Введение
С введением постановления Правительства РФ об увеличении выплат за выбросы при сжигании попутного нефтяного газа (ПНГ) на факельных установках нефтяные компании всё больше внимания уделяют проблеме его рационального использования. Одним из решений по утилизации ПНГ является применение газопоршневых генераторных установок для выработки электрической энергии для собственных нужд или для продажи в электрическую сеть. Газопоршневые электростанции представляют собой систему генерации, созданную на основе поршневого двигателя внутреннего сгорания, работающую на природном, попутном или другом горючем газе. Решение о применении данного оборудования на месторождениях зачастую зависит от качества попутного нефтяного газа, а именно – показателя детонационной стойкости (метанового числа). Метановое число – это условный показатель, который характеризует способность газов к бездетонационному сгоранию. Низкое качество газа приводит к быстрому выходу из строя оборудования, топливную аппаратуру забивает конденсат, детонация и перегрев двигателя не позволяют реализовать номинальную нагрузку. Потери мощности могут достигать 60%. Данный факт приводит к дополнительным затратам и нерентабельности использования оборудования.Для решения этой проблемы специалистами ООО «НПО «Уфанефтегазмаш» разработана и внедрена в производство адсорбционная установка по подготовке попутного нефтяного газа по метановому числу (далее – УПГ, рис. 1) для нужд газопоршневых установок. ООО «НПО «Уфанефтегазмаш» является изготовителем блочного оборудования для нефтяных и газовых месторождений и выполняет весь комплекс работ, от проектирования, разработки конструкторской документации, разработки системы автоматического управления и изготовления до пусконаладки и сервисного обслуживания.
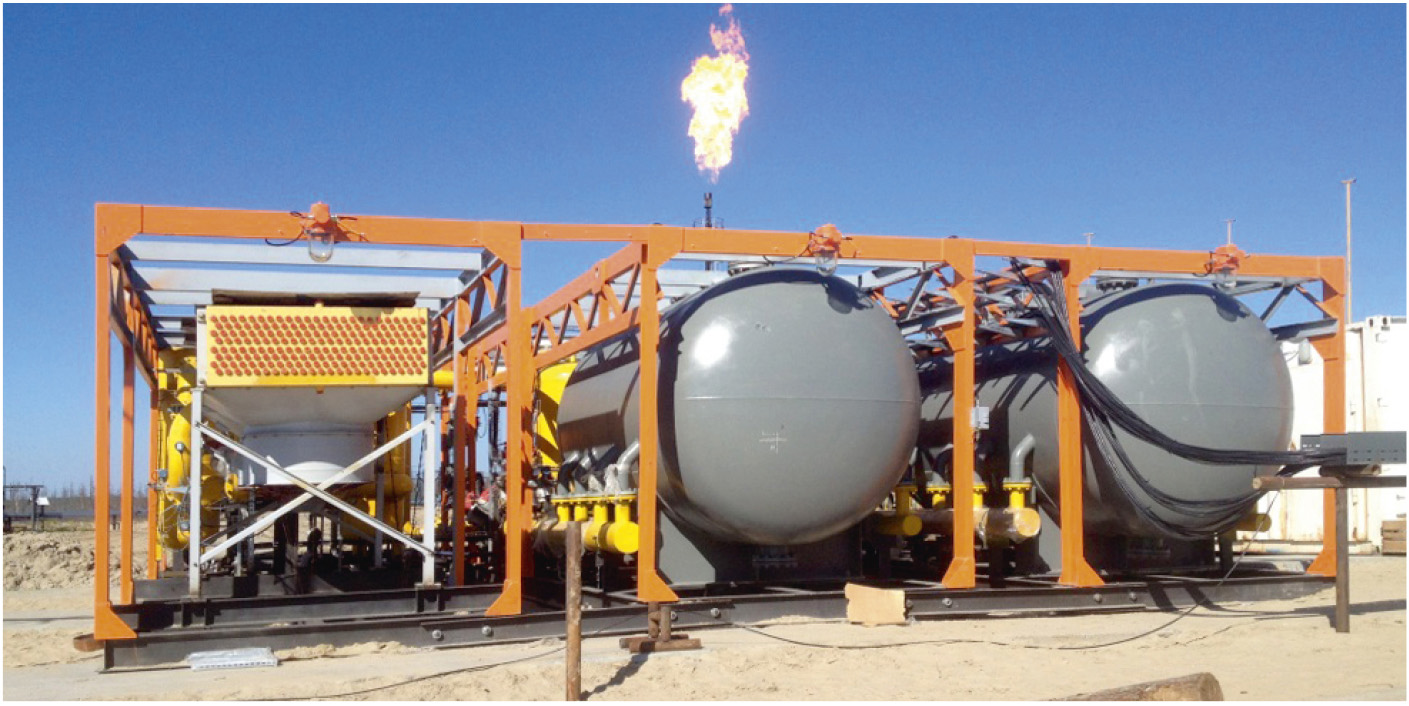
Краткая характеристика технологического процесса
Технологическая схема УПГ представлена на рис. 2.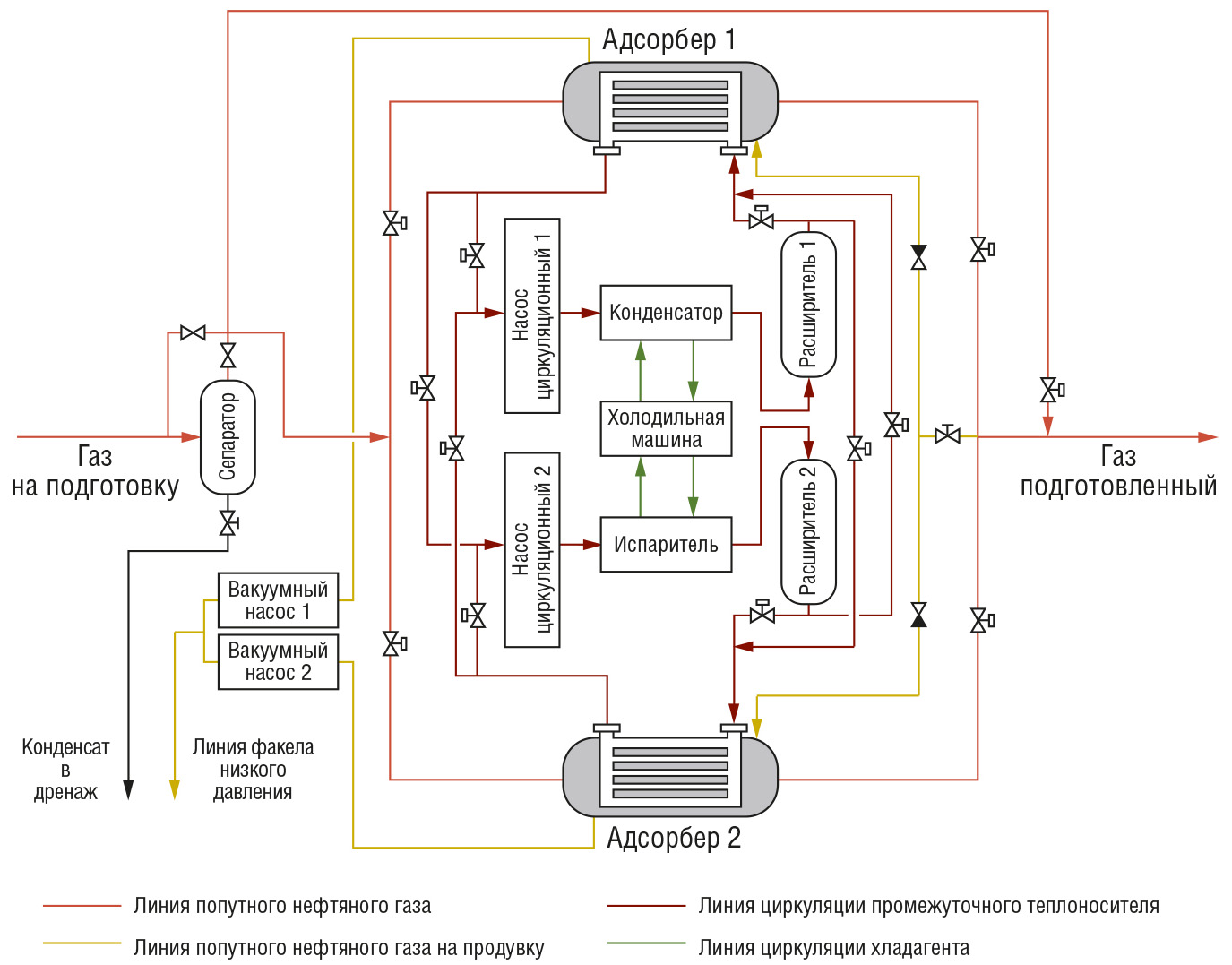
Исходный газ, содержащий нежелательные примеси (тяжёлые углеводороды, различные примеси, влагу и т.п.), поступает на предварительную очистку в газовый сепаратор. В сепараторе из исходного газа отделяют капельную жидкость и улавливают механические примеси. Капельная жидкость по мере накопления автоматически через регулирующий кран сливается в дренажную линию.
