо выявляются дефекты, находящиеся под углом от 7 до 12°.
УЗК наиболее востребован для контроля прочности стыковых сварных соединений. Кроме этого, он достаточно часто используется в процессе строительства или реконструкции жилых домов и зданий коммерческого назначения. С помощью этого метода можно проверить пластик, стекловолокно и т.д. Активно применяется в авиационной, химической промышленности и т.д.
Плюсы УЗК заключаются в низкой себестоимости, работе в полевых условиях, целостности детали. Аппаратура, предназначенная для ультразвукового контроля, включает в себя пьезоэлектрические преобразователи, электронный блок и вспомогательные устройства.
Положительным фактором УЗК является способность совершенно точно определять отличие данных типов дефектов друг от друга, что гарантирует надёжность данного метода.
Предполагаемое решение
Предлагаемая авторами концепция модернизации уже существующего способа обнаружения и распознавания дефектов на основе индикаций ультразвуковой томографии выглядит следующим образом: начальными данными с целью выполнения количественной оценки дефектов сварных соединений считаются трёхмерные воксельные данные, получаемые вследствие перестройки изображения объёма сварного шва по методу DFA.Каждый элемент объёма характеризуется отражающей или рассеивающей способностью эквивалентной интенсивности эхо-сигналов от заданного элемента объёма. Итак, в результате процедуры реконструкции за счёт положительной интерференции амплитуд эхо-сигналов происходит когерентное накопление совпадающих по фазе значений в элементах объёма, содержащих несплошности.
Разрешающая способность ультразвуковой томографии ограничена длиной волны ультразвука, поэтому несплошности, расположенные на расстоянии менее длины волны друг от друга, будут отображены как одна индикация, а геометрическая неточность при определении пространственных размеров дефектов может равняться длине волны ультразвуковых колебаний. Особенности объекта контроля будут оказывать существенное влияние на предполагаемые результаты инспекции.
Так как УЗК является относительным методом, то для достоверной оценки важно предварительно получить информацию о представлении томографических индикаций в случае обнаружения определённого типа несплошностей.
Обработка и хранение данных осуществляется при помощи персонального компьютера.
Лабораторная установка контроля представлена на рис. 2.
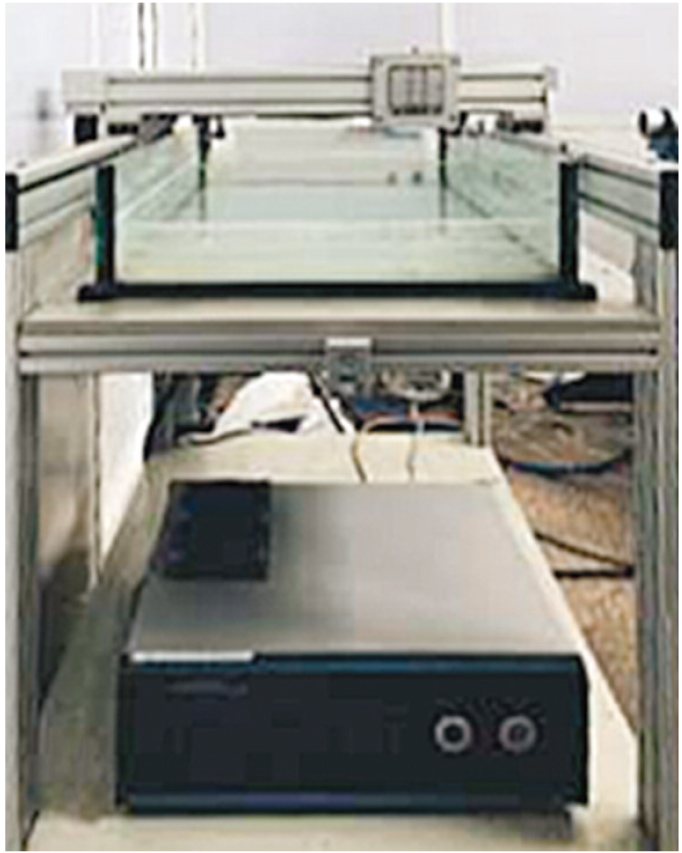
Чтобы осуществить различные варианты управления сварочных процессов и оборудования, существует большое число типов архитектурных аппаратных средств:
- контроллеры автономные – спецоборудование общего применения (автоматы и полуавтоматы для дуговой сварки и т.д.);
- линейные и системные – системы технического управления с распределённой вычислительной мощностью и распределённой конструкцией в качестве локального регулятора (концепции управления установками, робототехникой).
