Введение
История России неразрывно связана с торговым и военным кораблестроением. В настоящее время начался новый расцвет этой отрасли. Модернизация, происходящая на всех флотах, и освоение шельфовых месторождений полезных ископаемых ставят перед корабелами новые задачи. Одной из них является совершенствование ледокольного флота. Эта ответственная сфера требует от применяемого оборудования повышенной надёжности и самых передовых подходов и решений. Компания ООО «МегаСенсор Интегра» занимается проектированием и внедрением систем автоматизации с использованием передовых аппаратно-программных решений в области судовой автоматики. В статье рассмотрен опыт внедрения данных систем для управления гидравлическим оборудованием на судах. Использование современных компонентов предоставляет преимущества на всех стадиях производства, эксплуатации и разработки подобных систем.Описание и задачи системы
Система контроля, управления и мониторинга используется для управления гидромеханическим комплексом, предназначенным для транспортировки вертолёта, и открытия и закрытия ворот вертолётного ангара на ледоколах проекта 22220 (рис. 1).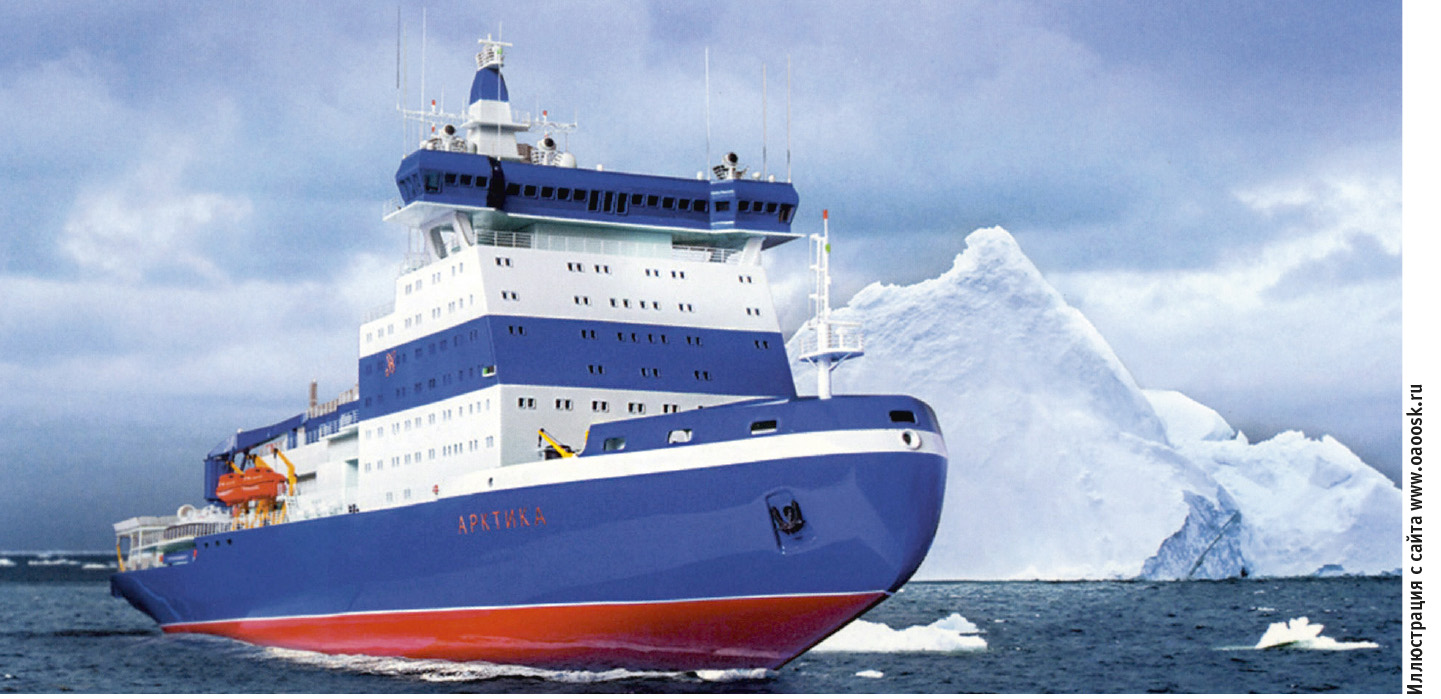
Подача рабочей жидкости в исполнительные механизмы осуществляется с помощью гидравлической станции с насосным агрегатом мощностью 22 кВт. Гидроцилиндры со встроенными датчиками конечных положений служат для открытия и закрытия правой и левой створок ворот ангара. Лебёдка, транспортирующая вертолёт, приводится в движение двумя гидромоторами. Задрайки предназначены для плотного закрытия дверей ангара и имеют соответствующие датчики положения. Информация о состоянии элементов системы собирается с датчиков в ПЛК, который обеспечивает выполнение заданных алгоритмов и находится в коммутационном шкафу управления.
