Введение
ГП «УкрНТЦ «Энергосталь» является ведущей инжиниринговой фирмой в СНГ, проектирующей, изготавливающей и вводящей в эксплуатацию газоотводящие тракты (ГОТ) конвертеров (К) с «мокрой» газоочисткой, электросталеплавильных печей с «сухой» газоочисткой для металлургических заводов России, Украины, Казахстана, не уступающие по своим характеристикам ГОТ передовых западных фирм. В состав ГОТ К входит современная АСУ ТП собственной разработки, как правило, на платформе SIEMENS. Для отработки программно-математического обеспечения программно-технических комплексов (ПТК) АСУ ТП ГОТ К в ГП «УкрНТЦ «Энергосталь» разработана математическая модель процессов в газоотводящем тракте конвертера кислородно-конвертерного цеха [1]. Прикладное программное обеспечение ПТК взаимодействует с математической моделью или с реальным технологическим объектом управления. Особую ценность модель имеет для анализа нештатных и аварийных ситуаций, которые на реальном объекте проверить и отработать невозможно или очень сложно.Одной из функций контроля и управления технологическим процессом ГОТ К является предотвращение аварийных ситуаций в работе котла-охладителя. Наиболее опасной ситуацией является «упуск» воды котла-охладителя конвертерных газов ГОТ.
«Упуск» воды из котла-охладителя может привести к аварии прежде всего циркуляционных насосов (ЦН). На вход ЦН будет поступать неоднородная среда, то есть пароводяная смесь, что является причиной появления гидравлических ударов, которые приводят к повреждению включённых ЦН.
Такие явления наблюдались во время имитации отказа управляющего контроллера при моделировании процессов в ГОТ конвертера.
При отказе управляющего контроллера необходимо не только прекратить продувку конвертера кислородом, но и обеспечить поддержание безопасного для включённых ЦН уровня воды в барабане-сепараторе (БС) котла-охладителя, так как после выключения кислородной продувки за счёт эффекта обратного «набухания», то есть резкого уменьшения парообразования в нагревательных поверхностях котла-охладителя и снижения уровня воды в БС, может произойти «упуск» уровня воды.
Аварийная ситуация возникает внезапно, при этом ритм работы и порядок выполнения операций резко изменяются. Решения необходимо принимать быстро и правильно, так как под угрозой находятся не только огромные материальные ценности, но и жизнь персонала.
В связи с тем, что аварийные ситуации очень редки, а готовность к ним должна быть постоянной, противоаварийная защита должна работать в автоматическом режиме.
ГП «УкрНТЦ «Энергосталь» (далее – Центр) в 2016 г. введена в эксплуатацию автоматизированная система управления технологическим процессом (АСУ ТП) газоотводящего тракта (ГОТ) конвертера № 2 (К2) кислородно-конвертерного цеха (ККЦ) ЧАО «Мариупольский металлургический комбинат им. Ильича» (ЧАО «ММК им. Ильича»). При работе над данным проектом использовался успешный опыт разработки и внедрения АСУ ГОТ конвертеров в ОАО «Нижнетагильский металлургический комбинат им. В.И. Ленина», ПАО «Челябинский металлургический комбинат», ПАО «Енакиевский металлургический завод» и на ряде других предприятий [2].
Объект автоматизации
Объектом автоматизации является модернизируемый ГОТ конвертера № 2. Этот тракт обеспечивает утилизацию тепла, охлаждение и очистку конвертерного газа, а также его отвод в атмосферу.Газоотводящий тракт конвертера – технологический комплекс, включающий котёл-утилизатор, газоочистку и дымосос. Обезуглероживание чугуна в конвертере с последующим полным или частичным дожиганием оксида углерода в газоходе котла, утилизация тепла в котле-охладителе путём нагрева воды и парообразования в охлаждающих экранах и ширмах, очистка
дымовых газов перед выбросом их дымососом в атмосферу являются сложными технологическими процессами (аэродинамическими и тепломассообменными). На динамику работы ГОТ влияют расход кислорода на продувку конвертера, фаза плавки стали в конвертере, теплообменные процессы в котле и газоочистке и т.п. Кроме того, в ГОТ имеется несколько десятков аварийных параметров, значения которых следует непрерывно контролировать. При достижении этими параметрами критических значений, а также при отказах определённых исполнительных механизмов, датчиков, оборудования АСУ ТП необходимо:
- включать защиты, блокировки, резерв, сигнализацию и безаварийно перевести оборудование ГОТ в безопасное состояние;
- запретить проведение текущей или следующей продувки;
- поддерживать безопасный для работы семи (в основном) включённых циркуляционных насосов уровень воды в барабане-сепараторе (БС) котла.
