Немного истории
Главный офис немецкой компании WAGO Kontakttechnik GmbH & Co. KG находится в городе Минден на северо-востоке земли Северный Рейн-Вестфалия. Ключевыми направлениями деятельности компании являются разработка и производство клемм для монтажа на DIN-рейку, миниатюрных клемм, клемм для печатных плат, мультиштекерных систем, а также программируемых логических контроллеров и контроллеров узла сети.Более полувека WAGO совершенствует уникальную технологию пружинного зажима. Запатентованное компанией в 1977 году пружинное соединение CAGE CLAMP стало революционным событием в электротехнической отрасли (рис. 1).
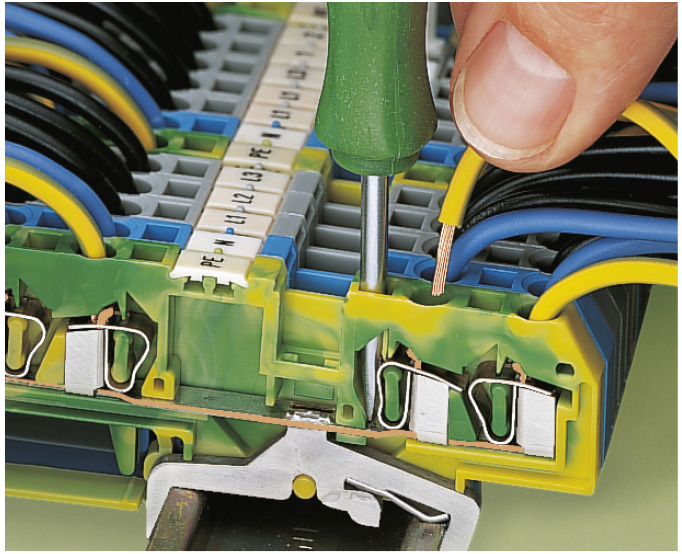
Эта технология решала две ключевые проблемы, характерные для применявшегося ранее винтового соединения: значительно сокращала время подключения одножильного или многожильного проводника и обеспечивала гарантированную надёжность соединения при вибрационных нагрузках. Патент на клеммы, изготовленные по технологии CAGE CLAMP, действовал 25 лет и гарантировал подключение проводников с сечением от 0,08 до 35 мм2. В 1998 году компания WAGO представила на рынке промышленной автоматизации новую технологию POWER CAGE CLAMP – систему пружинных соединений для проводников сечением до 95 мм2. Дальнейшим развитием пружинного зажима стало создание в 2003 году технологии CAGE CLAMP S, позволившей пользователю монтировать одножильные проводники и проводники с наконечником без применения специального инструмента.
В 1995 году компания WAGO вышла на рынок интеллектуальных систем сбора данных и управления с уникальным решением, позволившим ей занять свою собственную нишу. Система получила название WAGO I/O (I – англ. input, вход; O – англ. output, выход). Основная идея состоит в предоставлении разработчику широких возможностей по конфигурированию, наращиванию и обслуживанию системы. Можно изменить перечень модулей ввода-вывода, нарастить или уменьшить количество каналов и подключиться к любой промышленной шине, просто выбрав нужный головной модуль.
Головные модули разделяются на два вида – это программируемые логические контроллеры (ПЛК) и контроллеры узла сети (Fieldbus coupler). ПЛК способны автономно выполнять управляющий алгоритм без участия компьютера верхнего уровня, что делает построенную на их основе систему надёжной и не зависящей от аварий в сетях передачи данных. Программирование ПЛК осуществляется с помощью адаптированной среды CoDeSys, которая поддерживает 5 языков программирования по стандарту IEC 61131. Для хранения и обработки информации внутри ПЛК предусмотрено несколько типов памяти, включая энергонезависимую. Контроллеры узла сети (coupler) созданы для систем управления, в которых функция управления сконцентрирована на верхнем уровне. Сoupler выполняет функции обмена данными между модулями ввода-вывода по внутренней шине системы WAGO I/O (она имеет собственное название – K-bus) и осуществляет передачу данных на управляющий компьютер по сетевому протоколу. Имея упрощённый функционал, контроллер узла сети стоит значительно дешевле ПЛК. Фактически coupler – это интеллектуальная клемма.
ПЛК WAGO I/O позволяют для большей части модельного ряда подключать до 256 модулей ввода-вывода, а для контроллеров узла сети – до 64 модулей. Несколько лет назад в линейке производителя появились модели головных устройств, получивших обозначение ECO (экономичный), к которым можно подключать не более 8 модулей ввода-вывода. Применение моделей ECO оправданно на небольших объектах автоматизации для желающих сэкономить и не переплачивать за излишний функционал.
Не секрет, что многие производители оборудования стараются максимально привязать заказчика к своим решениям, используя специализированные виды протоколов передачи данных. Замена производителя приводит к затратам на освоение и переход на другую шину передачи данных. Концепция WAGO I/O решает данную проблему полностью. В линейке головных устройств есть модели с поддержкой Ethernet TCP/IP, PROFIBUS DP/FMS, PROFIBUS DP-V1, PROFIBUS DP fiber optic, INTERBUS, INTERBUS LWL, CANopen, Modbus, DeviceNet, CAL, LonWorks, II/O-LIGHTBUS. Использование контроллеров в существующих промышленных сетях PROFIBUS, INTERBUS, CANopen упрощается за счёт наличия конфигурационных файлов для интеграции в программные пакеты для этих сетей. Возможно применение WAGO I/O и в автоматизации зданий, система позволяет подключаться к открытым прикладным протоколам (LonWorks, KNX, BACnet); использовать протоколы, основанные на Ethernet (BACnet IP, KNX IP или Modbus TCP) и применять прикладные шины, такие как DALI, SMI, M-Bus.
Большую популярность сегодня приобрели системы на базе Industrial Ethernet. Их преимущества состоят в отказоустойчивости, высокой пропускной способности и скорости передачи данных, стойкости к электромагнитным излучениям. Большое количество протоколов, основанных на принципах сети Ethernet, их популярность и доступность гарантируют заказчику, ранее не знакомому с промышленной автоматизацией, высокую скорость и лёгкость интеграции системы в проект. Изначально в линейке присутствовало всего несколько моделей с поддержкой Ethernet TCP/IP. Контроллер 750-841 (рис. 2) по праву может называться легендарным, поскольку он продержался на конвейере более 10 лет и разошёлся по миру многотысячными тиражами.
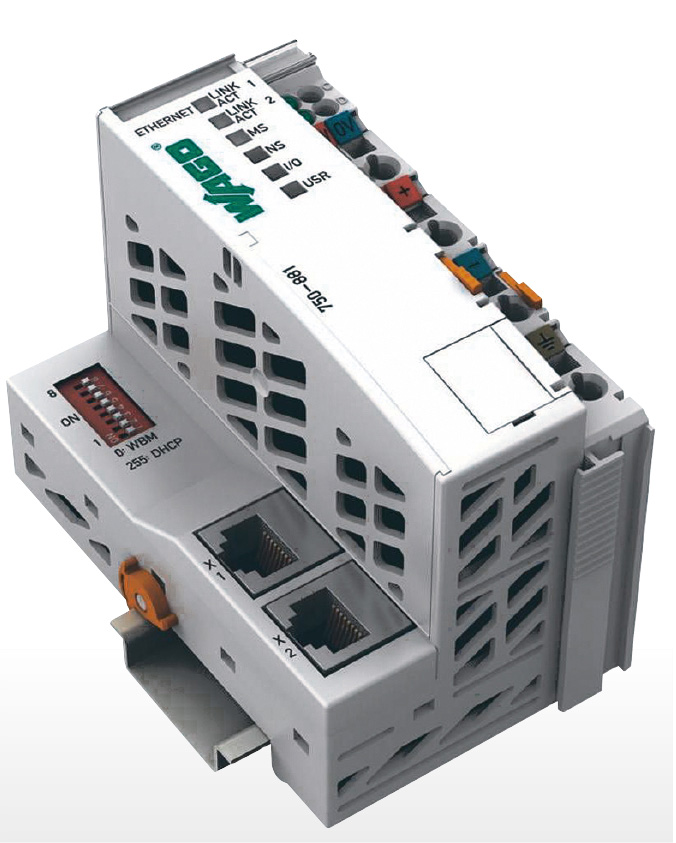
Уникальным решением модели стала возможность программирования ПЛК не только через специальный конфигурационный кабель, но и через порт Ethernet при помощи стандартного разъёма RJ-45. Встроенный Web-сервер позволял видеть состояние передачи по протоколу TCP/IP; информацию о среде CoDeSys; просматривать список установленных модулей и состояние каналов, находясь в любой точке мира, достаточно было подключиться к сети Internet и ввести адрес контроллера.
Популярность стека TCP/IP за последние годы только выросла. Многие предприятия предпочли иметь единый стек протоколов передачи данных и в офисе, и на производстве. Теперь настройкой связи промышленного оборудования мог заниматься системный администратор, ранее обслуживавший только офисную технику. Следуя этой тенденции, компания WAGO выпустила целое семейство разнотипных контроллеров исключительно с данным протоколом. Появились многопортовые модели со встроенными коммутаторами и дополнительными сетевыми адаптерами, с бюджетными и высокопроизводительными процессорами (табл. 1).
