Введение
В разные периоды развития науки и техники повышению качества производства, в том числе металлургического, уделялось большое внимание. Фундаментальные работы [1–4] заложили теоретическую основу современных методов повышения эффективности производственных предприятий. Широкую известность во многих предприятиях промышленного сектора получили концепции «шесть сигм», всеобщая система управления качеством, «точно в срок». Сегодня же наблюдается большой интерес научного сообщества к развитию идеологии Индустрии 4.0, о чём свидетельствуют обзоры [5–7]. Идеи четвёртой промышленной революции (Индустрии 4.0) открывают перспективы реализации оптимизационных мероприятий на производстве с применением качественно нового подхода, основанного на внедрении цифровых технологий. В [8] было выделено восемь ключевых технологий Индустрии 4.0: блокчейн, трёхмерная печать, беспилотные устройства, дополненная реальность, виртуальная реальность, искусственный интеллект, робототехника и Интернет вещей. Комплексное системное внедрение каждой из перечисленных технологий характеризуется высоким потенциалом для качественного улучшения и повышения эффективности производственных процессов. Согласно [5] уже удалось достичь значимых результатов в направлении внедрения технологий Индустрии 4.0 таким промышленным гигантам, как ПАО «НЛМК», ПАО «СИБУР», Siemens, Intel и другим отраслевым лидерам. Как показывает анализ из [9], внедрение цифровых технологий на производстве влечёт сокращение расходов до 30% по отдельным категориям.Организация процесса планирования на производстве оказывает колоссальное влияние на общую эффективность предприятия. Основополагающими факторами, влияющими на эффективность планирования, являются наличие на предприятии отлаженной системы сбора данных и способность их анализировать. Наиболее распространёнными методами расчёта потенциального спроса на продукцию промышленного предприятия являются метод коэффициентов, линейная регрессия и нейронные сети. В [10] было установлено, что линейная регрессия доставляет преимущество в погрешности только на 1% по сравнению с нейронной сетью. Однако нейронная сеть, как метод корректировки производственного плана, оказывается весьма дорогостоящей с точки зрения разработки и обслуживания. В [11] были получены аналогичные результаты о преимуществах регрессионного анализа в приложении к решению задач производственного планирования.
Другой взгляд на повышение качества металлургического производства изложен в [12]. Здесь ключевая роль отводится таким показателям, как износ оборудования и сопутствующие ему операционные издержки. В [13] выделяются три основные концепции на задачу повышения качества производства путём внедрения системы обслуживания и ремонта оборудования: всеобщее производственное обслуживание, обслуживание, основанное на надёжности, и обслуживание, основанное на бизнес-задачах. В [14] наиболее перспективной концепцией представляется обслуживание, основанное на надёжности, так как её центральным элементом выступает непосредственно оборудование и его техническое состояние, а в качестве эффективного подхода к реализации предлагаются методы системного анализа и корректировки. В то же время технологии Индустрии 4.0 предоставляют собственный аппарат реализации систем технологического осмотра и ремонта оборудования [15]. Так, например, на ПАО «НЛМК» реализован подход на основе машинного обучения для замены фурм доменных печей, что оценивается экономическим эффектом в объёме до 120 млн руб. ежегодно. Другим примером реализации технологии Индустрии 4.0 может быть установка на каждом агрегате NFC-метки (коммуникация ближнего поля) в ПАО «СИБУР» [6]. Этот подход не носит рекомендательный характер, но хранит и фиксирует в автоматическом режиме всю цепочку операций по обслуживанию и ремонту каждой отдельной единицы.
Принципиально отличный подход к повышению качества металлургического производства связан с прогнозированием дефектов конечной продукции. В [16] представлен широкий обзор научных трудов, посвящённых исследованию причин возникновения дефектов. В [17] был проведён анализ взаимосвязи недостаточного понимания причин возникновения дефектов и финансовых и репутационных потерь предприятия. В [18] для распознавания дефектов, причин их возникновения, классификации и мер корректировки предлагается четырёхуровневая система контроля качества: информационный контроль (готовая продукция), активный контроль (процесс производства), прогнозный контроль (оборудование и материалы) и профилактический контроль (внешние факторы).
Детальный анализ факторов в области прогнозного контроля предложен в [19]. Эконометрические методы (регрессионные модели, нейронные сети, кластерный анализ) для анализа причинно-следственных связей между
дефектами и потенциальными факторами были предложены в [20]. Для комплексного снижения уровня брака на производстве в [19] предлагается три подхода к диагностированию эффектов: контрольный реестр, стратификация расходов и кластерный анализ.