В подъёмном газоходе котла-охладителя происходит полное его дожигание. Продукты горения за счёт разрежения, создаваемого дымососом, направляются по системе газоходов котла-охладителя конвертерных газов (ОКГ), аппаратов и газоходов газоочистки в дымовую трубу.
Перед подачей в систему газоочистки газы необходимо охладить в котле-охладителе.
Котёл-охладитель конвертерных газов, кроме тепловоспринимающих поверхностей газоходов, включает барабан-сепаратор, узел подачи питательной воды, циркуляционные насосы и работает в условиях, связанных с цикличностью выхода конвертерных газов, их высокой температурой и большой запылённостью.
Цикличный характер выхода конвертерных газов обуславливает и цикличный характер выработки пара, происходящей только во время кислородной продувки, составляющей примерно 30–40% всего периода плавки. Образующаяся в поверхностях нагрева пароводяная смесь направляется в барабан-сепаратор котла.
Охлаждение газа происходит в процессе его движения через кессон, подъёмный и опускной газоходы ОКГ за счёт подачи воды в охлаждающие поверхности котла: экраны, ширмы и системы трубопроводов, расположенных по трассе движения газа. Охлаждённый до +450…+650°С газ поступает в «мокрую» газоочистку. Подача охлаждающей воды в ОКГ осуществляется из циркуляционной насосной, в состав которой входят циркуляционные насосы (9 шт., из них 7 включены в работу) и электроуправляемые исполнительные механизмы (ИМ). Барабан-сепаратор обеспечивает отделение пара от воды.
В системе защиты котла, транспортировки пара и регулирования подачи питательной воды через узел питания используются электроуправляемые ИМ и регулирующие клапаны.
«Мокрая» газоочистка ГОТ конвертера: в установке предварительного охлаждения (УПО) и скруббере – первой ступени газоочистки – осуществляется процесс дальнейшего понижения температуры конвертерного газа и его грубая очистка.
Труба Вентури служит для тонкой очистки конвертерного газа от пыли и окончательного охлаждения его до +55…+60°С.
В каплеуловителе происходит осушение конвертерного газа путём выделения капель воды из газового потока.
Дымосос обеспечивает разрежение по всей трассе движения конвертерного газа и отвод газов конвертера в атмосферу через дымовую трубу. В состав оборудования дымососа входят две маслостанции (для электродвигателя и нагнетателя).
Функции АСУ ТП ГОТ К2
АСУ ТП ГОТ К2 выполняет следующие функции:- контроль аварийных параметров ГОТ К и формирование сигнала «Разре-шение продувки» конвертера кислородом;
- регулирование уровня воды в БС во все периоды плавки с расходом кислорода на продувку конвертера от 350 до 450 нм3/мин и в межплавочный период;
- контроль параметров и управление исполнительными механизмами барабана-сепаратора, ширм и экранов ОКГ, газоочистки;
- контроль параметров дымососа;
- контроль работы двух маслостанций дымососа через их АСУ;
- контроль работы циркуляционных насосов;
- визуализация и архивирование технологических параметров;
- формирование сигнализации и сообщений по значениям технологических параметров и т.д.
Структура ПТК
Основой АСУ ТП ГОТ К2 является ПТК, состоящий из технических средств (АРМ, контроллерного и сетевого оборудования) и программно-математического обеспечения. Следует отметить, что существовавшая до реконструкции АСУ ТП ГОТ К2 базировалась на одном мощном программируемом логическом контроллере (ПЛК) с применением многофункциональных модульных станций распределённого ввода-вывода (SIMATIC ET-200M) на основе сетей PROFIBUS DP. Требовалось доработать или частично заменить оборудование АСУ ТП ГОТ К2, установить новые аппаратные средства, а также обновить программное обеспечение (ПО) без замены существующего модуля центрального процессора. Кроме того, было принято совместное с заказчиком решение о дополнительных мерах защиты котла при самой сложной аварийной ситуации – отказе центрального процессора. В такой ситуации (без специальных мер защиты) не только прекращается регулирование уровня воды в барабане котла, но и полностью перестают визуализироваться все параметры котла и ГО, что ставит оператора в чрезвычайно сложное положение.При реконструкции АСУ ТП ГОТ К2 было выполнено специальное требование заказчика проекта – максимально сохранить места расположения шкафов и кабельные трассы, а также программное обеспечение (ПО) не модернизируемых систем управления (АСУ конвертера и АСУ дозирования) с соблюдением концепции единого верхнего уровня. АСУ ТП ГОТ К2 спроектирована как автоматизированная двухуровневая управляющая система, обеспечивающая автоматическое управление режимами и контурами регулирования в реальном времени с распределённой организацией измерений, сбора и обработки информации, выдачи управляющих воздействий.