Очищенный от капельной жидкости и механических примесей газ поступает на адсорбционную подготовку в адсорбер № 1. По мере прохождения газа через слой адсорбента происходит поглощение тяжёлых компонентов газа и повышение его метанового числа. Подготовленный газ через регулятор давления поступает в газопоршневые генераторы. Адсорбер № 2 находится на стадии десорбции одновременно с проведением процесса адсорбции в адсорбере № 1.
Для повышения эффективности процесса десорбции применяются следующие технологические мероприятия:
1) понижение давления (вакуум) достигается с помощью вакуумного насоса;
2) повышение температуры за счёт использования тепла, вырабатываемого в процессе работы холодильной машины (теплового насоса);
3) продувка адсорбера чистым (подготовленным) газом.
Совокупное использование этих факторов позволяет провести процесс глубокой десорбции в течение 15–20 минут и полностью подготовить адсорбент к процессу.
По мере окончания процесса десорбции проходит продувка адсорбера подготовленным газом для его окончательной продувки и выноса оставшихся тяжёлых углеводородов с выравниванием давления в адсорберах № 1 и № 2 до рабочего. Далее осуществляется переключение между адсорбером № 1 и № 2.
В начальный момент переключения оба адсорбера работают параллельно с по-следующим перекрытием адсорбера № 1 и выводом его на процесс десорбции.
Структура системы управления УПГ
САУ УПГ состоит из трёх уровней – нижнего, среднего и верхнего. Общая структура системы представлена на рис. 3.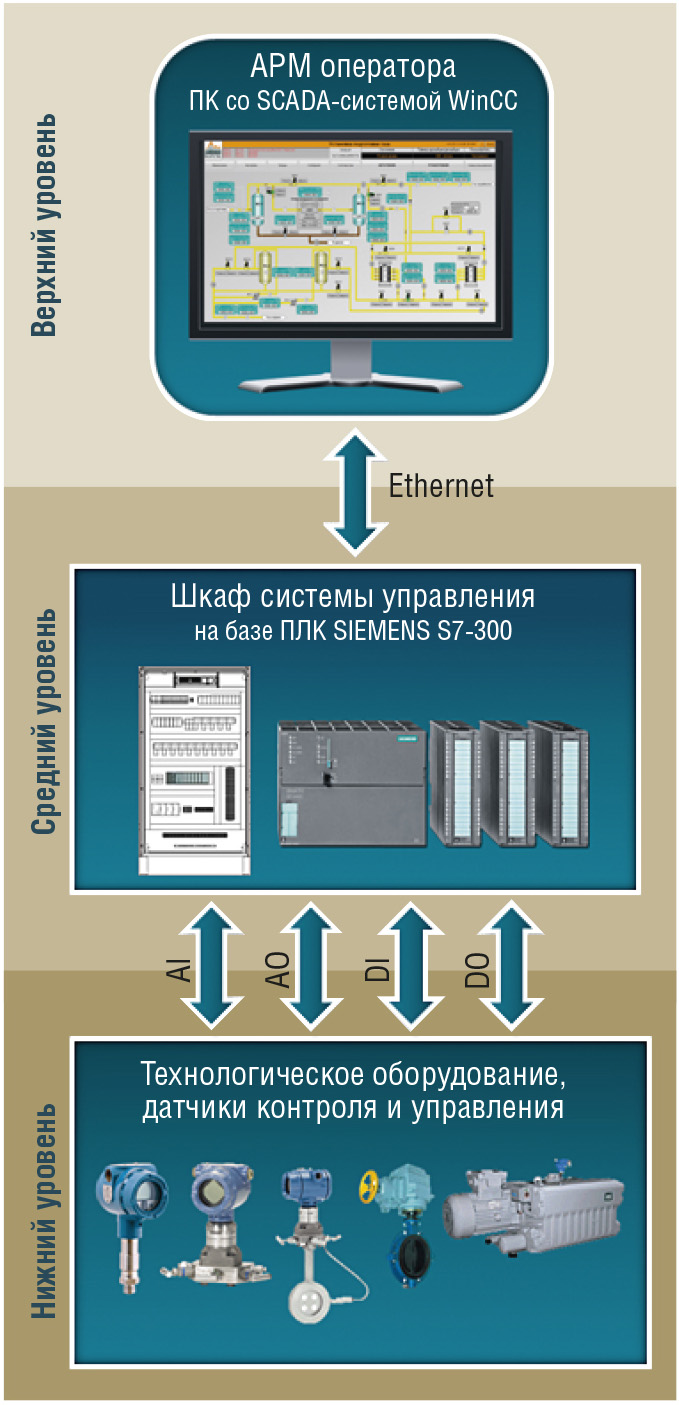
Нижний уровень включает в себя датчики, исполнительные механизмы, устройства сигнализации, установленные на технологическом оборудовании.
