Введение
В 2011 году в России была принята программа по модернизации нефтеперерабатывающих мощностей и вводу новых мощностей вторичной переработки нефти со сроком реализации до 2020 года.Выполнение данной программы предполагает качественный скачок в развитии отрасли, поэтому нефтяные предприятия последовательно выполняют взятые на себя обязательства. Не стало исключением и ООО «Ильский НПЗ», находящееся в пгт Ильский Северского района Краснодарского края.
Таким образом, в 2012 году стартовали работы по модернизации ООО «Ильский НПЗ». Одним из результатов реконструкции является строительство двухсторонней эстакады слива-налива нефтепродуктов на 60 вагонов-цистерн, предназначенной для слива нефти и налива мазута, бензина, дизельного топлива. Именно она и стала объектом автоматизации ООО «НОИНТ».
В ходе автоматизации железнодорожной эстакады слива-налива нефтепродуктов были выполнены следующие работы:
- проектирование раздела «Автоматизация производства» с учётом внедрения противоаварийной и противопожарной защиты;
- подбор, поставка и монтаж оборудования;
- разработка прикладного программного обеспечения согласно требованиям заказчика;
- пусконаладочные работы;
- обучение персонала завода.
Назначение и функции системы
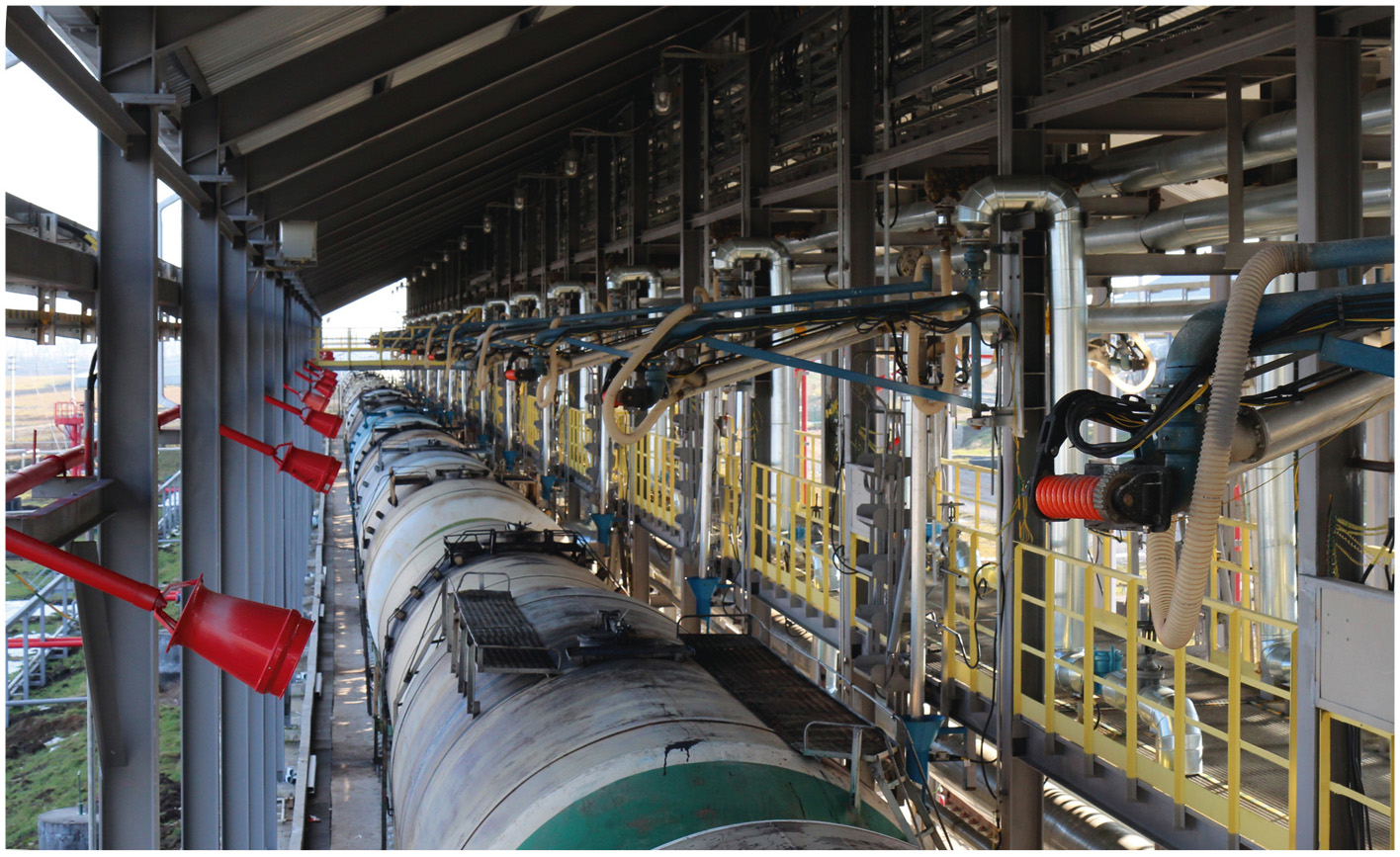
- автоматизированное управление процессами слива-налива нефтепродуктов согласно заданным алгоритмам работы;
- дистанционное управление оборудованием эстакады;
- контроль и точный учёт данных;
- получение оперативной информации о работе агрегатов;
- автоматическая передача данных в систему «1С: Бухгалтерия»;
- возможность управления процес-сами слива-налива в ручном режиме;
- автоматическая противоаварийная защита;
- автоматическая противопожарная защита.