В состав системы входят несколько постов и пультов для обеспечения управления из различных помещений.
Система предназначена для выполнения следующих функций:
- обеспечение выполнения программных режимов работы механизмов путём управления открытием гидрораспределителей согласно разработанному алгоритму;
- обеспечение взаимодействия с оператором посредством человеко-машинного интерфейса;
- пуск, останов, защита и контроль работы электродвигателя насосного агрегата и гидромоторов;
- управление элементами гидромеханической системы ворот ангара с разных пультов и постов управления, организация арбитража при одновременных попытках управления из разных мест;
- организация обработки сигналов с датчиков обратной связи для исключения запрещённых положений исполнительных механизмов вследствие неквалифицированных действий оператора;
- информационное взаимодействие с судовой системой управления верхнего и нижнего уровня для передачи данных о состоянии исполнительных механизмов и органов управления.
В связи с этим был сделан выбор в пользу современных информационных технологий – принято решение о применении ПЛК. Кроме того, использование ПЛК снижает трудозатраты при разработке и обеспечивает большее удобство и надёжность во время эксплуатации оборудования. При выборе аппаратной базы было довольно сложно найти оборудование, соответствующее всем требованиям заказчика: наличие сертификата типового одобрения от Российского морского регистра судоходства, высокая надёжность и соответствие требованиям политики импортозамещения. Оценив все преимущества и недостатки возможных решений, специалисты компании в качестве ядра системы управления выбрали программируемый логический контроллер морского исполнения фирмы FASTWEL.
Архитектура системы
Функциональная схема системы управления представлена на рис. 2.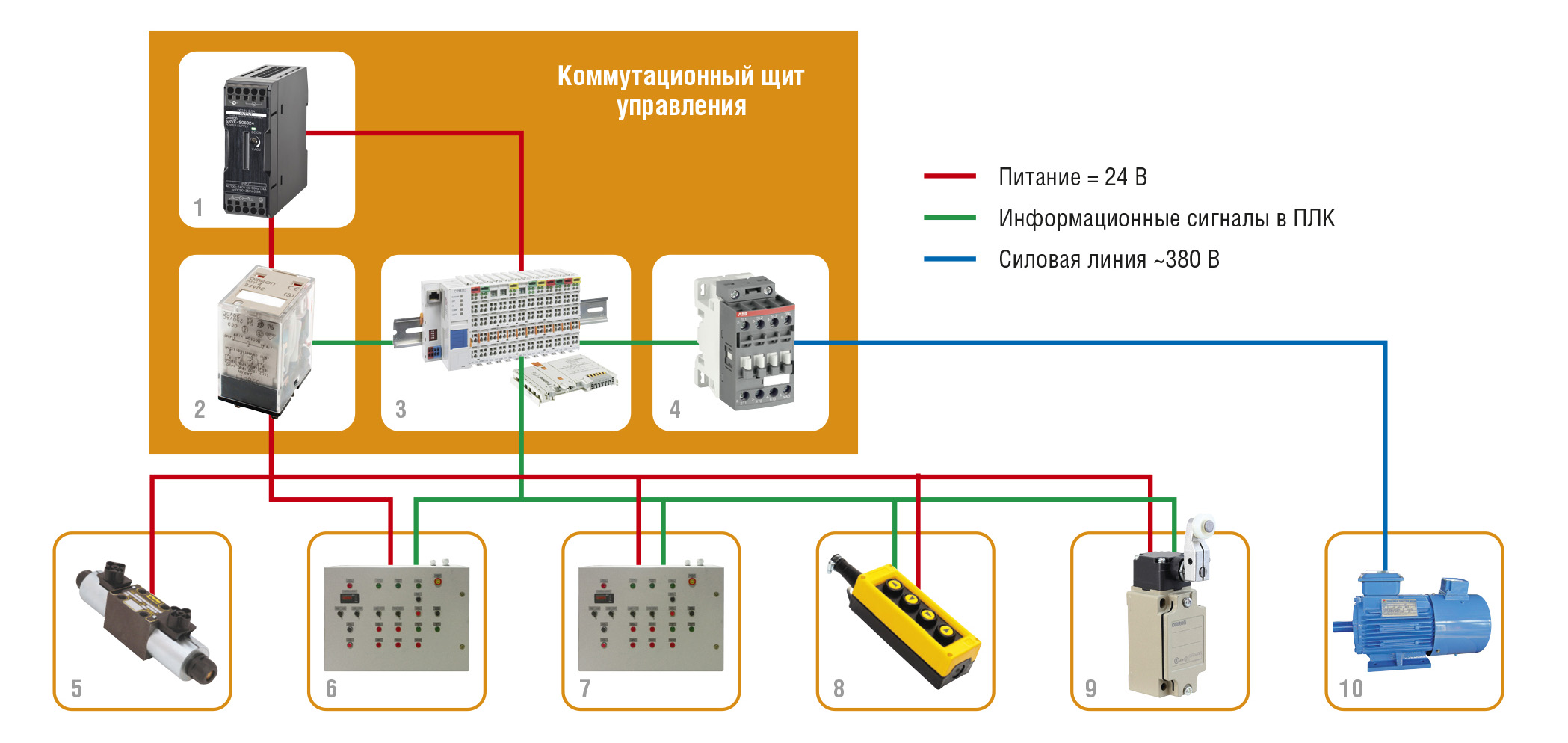
Условные обозначения:
1 – блок питания;
2 – блок реле;
3 – ПЛК;
4 – блок контакторов;
5 – гидравлический клапан;
6 – кнопочный пульт управления транспортировкой;
7 – кнопочный пульт управления воротами;
