История создания системы
ООО «ВИЗ-Сталь» – ведущий производитель холоднокатаной электротехнической стали и крупнейший производитель трансформаторной стали в России. Доля «ВИЗ-Стали» в мировом производстве трансформаторной стали составляет около 11%. Более 80% продукции отгружается на экспорт.
В настоящее время «ВИЗ-Сталь» занимается внедрением системы управления производством цеха холодной прокатки – системы MES компании PSI Metals. В связи с этим перед специалистами ООО «НПП «АИС» была поставлена задача создания системы распределённого сбора и обработки данных (РСОД) агрегата выпрямляющего отжига АВО-7. Система РСОД создавалась с целью оснащения технологического процесса обработки металла на агрегате АВО-7 автоматизированной системой. Она предназначена для сбора и обработки информации о значениях технологических параметров и о возникающих производственных событиях, а также для передачи систематизированных данных в систему MES. Помимо этого на систему РСОД возложены функции отображения информации, привязки значений технологических параметров к длине полосы металла определённого рулона и двустороннего обмена данными с системой MES (система РСОД не только передаёт информацию в систему MES, но и получает от неё технологические задания с исходными данными, запросы на определённые операции, извещения о приёме некоторых сообщений).
В дальнейшем подобными системами планируется оснастить все агрегаты цеха холодной прокатки (ЦХП). Решение о первоочередном внедрении системы РСОД именно на агрегате АВО-7 было принято в силу того, что на этом агрегате к тому времени уже функционировал ряд разрозненных устройств КИПиА и программно-технических комплексов (ПТК), контролирующих различные технологические параметры. Эти устройства КИПиА и ПТК были разработаны и внедрены разными организациями в разное время и имеют различную программно-аппаратную архитектуру.
Структура системы проектировалась таким образом, чтобы максимально задействовать ресурсы технических и программных средств имеющихся устройств КИПиА и ПТК. В силу этого решение задачи сбора и обработки данных потребовало разработки и реализации различных программно-аппаратных интерфейсов, с помощью которых возможно было бы собрать все необходимые данные с существующих устройств КИПиА и ПТК.
Таким образом, в описываемом проекте в качестве объекта автоматизации рассматривался агрегат АВО-7 с функционирующими на нём устройствами КИПиА и ПТК (далее – подсистемы АВО-7). Подсистемы АВО-7 были представлены в составе:
- устройства контроля температурных и газовых режимов;
- цифровые весы;
- автоматизированная система учёта магнитных свойств электротехнической стали (АСУ МСЭС) в части локального устройства агрегата АВО-7;
- измеритель плоскостности ИП-4;
- магнитно-измерительный комплекс (МИК), состоящий из
– измерителя толщины покрытия,
– измерителя тока Франклина,
– измерителя индукции и потерь намагничивания.
Концепция сбора данных
Агрегат АВО-7 предназначен для выполнения технологических операций по выпрямлению полосы металла после высокотемпературного отжига и нанесению на её поверхность электроизоляционного покрытия (ЭИП). На рис. 1 показана выходная часть агрегата АВО-7.
Для обеспечения непрерывного технологического процесса обработки металла отдельные рулоны (полосы металла) соединяются с помощью транспортного шва, который выполняется на листо-сшивной машине. Все измеренные технологические параметры необходимо привязывать к длине полосы относительно транспортного шва.
Таким образом, помимо сбора и обработки данных о значениях технологических параметров возникает задача отслеживания точного времени прохождения транспортного шва в местах расположения измерительных преобразователей – формирование диаграммы значений технологических параметров по длине полосы металла. При этом необходимо учитывать, что агрегат состоит из входной, технологической и выходной частей, которые разделяются петлевыми устройствами – накопителями, обеспечивающими постоянную скорость движения металла в технологической части агрегата при останове во входной или выходной частях, то есть фактически скорости движения металла в разных частях агрегата различны.
Отслеживание точного времени прохождения транспортного шва в контрольных точках выполняется методом обработки сигналов с листосшивной машины, датчиков контроля отверстий и инкрементных энкодеров. По сигналу с листосшивной машины определяется положение транспортного шва во входной части агрегата. Положение транспортного шва в технологической и выходной частях агрегата определяется с помощью датчиков контроля отверстий ДКО-2 (рис. 2).
Эти датчики срабатывают по наличию отверстия, выполненного персоналом ЦХП на листосшивной машине на полосе металла вблизи транспортного шва. Скорость движения полосы металла измеряется по сигналам с инкрементных энкодеров ЛИР-158, установленных на приводах разматывателей, тянущих роликов, петлевых устройств, а также по сигналам с тахогенераторов, установленных на моталках.