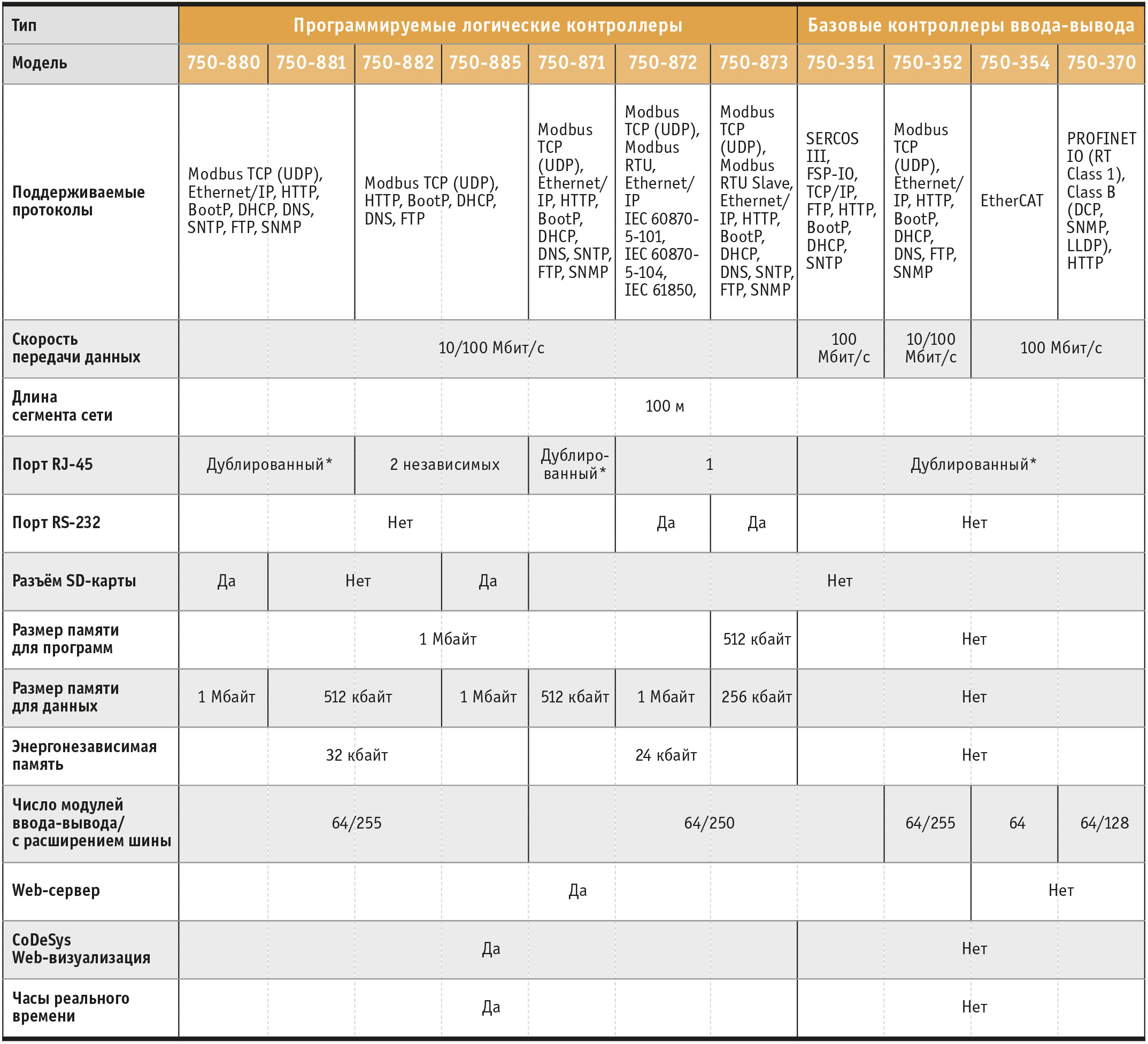
Новая серия получила маркировку 750-88x. Заменой легендарного контроллера 750-841 стала модель 750-881 (рис. 3).
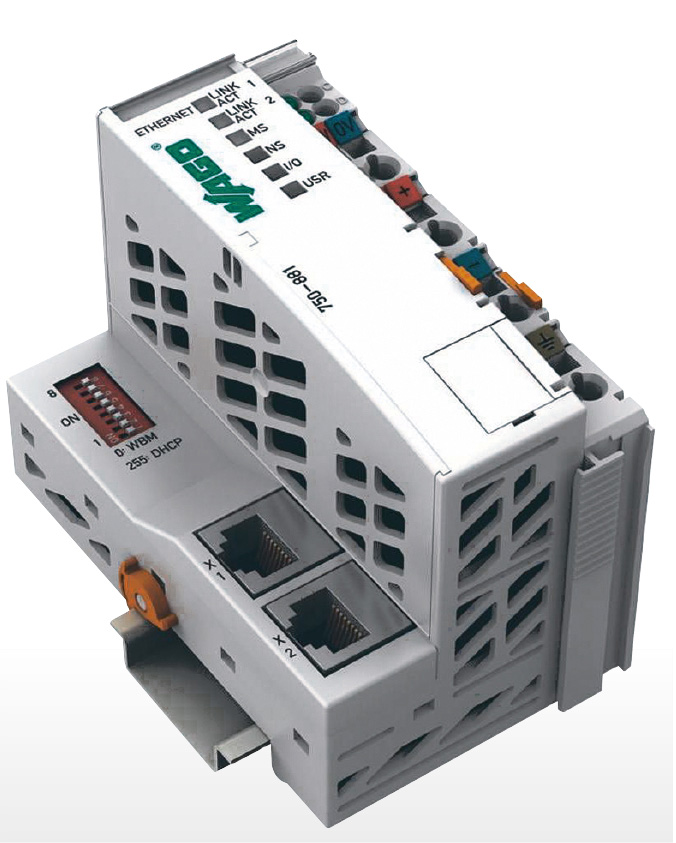
Её стоимость равнялась цене 750-841, но пользователь получал огромные преимущества по функционалу. В контроллере 750-881 установлен 32-битовый процессор с частотой 80 МГц, имеются два разъёма Ethernet и стандартный двухпортовый переключатель – в процессе работы информационный обмен идёт по одной линии связи, а при диагностике обрыва автоматически переключается на резервную. Предусмотрено наличие съёмного SD-носителя информации ёмкостью 8 Гбайт. Мощный вычислитель новинки позволил в полной мере использовать возможности встроенной в CoDeSys Web-визуализации (рис. 4).
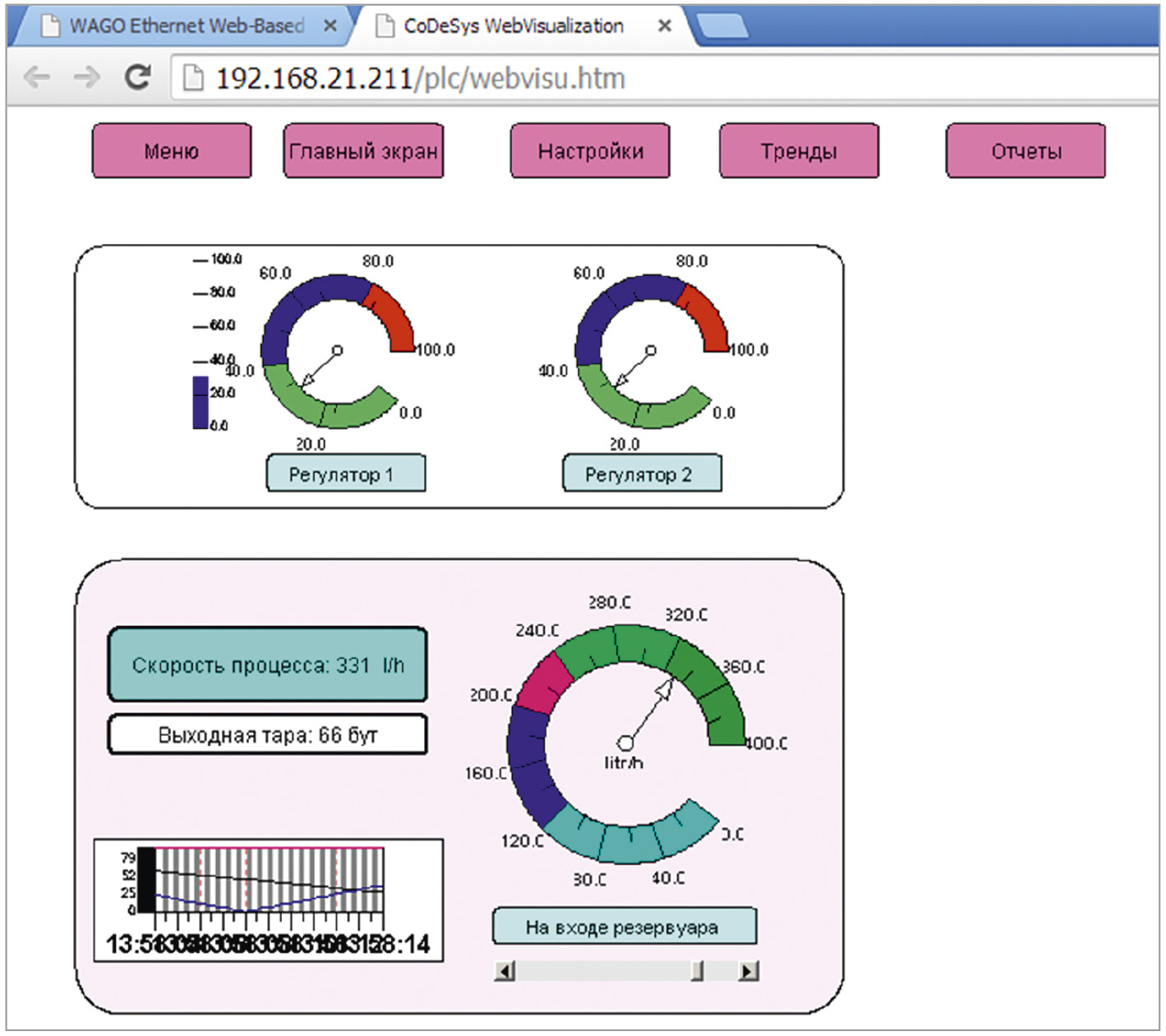
Помимо поддержки протокола Modbus TCP и доступа через FTP к флэш-памяти на контроллере реализована Web-технология SSI (Server Side Intreface). Встроенный в контроллер Web-сервер поддерживает JScript – популярный и поддерживаемый всеми современными Internet-браузерами язык программирования для динамического обновления информации на Web-странице. Его использование позволяет применять различные элементы для индикации и управления при разработке интерфейса Web-приложения. Также возможна разработка Web-страниц с использованием языка HTML, шаблонов страниц и каскадных таблиц стилей CSS. Есть поддержка Java-апплетов.