Его функциями являются:
- измерение параметров техпроцесса и передача данных на средний уровень системы;
- управление исполнительными механизмами (насосами, клапанами, затворами с электроприводами и т.п.), контроль их состояния и формирование соответствующих сигналов на средний уровень;
- оповещение персонала при помощи светозвуковой сигнализации о возникновении аварийных ситуаций (загазованности, пожаре, аварии установки).
- сбор оперативной информации и первичная обработка аналоговых сигналов постоянного тока с измерительных преобразователей (датчиков) технологических параметров и параметров состояния оборудования;
- контроль аварийных отклонений параметров от установленных регламентных границ и в случае обнаружения отклонений выдача световой и звуковой сигнализации об аварийных ситуациях и отклонениях параметров;
- формирование управляющих воздействий на исполнительные механизмы по заданным алгоритмам, поддержание технологических режимов в требуемых пределах.
Аппаратная часть
Рассмотрим аппаратную часть реализации системы управления. В качестве приборов дистанционного контроля давления и температуры использовались датчики производства ЗАО «Промышленная группа «Метран». На установке подготовки газа ведётся учёт и регистрация расхода попутного нефтяного газа на входе, очищенного и подготовленного газа на выходе, а также тяжёлых компонентов попутного нефтяного газа, получаемых в процессе десорбции, применены расходомеры Rosemount. Непрерывный контроль концентрации взрывоопасных газов обеспечивается путём применения стационарного модульного газоанализатора ГСМ-03 НПП «Томская электронная компания», состоящего из детекторных элементов, установленных по периметру блока, и устройства сигнализации, установленного в шкафу управления.Комплекс технических средств среднего уровня представлен в виде двух шкафов:
- шкаф системы управления (рис. 4);
- шкаф управления вакуум-насосами.
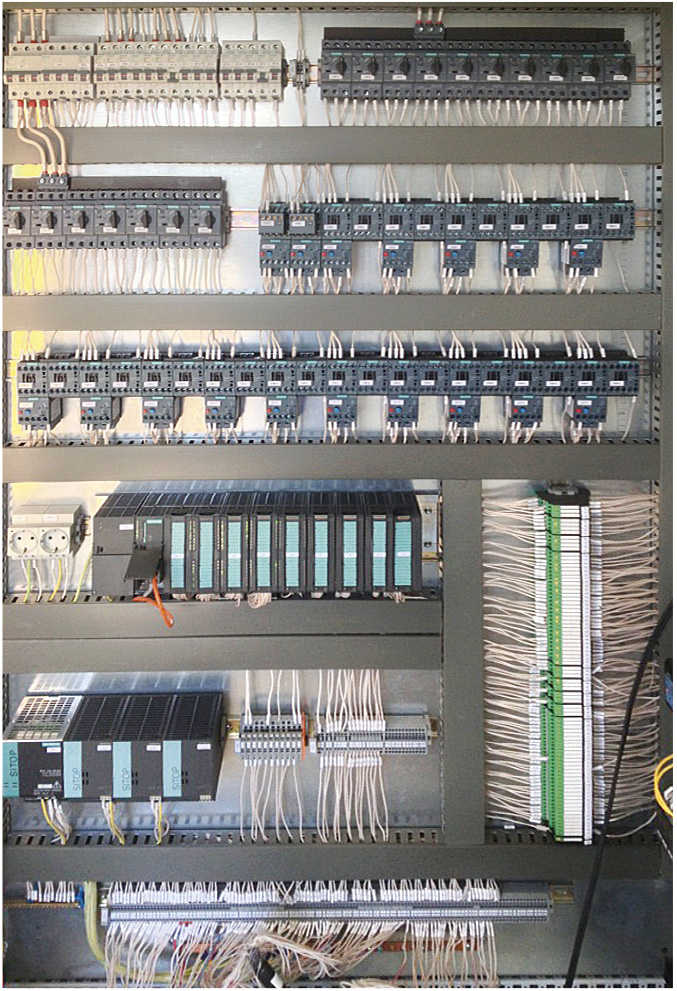
Шкаф системы управления и шкаф управления вакуум-насосами выполнены на базе системных шкафов серии SE 8 фирмы Rittal с габаритными размерами 200×2000×600 мм и 600×600×2000 мм соответственно. В шкафу установлены две вентиляционные решётки с входными
и выходными фильтрами. Обеспечение бесперебойной работы приборов и средств автоматизации реализуется с помощью линейно-интерактивного источника бесперебойного питания (ИБП) APC Smart-UPS 1500VA LCD RM 2U 230V мощностью 1500 В·А. Функция автоматической регулировки напряжения позволила обеспечить работу ИБП без перехода на питание от аккумулятора в условиях нестабильного электроснабжения. ИБП выполнен в стоечном исполнении и установлен на направляющих в верхней части шкафа управления. Система автоматизации построена на базе контроллеров SIEMENS S7-300. Центральный процессор CPU 314C-2 PN/DP оснащён картой памяти и встроенными интерфейсами Ethernet (PROFINET) и RS-485 (PROFIBUS DP).
Шкаф системы управления имеет следующие каналы ввода-вывода:
- входные аналоговые сигналы 4…20 мА (34 сигнала);
- входные дискретные сигналы типа «сухой» контакт (72 сигнала);
- выходные дискретные сигналы типа «сухой» контакт (64 сигнала).
ти D1010D/B фирмы G.M. International (рис. 5). Для обеспечения искрозащиты цепей дискретных сигналов стандарта NAMUR в шкафу установлены двухканальные барьеры искробезопасности D1030D/B. Связь со шкафом управления вакуум-насосами осуществляется по протоколу PROFIBUS DP.
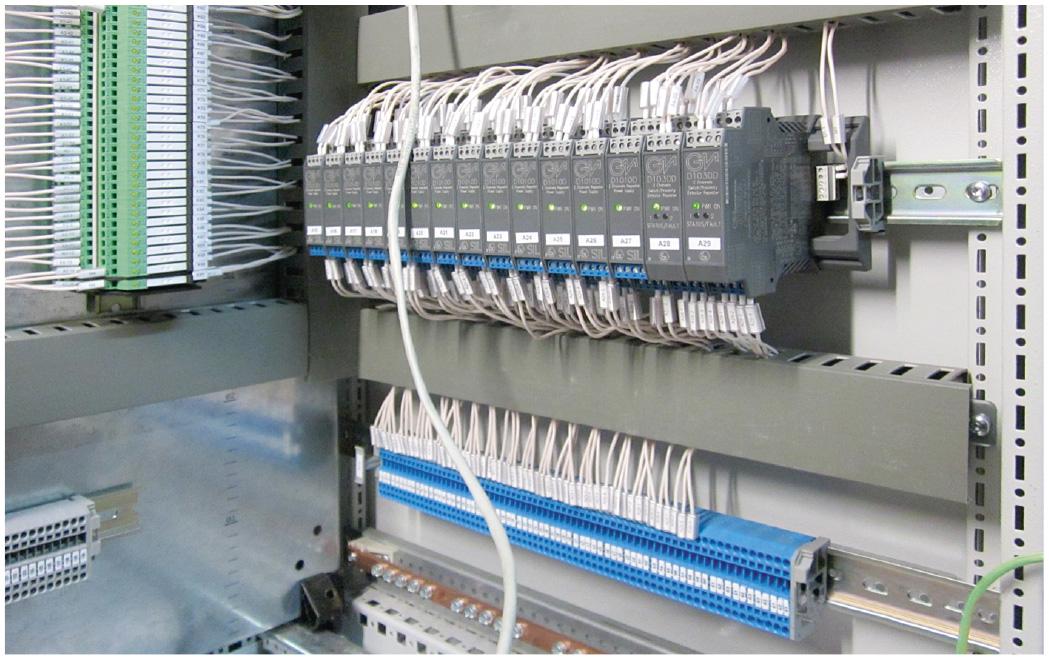
Передача данных на верхний уровень (АРМ оператора) осуществляется по волоконно-оптической сети Ethernet через коммуникационный драйвер SIMATIC S7 Protocol Suite. Для реализации волоконно-оптической связи использованы коммутаторы Moxa EDS-308-SS-SC.