Длина полосы металла также является изменяемой величиной. Во входной части агрегата перед соединением концов полос непрокатанные участки от наружных витков рулонов вырезают.
В выходной части агрегата выполняют отбор проб для испытания магнитных, электроизоляционных и механических свойств, производят отмотку металла с низким уровнем электромагнитных свойств ЭИП, а также вырезают транспортный шов. Поэтому помимо сбора и обработки данных система обеспечивает учёт следующих производственных событий:
- установка рулона металла на разматыватель – принятие рулона в обработку;
- частичное или полное снятие рулона с разматывателя;
- вырезка непрокатанных участков от наружных витков рулонов;
- отбор проб;
- снятие рулона с моталки – завершение обработки рулона;
- взвешивание рулона.
События установки рулонов на разматыватели, а также частичного или полного снятия рулонов с разматывателей регистрируются с помощью ультразвуковых датчиков расстояния SICK.
Архитектура системы
Система реализована в виде трёхуровневого комплекса технических средств.
Нижний уровень включает в себя первичные и вторичные преобразователи сигналов, характеризующих технологические параметры, а также датчики контроля положения и состояния оборудования агрегата. Этот уровень выполняет функции формирования сигналов технологического контроля.
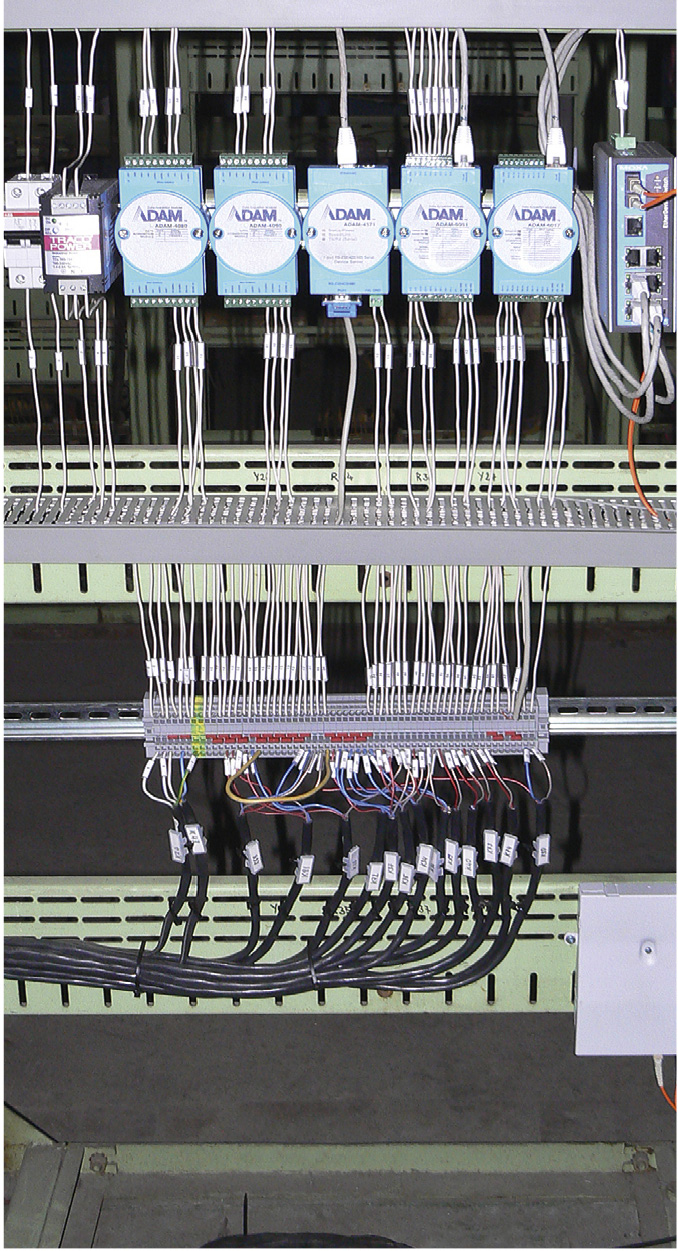
Средний уровень использует модули удалённого ввода аналоговых и дискретных сигналов, а также модули удалённого ввода частотно-импульсных сигналов семейства ADAM компании Advantech (рис. 3). Здесь реализуются следующие функции:
- сбор и преобразование в цифровую форму сигналов от датчиков, преобразователей, оборудования агрегата;
- передача данных верхнему уровню.