Контроллеры серии PFC200
В модельный ряд компании WAGO давно вошли устройства с мощными процессорами и возможностью вывода графики через отдельный порт, например VGA или DVI. Такие модели оснащались несколькими типами сетевых интерфейсов, обычно PROFIBUS и CANopen, и имели несколько портов USB для подключения клавиатуры и мыши. На момент создания они назывались промышленными компактными компьютерами (Сompact PC). Идея такого устройства заключалась в переносе мощности компьютера верхнего уровня максимально близко к полевым устройствам. Одновременно с этим модули ввода-вывода непосредственно подключались к Сompact PC, а программирование осуществлялось в адаптированной среде CoDeSys (WAGO-I/O-PRO CAA). На базе такого компьютера можно построить автономный узел с архивированием событий на съёмный носитель CompactFlash. В качестве операционной системы применялась Linux 2.6.Разработчики Сompact PC были ограничены доступностью процессоров с низким тепловыделением и вычислительной мощностью. Если говорить о компактных моделях начального уровня, то в модели 758-870 применялся процессор AMD Geode SC1200 с частотой 266 МГц. Ему на замену пришла модель 750-876, получившая среди пользователей название «бронепоезд» за свой внешний вид и внушительную массу (рис. 5).
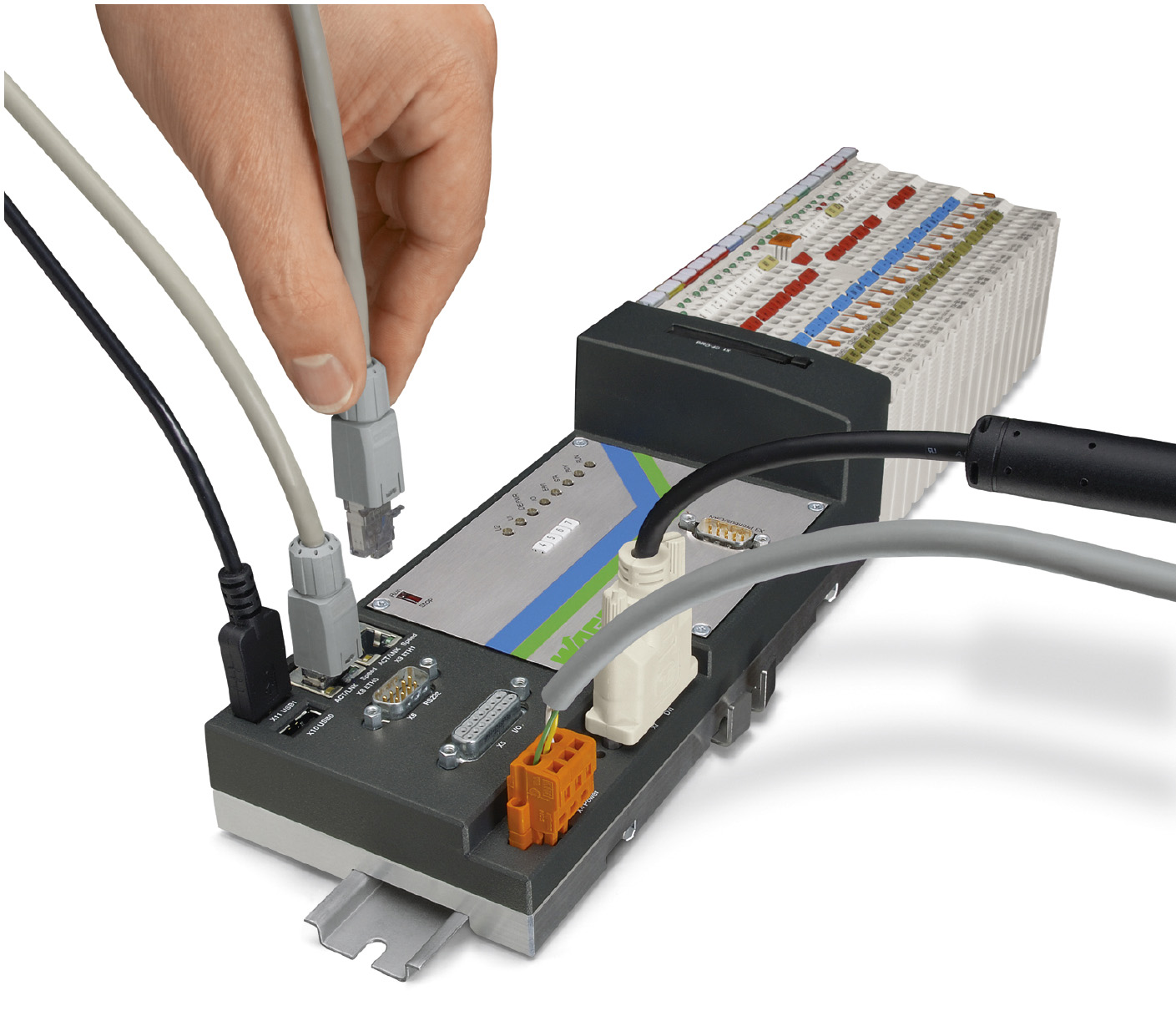
Избыточный вес создавало мощное основание-радиатор для охлаждения процессора Celeron c частотой от 600 МГц до 1,4 ГГц.
Появление новых процессоров позволило создать мощные и одновременно компактные модели Сompact PC. Кроме того, были переработаны алгоритмы вычислений, что дало возможность использовать модели с низкой тактовой частотой.
На смену тяжёлым решениям пришли компактные модели серии PFC200 (рис. 6).
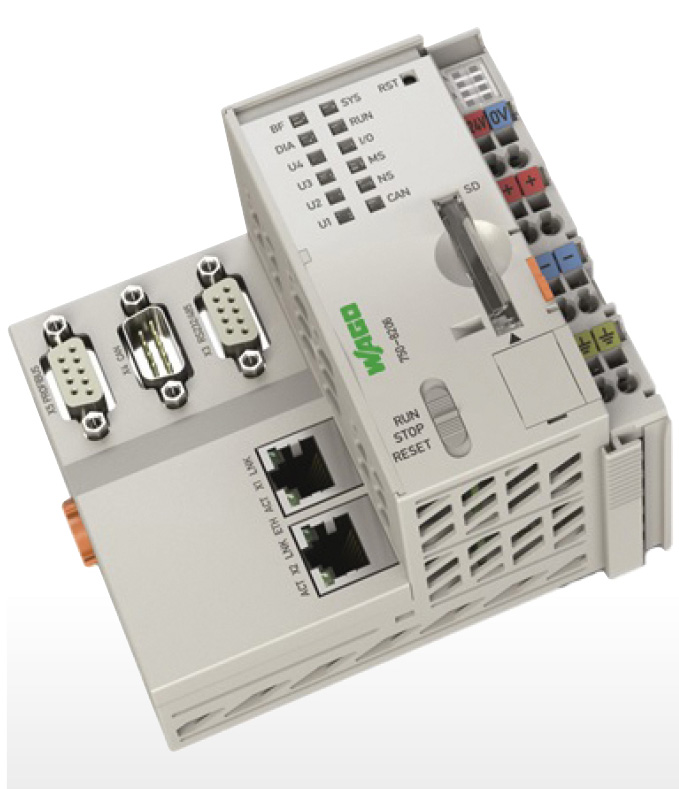
Они обладают следующими характеристиками: процессор ARM Cortex-A8 600 МГц, дублированный порт Ethernet 10/100 Mбит/с, возможность установки SD-карты ёмкостью до 32 Гбайт, операционная система реального времени Linux 3.6 (с RT-Preemption patch), программирование на C/C++, встроенный Web-сервер и возможности визуализации. В табл. 2 приведены сравнительные характеристики новых контроллеров.
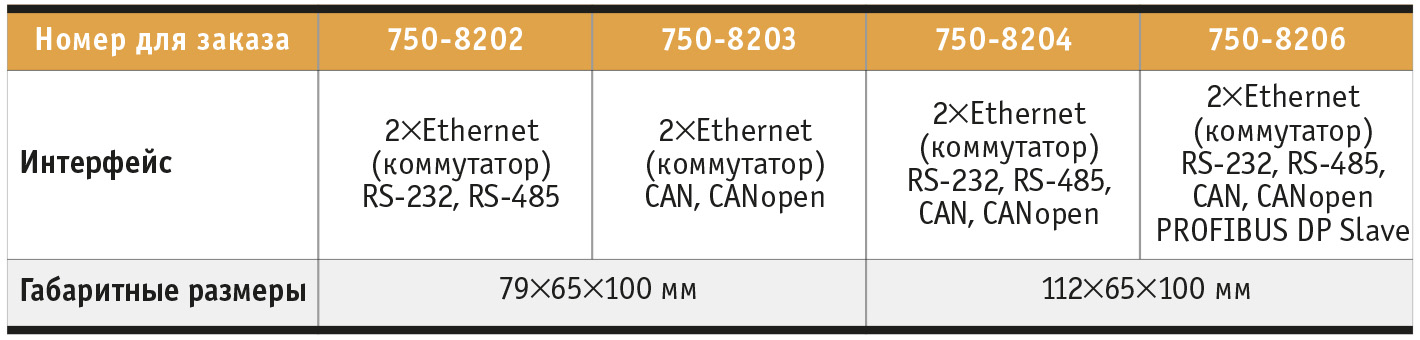
Уникальный функциональный набор контроллера (рис. 7) сделал его незаменимым для обучения в вузах, поскольку он позволяет решать прикладную задачу сразу несколькими способами.
ПО контроллера позволяет удалённо работать с базами данных MySQL и MS SQL в качестве клиента.