8 – переносной пульт управления транспортировкой;
9 – исполнительные механизмы;
10 – электродвигатели.
Рис. 2. Функциональная схема системы управления комплексом гидрооборудования
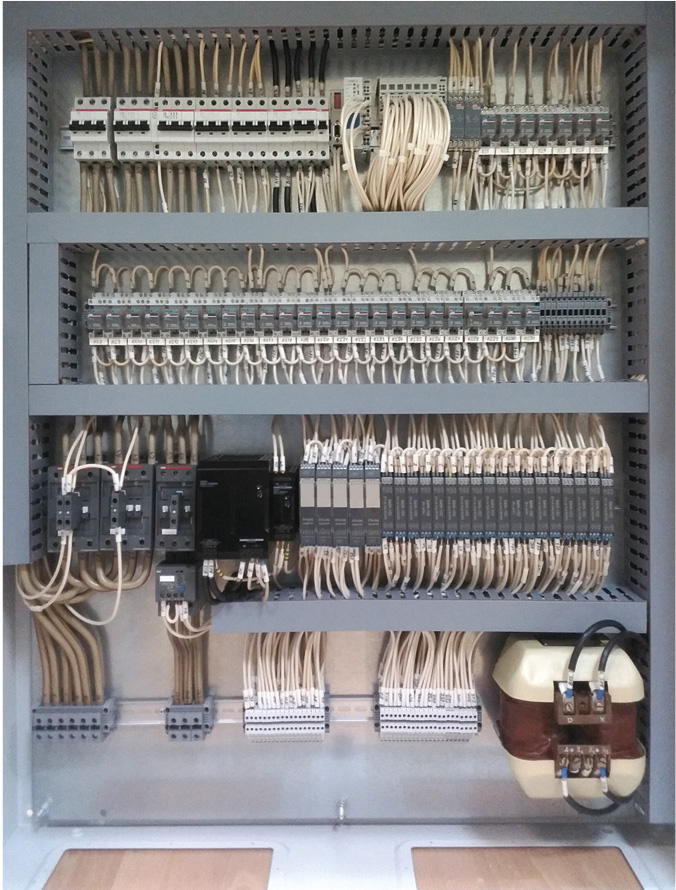
Работа над проектом
В ходе реализации данного проекта специалистам компании приходилось оперативно реагировать на изменения, вносимые заказчиком, и учитывать сокращение сроков разработки и наладки. Используемая архитектура позволяла проводить необходимые корректировки. По завершении разработки специалисты пришли к выводу, что данная архитектура имеет ряд преимуществ на всех стадиях жизни изделия, начиная от этапа проектирования, заканчивая эксплуатацией, ремонтом и обслуживанием.На этапе проектирования:
- Упрощение цикла разработки программного обеспечения и проектной документации достигается за счёт того, что специалисты осуществляют свою работу параллельно. Определив на начальной стадии протокол согласования электрических и логических цепей (вводные и выходные сигналы контроллера), можно обеспечить их независимую работу друг от друга. Реализацией требуемого алгоритма занимается программист. Схемные решения и организацию взаимодействия между контроллером и исполнительными устройствами обеспечивает проектировщик.
- Реализация логики системы в виде программы позволяет избежать усложнения схемы при добавлении новых устройств и функций и помогает обойтись без увеличения стоимости разработки.
- Снижение вероятности возникновения ошибок на этапе проектирования достигается за счёт минимизации ассортимента используемых элементов и упрощения схемотехники.
- Использование ПЛК позволяет проводить отладку управляющей программы посредством симуляции. Это ведёт к удешевлению работ и снижению трудоёмкости наладки на объекте.
- Использование типовых унифицированных схем для различных по назначению и масштабу систем даёт возможность добиться увеличения скорости разработки при реализации последующих проектов.
- Из-за использования ПЛК вместо релейно-контакторных схем значительно снижается сложность монтажа, что ведёт к ускорению производства оборудования.