Верхний уровень состоит из объединённого автоматизированного рабочего места (АРМ) оператора, представленного компьютером промышленного исполнения фирмы Advantech, и пульта контролёра ОТК для ввода данных о дефектах полосы обрабатываемого металла, представленного панелью оператора фирмы Weintek. Функции верхнего уровня:
- обмен данными с системой MES;
- сбор данных с подсистем АВО-7;
- приём данных от среднего уровня;
- приём данных, вводимых оператором и контролёром ОТК;
- обработка, анализ и хранение (архивирование) полученных данных;
- отображение информации о состоянии контролируемого оборудования и ходе технологического процесса;
- регистрация значений технологических параметров с привязкой к длине полосы металла относительно транспортного шва;
- регистрация штатных и аварийных событий;
- предупредительная и аварийная сигнализация;
- автоматическая диагностика;
- формирование и выдача отчётной документации.
Схема функциональной структуры системы приведена на рис. 4.
Описание управляющей программы АРМ оператора
Управляющая программа АРМ оператора разработана с помощью Microsoft Visual C# и имеет модульную архитектуру. Архитектура управляющей программы АРМ оператора представлена на рис. 5.
Управляющая программа АРМ оператора системы РСОД предоставляет для работы многооконный графический интерфейс (рис. 6).
Он разработан с учётом удобства использования оператором. Работа оператора с управляющей программой АРМ выполняется в диалоговом режиме. При возникновении определённых событий управляющая программа выводит диалоговые окна для подтверждения действий персонала цеха либо для ввода дополнительной информации о ходе технологического процесса.
При установке рулона полосы металла на разматыватель управляющая программа запрашивает у системы MES входные данные рулона и принимает его в обработку. Во время обработки полосы металла на агрегате управляющая программа собирает и обрабатывает информацию с модулей удалённого ввода сигналов, подсистем агрегата, пульта контролёра ОТК и в систематизированном виде отправляет данные о ходе технологического процесса, измеренных значениях технологических параметров, дефектах металла в систему MES. По окончании обработки управляющая программа отправляет в систему MES информацию о характеристиках обработанного металла.
Обмен данными между системой распределённого сбора данных агрегата АВО-7 и системой MES реализован с помощью PSIiface – инструмента PSI. PSIiface использует обмен данными посредством телеграмм с заранее определённой структурой. В качестве транспортного уровня обмена используются таблицы баз данных (БД). Для работы с локальной и транспортной БД используется система управления БД Microsoft SQL Server. Локальная база данных предназначена для хранения архива событий и параметров, транспортная – для обмена телеграммами с системой MES.
Описание пульта контролёра ОТК
Для ввода данных о дефектах система РСОД оборудована промышленной сенсорной панелью оператора – пультом контролёра ОТК (рис. 7), расположенным вблизи моталок. Ввод данных о дефектах производится в диалоговом режиме.
Все дефекты сгруппированы по вкладкам в соответствии с местом их возникновения. При обнаружении начала дефектного участка контролёр ОТК нажимает кнопку кода дефекта на сенсорной панели пульта и вводит дополнительные параметры, характеризующие дефект:
- категория;
- сторона (верх/низ);
- ширина;
- сторона задания глубины (лево/право);
- глубина.
По окончании дефектного участка контролёр должен нажать кнопку «Отправить» для передачи информации в систему. Система выполняет подсчёт длины и определяет положение дефектного участка. Систематизированная информация о дефектах отправляется в систему MES при снятии рулона с моталки.
С помощью этого пульта контролёры ОТК могут вводить информацию о дефектах непосредственно на месте их визуального определения, что повышает эффективность работы контролёров.
Уникальные особенности проекта
Структура технических средств и структура программного обеспечения представленной системы имеют модульную архитектуру, подразумевающую лёгкость наращивания функциональных и технических возможностей при возникновении необходимости модернизации системы или добавления функций автоматического управления механизмами агрегата.
Разработанное решение благодаря своей модульности также может быть перенесено на другие агрегаты цеха с минимальными затратами на разработку и внедрение. ●
E-mail: shustova-ms@mail.ru
Если вам понравился материал, кликните значок - вы поможете нам узнать, каким статьям и новостям следует отдавать предпочтение. Если вы хотите обсудить материал - не стесняйтесь оставлять свои комментарии : возможно, они будут полезны другим нашим читателям!