В [21–23] для снижения брака на стане горячей прокатки и повышения качества конечной продукции предлагаются алгоритмы распознавания образов в геометрической постановке. Для классификации видов продукции по стоимости брака в [24] предложены методы ABC-анализа, в [25] – методы на основе дерева решений, в [26] – пошаговая регрессия для построения прогнозной модели потенциальных затрат на бракованную продукцию в рамках планового периода.
В рамках прогнозного контроля отдельного внимания заслуживает метод быстрого прототипирования, предложенный в [27]. Этот метод объединяет группу технологий и технологических процессов, использующих трёхмерную печать на базе компьютерного моделирования.
Таким образом, в парадигме перехода металлургических предприятий на уровень Индустрии 4.0 активно развиваются такие подходы к оптимизации технологических процессов, как прогнозирование спроса, мониторинг износа оборудования, контроль качества. Однако комплексные задачи планирования, управления и логистики сложных металлургических переделов освещены в современной литературе довольно слабо.
В настоящей статье предлагается новый метод организации производственных данных на основе понятия объектных отношений как универсальной структуры для моделирования производства. В основе предлагаемого метода лежит понятие «объекта», представляющего собой любую сущность производственной цепочки (завод, цех, агрегат, производственная операция, единица продукции и т.д.). Ключевым отличием метода объектных отношений от агентного моделирования является то обстоятельство, что объектам не навязаны никакие поведенческие сценарии. Тем самым структура «объект» оказывается полномочной вступать в любые отношения с другими «объектами» в рамках рассматриваемой модели, что, в свою очередь, позволяет аккумулировать различного рода данные в единую иерархию и гарантирует достоверность анализа любого уровня. Разработанный метод объектных отношений (Object Relations Technique или ORT) был применён на нескольких полномасштабных производственных площадках, подтвердив тем самым свою устойчивость и работоспособность.
Основные положения ORT
Цифровизация подразумевает получение эффекта на основе интеллектуальной обработки производственных данных. Причём в области интеллектуальной обработки данных появилось множество инструментов, в том числе на основе Open Source технологий, включающих обработку больших данных, зрелый Open Source BI, системы для аналитиков на основе Juputer Lab, включающие самые последние библиотеки статистического анализа и машинного обучения.Однако эффективное применение современных инструментов затруднено, поскольку данные предприятия замкнуты внутри большого количества систем автоматизации и цифровизации. Модели и форматы данных определяются бизнес-процессом участка производства и поэтому специфичны для каждой системы.
В результате независимо от уровня вооружённости предприятия системами цифровизации основным инструментом анализа данных для принятия управленческих решений является EXCEL.
Как только для управления требуются данные от разных систем, единственным способом работы с данными становится выгрузка отчётных форм в EXCEL из разных систем, работа по сведению данных и обработка сводных отчётов (рис. 1).
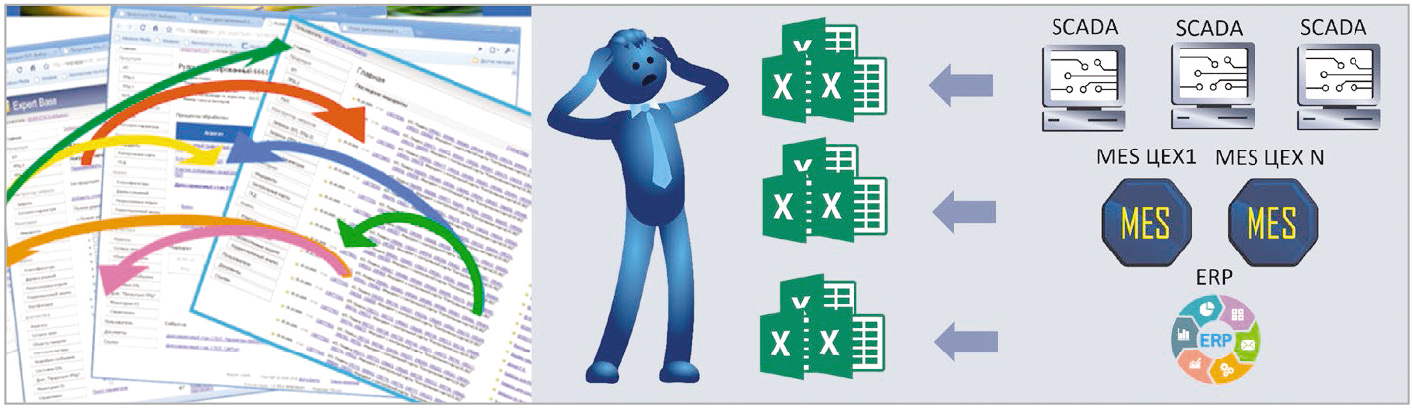
Но и это не последняя трудность. Если вы ищете пути оптимизации производства на основе собранных вами данных, то ваша работа постоянно прерывается для перехода между системами. Построение сводных таблиц вы сделаете в Exel, статистическую обработку данных – в специализированном пакете типа Matlab, отчёт о результатах работы оформите в Word и разошлёте по электронной почте. Потом вас попросят уточнить результаты за другой временной период, и всё с начала!