В шкафу управления насосами установлены два частотных преобразователя SINAMICS G120 фирмы SIEMENS мощностью 7,5 кВт. Частотные преобразователи построены по модульному принципу и включают в себя силовой модуль PM240, управляющий модуль PROFIBUS DP, сетевой и выходной дроссели. Для упрощённого ввода в эксплуатацию, настройки, контроля и управления частотными преобразователями на передней дверце шкафа управления насосами установлены две панели оператора BOP-2. Значения и единицы измерения отображаются на 5-разрядном дисплее. Панель оператора позволяет переключаться между ручным и автоматическим режимами работы привода, контролировать скорость привода и основные электрические характеристики (ток, частоту, мощность и т.д.).
Подключение внешних кабелей к шкафам управления осуществляется пружинными клеммами фирмы WAGO. Подвод кабеля к шкафам – снизу. Для удобства монтажа и обслуживания шкафы установлены на цоколь высотой 200 мм. С целью защиты цепей 4…20 мА от токов короткого замыкания применены клеммы с держателями плавких предохранителей 5×20 мм. Управление и защита силовых цепей приводов запорно-регулирующей арматуры осуществляется при помощи автоматических выключателей 3RV и реверсивных контакторов 3RA с тепловым реле 3RU фирмы SIEMENS.
Верхний уровень (АРМ оператора) реализован на базе персонального компьютера с программным обеспечением WinCC v7.0 и набором лицензий WINCC-V7 RC 100K PTg 512 ATg. Программное обеспечение системы управления технологическим процессом (средний уровень) разработано в пакете STEP 7 фирмы SIEMENS. В качестве операционной среды для АРМ оператора используется операционная система Windows XP SP3.
Программное обеспечение АРМ оператора выполняет следующие основные функции:
- отображение состояния технологического оборудования УПГ;
- отображение текущих технологических параметров УПГ;
- световая сигнализация при отклонении технологического режима от нормы;
- световая сигнализация при аварийных ситуациях;
- квитирование оператором предаварийных и аварийных ситуаций;
- выбор оператором режимов работы технологического оборудования;
- осуществление ручного управления технологическим оборудованием;
- ввод технологических уставок;
- ведение архива значений технологических параметров;
- ведение архива журнала событий.
- «Оператор» – возможны просмотр технологической информации, квитирование аварийных ситуаций, управление технологическим оборудованием;
