Введение
Коченёвский НПЗ в настоящее время находится в процессе масштабной модернизации. Это современное и динамично развивающееся предприятие, в структуре которого имеются все подразделения, обеспечивающие производственную деятельность на высоком технологическом и экологическом уровне. На заводе происходит непрерывное совершенствование производственных технологий, повышается безопасность труда.В соответствии с инвестиционным планом развития предприятия в 2013 году руководством было принято решение о проектировании и строительстве резервуарного парка светлых и тёмных нефтепродуктов объёмом 31 тыс. м3.
Первая очередь резервуарного парка объёмом 19 тыс. м3 введена в промышленную эксплуатацию в сентябре 2014 г., вторая очередь объёмом 12 тыс. м3 – в июле 2015 г.
В состав резервуарного парка входит следующее основное технологическое оборудование:
- 16 резервуаров РВС (резервуар вертикальный стальной) разного объёма (12 шт. – 2000 м3, 1 шт. – 4000 м3, 3 шт. – 1000 м3);
- насосная сырья и нефтепродуктов;
- 6 установок налива нефтепродуктов в автомобильные цистерны;
- 2 установки слива нефти из автомобильных цистерн;
- 3 дренажные ёмкости.
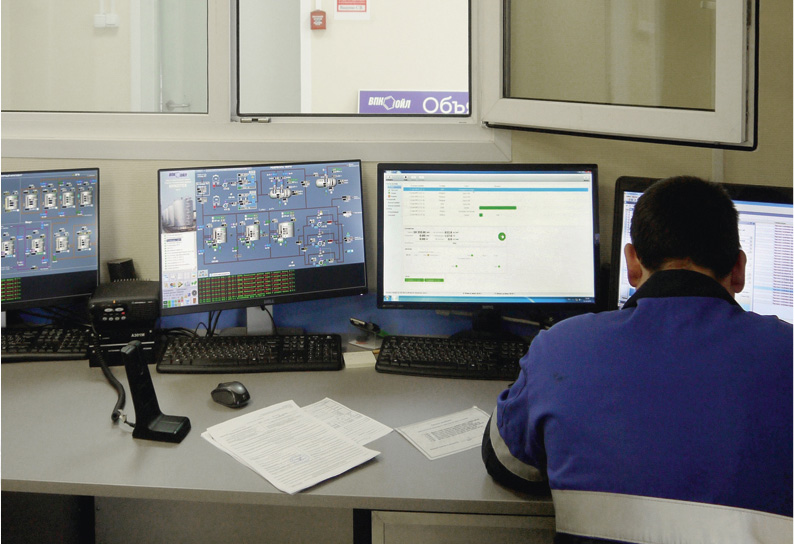
Нефть из автомобильных цистерн и с железнодорожной (ж/д) эстакады № 1 поступает в сырьевые резервуары парка, откуда насосами подаётся на установку атмосферно-вакуумной ректификации ЭЛОУ-АВТ-600. Нефтепродукты из этой установки поступают на хранение в резервуары парка. Отгрузка светлых нефтепродуктов выполняется через установки налива в автомобильные цистерны и ж/д эстакаду № 2, отгрузка тёмных нефтепродуктов – через ж/д эстакаду № 1.
В процессе создания АСУ ТП резервуарного парка ООО НТФ «Инкотех» были выполнены следующие работы:
- разработка проекта автоматизации;
- разработка проектно-конструкторской и эксплуатационной документации на шкафы управления;
- комплектация и изготовление шкафов контроля и управления на производственном участке ООО НТФ «Инкотех»;
- разработка пользовательского программного обеспечения АСУ ТП;
- пусконаладочные работы по АСУ ТП, включая:
– авторский надзор за монтажом шкафов управления и подключением к ним датчиков и исполнительных механизмов (ИМ);
– проверку функций приёма измерительной информации и управления исполнительными механизмами;
– проверку системы противоаварийной защиты (ПАЗ);
– обучение оперативного и эксплуатационного персонала;
– участие в комплексном опробовании системы контроля и управления резервуарным парком;
– актуализацию программного обеспечения и исполнительной документации по результатам комплексного опробования.
Назначение системы
Созданная АСУ ТП предназначена для выполнения следующих основных функций:- контроль технологических параметров: расходов, уровней, плотностей, температур и давлений;
- контроль (на основе показаний массовых расходомеров) масс, объёмов, плотностей и температур нефтепродуктов, перекачиваемых по входным и выходным трубопроводам резервуарного парка;
- противоаварийная защита:
– резервуаров и дренажных ёмкостей от перелива и опорожнения;
– насосных агрегатов в соответствии с требованиями технических условий (ТУ) заводов-изготовителей;
- дистанционное управление ИМ;
- автоматическое регулирование:
– давлений на нагнетании насосов и расходов перекачиваемой жидкости путём изменения частоты вращения их электроприводов;
– скоростей вращения электродвигателей мешалок в зависимости от уровня нефтепродукта в резервуаре;
- плавный пуск насосов и мешалок;
- автоматический пуск резервного насоса подачи нефти на установку ЭЛОУ-АВТ-600 при отказе основного;
- контроль загазованности в обваловании резервуаров, в рабочей зоне насосной;
- включение устройств световой и звуковой сигнализации для оповещения персонала на территории резервуарного парка о возникновении загазованности;
- ручной ввод значений плотностей нефтепродуктов при нормальных условиях по данным анализов проб, выполненных в центральной заводской лаборатории;
- автоматический расчёт по каждому резервуару:
– усреднённой температуры нефтепродукта на основе показаний датчика уровня и многозонного датчика температуры;
– плотности, приведённой к рабочим условиям на основе данных лабораторного анализа и усреднённой температуры;
– объёма остатка на основе показаний датчика уровня и калибровочной таблицы;
– массы остатка;
– для нефтяных резервуаров – скорости перемещения понтона и движения нефти в трубопроводах приёмного и раздаточного патрубков на основе показаний аналогового датчика уровня в резервуаре;
– плотности при нормальных условиях по показаниям массовых расходомеров при выполнении операции откачки;
- контроль работоспособности:
– дублированных контроллеров;
– локальной вычислительной сети АСУ ТП;
– коммуникационных процессоров устройств связи с объектом (УСО) и модулей ввода/вывода сигналов;
– источников вторичного электропитания;
– контуров регулирования и ИМ (электроприводной регулирующей и запорной арматуры с дистанционным управлением, насосов, мешалок);
- архивирование значений технологических параметров;
- отображение текущей и архивной информации о работе резервуарного парка в виде трендов, графиков и сообщений;
- ведение протокола событий путём сохранения в архиве системы сообщений: информационных, предупредительных, предаварийных, о действиях оператора и неисправностях оборудования;
- включение звуковой сигнализации на АРМ оператора при нарушениях норм технологического режима;
- защита от несанкционированного вмешательства в технологический процесс на основе системы парольного доступа к функциям контроля и управления;
- ведение внутрипаркового учёта и расчёт балансов движения товарной продукции и сырья по предприятию;
- формирование отчётной документации (рапортов смен, баланса за сутки, баланса за период);
- интеграция в АСУ ТП резервуарного парка функций контроля и управления, реализуемых комплектными установками налива нефтепродуктов в автоцистерны, включая контроль заземления цистерн, состояния датчиков предельного налива, положения трапов устройств налива, формирование заданий по количеству (массе) отпускаемых/принимаемых нефтепродуктов, запуск/останов насосов парка по командам, поступающим из систем управления установок налива;
- обмен данными с внешними АСУ ТП по протоколам OPC DA и TCP/IP.