Управление на основе данных постоянно прерывается для перехода между системами. Это всё равно, что возить заготовки между разными предприятиями вместо их обработки на едином конвейере (рис. 2).

Большие надежды в области решения означенной задачи возлагались на инструментарий Big Data. Предполагалось, что всё получится, если собрать данные вместе. Итог подвел журнал «Форбс» в 2018 году в статье «What Is Continuous Intelligence?». В частности, отмечалось следующее.
- Складывание всех данных в одном месте для их обработки далее требует ещё больше работы, чтобы сделать их пригодными для использования.
- Пёстрая коллекция таблиц и файлов данных, выгружаемых из источников в озёра данных… привела к новому болезненному процессу – это подготовка сырых данных для выполнения последующей аналитики над ними, преобразование сырых (грязных) данных, хранящихся в любых произвольных форматах, в требуемые для аналитических приложений.
- Аналитики, которые разведены отдельными модулями, отдельными задачами и отдельными командами со специализированными навыками, только крадут время, не добиваясь самого главного – своевременной непрерывной информации из всех ваших данных.
Таким образом, была обозначена необходимость – создать модель представления производственных данных, которая является единой для любого производственного модуля и любой производственной задачи. Естественно, создать такую модель на основе описания производственных бизнес-процессов было невозможно в силу множественности и специфичности этих бизнес-процессов.
ORT формулирует подход к производственным данным, исключив разделение описания структур данных под отраслевую, физическую и иную предметную специфику.
В основе подхода лежит переход от описания бизнес-процессов к самим объектам, на которые эти процессы направлены. Производство в этом случае представлено как поток объектов, которые под воздействием процессов меняют свойства и вступают в отношения друг с другом (Object Relations Technique или ORT).
Объекты ORT – это учётные единицы производства (полуфабрикат, материалы, готовая продукция) и узлы обработки (агрегаты, технологические узлы, склады и их места хранения). Свойства объектов описываются через их параметры. Между объектами возникают связи. Например, переработка материала в заготовки устанавливает связь между материалом и заготовками (генеалогия). Загрузка материала в печь образует связь между материалом и печью (событие начала обработки), отгрузка на склад – связь между продукцией и местом хранения. Нетрудно заметить, что любые производственные события — это установление и прекращение связи. Объектами являются не только единицы продукции, но и любые учётные единицы, на которые направлен бизнес-процесс предприятия. Модель ORT способ-на учесть и обработать кроме единиц продукции (полуфабриката, изделия) наряд-заказы, простои, сменные задания, оперативные планы, стадии выполнения бизнес-процессов. Например, в объектной модели поступление задания в цех описывается как возникновение связи между объектом «цех» и объектом «задание» (рис. 3).