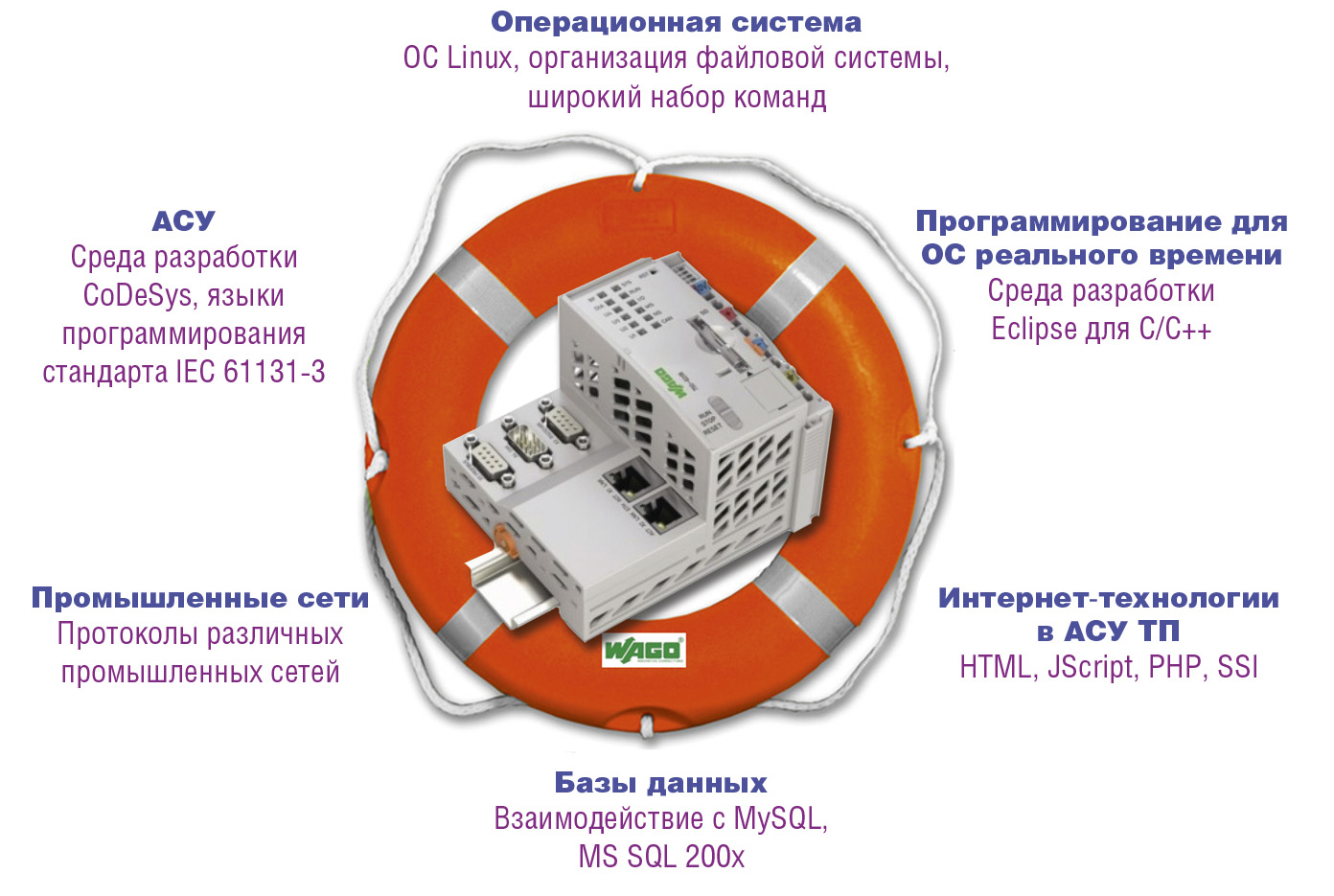
В серии PFC200 реализована поддержка протоколов удалённого доступа: Telnet, SSH, FTP, SFTP. В комплект поставки контроллера входит кросс-средство (toolchain) для разработки ПО на языках программирования С/С++, которое легко интегрируется с IDE Eclipse.
Серия PFC200 способна решать очень широкий круг задач: быть мощным вычислительным ядром, коммуникационным шлюзом между несколькими протоколами, сервером Web-приложений, платформой для встраиваемых решений.
Решения для экстремальных условий эксплуатации
Компания WAGO изначально имела несколько линеек модулей для различных температурных диапазонов. Наиболее популярные серии рассчитаны на стандартный диапазон от 0 до +55°С. Реже были востребованы модели c условиями эксплуатации от –20 до +60°С, что вполне достаточно для применения в Европе. Однако опыт других производителей, в том числе российских, дал толчок к разработке устройств для более жёстких условий.Новая серия, изначально получившая название Temper IO, в дальнейшем была переименована в XTR (eXtreme Temperature Range). Модули и контроллеры XTR (рис. 8) работают в диапазоне температур –40…+70°C, имеют повышенный уровень защиты от импульсных скачков напряжения (до 5 кВ) и устойчивы к вибрационным нагрузкам до 5g.
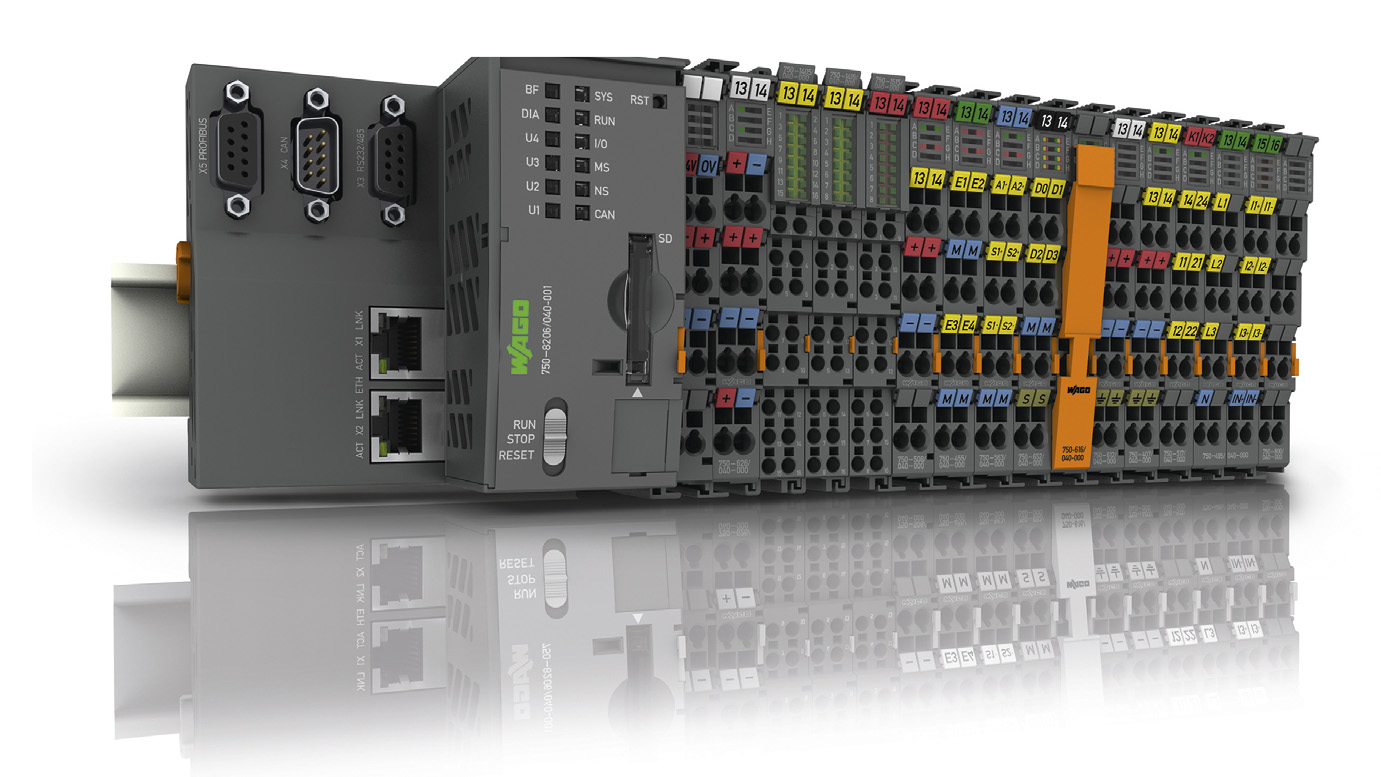
Платы и электронные компоненты оборудования покрыты специальным лаком, что позволяет применять систему в условиях повышенной влажности: модели имеют влагостойкость класса 3K7 в соответствии со стандартом EN 60721-3-3 (без прямого воздействия струи воды). Соответствие протоколам EN 60870-2-1 (стабильность напряжения и изоляции) а также поддержка протоколов телемеханики IEC 60870-5-101, -103, -104, IEC 61850-7 и IEC 61400-25 и повышенная вибростойкость делают новую серию незаменимой на современных электрических подстанциях.
Сфера применения серии XTR подразумевает установку на самом объекте или максимально близко к нему, например, для контроля температуры хранилищ нефтеперерабатывающего производства или в составе системы управления проходческого щита для прокладки туннелей. Модули для расширенных диапазонов рабочих температур отличаются номером для заказа: в нём после знака «/» идёт температура в формате 025 или 040, например 750-881/040-000.
Новые тенденции – комплексный инжиниринг и мехатроника. Среда разработки e!COCKPIT
Слово COCKPIT имеет несколько значений: рубка корабля, кабина пилота самолёта или спортивного автомобиля. Применительно к новой концепции WAGO это новый вид программного обеспечения, которое позволит заказчику контролировать, программировать или управлять большим количеством систем, используя лишь одну точку входа.Разработка подобной системы связана с усилением роли мехатроники в современном обществе. Для мехатроники характерно стремление к полной интеграции механики, электрических машин, силовой электроники, программируемых контроллеров, микропроцессорной техники и программного обеспечения. Таким образом, на создание механизма, состоящего из множества компонентов, требуется всё меньше и меньше времени. Необходимо одно ПО, способное управлять целой группой контроллеров, осуществлять сквозное программирование десятков и сотен узлов одновременно. Такое ПО должно сократить время от строительства до ввода машины в эксплуатацию.
В основе e!COCKPIT лежат четыре составляющие: конфигурирование, программирование, визуализация и диагностика. Рассмотрим их в сравнении со стандартной средой программирования контроллеров WAGO-I/O-PRO CAA.
Конфигурирование: новый интерфейс максимально ориентирован на визуальное представление системы. На экране контроллер отображается в виде рисунка, на нём можно выделить конкретный модуль, посмотреть и при необходимости поменять его параметры, значения входов и выходов. Можно отслеживать коммуникационный обмен, использовать функции drag-and-drop, copy-and-paste или функции групповой обработки объектов.
Программирование: ядром новой системы стал программный комплекс CoDeSys 3.0. Активно исспользуется объектно-ориентированное программирование. Текстовые сообщения заменены графическими объектами. Значительно обновлена концепция визуализации, где вместо Java-аплетов применяется технология HTML5. Это позволило многократно использовать существующий проект, дорабатывать его и загружать сразу на группу контроллеров, одновременно контролируя параметры сети.