Структура АСУ ТП
АСУ ТП имеет трёхуровневую структуру:- Нижний уровень обеспечивает сбор данных о параметрах технологического процесса и состоянии оборудования, реализует управляющие воздействия и включает:
– контрольно-измерительные приборы;
– ИМ (насосы, электроприводные регулирующие клапаны, запорная арматура с электроприводом, мешалки);
– комплектные установки слива/налива сырья и нефтепродуктов из автомобильных цистерн и в них.
- Средний уровень обеспечивает:
– противоаварийную защиту оборудования и технологических процессов;Основой среднего уровня являются дублированные промышленные контроллеры и искробезопасные и общепромышленные устройства ввода/вывода аналоговых и дискретных сигналов.
– сбор информации о параметрах процессов приёма, хранения и отгрузки нефтепродуктов;
– автоматическое регулирование и управление технологическими процессами слива/налива сырья и нефте-продуктов;
– выполнение необходимых расчётов.
- Верхний уровень обеспечивает:
– централизованный контроль и дистанционное управление технологическими процессами приёма, хранения и отгрузки нефтепродуктов из помещения операторной;Основой верхнего уровня является АРМ оператора резервуарного парка, реализованное на базе двух промышленных системных блоков ПЭВМ и мониторов.
– накопление архивной информации, расчёт балансов, формирование и выдачу отчётных документов;
– дистанционный доступ руководителей предприятия к информации о параметрах, характеризующих текущее состояние резервуарного парка.
Структурная схема АСУ ТП приведена на рис. 3.
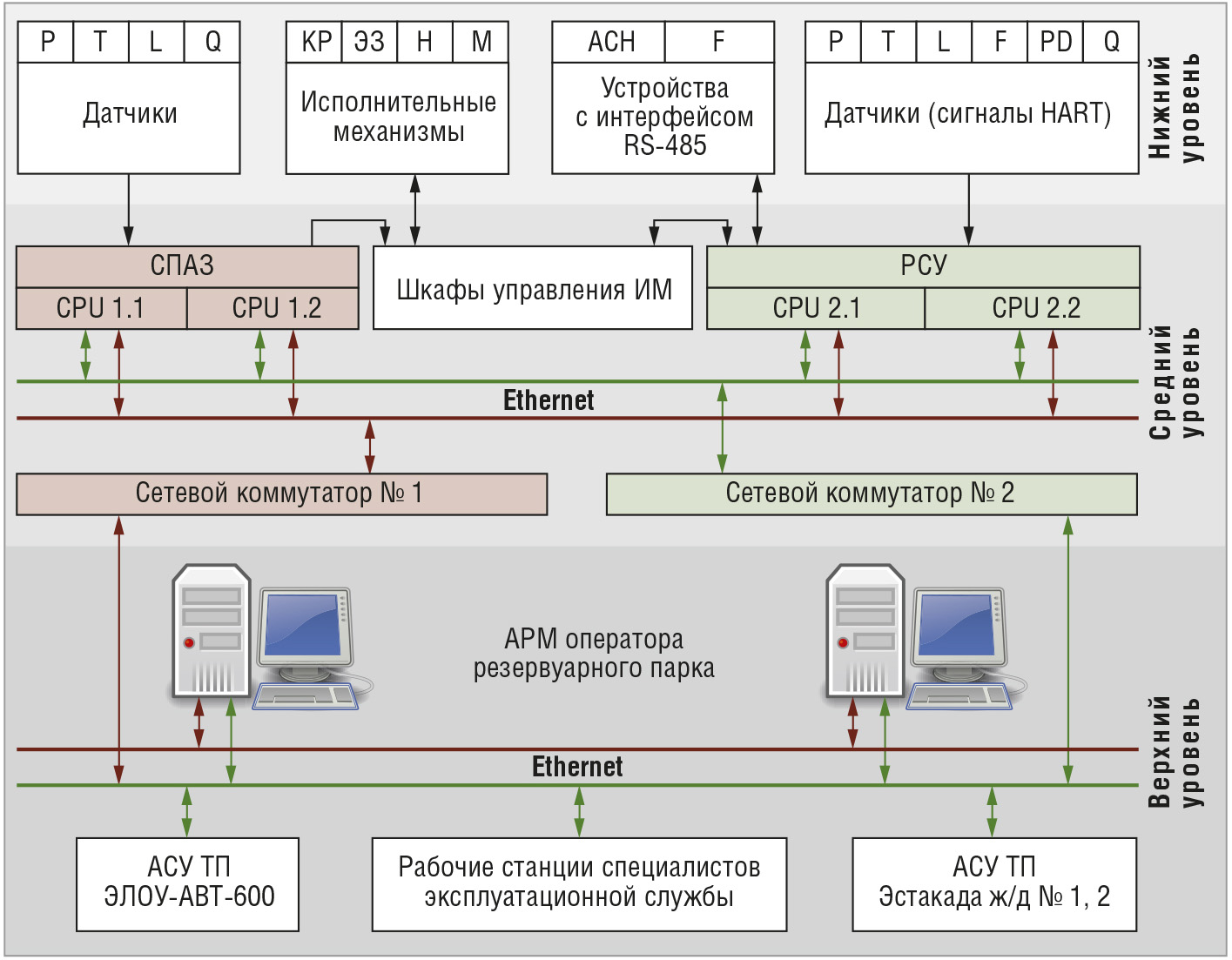
Условные обозначения: КР – клапан регулирующий, ЭЗ – электрозадвижка, Н – насос, М – мешалка, АСН – автоматизированная система налива, СПАЗ – система противоаварийной защиты, РСУ – распределённая система управления, CPU – контроллер, ИМ – исполнительные механизмы, P – давление, T – температура, L – уровень, Q – концентрация, F – расход, PD – перепад давления.
Технические средства среднего уровня АСУ ТП, включая контроллеры, модули ввода/вывода, сетевые коммутаторы, пусковую аппаратуру электроприводов и пр., размещены в шкафах, смонтированных в помещении электрощитовой здания операторной резервуарного парка. Общее количество шкафов АСУ ТП составляет 16 шт., из них шкафов контроллерного управления – 4 шт., управления электроприводами регулирующей и запорной арматуры – 4 шт., силового управления – 8 шт.Характеристики информационной нагрузки АСУ ТП приведены в табл. 1.