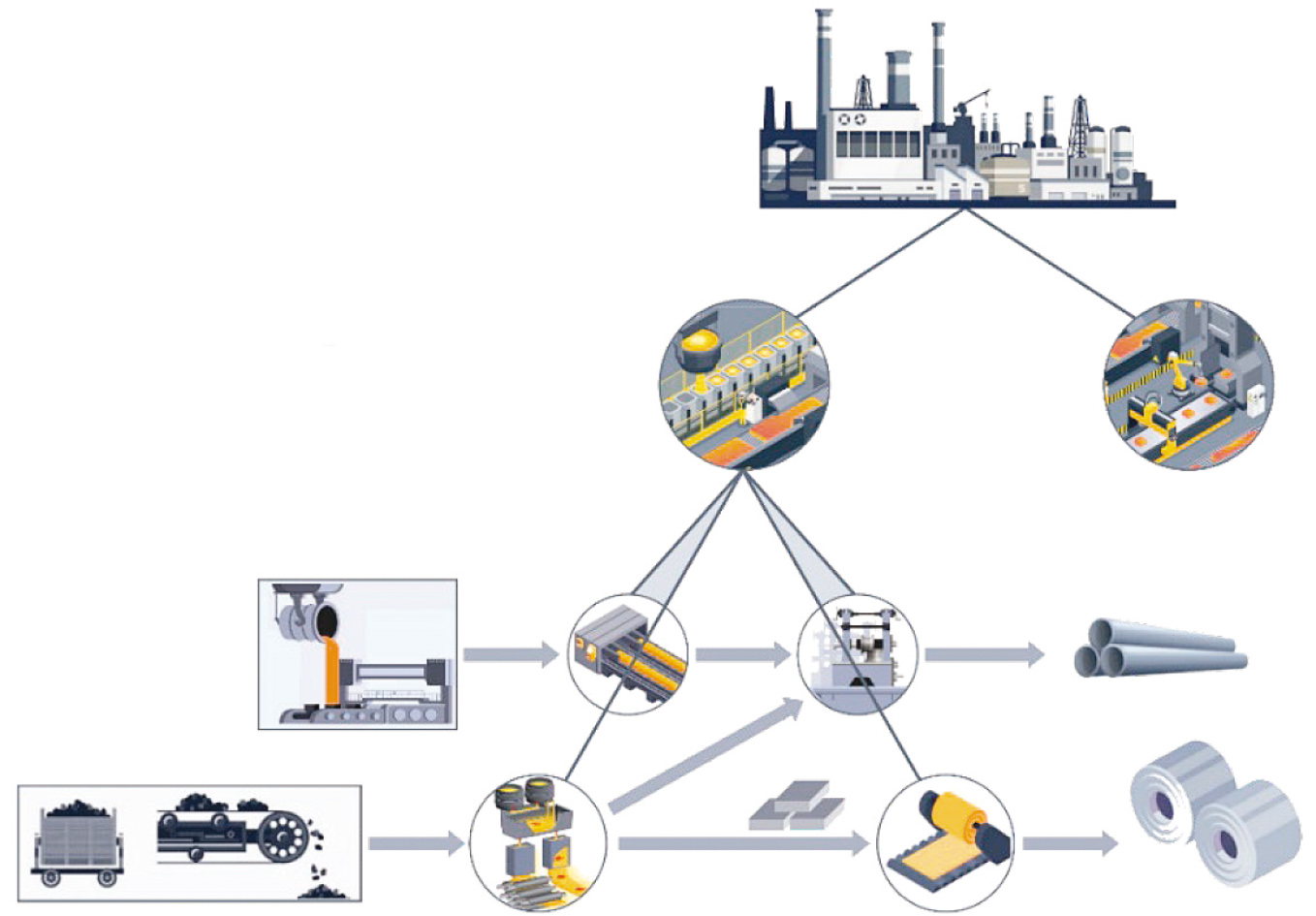
Представление производства как отношения объектов хорошо совместимо с современными инструментами интеллектуального управления и инструментами Big Data.
Наш 30-летний опыт построения систем управления производством на основе данных показал, что описываемый подход применим, независимо от предметной специфики, для решения любых задач цифровизации, например: трекинг продукции и материальных потоков предприятия; глобальная аналитическая система на основе больших данных; оптимальное оперативное планирование; анализ качества и оптимизация технологических процессов; создание единого источника данных для всех звеньев цифровизации (единого источника правды); создание интеллектуальных помощников и подсказчиков; глобальных BI-систем; систем для data science. Подход позволил получать от данных реальный эффект за счёт понятной, единой, целостной картины производства в режиме реального времени и таким образом решить задачу создания Continuous Intelligence систем на производстве.
Для применения описываемого подхода существует следующий набор инструментов.
DATA-TRACK – потоковая трансформация производственных данных в объекты, их свойства и отношения.
EXPERT BASE – извлечение информации из объектных данных, универсальная система гибких глобальных запросов, BI и аналитическая система.
DATA-PLAN – открытая система решений для управления, планирования и оптимизации производства.
Потоковая трансформация производственных данных в объекты, их свойства и отношения
Объект для описываемого подхода – это любая производственная сущность, на которую направлены усилия, внимание, желание и воля бизнеса. Объекты вступают между собой в отношения через формирование связей. Например, объект «цех» связан с объектами «центры обработки». Или для металлургического производства объект «Горячекатаный рулон» связан со слябом, из которого он прокатан, а сляб связан с плавкой, из которой он разлит на машине непрерывного литья. Если продолжать пример из металлургии, то объект «плавка» вступал в отношения (связи) с конвертером, агрегатами внепечной обработки, машиной непрерывного литья. Если объект вступил в отношения с центром обработки, то он приобретает новые свойства, которые протоколируются как параметры, связанные с объектом.Через объекты, их свойства и параметры общая картина производственных данных становится прозрачной для пользователя как в текущий момент времени, так и в виде исторических данных. Полностью контролируется, где находится (находился) материал, фактические параметры обработки, по какому заданию и техкарте производилась обработка (задания, техкарты, планы также являются объектами системы).