Архитектура системы
Архитектура автоматизированной системы управления железнодорожной эстакады представлена на рис. 2, она включает три подсистемы: АТХ – автоматизация техпроцесса, ПАЗ – противоаварийная защита, АПТ – автоматическое пожаротушение.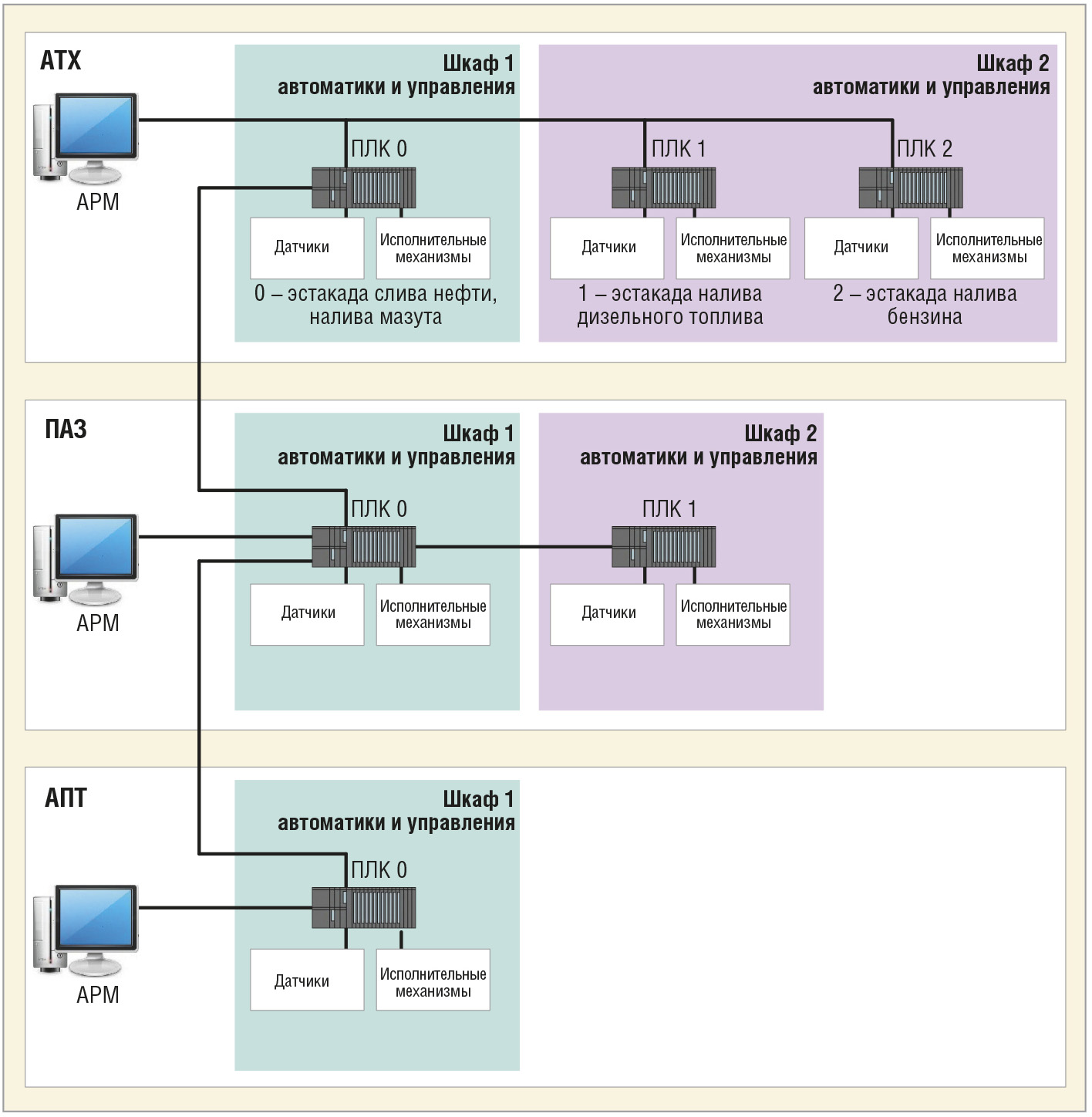
Верхний уровень, важной составляющей которого является человеко-машинный интерфейс, представлен SCADA-системой. Основные функции, выполняемые на верхнем уровне:
- контроль периферии;
- управление исполнительными устройствами;
- регистрация информации;
- хранение информации.
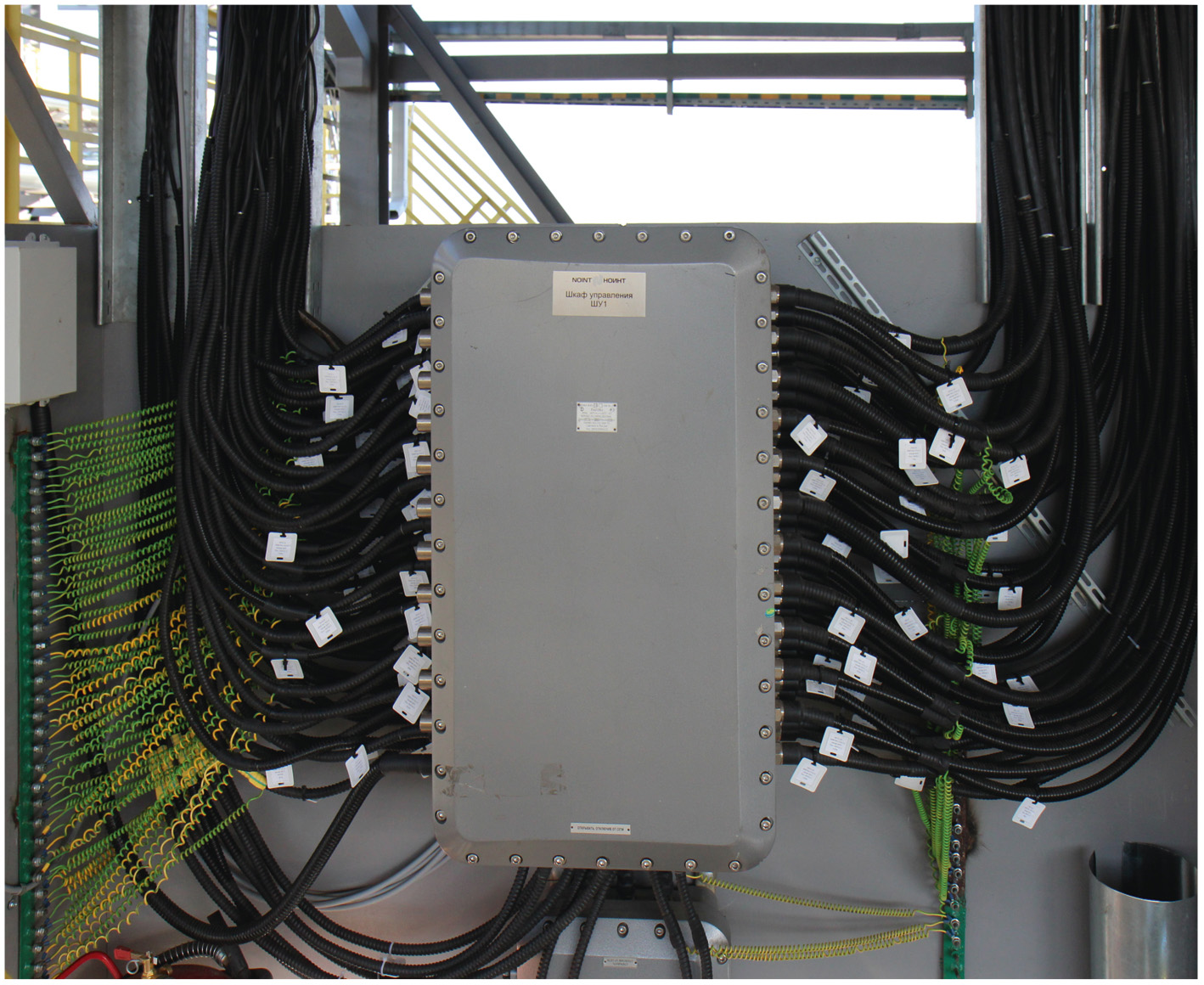
Используемые технические и программные средства
Подсистема АТХ (АСУ ТП) реализована с использованием трёх ПЛК SIEMENS серии SIMATIC S7-300. Получение информации о текущем состоянии оборудования и управление им осуществляется через модули ввода-вывода, входящие в состав контроллера. Для наблюдения за ходом технологического процесса и оперативного управления им в состав подсистемы входит компьютер с соответствующим программным обеспечением – автоматизированное рабочее место оператора (АРМ оператора). Кроме функций наблюдения и оперативного управления технологическим процессом, АРМ оператора позволяет собирать, хранить данные о ходе технологического процесса в архиве и производить анализ на основе этих данных.