Визуализация: обновлена и сильно доработана, с точки зрения отображения процесса, мощный встроенный редактор изображений, поддержка drag-and-drop, прямой доступ к переменным программы. Реализована поддержка современных Web-браузеров с HTML 5 и СSS, а также неограниченного числа языков интерфейса (поддержка Unicode).
Диагностика: интегрированная возможность тестирования подключений и самих устройств. Возможность вывода на экран различных графиков отображения процесса работы, тревог, настройки всплывающих окон с сообщениями (рис. 9), – всё это позволяет проводить оперативный поиск и устранение ошибок.
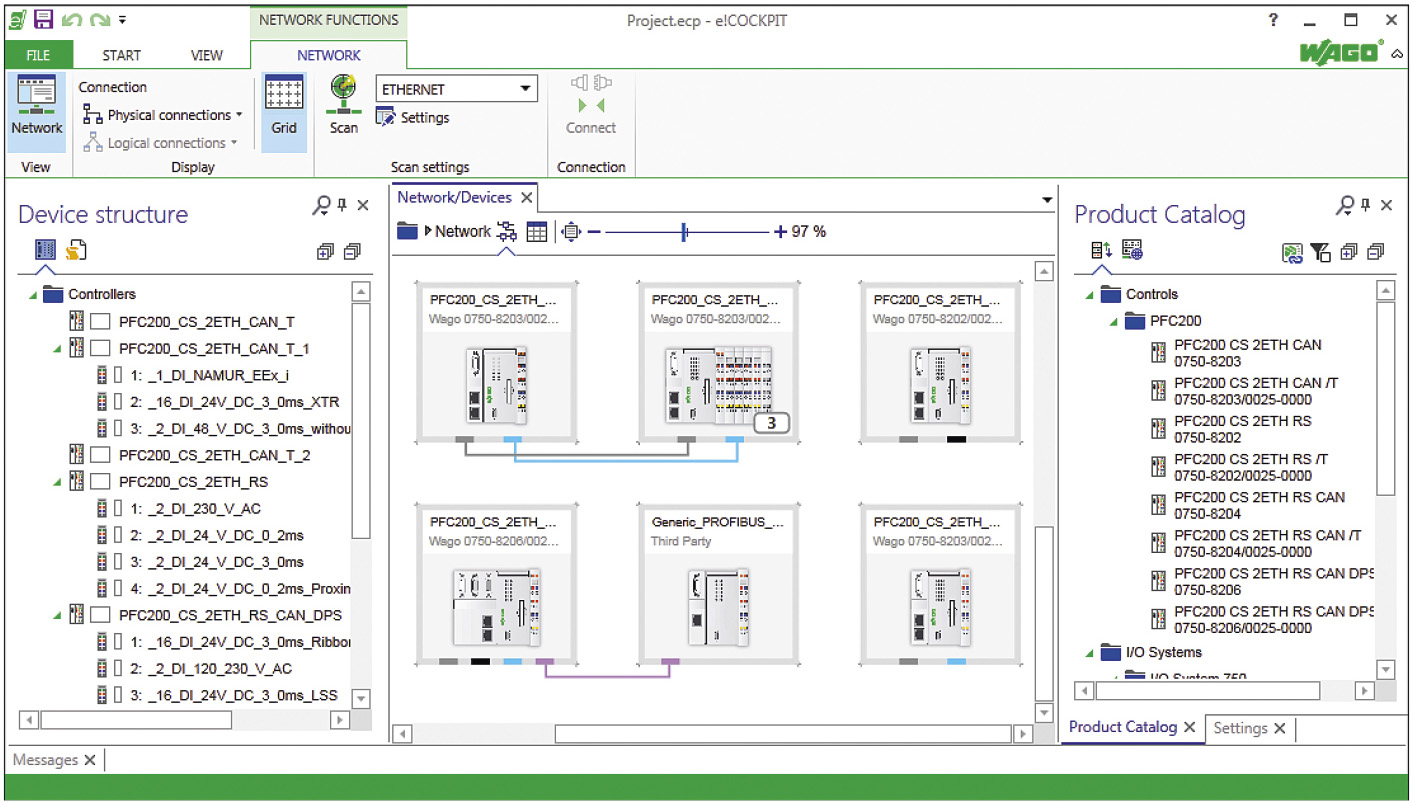
Примеры применения
Строительство
На страницах журнала «Современные технологии автоматизации» уже описывались типовые решения компании ООО «КИП-Сервис» (г. Казань) для автоматизации бетоносмесительных установок (БСУ) на базе контроллеров WAGO I/O [1]. Высокая надёжность оборудования (порядка 100 проектов без единого отказа) повлияла и на дальнейшее расширение спектра выполняемых задач. Компания осваивает всё новые и новые ниши строительной индустрии, и, пожалуй, одним из самых интересных внедрений контроллеров WAGO I/O стали проекты по адресной подаче бетона.При автоматизированной подаче бетонной смеси осуществляется полноценный производственный цикл, от заказа необходимого количества определённой марки бетона до его изготовления и доставки до места формовки. На рис. 10 приведена основная мнемосхема технологического процесса, а на рис. 11 в упрощённом виде представлена структурная схема автоматизированной системы, в которой все основные узлы объединены в локальную сеть Ethernet.
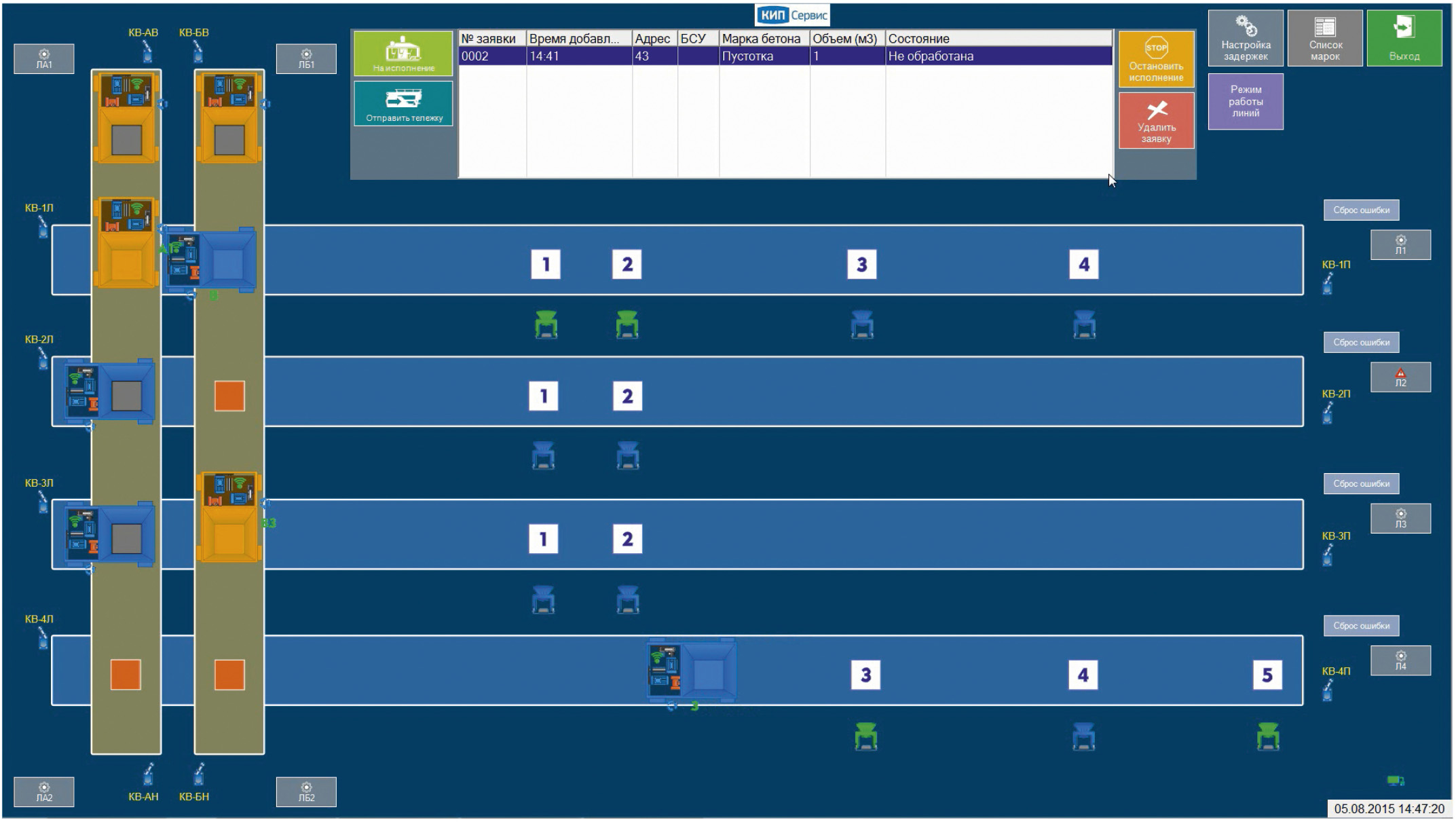
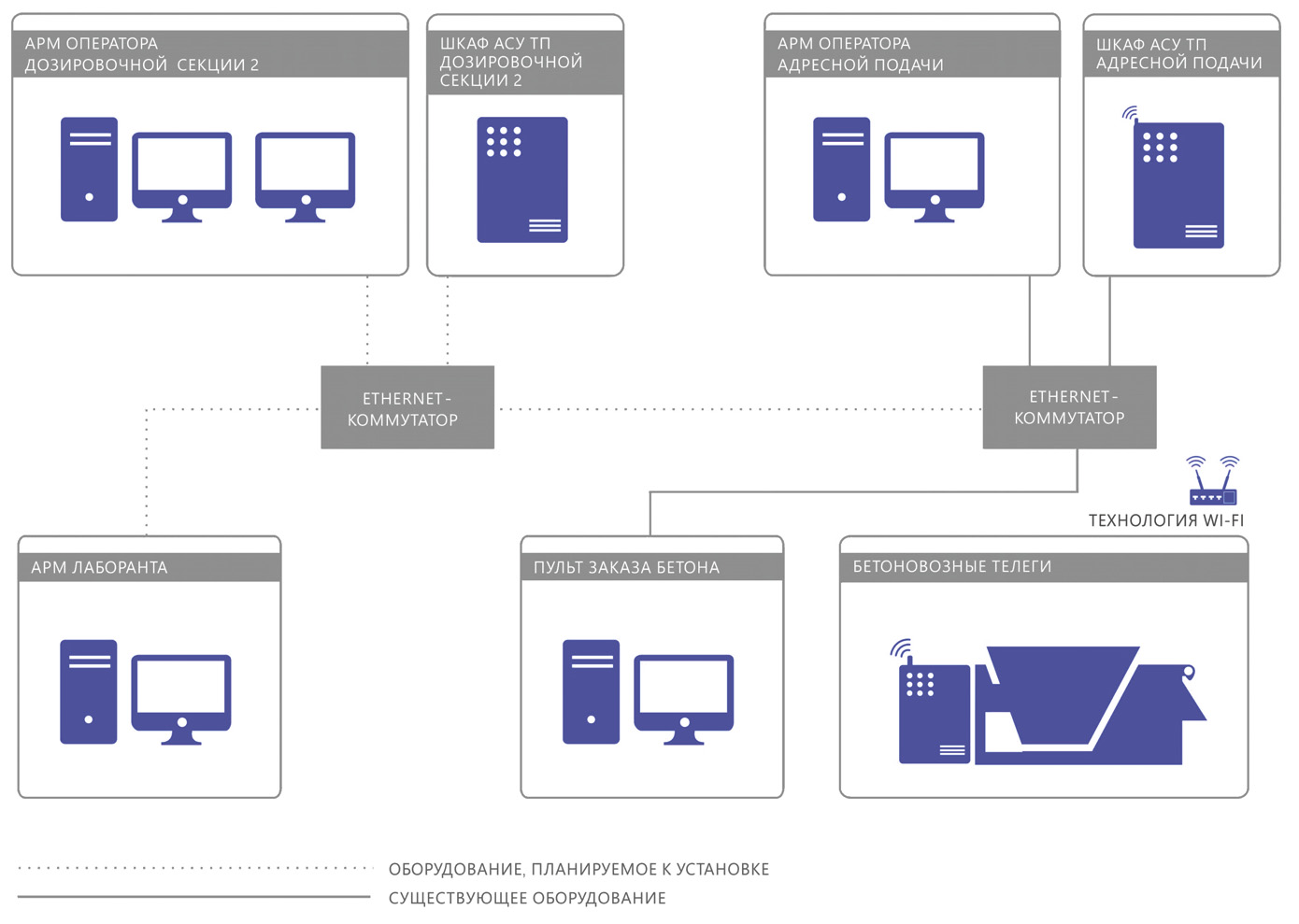
В формовочном цехе по местам производства железобетонных изделий установлены пульты заказа бетона (рис. 12).