Для получения «объектной картины мира» предоставляется платформа DATA-TRACK, которая при настройке на производственную площадку преобразует поток производственных данных в объекты ORT и их отношения. Для достижения результата конфигурируется цифровой двойник движения продукции по производственным линиям и решается задача трекинга. Таким образом, движение материальных потоков и информационные потоки связываются как объекты и параметры ORT.
DATA-TRACK – Low code платформа, которая предоставляет единую систему описания трансформации данных процессов через объекты «Object Oriented Data Transformation Stream», или сокращённо «OODTS».
Другими словами, основная функция DATA-TRACK – объединение ключевой информации информационных систем предприятия в единое предметно-ориентированное хранилище. Это позволяет собирать, связывать, анализировать данные и вовремя предоставлять информацию функциональным модулям с помощью универсальной системы гибких глобальных запросов.
Извлечение информации из объектных данных. Универсальная система гибких глобальных запросов
Из структурированных через OODTS данных можно извлечь любую полезную производственную информацию путём построения запроса. При этом формат построения запроса универсален и основан на отношениях объектов. Продолжая пример из металлургической тематики, можно для анализа данных по горячекатаным рулонам запросить параметры самого рулона (например, температуры прокатки), а также химсостав плавки, из которой рулоны были прокатаны. Для этого при формировании отчёта нужно просто пройти по связи от рулона к плавке и запросить нужные параметры уже для плавки. Следует обратить внимание, что пользователь оперирует только объектами, параметрами и их связями, а значит, при составлении запроса работает с терминами своей предметной области (каждый объект содержит своё название, свои параметры и свои связи). Не требуется быть IT-специалистом для извлечения нужной информации, при этом можно получать любые данные для решения любой производственной задачи, например, простои можно контролировать по количеству вступивших в связь с узлом обработки объектов за определённый промежуток времени. Также легко решается задача извлечения данных для построения различных KPI для BI-дашбордов (рис. 4).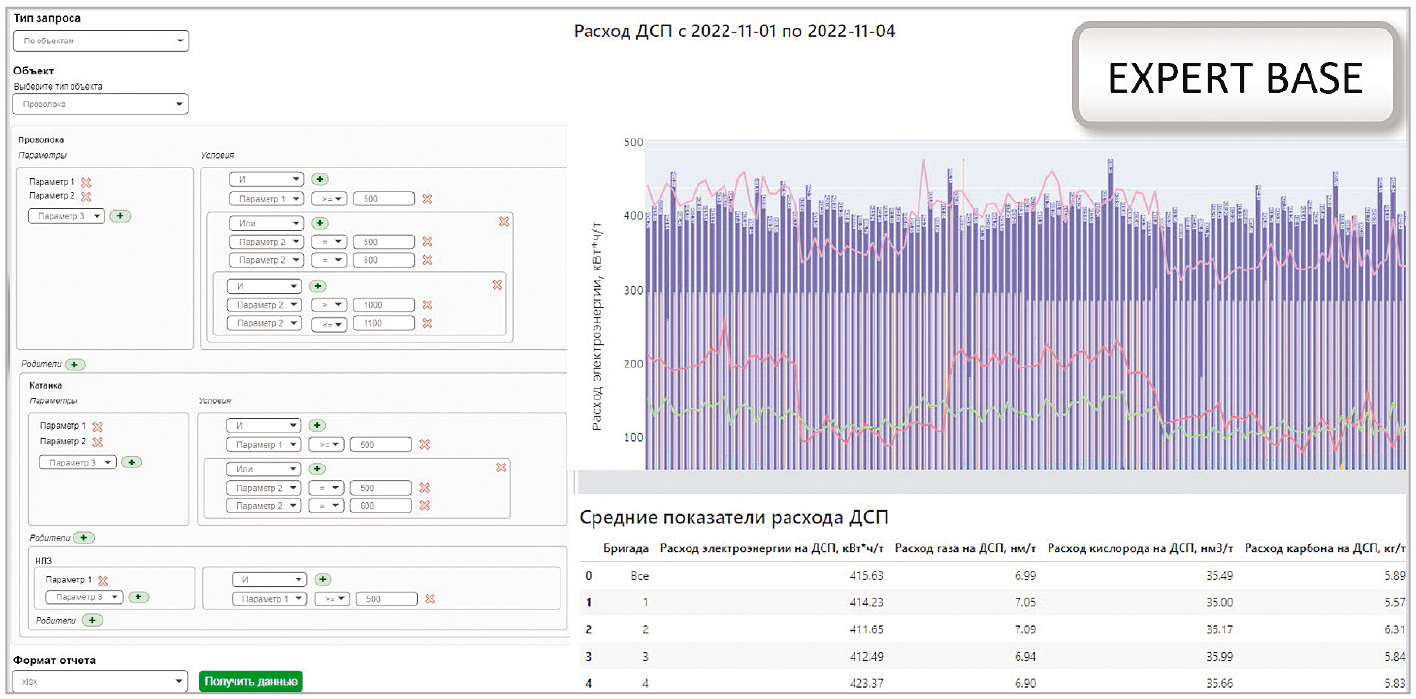
Важно, что получателем данных после формирования запросов может быть не только Data Scientist, но и смежные системы цифровизации.