Общее количество каналов ввода/вывода АСУ ТП составляет:
- аналоговых и дискретных – 807 шт.;
- цифровых (протоколы HART и Modbus RTU) – 328 шт.
- запорную арматуру с электроприводами фирмы AUMA – 30 шт.;
- регулирующие клапаны ESD-VCX-90 производства фирмы «Элеси» – 10 шт.;
- мешалки НХ 63 – 5 шт.;
- насосы разных типов: НКВ, КМН, УОД, ГНЦВ и др. – 20 шт.;
- установки АТ-8870 налива нефтепродуктов в автомобильные цистерны – 6 шт.;
- установки АТ-8870 слива нефти из автомобильных цистерн – 2 шт.
Аппаратное обеспечение
АСУ ТП построена на базе:- IBM РС-совместимых промышленных контроллеров XP-8341-ATOM-CE6 (РСУ), XP-8041-CE6 (СПАЗ) фирмы ICP DAS;
- модулей ввода/вывода искробезопасных сигналов серии I.S.1 фирмы R.Stahl;
- модулей вода/вывода неискробезопасных сигналов серии I-8000 фир-мы ICP DAS, которые устанавливаются в крейт-контроллеры I-8810 или I-8410.
Контроллеры одной пары являются дублированными и работают в режиме «горячего» резерва, они идентично сконфигурированы, соединены между собой нуль-модемным кабелем и по двум независимым Ethernet-сетям. Исполнение программы управления, а также управление работой модулей ввода/вывода и взаимодействие с подсистемой верхнего уровня выполняет активный контроллер. Активным становится контроллер, который после включения электропитания обоих контроллеров первым принял управление модулями ввода/вывода. При этом второй контроллер становится пассивным, обеспечивая синхронизацию собственных данных на основе информации активного контроллера, а также выполнение мониторинга его работоспособности. При отказе активного контроллера пассивный контроллер становится активным и выполняет функции управления. Переключение управления между контроллерами осуществляется безударно, поскольку резервный контроллер располагает полной актуальной информацией о состоянии каналов ввода/вывода и программных переменных активного контроллера.
Системы РСУ и ПАЗ имеют независимые друг от друга подсистемы ввода/вывода, поэтому работа РСУ не влияет на работу СПАЗ, как в штатном режиме, так и в случае нарушения работоспособности.
Обмен данными между управляю-щими контроллерами и устройствами ввода/вывода выполняется по интерфейсу RS-485. Для связи с коммуникационными процессорами системы R.Stahl используется протокол Modbus RTU, для связи с крейт-контроллерами I-8x10 – протокол DCON.
Все устройства с интерфейсом RS-485, расположенные во взрывоопасных зонах, подключаются к контроллерам через одноканальные барьеры искрозащиты D1061S (GM International). Для подключения используются встроенные COM-порты контроллеров, а также COM-порты плат расширения ICP DAS.
Многозонные датчики температуры в резервуарах парка, измерительная
информация из которых вычитывается по протоколу HART, подключаются к модулям шлюза HART/Modbus HRT710 через двухканальные барьеры искрозащиты KFD2-STC4-Ex2 производства компании Pepperl+Fuchs. Модули HRT710 подключаются к контроллерам по интерфейсу RS-485, протокол Modbus RTU.
Для запуска/останова насосов и мешалок используется следующее оборудование:
- преобразователи частоты ATV61HD (Schneider Electric) для управления скоростью вращения мешалок;
- преобразователи частоты E2-8300 (Веспер) для управления производительностью насосов;