- «Технолог» – возможны все действия уровня «Оператор», настройка уставок;
- «Программист» – доступ ко всем функциям системы, включая определение списка пользователей, изменение адресов связи с устройствами, единиц измерения переменных и т.д.
В основном окне (рис. 6) представлена мнемосхема всей УПГ.
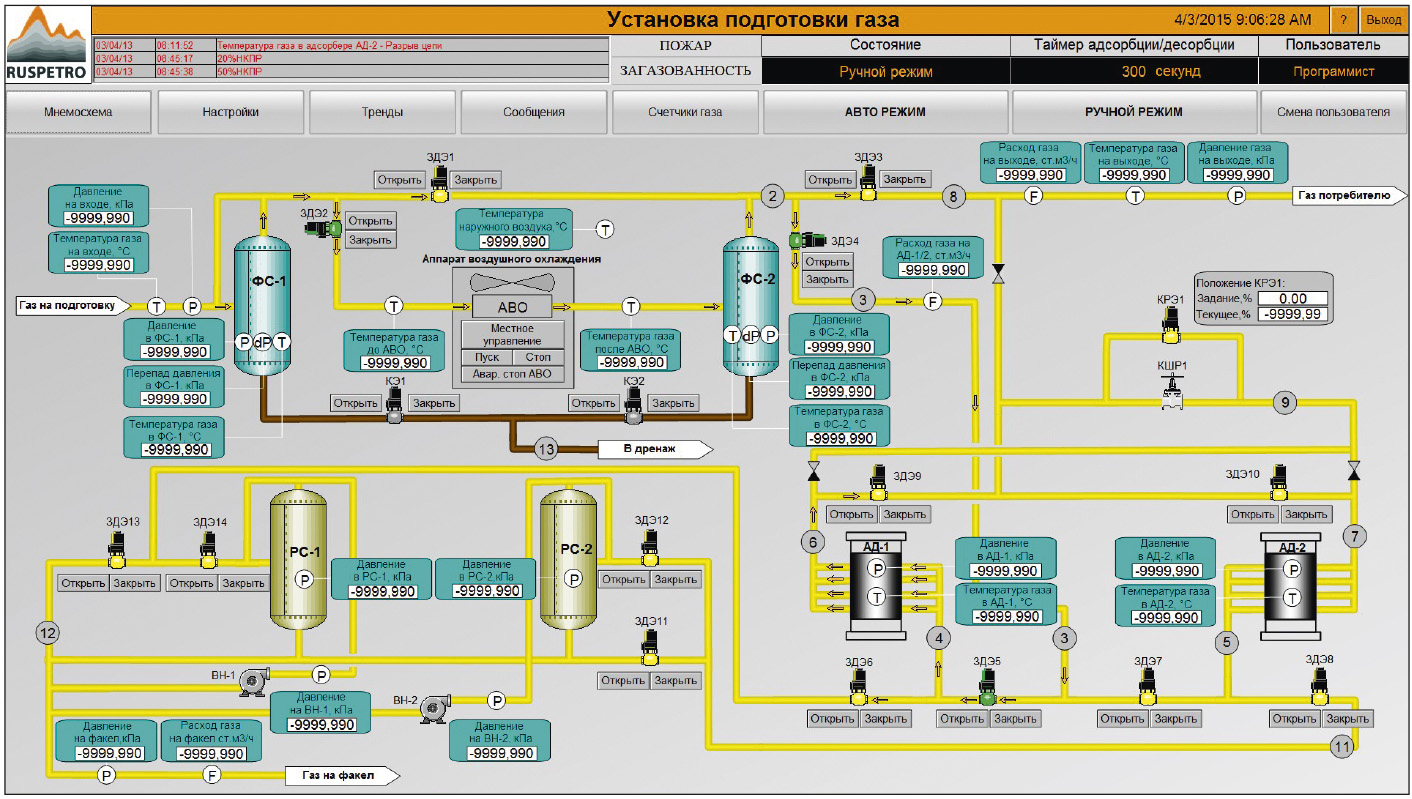
В верхней части основного окна отображены:
- кнопка «Мнемосхема» – по нажатию вызывается главная мнемосхема установки подготовки газа;
- поле отображения активных сообщений (достижение аварийных значений технологических параметров);
- кнопка «Настройки» – по нажатию вызывается меню настройки, которое позволяет задать время цикла адсорбции/десорбции, диапазоны измерения датчиков, уставки регулирования давления;
- кнопка «Тренды» для вызова мнемо-схемы трендов;
- кнопка «Сообщения» для вызова мнемосхемы сообщений оператора;
- кнопка «Счётчики газа» для вызова мнемосхемы показаний датчиков расхода; на мнемосхеме отображены значения объёмного и приведённого к нормальным условиям расхода попутного нефтяного газа;
- кнопки «Авторежим»/«Ручной режим» позволяют перевести установку в автоматический или ручной режим;
- кнопка вызова окна регистрации – для смены уровня доступа;
- текущий режим работы установки;
- оставшееся время режима адсорбции/десорбции;
- поле отображения текущего пользователя;
- кнопка выхода из режима RunTime.
- жёлтый, если значение аналогового сигнала превышает предупредительный уровень;
- красный, если значение аналогового сигнала превышает аварийный уровень.
Заключение
Адсорбционные установки по подготовке попутного нефтяного газа по метановому числу с описанной системой автоматического управления прошли успешные испытания и введены в эксплуатацию на объектах Красноленинской группы месторождений Ханты-Мансийского автономного округа. В процессе работы УПГ доказала работоспособность принятых технических решений. Качество подготовленного попутного нефтяного газа позволило существенно увеличить мощность газопоршневых электрогенераторов в режиме отсутствия детонации. ●E-mail: sharipovbulat@gmail.com
Если вам понравился материал, кликните значок - вы поможете нам узнать, каким статьям и новостям следует отдавать предпочтение. Если вы хотите обсудить материал - не стесняйтесь оставлять свои комментарии : возможно, они будут полезны другим нашим читателям!