Структурная схема оборудования ПТК АСУ ТП ГОТ К2 представлена на рис. 1.
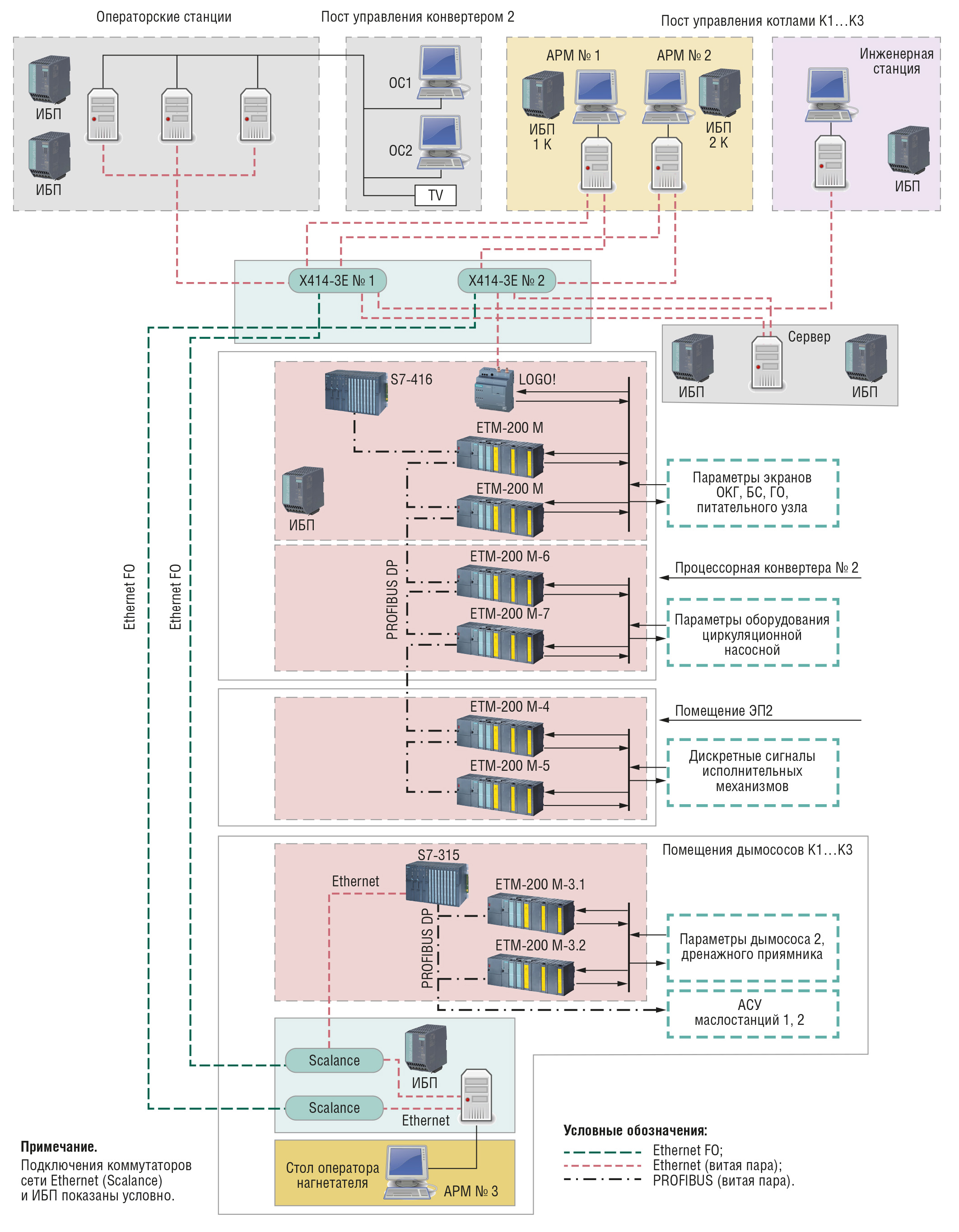
Нижний уровень (НУ) управления выполнен на базе контроллеров SIEMENS (с применением распределённых устройств ввода-вывода), осуществляющих приём, обработку сигналов и выдачу управляющих воздействий на исполнительные механизмы ГОТ К2.