Инструментарий для интерактивного формирования запросов, вычисления KPI и прочих характеристик производства, исследования данных и формирования информации для других звеньев цифровизации предоставляет платформа EXPERT BASE.
EXPERT BASE – Low code платформа, позволяющая стандартным образом интерактивно построить запрос к объектным данным, обработать полученную информацию и сформировать BI-дашборды для дальнейшего использования или выдать информацию смежным системам. Интеллектуальные советники и оптимизаторы также строятся средствами системы, поскольку система располагает библиотеками для статистической обработки данных и средствами ML.
Иными словами, EXPERT BASE реализует Универсальную систему гибких глобальных запросов, «Universal Global Flaxible Requests System» – UGFRS.
Открытая система решений для управления, планирования и оптимизации производства
Поскольку текущее состояние производства прозрачно для системы, то на базе текущих и исторических данных предлагаются готовые решения оптимизации производства на базе модулей оптимального оперативного планирования DATA-PLAN. При этом EXPERT BASE предоставляет инструменты для построения собственных оптимизационных модулей.Сочетание DATA-PLAN и EXPERT BASE предоставляет пользователю Открытую систему решений для управления, планирования и оптимизации производства, или, иначе, Интеллектуальную систему управления на основе производственных данных, «OS Manufacturing Data Mind» – OS MDM (рис. 5).
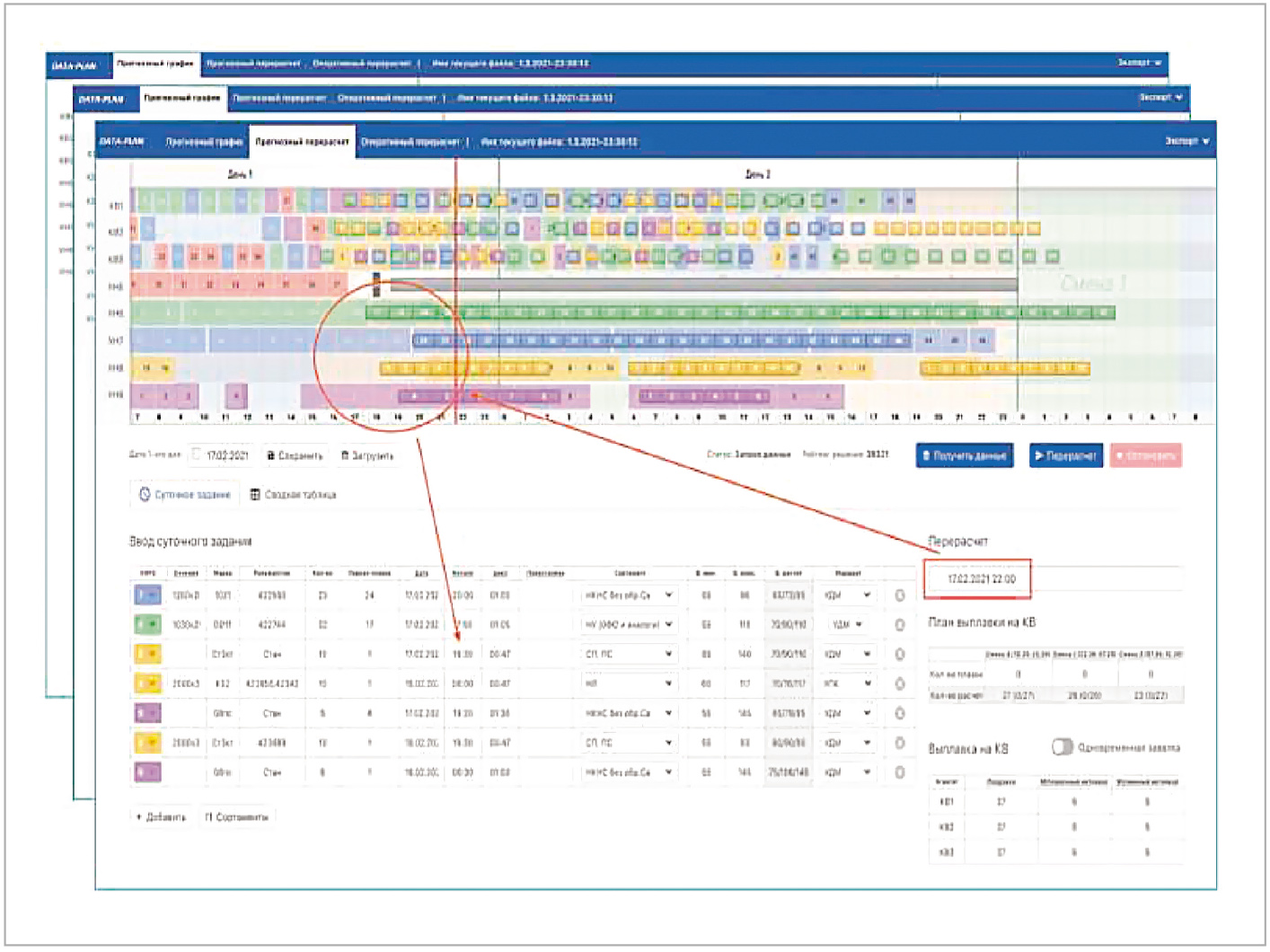
Заключение
ORT MDM модель производственных данных, а также способы их обработки OODTS, UGFRS и OS MDM имеют следующие преимущества.- Приём потоковых данных производства проходит объектно-ориентированную трансформацию, которая описывает объект с учётом его преобразований и условий, которые его окружают в процессе этих преобразований. Результат протоколируется в виде объектов, их параметров и отношений (связей) объектов.