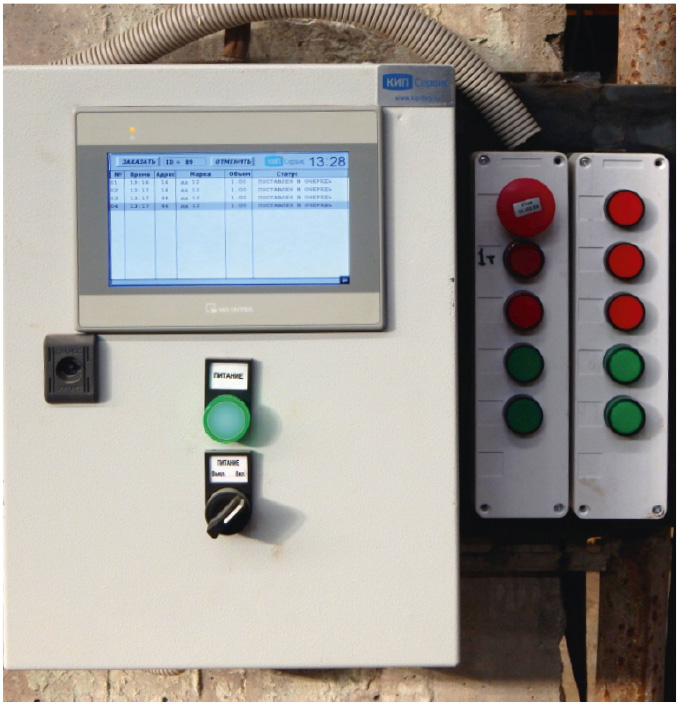
С пульта электронная заявка автоматически попадает на АРМ оператора дозировочной секции и АРМ оператора адресной подачи, после чего начинается этап подготовки и выполняется доставка бетонной смеси нужной марки к формовочному участку. Транспортировка бетонной смеси заказа происходит с помощью бетоновозных тележек в автоматическом режиме под управлением главного шкафа АСУ ТП адресной подачи.
На каждой тележке установлен шкаф управления (рис. 13), выполненный на базе контроллера WAGO I/O серии 750-88х с набором модулей ввода-вывода.

Контроллер WAGO I/O выполняет следующие задачи:
- взаимодействует с главным шкафом АСУ ТП по протоколу Modbus TCP через канал беспроводной связи Wi-Fi;
- выполняет управление точным позиционированием тележки на местах погрузки/выгрузки бетонной смеси;
- осуществляет контроль защиты от столкновений с препятствиями на пути тележки.
с интерфейсом для подключения инкрементного шифратора. Шифратор механически соединён с вращающимся валом тележки, и его выходы А и В (квадратура выхода, предназначенная для подсчёта импульсов/пройденного расстояния и определения направления движения), а также выход Z (указатель нулевой отметки/импульс полного оборота) непосредственно подключаются к соответствующим входам модуля.
Поскольку в процессе эксплуатации бетоновозной тележки работают мощный вибратор и затворы, а движение осуществляется по рельсам, то важным преимуществом применения контроллеров WAGO I/O в этом проекте является его вибростойкая модульная конструкция. Кроме того, вибростойкий контакт проводов обеспечивается пружинной клеммой CAGE CLAMP на каждом модуле WAGO I/O.
Добыча и подготовка нефти
Важным требованием к оборудованию для автоматизации технологических процессов добычи и подготовки нефти является наличие соответствующих разрешительных документов.К моменту обсуждения решений для одного из проектов ОАО «Ульяновскнефть» в 2014–2015 годах на контроллеры и модули серии WAGO I/O уже имелись сертификат соответствия техническому регламенту Таможенного союза и сертификат об утверждении типа средств измерений Федерального агентства по техническому регулированию и метрологии. Это стало одним из важных аргументов при выборе оборудования WAGO I/O для АСУ ТП установки предварительного сброса воды (УПСВ) Верхозимского месторождения ОАО «Ульяновскнефть». В эксплуатацию система была введена в 2015 году специалистами Альметьевского наладочного управления (АНУ) ПАО «Нефтеавтоматика».
В системе сбора и подготовки нефти на месторождении УПСВ выполняет важные функции: подготовка нефтяной эмульсии к расслоению путём подачи реагента-деэмульгатора, сепарация и обезвоживание нефти с последующей подачей воды в систему поддержания пластового давления, сепарация попутного нефтяного газа от жидкости с последующей его утилизацией. Основными объектами контроля и автоматизации являются нефтегазосепараторы со сбросом воды (НГСВ), резервуары вертикальные (РВС), узлы учёта газа на печи и факелы, блок гребёнок на узле учёта пластовой воды, станция внутренней перекачки, путевые подогреватели, блочная насосная станция (БНС), система контроля загазованности. АСУ ТП УПСВ отвечает за поддержание рационального технологического режима работы УПСВ и обеспечение оперативного информационного контроля режима работы аппаратов и установок, регулирование параметров технологического процесса и управление работой технологического оборудования.
АСУ ТП УПСВ Верхозимского месторождения построена по традиционной трёхуровневой схеме. Структурная схема АСУ ТП приведена на рис. 14.