В состав НУ включены:
- основной контроллер S7-416 и многофункциональные модульные станции распределённого ввода-вывода (SIMATIC ET-200M);
- контроллер дымососа S7-315 и многофункциональные модульные станции распределённого ввода-вывода (SIMATIC ET-200M);
- контроллер защиты LOGO! и размножители входных аналоговых токовых сигналов от датчиков уровня воды в БС;
- АРМ операторов котла и ГО (два);
- АРМ оператора дымососа;
- шкаф связи в дымососном отделении.
Контроллер дымососа S7-315 выполняет контроль параметров газохода (до и после дымососа), помещения дымососной, дымососа (температуры и вибрации подшипников), двух маслостанций дымососа, формирует сигнал «Аварийно выключить дымосос» при превышении аварийного значения хотя бы одним аварийным параметром (температура и вибрация подшипников) и передаёт измеренные параметры на верхний уровень.
Контроллер защиты LOGO! предназначен для поддержания безопасного для работы включённых ЦН уровня воды в БС при отказе основного контроллера. Контроллер LOGO! получает из ОК сигнал «ОК работает» и имеет связь с ОК по сети Ethernet, принимает сигналы с датчиков уровня воды в БС, дискретные сигналы положения регулирующих клапанов (РК) «Закрыт», обеспечивает индикацию уровня воды в БС на специальной панели видеокадра «Барабан-сепаратор». Панель может вызвать оператор нажатием кнопки на видеокадре, или она появится автоматически при отказе ОК. Измеренные параметры LOGO! передаёт на верхний уровень ПТК для архивирования и визуализации.
При работе ОК контроллер защиты LOGO! получает из ОК сигнал «ОК работает» и (или) имеет связь с ОК по сети Ethernet, управляющие сигналы на ИМ не формирует (ОК обеспечивает регулирование уровня воды в БС).
При отказе ОК контроллер защиты LOGO! не получает из ОК сигнал «ОК работает» и не имеет связи с ОК по сети Ethernet, принимает управление на себя – формирует и выдаёт управляющие команды на РК:
- команда «Больше» заранее определённой длительностью (определяется ОК до отказа и передаётся в контроллер защиты) выдаётся только при уровне воды в БС ниже уровня открытия РК;
- команда «Меньше» выдаётся до получения сигнала РК «Закрыт» только при уровне воды в БС выше уровня закрытия РК.
Эффективность поддержания безопасного для включённых циркуляционных насосов уровня воды в барабане-сепараторе в такой аварийной ситуации подтверждена результатами моделирования.
Верхний уровень (ВУ) представлен автоматизированными рабочими местами (АРМ-серверами оператора котла и оператора дымососа), оборудованными средствами, позволяющими выполнять функции человеко-машинного интерфейса (ЧМИ) и архивирования информации.
На рис. 2 в качестве примера представлен видеокадр мнемосхемы «Барабан-сепаратор», который включает собственно барабан-сепаратор, узел питательной воды, аварийный слив, паропроводы, частично трубопроводы циркуляционных контуров и др.