- устройства плавного пуска насосов Altistart 48 (Schneider Electric);
- силовая аппаратура (автоматические выключатели, контакторы, тепловые реле) фирмы Hyundai;
- промежуточные реле фирм Relpol и Phoenix Contact.
Резервированное питание 24 В по-стоянного тока в шкафах контроля и управления обеспечивают дублированные источники серий DSP (TDK-Lambda) и QUINT (Phoenix Contact), выходы которых соединены через развязывающие диоды QUINT-DIODE/40.
В состав АРМ оператора входят две рабочие станции на базе промышленных шасси IPC 610-L производства компании Advantech, размещённые в 19” стойке пульта оператора. Рабочие станции укомплектованы 24″ TFT-мониторами, клавиатурами и манипуляторами мышь. Для звуковой сигнализации используются акустические колонки. Вывод оперативной и архивной информации на бумажные носители обеспечивается на сетевой лазерный принтер.
Связь рабочих станций АРМ с дублированными контроллерами осуществляется по сети Ethernet, протокол TCP/IP. Для организации сети используются неуправляемые резервированные коммутаторы EDS-316 (MOXA).
Внешний вид шкафов управления приведен на рис. 4, 5, 6.
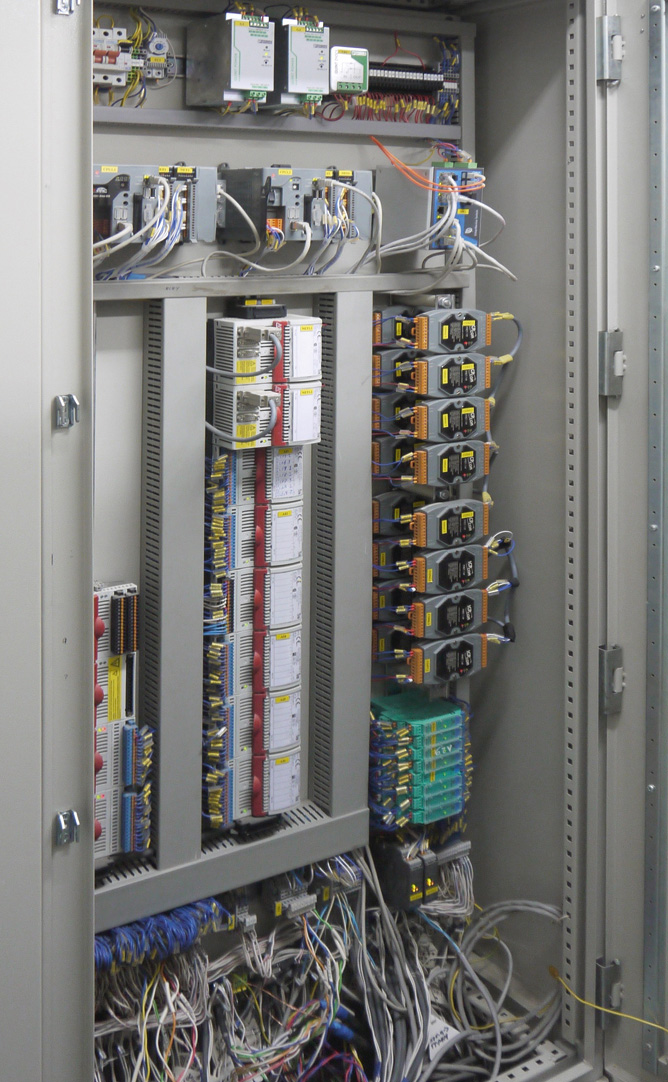
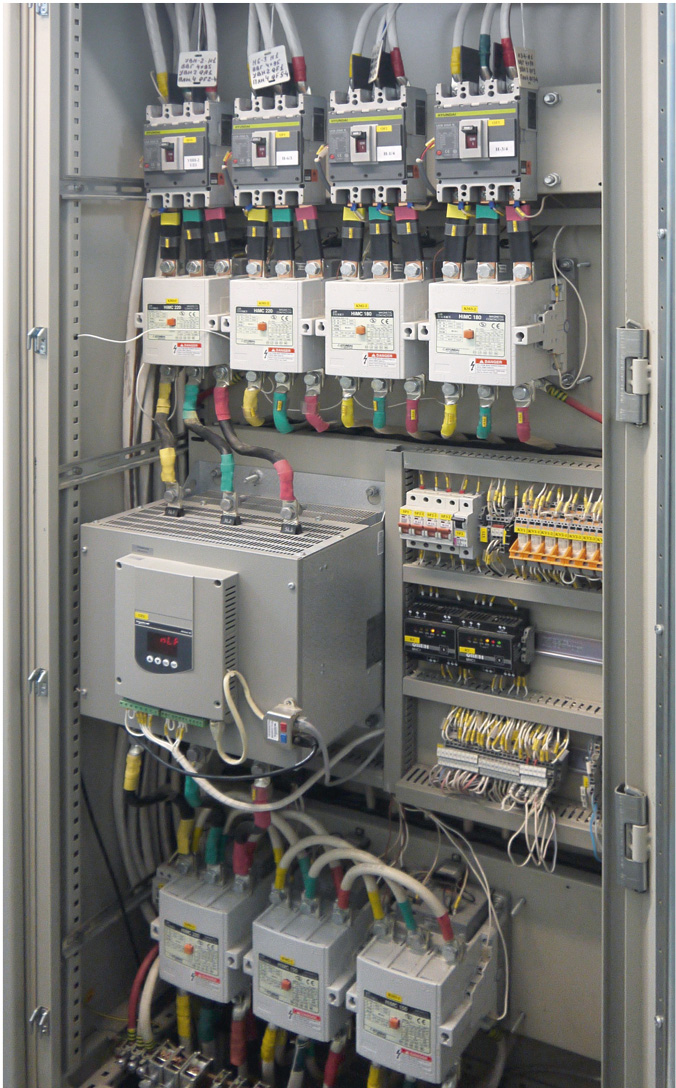
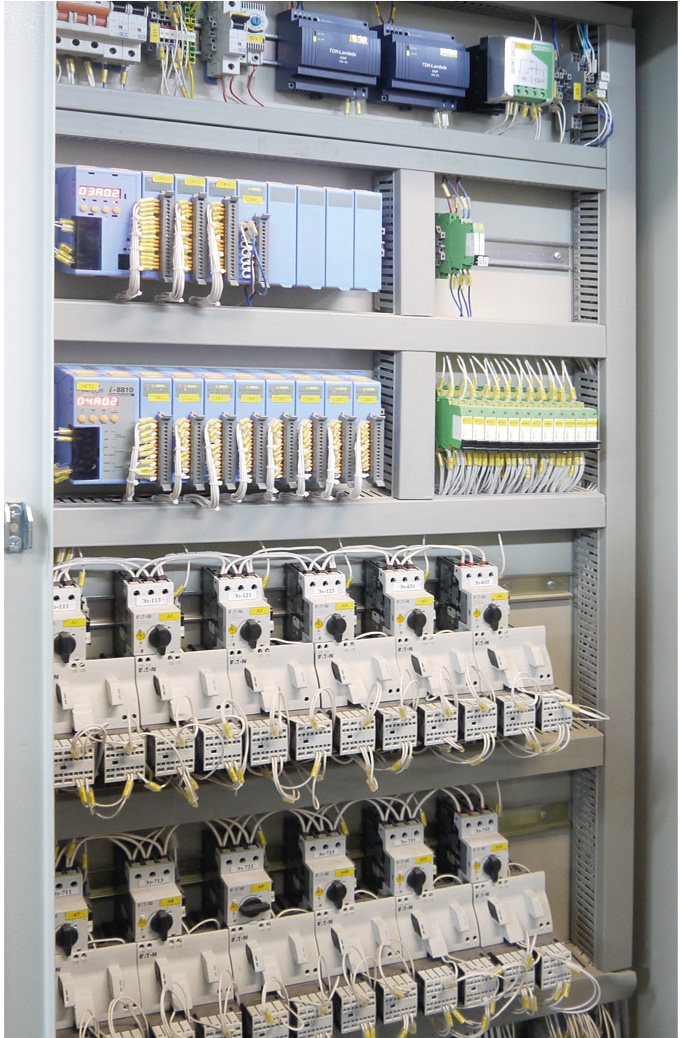
Технические решения
При проектировании и внедрении АСУ ТП были применены следующие основные технические решения:- Массовые кориолисовые расходомеры Promass 83f (Endress+Hauser) системы учёта (10 шт.) подключены к контроллеру РСУ по интерфейсу RS-485, обмен данными с ними выполняется по протоколу Modbus RTU. Подключение расходомеров по интерфейсу RS-485 позволило:
– обеспечить приём в систему данных мгновенных значений массовых и объёмных расходов, интегральных массовых и объёмных расходов, температур и плотностей нефтепродуктов;
– обеспечить высокий уровень диагностики состояния расходомеров (статус, код ошибки);
– повысить точность измерения и исключить потерю информации при отсутствии связи расходомеров с контроллером РСУ (расчёт интегральных значений выполняется на уровне расходомеров и не зависит от работоспособности АСУ ТП);
– уменьшить количество контрольных кабелей в сравнении с классическим решением приёма измерительной информации на основе сигналов 4–20 мА.
- В каждом резервуаре парка установлено по пять температурных сенсоров, чувствительные элементы которых расположены на разных высотах. Все сенсоры подключены к нормирующим преобразователям TMT82, размещённым в соединительной коробке, установленной на крыше резервуара. Преобразователи термодатчиков одного резервуара соединены между собой по одному каналу 4–20 мА и объединены в сеть HART. Для каждого преобразователя установлен свой HART-адрес. Контроллер РСУ через модуль шлюза Modbus/HART (HRT710) последовательно опрашивает преобразователи температуры и на основе их показаний, а также показаний аналогового датчика уровня рассчитывает среднюю температуру нефтепродукта в резервуаре. Такая схема позволила использовать магистральные кабели с меньшим количеством жил и уменьшить количество каналов ввода искробезопасных сигналов, которые потребовались бы в случае приёма от каждого термодатчика индивидуального сигнала 4–20 мА.