- Процесс обращения к данным сильно упрощён по сравнению с другими решениями путём применения единого универсального интерфейса, который не требует переписывания данных под задачу и преобразования данных из одного формата описания в другой для решения конкретной задачи.
- Помимо поставляемых модулей для решения задач по планированию и оптимизации производства, предоставляется инструментарий, чтобы быстро извлечь и обработать необходимую информацию, а в случае необходимости построить новый интерфейс для смежных модулей.
Литература
- Ford H., Crowther S. My Life and Work. Garden City, New York: Garden City Publishing Company, Inc. 1922. 231 p.
- Deming W. Edwards. Statistical Adjustment of Data. Dover. 1943. 261 p.
- Taylor F.W. The Principles of Scientific Management. New York; London: Harper & brothers. 1911. 144 p.
- Gantt H.L. A graphical daily balance in manufacture // Transactions of the American Society of Mechanical Engineers. 1903. Vol. 24. P. 1322–1336.
- Лисовский А.Л. Оптимизация бизнес-процессов для перехода к устойчивому развитию в условиях четвёртой промышленной революции // Стратегические решения и риск-менджмент. 2018. № 4. С. 10–19.
- Тарасов И.В., Попов Н.А. Индустрия 4.0: Трансформация производственных фабрик // Стратегические решения и риск-менджмент. 2018. № 3. С. 38–53.
- Roblek V., Mesko M., Krapez A. A Complex View of Industry 4.0 // SAGE Open. 2016.
- Пуха Ю. Индустриальная революция 4.0 // PricewaterhouseCoopers. 2017. URL: https:// www.pwc.ru / ru/assets/pdf/industry-4-0 pwc.pdf.
- Rojko A. Industry 4.0 concept: background and overview // International Journal of Interactive Mobile Technologies (iJIM). 2017. Vol. 11, № 5. P. 77–90. URL: https://doi.org/10.3991/ijim. v11i5.7072.
- Dean P.R., Xue D., Tu Y.L. Prediction of manufacturing resource requirements from customer demands in mass-customisation production // International Journal of Production Research. 2009. Vol. 47. № 5. P. 1245–1268.