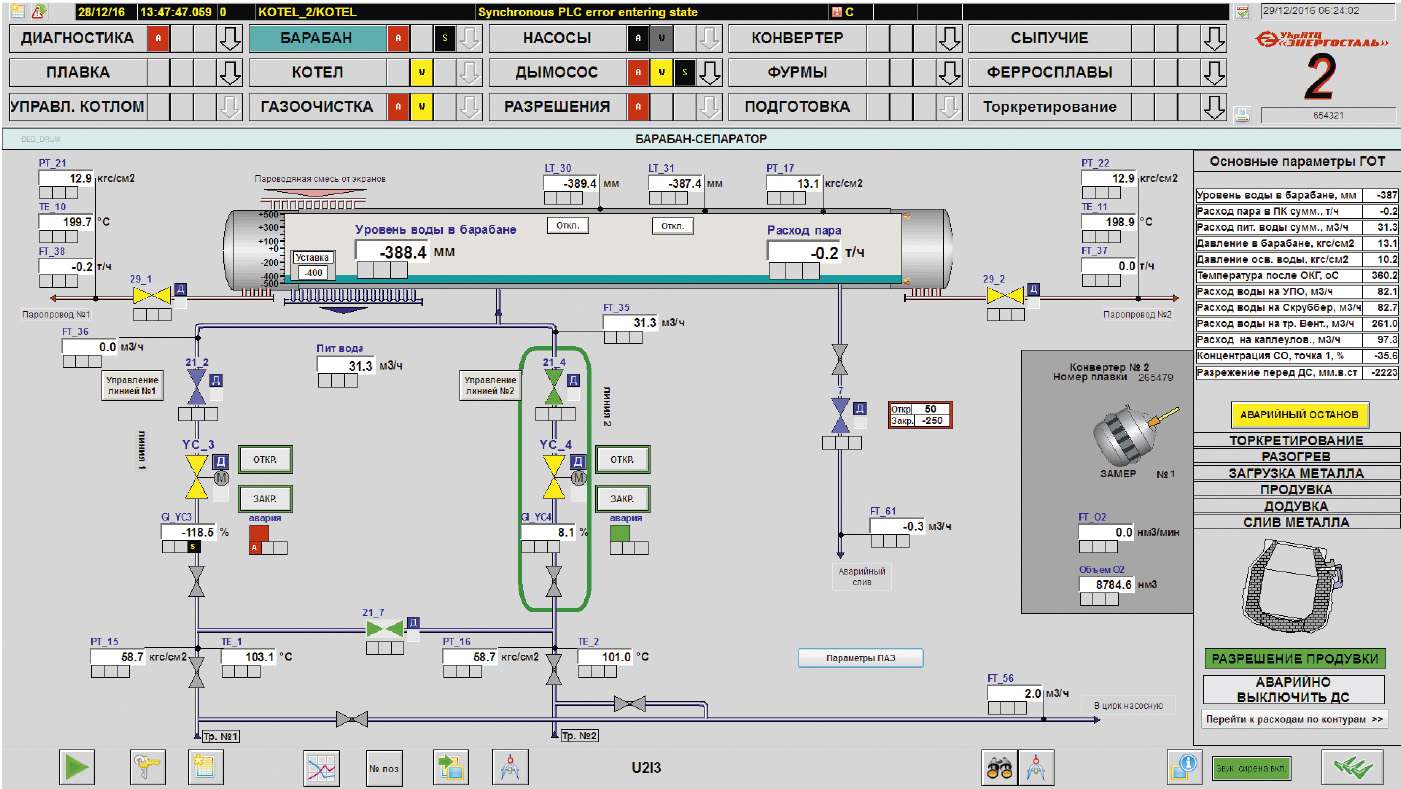
На рис. 3 показана всплывающая на видеокадре мнемосхемы «Барабан-сепаратор» панель контроллера защиты (контроль уровня воды в БС, управления регулирующими клапанами).
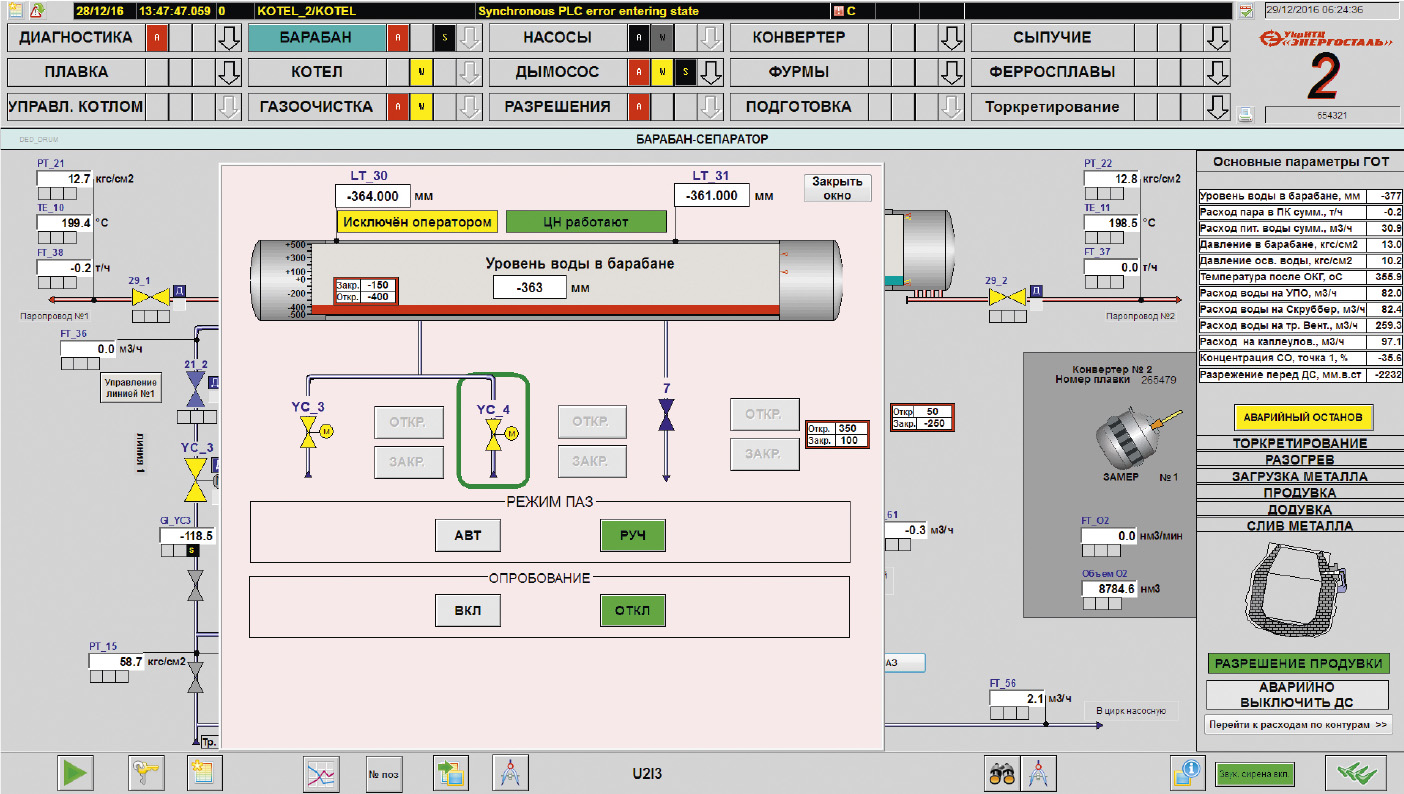
На рис. 4 приведена фотография контроллерного шкафа с основным контроллером и контроллером защиты.
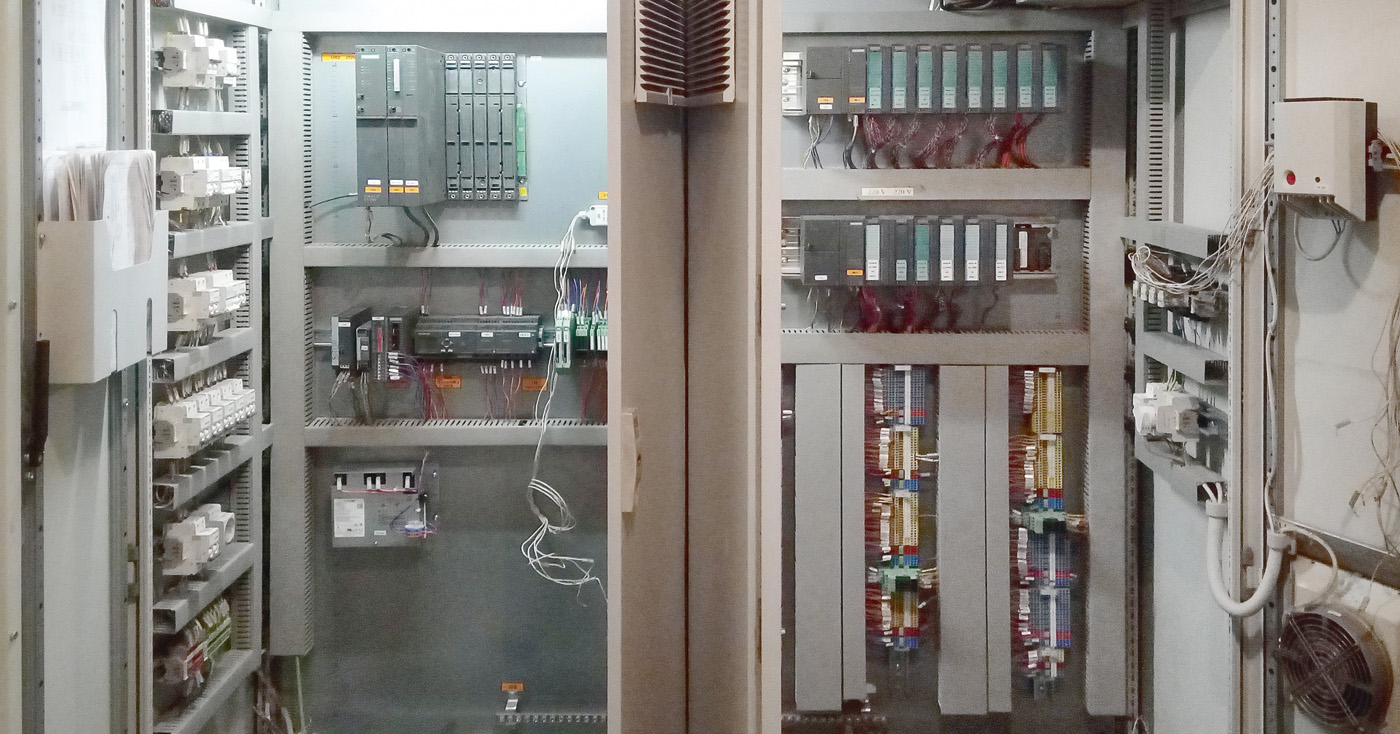
Программное обеспечение
Программный проект нижнего уровня сконфигурирован в среде разработки Step7 и интегрирован в мультипроект, содержащий как программу управления конвертером и газоотводящим трактом (нижний уровень), так и сконфигурированные станции АРМ-серверов и сервера (верхний уровень).Программный проект верхнего уровня АРМ-сервера включает информацию обо всех подсистемах: АСУ конвертера, АСУ дозирования, АСУ газоотводящего тракта. Это даёт возможность визуализировать любые подсистемы и управлять ими с любого АРМ-сервера.
Программный проект сервера представляет собой копию программного проекта АРМ-сервера с добавлением ряда скриптов и архивов.