- Комплектные установки слива/налива сырья и нефтепродуктов (8 шт.) соединены в сеть RS-485, обмен данными между установками и контроллером РСУ АСУ ТП резервуарного парка обеспечивается по протоколу Modbus RTU. По командам, поступающим с местных постов управления этими установками, контроллер РСУ пускает/останавливает соответствующий насос. Программная коммутация насосов и комплектных установок налива нефтепродуктов выполняется через специальные экранные формы. При срабатывании сигнализаторов загазованности, нарушения заземления или перелива цистерны контроллер РСУ останавливает соответствующий насос. Разработанные фрагменты мнемосхем позволяют оператору формировать задание на налив светлых нефтепродуктов в автомобильные цистерны, управлять процессом налива и контролировать показания датчиков установок налива через единый операторский интерфейс.
- Устройства плавного пуска (УПП) и преобразователи частоты (ПЧ) соединены в сеть RS-485, обмен данными с контроллером РСУ выполняется по протоколу Modbus RTU. Такое подключение позволило:
– обеспечить приём в АСУ ТП следующих параметров УПП и ПЧ: токов, моментов, мощностей, времён работы двигателей, тепловых состояний, статусов и кодов неисправностей;
– выполнять пуск нескольких (до пяти) электродвигателей насосов разной мощности через одно УПП за счёт возможности программно изменять в УПП уставку номинального тока электродвигателя перед каждым пуском насоса;
– установить в восьми силовых шкафах с габаритными размерами 1955×806×405 мм (В×Ш×Г) пусковую аппаратуру для 25 исполнительных механизмов, в том числе 7 ПЧ, 7 УПП, 7 дросселей преобразователей частоты, 33 автоматических выключателя, 57 контакторов и 8 электротепловых реле;
– сэкономить площадь помещения электрощитовой в здании операторной парка и, как следствие, уменьшить затраты на строительство.
- Унифицировано оснащение датчиками и ИМ резервуаров и ёмкостей разных типов и назначения, в том числе:
– для резервуара с понтоном – 3 сигнализатора верхнего уровня, 1 сигнализатор нижнего уровня, аналоговый уровнемер, многозонный датчик температуры, электроприводная запорная арматура на приёмном и раздаточном патрубках;
– для резервуара без понтона – 1 сигнализатор верхнего уровня, 1 сигнализатор нижнего уровня, аналоговый уровнемер, многозонный датчик температуры, датчик избыточного давления паров нефтепродуктов, электроприводная запорная арматура на приёмном и раздаточном патрубках;
– для дренажной ёмкости – 1 сигнализатор нижнего уровня, 1 аналоговый уровнемер, 1 датчик температуры.
Унифицированы также типы датчиков и приводов арматуры, что позволило уменьшить количество ЗИП.
Операторский интерфейс
Резервуары парка разделены на группы по видам нефтепродуктов и сырью.Для каждой группы резервуаров предусмотрена отдельная мнемосхема, на которой отображаются:
- текущие значения аналоговых и дискретных параметров;
- состояния ИМ;
- положения электроприводных регулирующих клапанов;
- частоты вращения двигателей насосов и мешалок, управляемых с ПЧ;
- режимы работы контуров регулирования;
- индикаторы ошибок (с расшифровкой кода и времени возникновения ошибки);
- индикаторы срабатывания блокировок ПАЗ, содержащие причину и время срабатывания блокировки (с возможностью перехода на соответствующую мнемосхему ПАЗ);
- направления изменений уровней нефтепродуктов в резервуарах при наливе/откачке (отображается в виде стрелки соответствующего направления возле изображения резервуара);
- значения заданий и проценты выполнения операций налива нефтепродуктов в автомобильные цистерны, состояния ИМ и датчиков комплектных установок налива;
- выполнение операций слива подтоварной воды.
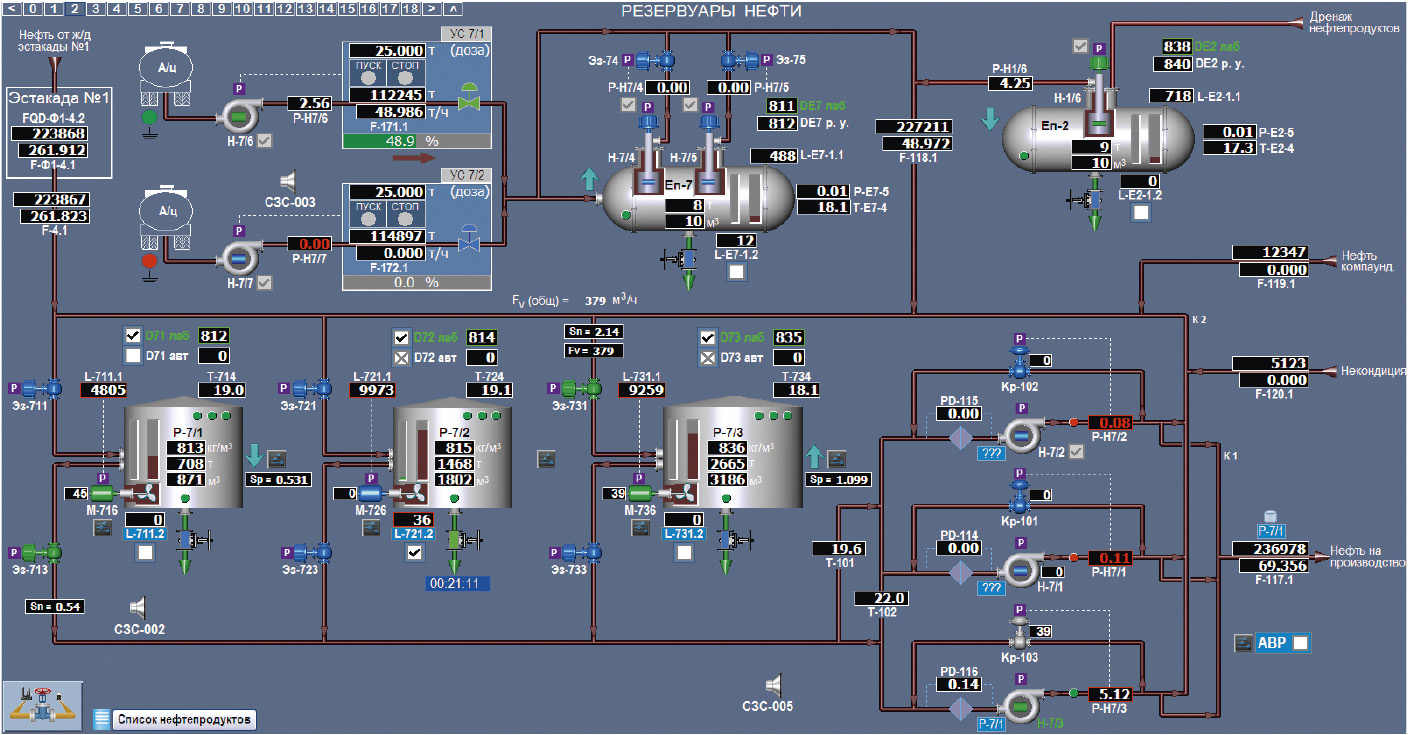
При щелчке указателем мыши на изображении резервуара на основной мнемосхеме открывается всплывающее окно с детальной информацией по данному резервуару, включая:
- уровни нефтепродукта и подтоварной воды в резервуаре;
- массу и объём нефтепродукта;
- объём подтоварной воды;
- температуру нефтепродукта по высоте резервуара в пяти точках;
- избыточное давление паров нефтепродуктов (для резервуаров без понтона);
- значения уровня за предыдущий и текущий час, изменение уровня;
- состояния ИМ резервуара;
- лабораторную плотность нефтепродукта при +20°С и плотность при рабочих условиях;
- тренды параметров;
- гистограммы температур нефтепродукта на разных высотах резервуара.