Заключение
Подводя итог работы, можно сделать следующие выводы, относящиеся к внедрению автоматизации управления технологическим процессом и модернизации способов обнаружения трещин на сварочных швах.- Главной частью методики УЗК является определение подходящих параметров метода и аппаратуры для проведения эффективного сканирования посредством ультразвуковой томографии. Её реализация достигается путём расчёта и обоснования каждого из параметров, потенциально влияющих на результаты сканирования.
- Автоматизированная система управления технологическим процессом предполагает такие важные достоинства, как: экономия сырья и рабочей силы, улучшение качества изготавливаемого продукта, обеспечение защиты здоровья человека, а также научно-технический прогресс. ●
Литература
- Дефектация сварных швов и контроль качества сварных соединений: учебник для студ. учреждений сред. проф. образования / В.В. Овчинников. 3-е изд., стер. М.: Издательский центр «Академия», 2017. 224 с.
- Алешин Н.П., Щербинский В.Г. Контроль качества сварочных работ: учеб. пособие. М.: Высш. шк., 1986. 206 с.
- Троицкий В.А., Радько В.П., Овчинников В.К. Дефекты сварных соединений и средства их обнаружения. М.: Изд-во МГИУ, 2006. 164 с.
- Чернышов Г.Г. Сварочное дело: Сварка и резка металлов: учебник. 7-е изд., стер. М.: Изд. центр «Академия», 2012. 496 с.
- Контроль качества сварки / под ред. В.Н. Вол-ченко. М.: Машиностроение, 1975. 328 с.
- Щербинский В.Г., Алёшин Н.П. Ультразвуковой контроль сварных соединений. М.: Изд-во МГТУ им. Баумана, 2000. 496 с.
- Михайлов А.М., Бауман Б.В. [и др.] / под общ. ред. А.В. Курдюмова. 2-е изд., перераб. и доп. М.: Машиностроение, 1990. 272 с.
- Введение в основы сварки: учебное пособие / В.И. Васильев, Д.П. Ильященко, Н.В. Пав-лов; Юргинский технологический институт. Томск: Изд-во Томского политехнического университета, 2011. 317 с.
- Сварка. Резка. Контроль: Справочник. В 2 т. / под общ. ред. Н.П. Алешина, Г.Г. Чернышова. М.: Машиностроение, 2004. Т. 1. 624 с.
- Теория сварочных процессов: учеб. для вузов по спец. «Оборуд. и технология сварочн. пр-ва» / В.Н. Волченко, В.М. Ямпольский, В.В. Винокуров [и др.]; под ред. В.В. Фролова. М.: Высш. шк., 1988. 559 с.
- Хромченок Ф.А. Справочное пособие электросварщика. М.: Машиностроение, 2003. 416 с.
- Разработка методики УЗК в целях обеспечения технологической безопасности объектов АЭ / В.В. Абрамец [и др.] // Инновации в атомной энергетике: сб. докладов конференции молодых специалистов (25–26 ноября 2015 г., Москва). М.: Изд-во АО «НИКИЭТ», 2015. С. 608–621.
- Количественная ультразвуковая оценка дефектов сварных соединений объектов атомной энергетики / Т.С. Твердохлебова [и др.] // Инновации в атомной энергетике: сб. докладов конференции молодых специалистов (25–26 ноября 2015 г., Москва). М.: Изд-во АО «НИКИЭТ», 2015. C. 516–523.
- Контроль неразрушающий. Соединения сварные. Методы ультразвуковые: ГОСТ 14782-86. Взамен ГОСТ 22368-77; введ. 01.01.1988.
Авторы – сотрудники Оренбургского Государственного Университета
Если вам понравился материал, кликните значок - вы поможете нам узнать, каким статьям и новостям следует отдавать предпочтение. Если вы хотите обсудить материал - не стесняйтесь оставлять свои комментарии : возможно, они будут полезны другим нашим читателям!