Изменение программных проектов верхнего уровня АРМ-сервера произведено путём точечной интеграции видеокадров, разработанных ГП «УкрНТЦ «Энергосталь», в общее дерево вызовов видеокадров. Добавлены скрипты типовых программных модулей, созданных Центром и отработанных на стенде и в процессе эксплуатации. Благодаря этому можно открывать всплывающие окна лицевых панелей одним нажатием на значки отображения элементов и передавать информацию о типе программного модуля, что позволяет добиться универсальности лицевых панелей. Применение данных модулей существенно снизило вероятность внесения ошибки в программное обеспечение.
Выводы
- ГП «УкрНТЦ «Энергосталь» модернизирована и введена в эксплуатацию новая АСУ ТП газоотводящего тракта конвертера № 2 кислородно-конвертерного цеха ЧАО «ММК им. Ильича».
- Особенностью нового ПТК АСУ ТП является поддержание безопасного для включённых циркуляционных насосов уровня воды в барабане-сепараторе как в автоматическом, так и в ручном режиме управления, даже при отказе основного контроллера с обеспечением оператора котла информацией по уровню воды в барабане-сепараторе. Для этого в состав ПТК АСУ ТП введён специальный компактный (модуль LOGO!) контроллер защиты с соответствующим программным обеспечением. Эффективность поддержания безопасного для включённых циркуляционных насосов уровня воды в барабане-сепараторе в такой аварийной ситуации подтверждена результатами моделирования.
- Работа АСУ ТП ГОТ К2 при плавках стали в конвертере (проведено более 1000 плавок) уже показала, что заложенные при проектировании технические решения обеспечивают устойчивую работу технологического оборудования. •
Литература
- Криволапов А., Кривоносов А., Пирогов А., Базюченко С. и др. Особенности проектирования и отработки АСУ ТП газоотводящего тракта конвертера // Современные технологии автоматизации. – 2009. – № 4.
- Кривоносов А., Криволапов А., Каплунов Ю., Пироженко А. и др. АСУ ТП газоотводящего тракта конвертера // Современные технологии автоматизации. – 2013. – № 1.
Если вам понравился материал, кликните значок - вы поможете нам узнать, каким статьям и новостям следует отдавать предпочтение. Если вы хотите обсудить материал - не стесняйтесь оставлять свои комментарии : возможно, они будут полезны другим нашим читателям!