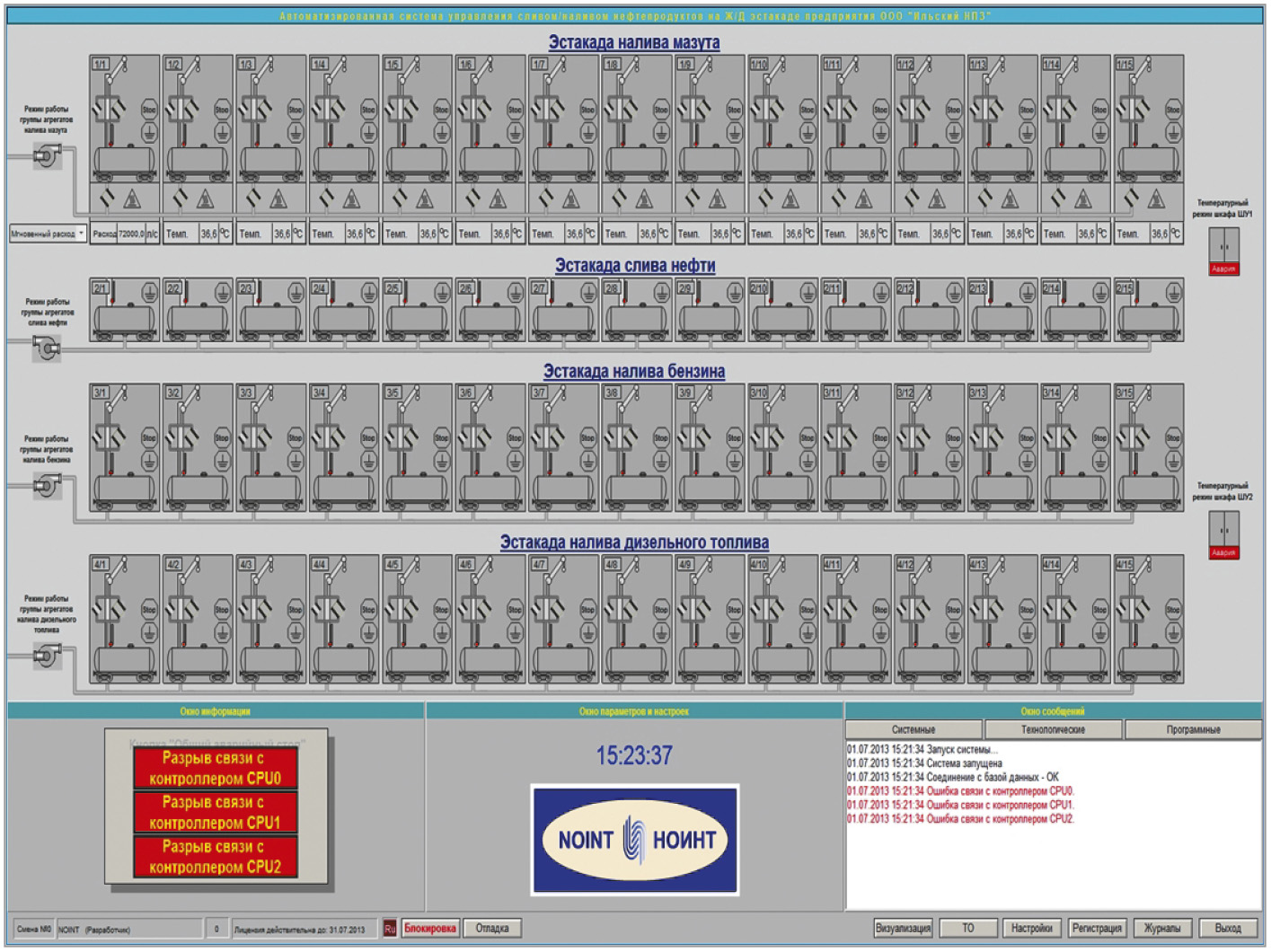
Описание АСУ ТП
Программируемый логический контроллер автоматически выполняет все необходимые действия по обеспечению дистанционного управления технологическим оборудованием системы. В функции ПЛК входит:- сбор информации о текущем состоянии всех устройств и агрегатов системы и режиме управления ими;
- формирование информационных сообщений обо всех изменениях в системе, полученных командах управления и результатах их выполнения;
- передача полученной информации, диагностических и информационных сообщений на АРМ оператора для их отображения, записи в журналы и организации диалога с оператором;
- автоматическое управление устройствами и агрегатами по заданным алгоритмам работы;
- приём команд управления с АРМ оператора.
- Управление устройствами и агрегатами позволяет менять состояние заданного устройства, при этом в окне параметров и настроек отобразится панель управления выбранным устройством. Содержимое этой панели (рис. 5) будет зависеть от типа устройства, а в окне визуализации рамка вокруг выбранного устройства начнёт мигать.