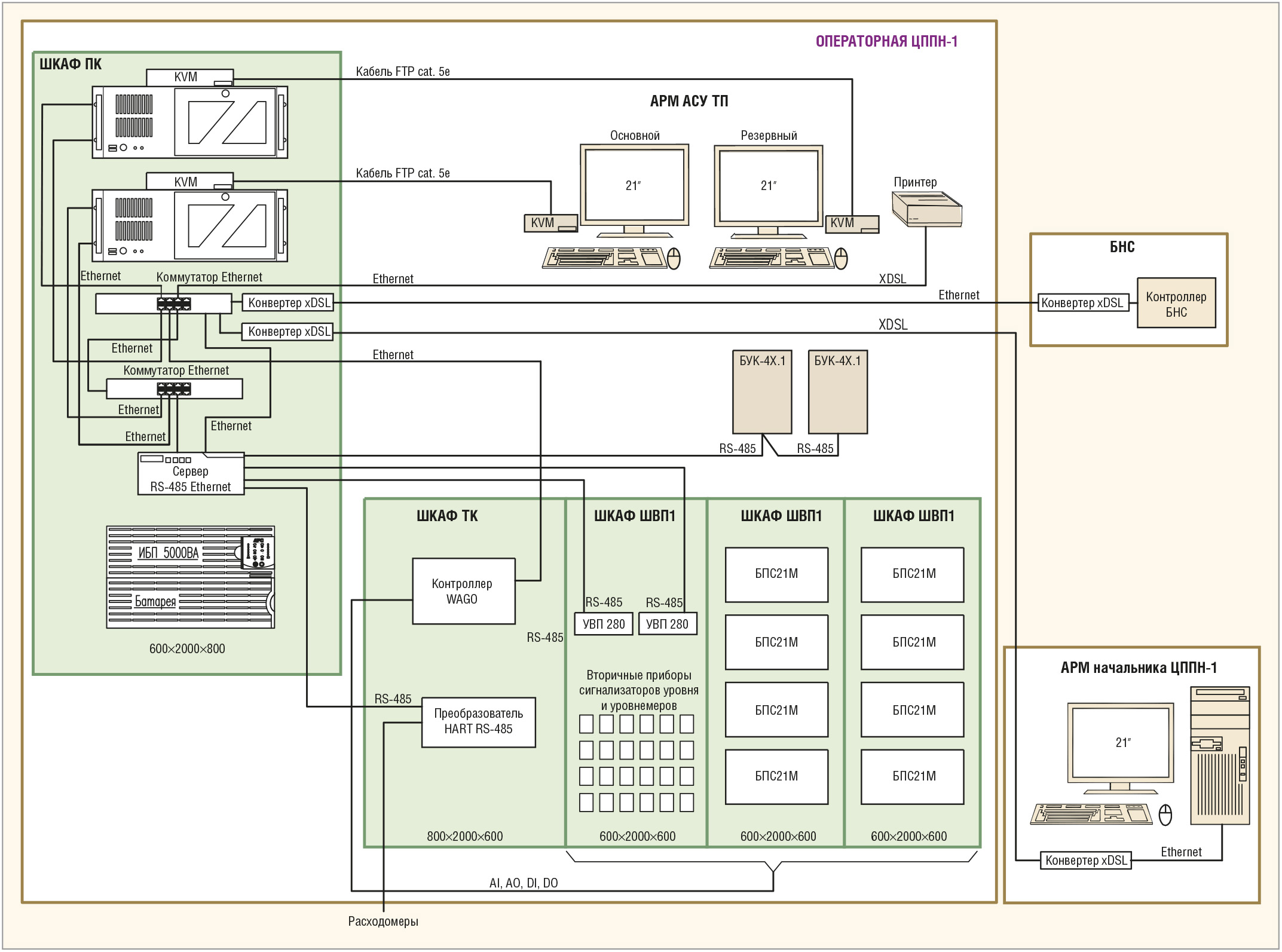
Условные обозначения: шкаф ПК – шкаф промышленных компьютеров; KVM – KVM-удлинитель комплекта устройств ввода-вывода; шкаф ТК – шкаф терминал–контроллер; ИБП – источник бесперебойного питания; шкаф ШВП1…3 – шкаф вторичных приборов; УВП 280 – вторичные приборы для узлов учёта газа; БПС21М – блок питания и сигнализации; БУК-4X.1 – вторичный прибор путевых подогревателей (печей); БНС – блочная насосная станция; AI, DI, AO, DO – аналоговые входы, дискретные входы, аналоговые и дискретные выходы соответственно; ЦППН – цех подготовки и перекачки нефти.
Нижний уровень – первичные средства автоматизации (измерительные преобразователи и датчики, приборы местного контроля, вторичные приборы, агрегатные средства КИПиА, исполнительные устройства и механизмы).Средний уровень АСУ ТП УПСВ построен на базе программируемых логических контроллеров WAGO I/O 750-881. Модульная конструкция системы WAGO I/O позволила гибко подойти к выбору тех или иных типов модулей, исходя из общего перечня сигналов: 80 аналоговых входных сигналов 4…20 мА, 8 аналоговых выходных сигналов 4…20 мА, 384 дискретных входных сигнала (=24 В), 128 дискретных выходных сигналов (=24 В), 5 интерфейсных каналов (HART, Modbus RTU, Modbus TCP). Понятно, что АСУ ТП УПСВ имеет достаточно большую информационную ёмкость, особенно по каналам дискретного ввода-вывода. При подборе соответствующих дискретных модулей WAGO I/O это обстоятельство сыграло в пользу применения расширенных 16-канальных версий – модулей 750-1405 и 750-1505. Такое решение позволило оптимизировать число модулей и общую длину конструкции ПЛК. Для цепей 4…20 мА применены стандартные модули 750-455 и 750-555. На рис. 15 изображён шкаф контроллера ТК с установленной системой WAGO I/O.
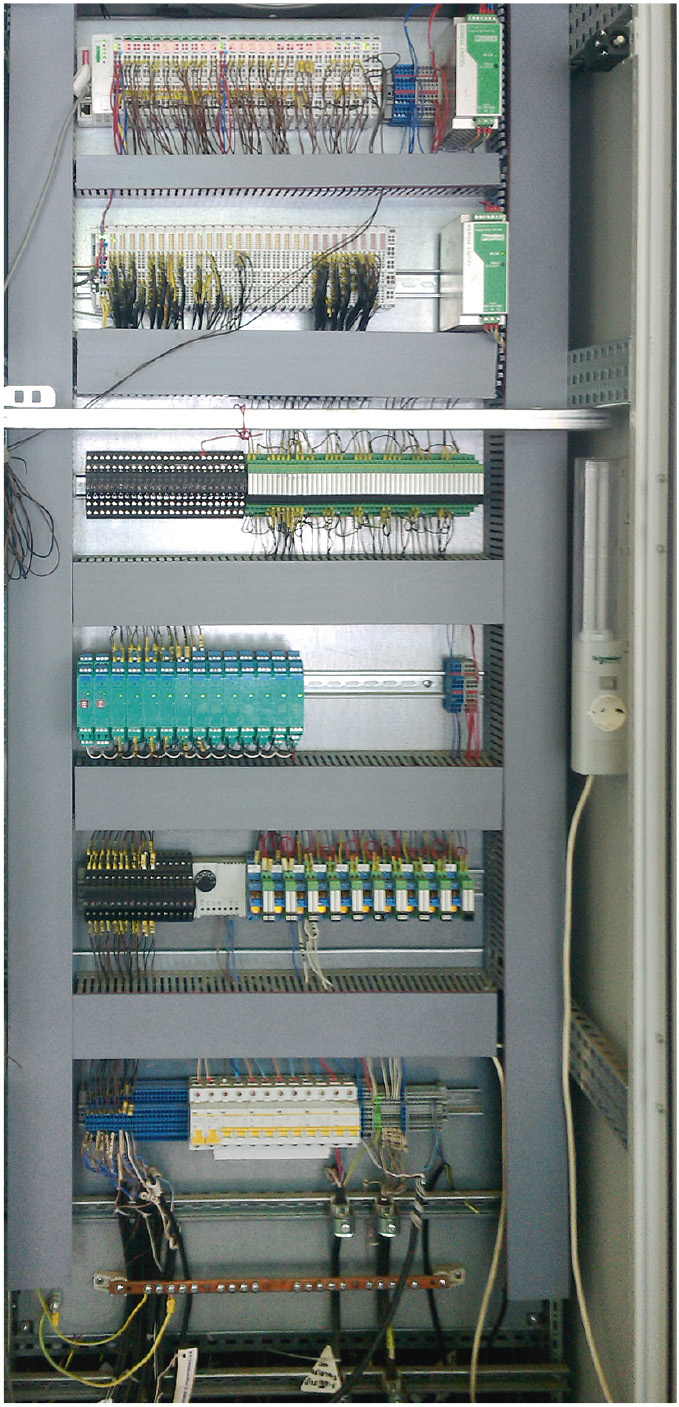
Верхний уровень – программно-аппаратные средства дистанционного контроля и управления технологическими процессами на базе компьютеров AdvantiX (рис. 16): АРМ оператора основной и резервный, АРМ начальника.
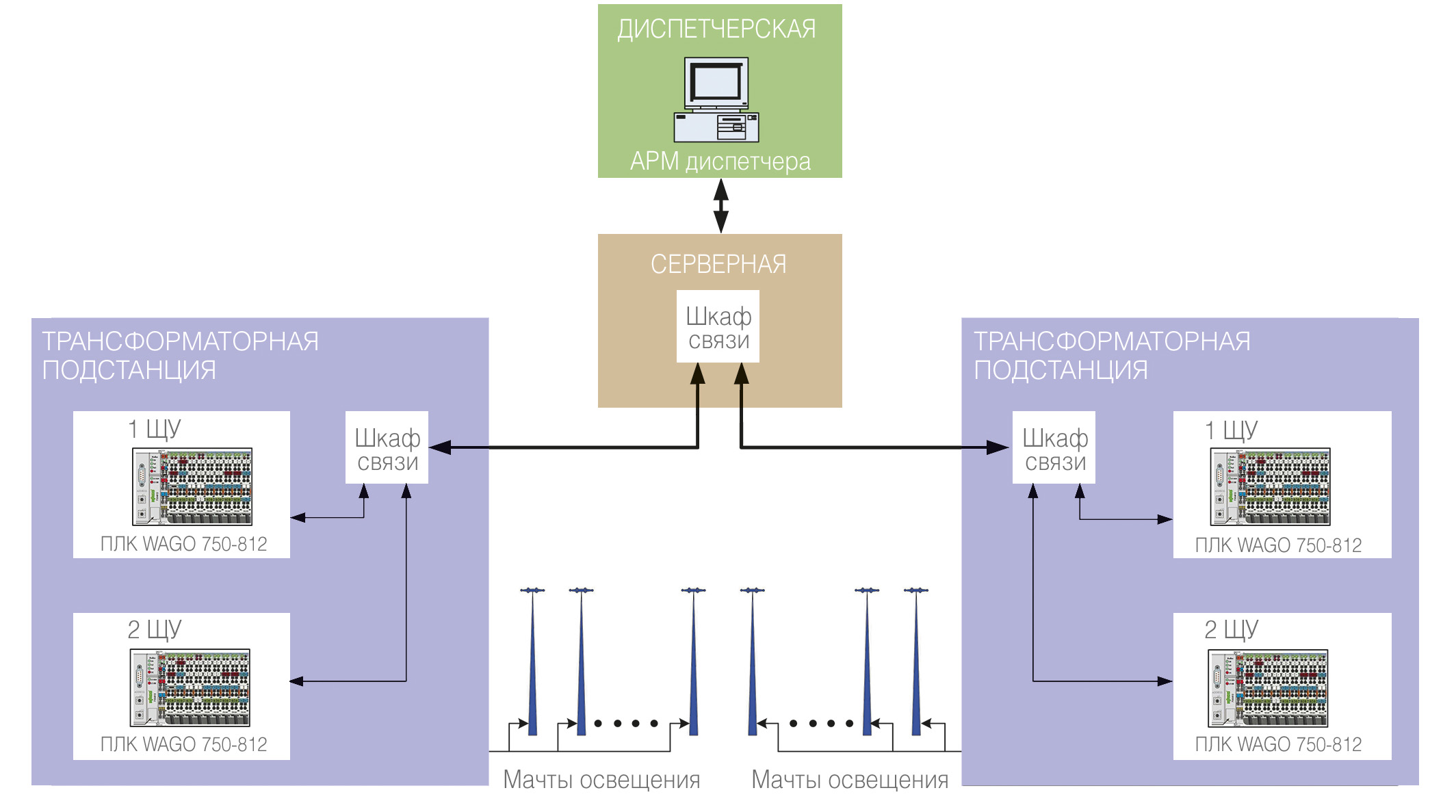
Оборудование АСУ ТП размещено в шкафах компании Rittal. В коммуникационной системе используются удлинитель сети Ethernet компании
EtherWAN и сервер последовательных интерфейсов компании Advantech.