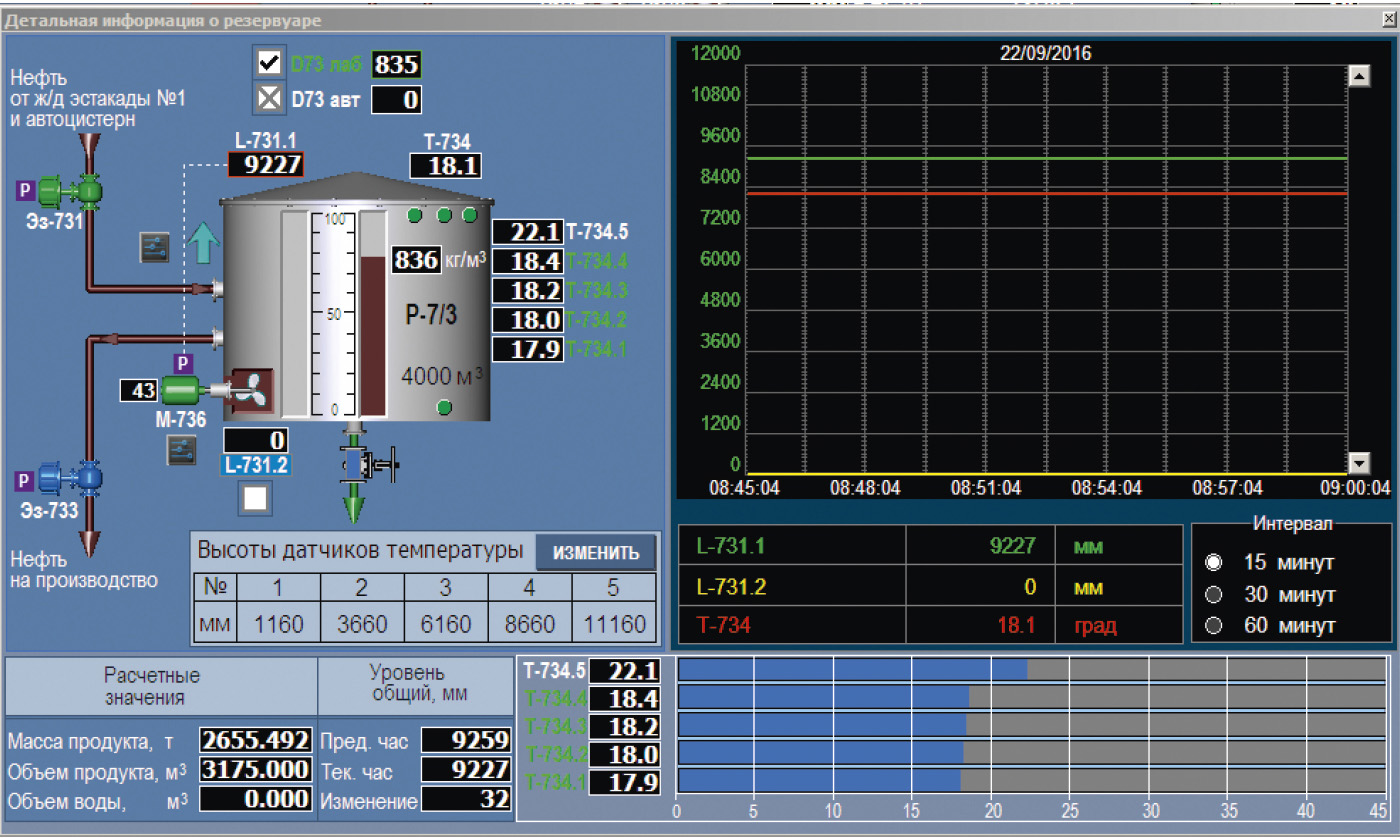
Для защиты технологического процесса от несанкционированного вмешательства предусмотрено парольное разграничение прав доступа пользователей к функциям контроля и управления. Для начала работы с системой необходимо ввести пароль – пройти регистрацию. Все действия зарегистрированных пользователей в системе по управлению процессом и изменению настроек фиксируются в протоколе событий. Для незарегистрированных пользователей допускается только просмотр информации.
Взаимодействие оператора с системой осуществляется посредством экранных панелей управления. При нажатии кнопкой мыши на изображение параметра или ИМ отображается панель управления, содержащая элементы индикации и управления, соответствующие типу вызванного контура.
Используя панели, оператор выполняет все действия по управлению технологическим процессом, в том числе:
- включает и отключает насосы и мешалки;
- открывает и закрывает электроприводную запорную арматуру;
- изменяет:
– режимы управления контуров регулирования (К – каскадный, А – автоматический, Р – дистанционный ручной, М – местный);
– положения штоков регулирующих клапанов;
– частоты вращения электродвигателей насосов и мешалок;
– границы допустимых диапазонов изменения управляющих сигналов – частот вращений электродвигателей, положений клапанов;
- назначает схемы запуска насосов – через УПП или прямой пуск.
Пример панелей управления приведён на рис. 9, 10.