В зависимости от типа устройства, выполняемых им функций и аппаратной реализации некоторые поля и органы управления могут не отображаться или быть недоступными (отображение серым цветом означает, что выполнение соответствующих операций для данного устройства или агрегата невозможно). Надписи на кнопках управления состоянием устройства также изменяются. В верхней части окна в разделе «Текущие параметры» отображаются полное наименование выбранного устройства, установленный режим управления и его текущее состояние. В случае обнаружения системой аварии какого-либо устройства на экран выводится причина её возникновения. Если система обнаруживает аварию устройства или ошибки в его работе, то после устранения неисправности для восстановления нормального функционирования устройства используется кнопка «Сброс аварии». С помощью кнопок «Дистанционный», «Местный» и «Ремонтный» устройство переводится в соответствующий режим. Если для выбранного устройства включён ремонтный режим, то вместо кнопки «Ремонтный» отображается кнопка «Рабочий», служащая для его отключения. На рис. 6 показано окно параметров и настроек стояков налива мазута, где приводятся все текущие показатели расходомера по выбранному стояку налива, а также задаётся доза налива.
- Управление режимом технического обслуживания (ТО) – смена режима обслуживания разрешается только пользователям, имеющим соответствующие права. Включение и отключение ремонтного режима осуществляется в окне управления техническим обслуживанием.
- Блокировка АРМ оператора позволяет в случае временного отсутствия персонала заблокировать доступ к системе. Перемещение мыши ограничивается областью окна, представленного на рис. 7. Таким образом становятся недоступными все органы управления системой.
- Журнал событий: при работе системы автоматически формируются сообщения о возникающих событиях, которые сохраняются в журнале событий. В нём фиксируются все события, произошедшие в системе управления (информационные, аварийные, команды управления). Этот журнал позволяет анализировать работу системы и действия персонала. Окно содержит три поля: для задания условий отображения, отображения трендов и отображения событий. При первоначальном запуске поле отображения событий скрыто.