- Перенос логики в контроллер позволяет отказаться от громоздких релейных сборок, уменьшить количество электрических соединений, маркировки, проводов и прочих расходных материалов. Помимо этого уменьшаются массо-габаритные характеристики коммутационных шкафов управления, что делает их установку и транспортировку более удобной.
- Использование унифицированных элементов и оборудования даёт возможность содержать на складе запас нужных компонентов и добиться их взаимозаменяемости.
- Упрощение монтажа на объекте и экономия пространства достигается за счёт низких массо-габаритных характеристик применяемого оборудования.
- При использовании программной логики управления снижается риск затрат на трудоёмкий перемонтаж из-за ошибок на стадии проектирования или сборки, вследствие чего уменьшаются издержки производства.
- За счёт уменьшения ассортимента используемых компонентов удаётся повысить надёжность системы и снизить вероятность отказов и сбоев.
- Наличие светодиодной индикации на модулях позволяет сократить время, затрачиваемое на диагностику системы, и сделать этот процесс более наглядным.
- При выходе из строя какого-либо элемента есть возможность быстро определить причину и провести необходимую замену.
Внедрение описанной системы управления позволило обеспечить требуемую надёжность, быстродействие, оперативность диагностики, новый уровень информационного взаимодействия между различными корабельными системами нижнего и верхнего уровня. На начало 2017 года заказчику переданы уже три комплекта этой системы. Получив опыт разработки данных систем на базе контроллера FASTWEL I/O, компания «МегаСенсор Интегра» разработала семейство решений для обеспечения управления различными системами судовой гидравлики. ●
Если вам понравился материал, кликните значок - вы поможете нам узнать, каким статьям и новостям следует отдавать предпочтение. Если вы хотите обсудить материал - не стесняйтесь оставлять свои комментарии : возможно, они будут полезны другим нашим читателям!