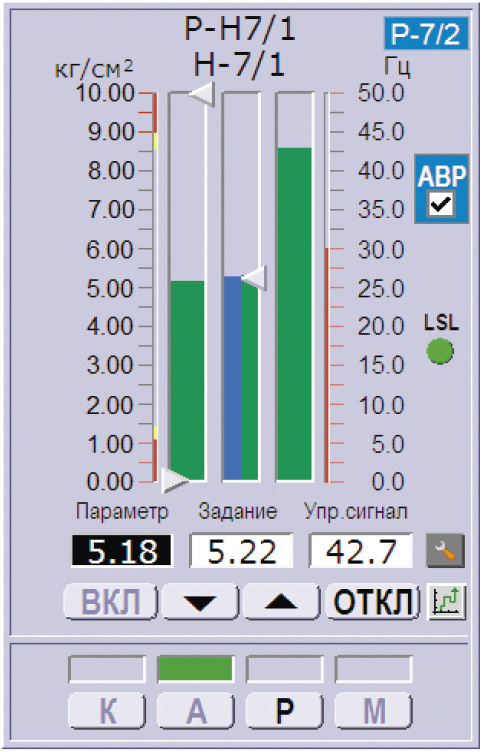
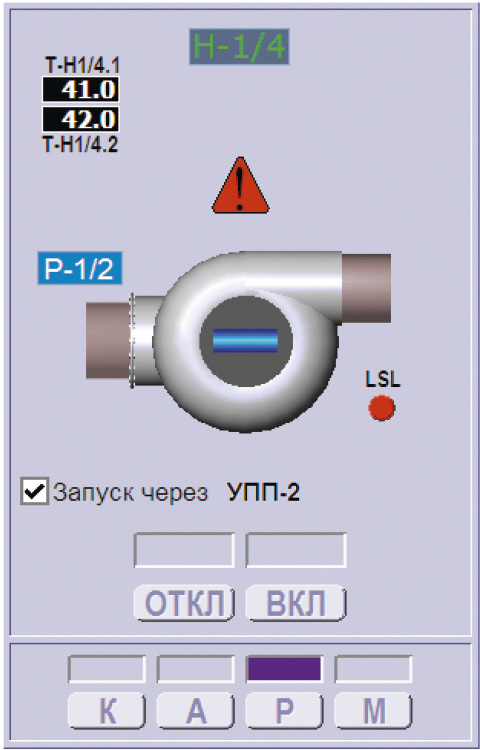
Для удобства работы оператора и обеспечения быстрого доступа к различной информации в системе также предусмотрены следующие вспомогательные мнемосхемы, на которых отображаются:
- обзорный фрагмент, на котором показаны все резервуары парка с визуализацией основных параметров и тенденций изменения уровней нефтепродуктов;
- план размещения сигнализаторов загазованности и устройств светозвуковой сигнализации на территории парка с выводом состояний всех указанных устройств;
- информация по остаткам сырья и нефтепродуктов в резервуарах;
- информация по массовым расходомерам;
- перечень всех ИМ резервуарного парка с индикацией их текущих состояний/положений, неисправностей, наличия активных блокировок системы ПАЗ;
- информация по комплектным установкам слива сырья и налива нефтепродуктов;
- контроль состояний блоков вторичного электропитания шкафов управления;
- таблицы с текущими значениями параметров устройств плавного пуска и преобразователей частоты;
- перечень всех аналоговых и дискретных параметров резервуарного парка с возможностью блокировки выдачи сообщений при нарушениях предупредительных границ.
Структурные схемы ПАЗ показаны на отдельных мнемосхемах. Пример такой мнемосхемы приведён на рис. 11.
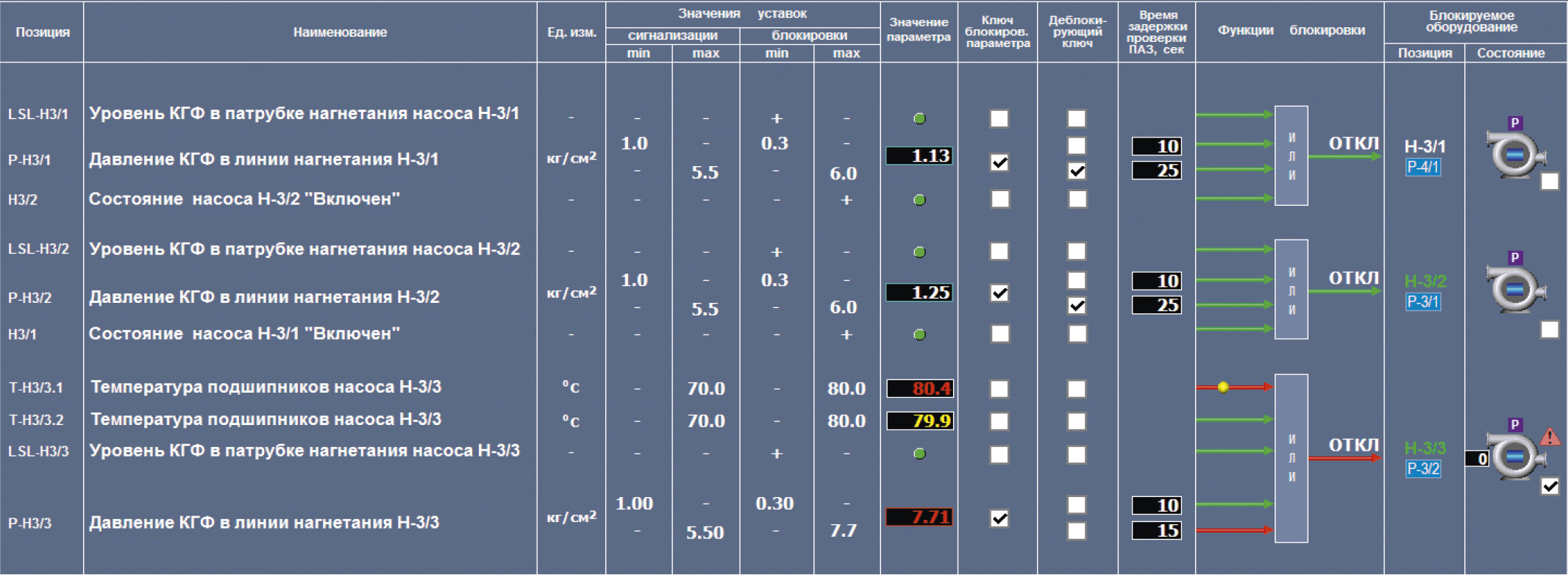
Структурные схемы защиты отображаются в виде таблиц, в которых представлена информация по параметрам системы ПАЗ с указанием их проектных позиций, единиц измерения, значений уставок предупредительной сигнализации и блокировки, текущих значений аналоговых и дискретных параметров. Для установки/снятия блокировочных и деблокировочных ключей, которые предназначены соответственно для отключения опроса измерительных каналов и отключения защит по параметрам (вывода параметров из ПАЗ), предусмотрены специальные элементы управления. В поле «Время задержки проверки ПАЗ» указывается время отсрочки проверки условия срабатывания ПАЗ для параметров, которые блокируют пуск оборудования. Например, используя задержку, оператор может запустить насос, у которого в отключённом состоянии давление нагнетания меньше предаварийной уставки. После включения насоса в работу начинается отсчёт времени, по истечении которого давление нагнетания автоматически включается в список условий срабатывания ПАЗ.
В секции «Функции блокировки» приведены логические условия и структурные связи параметров с ИМ, которые в аварийной ситуации должны переводиться системой ПАЗ в безопасное состояние/положение. Над изображениями линий со стрелками, направленны-ми к ИМ, отображаются надписи с сокращёнными обозначениями команд, подаваемых на ИМ при блокировках: «ОТКЛ», «ВКЛ» для электрооборудования и «ОТКР», «ЗАКР» для арматуры с дистанционным управлением. Зелёный цвет стрелок соответствует работе в штатном режиме. Подача команды на перевод ИМ в безопасное состояние/положение индицируется красным цветом стрелок. При этом специальным индикатором выделяется стрелка напротив условия, явившегося первопричиной срабатывания ПАЗ.