- Сербул А. Нейронки: какому бизнесу нужен искусственный интеллект (и лайфхаки, как его внедрить) // Деловой журнал «Inc.». 2018. URL: https://incrussia.ru/understand/nejronki-kakomu-biznesu-nuzhen-iskusstvennyj-intellekt-i-lajfhaki-ka....
- Ding S.H., Kamaruddin S. Maintenance policy optimization – literature review and directions // The International Journal of Advanced Manufacturing Technology. 2015. Vol. 76, № 5–8. P. 1263–1283. URL: https://doi.org/10.1007/s00170.014.6341.2.
- Tinga T. Maintenance concepts // Principles of loads and failure mechanisms / Ed. H. Pham. London: Springer. 2013. P. 161–186.
- Vishnu C.R., Regikumar V. Reliability based maintenance strategy selection in process plants: a case study // Procedia Technology. 2016. Vol. 25. P. 1080–1087.
- Аршанский А. Искусственный интеллект в металлургии // НЛМК. 2018. URL: http://www.cloudmobility.ru/sites/default/files/13.25-13.45_arhavsky_nlmk_new.pdf.
- Harding J.A., Shahbaz M., Srinivas et al. Data mining in manufacturing: a review // Journal of Manufacturing Science and Engineering. 2006. Vol. 128, № 4. P. 969–976. URL: https://doi.org/10.1115/1.2194554.
- Chongwatpol J. Prognostic analysis of defects in manufacturing // Industrial Management & Data Systems. 2015. Vol. 115, № 1. P. 64–87.
- O’Regan P., Prickett P., Setchi R. et al. Engineering a More Sustainable Manufacturing Process for Metal Additive Layer Manufacturing Using a Productive Process Pyramid // International Conference on Sustainable Design and Manufacturing. Cham: Springer. 2017. P. 736–745. URL: https:// doi.org/10.1007/ 978.3.319.57078.5_69.
- Leachman C., Pegels C., Kyoon Shin S. Manufacturing performance: evaluation and determinants // International Journal of Operations & Production Management. 2005. Vol. 25, № 9. P. 851–874.
- Hazen B.T., Boone C.A., Ezell J.D. et al. Data quality for data science, predictive analytics, and big data in supply chain management: An introduction to the problem and suggestions for research and applications // International Journal of Production Economics. 2014. Vol. 154. P. 72–80. URL: https://doi.org/10.1016/ j.ijpe.2014.04.018.
- Gitman M.B., Trusov P.V., Fedoseev S.A. On optimization of metal forming with adaptable characteristics. Journal of Applied Mathematics and Computing (2020) vol. 7, no. 2, P. 387–396.
- Gainanov D.N., Berenov D.A. Algorithm for predicting the quality of the product of metal-lurgical production. In: CEUR Workshop Proceedings (2017) vol. 1987. Р. 194–200.
- Gainanov D.N., Berenov D.A., Rasskazova V.A. Algorithm for Predicting the Quality of the Product Based on Technological Pyramids in Graphs. LNCS (2021) 12931. Р. 128–141.
- Kampf R., Lorincova S., Hitka M. et al. The application of ABC analysis to inventories in the automatic industry utilizing the cost saving effect // NASE MORE: znanstveno-strucnicasopisza more ipomorstvo. 2016. Vol. 63, № 3. Spec. Issue. P. 120–125. URL: https://doi.org/10.17818/NM/2016/SI8.
- Kim A., Oh K., Jung J.Y. et al. Imbalanced classification of manufacturing quality conditions using cost-sensitive decision tree ensembles // International Journal of Computer Integrated Manufacturing. 2018. Vol. 31, № 8. P. 701–717.
- Квасова Н.А., Целых В.Н. Методика оценки экономических потерь по видам дефектов на основе системы критериев КР-бенчмаркинга // Современные проблемы транспорт-ного комплекса России. 2012. № 2. С. 295–298.
- Rayna T., Striukova L. From rapid prototyping to home fabrication: How 3D printing is changing business model innovation // Technological Forecasting and Social Change. 2016. Vol. 102. P. 214–224.
и технического директора Волкова А.В.
Авторы – сотрудник ООО «Дата-Центр Автоматика», г. Екатеринбург, berenov@dc.ru
и сотрудник МАИ (национальный исследовательский университет), г. Москва, varvara.rasskazova@mail.ru
Если вам понравился материал, кликните значок - вы поможете нам узнать, каким статьям и новостям следует отдавать предпочтение. Если вы хотите обсудить материал - не стесняйтесь оставлять свои комментарии : возможно, они будут полезны другим нашим читателям!