Алгоритм работы системы на примере процесса налива мазута
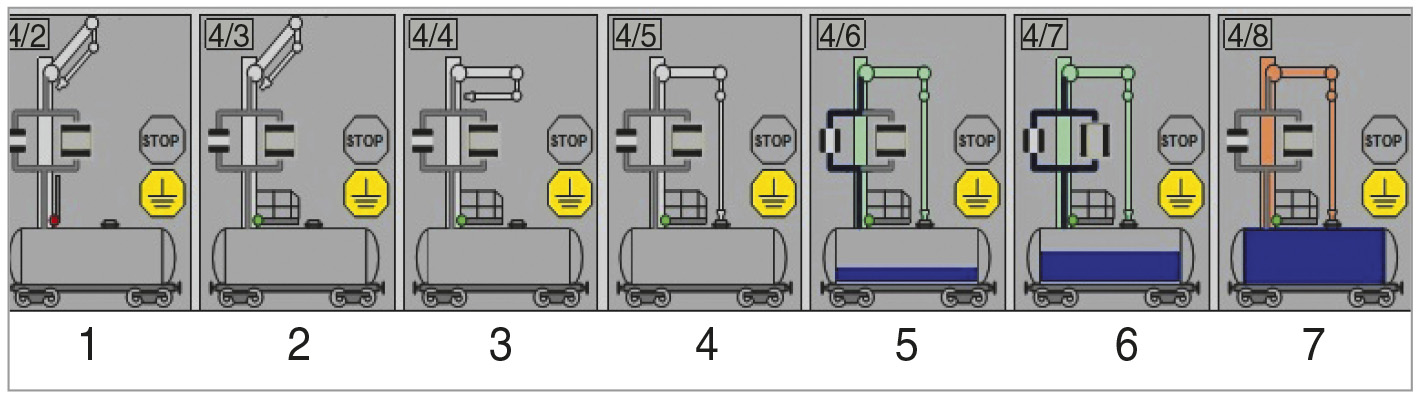
Алгоритм работы показан на рис. 8 и состоит из следующих шагов:
- оператор на железнодорожной эстакаде производит заземление железнодорожной цистерны (1);
- приводит в рабочее состояние трап, наконечник и консоль стояка налива (2, 3, 4);
- оператор налива по АРМ контролирует состояние технологического оборудования, задаёт дозу налива и запускает налив для каждого стояка отдельно;
- после подтверждения включения насосов открывается клапан малого расхода (5);
- по истечении времени налива на малом расходе открывается клапан большого расхода (6);
- за 500 кг до завершения дозы налива закрывается клапан большого расхода, количество продукта контролируется с помощью датчика расхода (7);
- при получении сигнала «Максимальный уровень» завершается налив.
- контроль положения запорной арматуры,
- контроль заземления железнодорожной цистерны,
- контроль положения устройства верхнего налива (УВН),
Для оперативного и безопасного процесса налива в системе предусмотрено:
- контроль расхода мазута (осуществляется расходомером);
- контроль положения (выполняется индуктивными бесконтактными датчиками приближения);
- противоаварийная защита (осуществляется датчиком предельного уровня).
Результаты внедрения
До реконструкции на предприятии в ручном режиме функционировала небольшая эстакада из 14 стояков слива-налива.В рамках реконструкции была построена новая полностью автоматизированная эстакада на 60 стояков налива.
Система автоматизации была запущена специалистами ООО «НОИНТ» в октябре 2013 года и сразу же позволила добиться следующих изменений:
- увеличение скорости слива-налива нефтепродуктов: до реконструкции налив семи вагонов производился за 1 час 10 минут, сейчас благодаря внедрению системы время налива 15 вагонов составляет 1 час 50 минут; также за счёт увеличения числа вагонов произошло сокращение объёма маневровых работ;
- сокращение количества обслуживающего персонала на единицу эстакады: ранее эстакаду из 14 стояков слива-налива обслуживали 7 товарных операторов, на данный момент эстакада из 60 стояков обслуживается десятью операторами;
- повышение точности учёта данных: расходомеры фирмы SIEMENS позволяют осуществлять коммерческий учёт налива нефтепродуктов без использования железнодорожных весов;
- автоматическая передача данных в систему «1С: Бухгалтерия».
Помимо преимуществ тотального автоматизированного контроля за всеми процессами на объекте, операторы завода отмечают удобный и наглядный интерфейс SCADA-системы. ●
E-mail: dir_noint@mail.ru
Если вам понравился материал, кликните значок - вы поможете нам узнать, каким статьям и новостям следует отдавать предпочтение. Если вы хотите обсудить материал - не стесняйтесь оставлять свои комментарии : возможно, они будут полезны другим нашим читателям!