Система ПАЗ резервуарного парка обеспечивает:
- защиту от перелива резервуаров и автоцистерн;
- защиту резервуаров от полного опорожнения;
- закрытие запорной арматуры с электроприводом на приёмно-раздаточных патрубках резервуаров при возникновении разгерметизации, определяемой по срабатыванию сигнализаторов загазованности;
- останов насосов:
– при загазованности, повышении температуры подшипников, отсутствии перекачиваемой жидкости (защита от «сухого» хода), повышении или понижении давления в линиях нагнетания;В работе системы ПАЗ используется информация о схемах коммутации оборудования (резервуар – насос – установка налива), заданных оператором. Таким образом, при срабатывании защиты по резервуару или установке налива останавливается только тот насос, который задействован в схеме коммутации. Пример окна, в котором устанавливается коммутация технологического оборудования склада ГСМ, приведён на рис. 12.
– при поступлении команд на отключение насосов парка из АСУ ТП ж/д эстакад, на которых осуществляется налив нефтепродуктов;
– при нарушениях в работе комплектных установок налива нефтепродуктов в автомобильные цистерны.
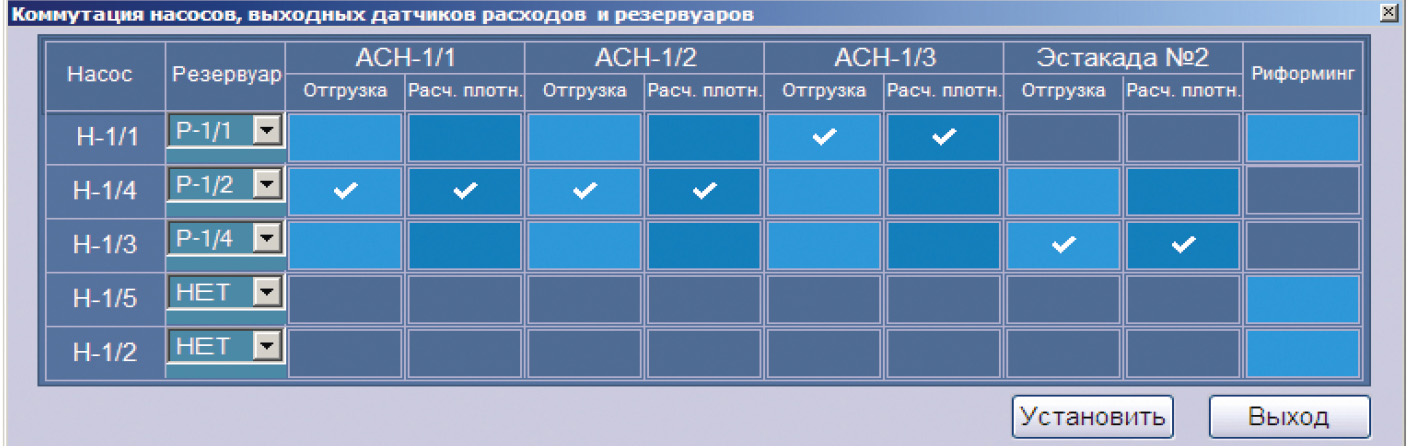
Программное обеспечение
В качестве программного обеспечения АСУ ТП использованы:- операционная система операторских станций Windows 7 Professional SP1;
- SCADA-пакет ViS@ 7.6 для разработки операторского интерфейса;
- операционная система промышленных контроллеров управления Win-dows CE.NET 6.0;
- пакет технологического программирования ТехноСи 2.1 для программирования, отладки и исполнения задач в управляющих контроллерах, с поддержкой резервирования контроллеров и сетевых интерфейсов;
- специально разработанные:
– ActiveX-компоненты для редактирования базы данных SQLITE;Пакеты для программирования контроллеров ТехноСи 2.1 и SCADA ViS@ 7.6 разработаны сотрудниками ООО НТФ «Инкотех» и в течение многих лет успешно используются в работах по созданию АСУ ТП на предприятиях нефтеперерабатывающей, химической и пищевой промышленности, энергетики, строительной индустрии.
– ODBC-драйверы для доступа к базе данных SQLITE из системы формирования отчётов;
– JavaScript-сценарии для динамического формирования отчётов по выбранным видам продуктов и расчёта балансов.
Пользовательское программное обеспечение АСУ ТП разработано в двух конфигурациях:
- Debug отображает в режиме имитации работу ИМ, контуров регулирования, аналоговых и дискретных датчиков (модель резервуарного парка); предназначена для обучения операторов и выполнения локальных задач по отладке ПО;
- Release выполняет задачи защиты, управления и регулирования в режиме реального времени в дублированных контроллерах систем ПАЗ и РСУ.
- Для комплексного решения задач, связанных с производством и отгрузкой нефтепродуктов, при создании АСУ ТП «Склад ГСМ» были реализованы функции, обеспечивающие её взаимодействие с другими системами, а именно:
- чтение из АСУ ТП установки ЭЛОУ-АВТ-600 по протоколу OPC DA интегральных данных массовых расходомеров нефтепродуктов, поступающих в парк из установки, для расчёта и формирования баланса по резервуарному парку;
- обмен данными по протоколу TCP/IP с АСУ ТП ж/д эстакад № 1, 2 слива/налива сырья и нефтепродуктов:
– для автоматического пуска/останова насосов по командам, поступающим от местных постов управления комплектных установок налива на эстакадах,
расположенных на расстоянии 500 м от насосной резервуарного парка;
– для останова насосов после отгрузки заданных доз нефтепродуктов;
– для автоматического снижения частоты электродвигателей насосов при переходе на клапан малого расхода в момент завершения загрузки нефтепродуктов в ж/д цистерны;
– для автоматического открытия регулирующих клапанов на байпасах насосов при завершении загрузки нефтепродуктов в ж/д цистерны для исключения гидроударов.
Результаты внедрения
Внедрение АСУ ТП «Склад ГСМ» позволило:- реализовать современную и надёжную систему противоаварийной защиты, которая соответствует требованиям федеральных законов, норм и правил РФ в области промышленной безопасности;
- обеспечить требуемую точность учёта материальных потоков, оперативно выполнять расчёты материального баланса и формировать отчётную документацию о движении материальных потоков;
- уменьшить время операций слива/налива сырья и нефтепродуктов в автоцистерны за счёт автоматического регулирования этих процессов;
- снизить затраты на ремонт оборудования за счёт соблюдения регламентных режимов работы и диагностирования неисправностей. •
E-mail: incotech@pochta.ru
Если вам понравился материал, кликните значок - вы поможете нам узнать, каким статьям и новостям следует отдавать предпочтение. Если вы хотите обсудить материал - не стесняйтесь оставлять свои комментарии : возможно, они будут полезны другим нашим читателям!