Транспортная инфраструктура
Контроллеры серии WAGO I/O часто применяются на самых ответственных участках транспортной инфраструктуры. Примером такого проекта является система рабочего и дежурного освещения перрона одного из аэропортов Поволжья. В рамках реконструкции этой части аэропортового комплекса системный интегратор ООО «Шатл» (г. Казань) был приглашён для разработки программного обеспечения контроллеров силовых щитов и автоматизированного рабочего места диспетчера, проектирования системы связи. А компания «Вьютек» (г. Казань) выполнила окончательные пусконаладочные работы и передала систему дистанционного управления освещением перрона в рабочую эксплуатацию аэропорта.Объектами управления в данном проекте являлись:
- мачты освещения перрона с лампами рабочего освещения перрона;
- мачты освещения перрона с лампами дежурного освещения;
- лампы заградительных огней.
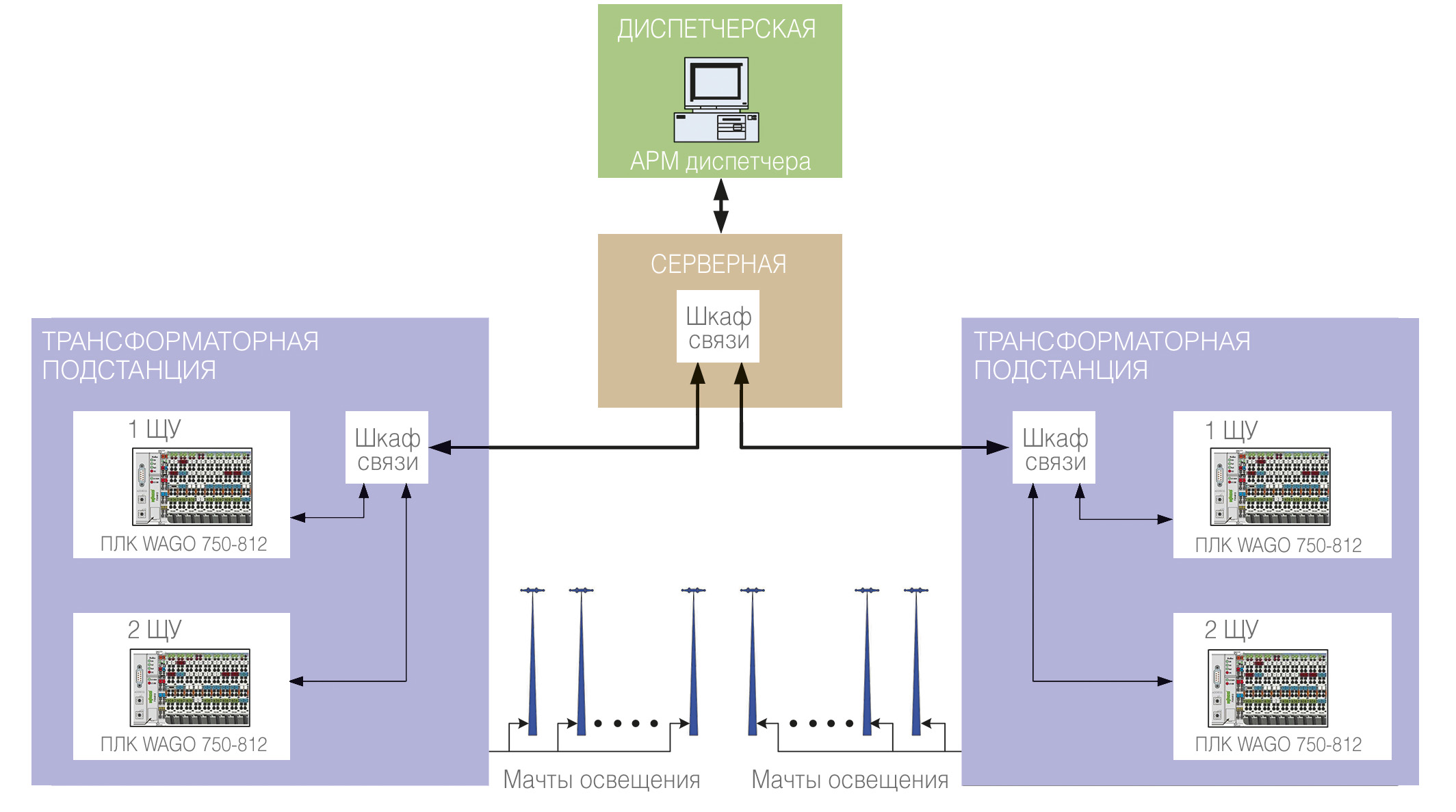
Управление освещением должно было производиться с нескольких трансформаторных подстанций, где планировалось разместить по два силовых щита, отдельно на рабочее и дежурное освещение. Было принято решение в каждом щите в качестве устройства управления использовать программируемый контроллер 750-812 серии WAGO I/O, имеющий интерфейс полевой шины стандарта RS-485 и поддерживающий сетевое взаимодействие по промышленному протоколу Modbus. Программная настройка сетевых параметров порта RS-485 предоставила разработчикам возможность определить наилучшую конфигурацию для линии передачи данных. А модульная конструкция контроллера серии WAGO I/O позволила оптимально подобрать необходимый набор модулей дискретного ввода-вывода (рис. 18) на первом этапе модернизации и обеспечить гибкое масштабирование системы управления в будущем.
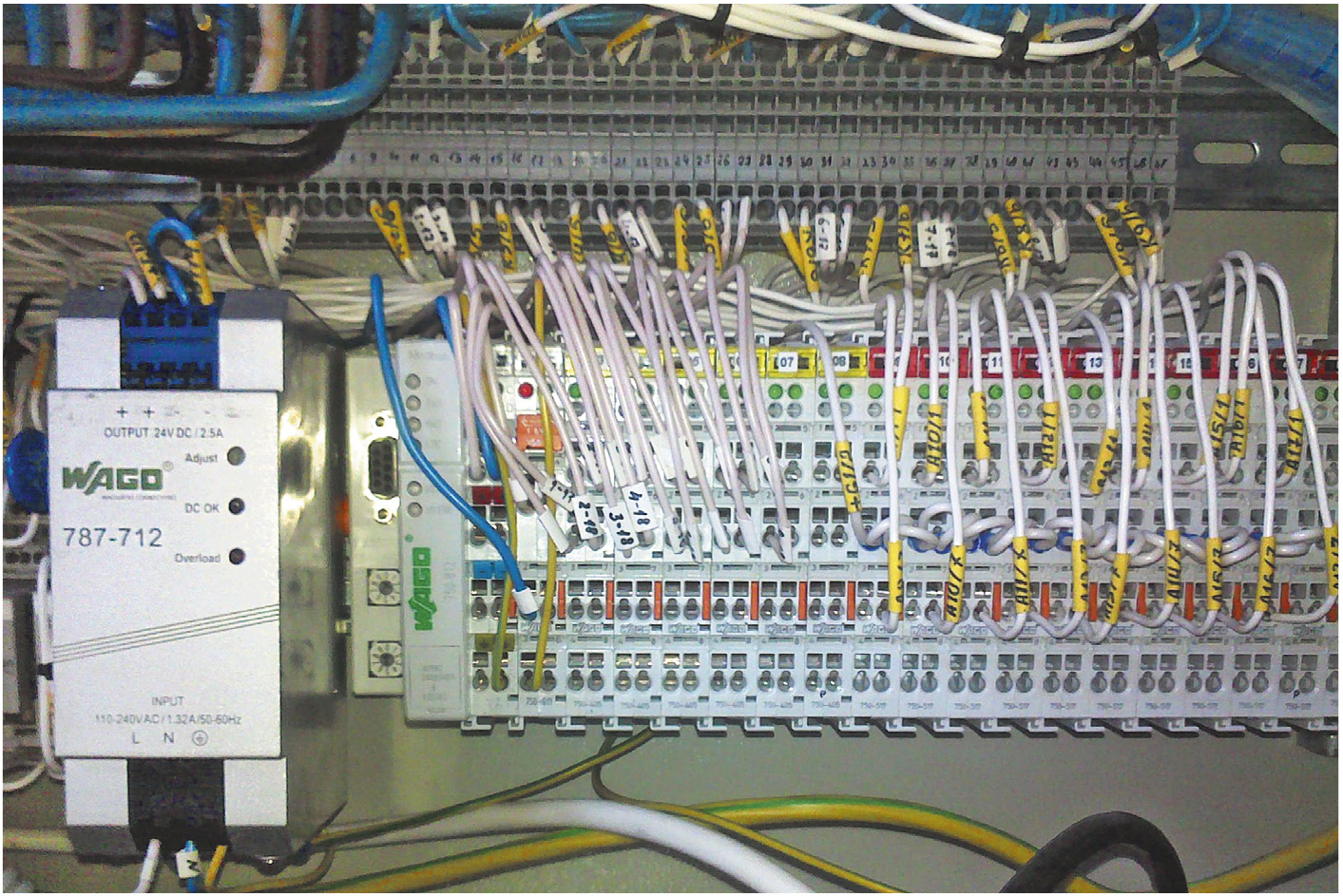
Для реализации обмена данными телеуправления между контроллерами и АРМ диспетчера были задействованы отдельные шкафы связи на каждой трансформаторной подстанции.
После внедрения системы диспетчер, находясь в здании терминала аэропорта, может со своего автоматизированного рабочего места подавать команды на включение/отключение светильников рабочего/дежурного освещения и заградительных огней, контролировать сигнализацию состояния каждого светильника. Пример одного из экранов АРМ диспетчера приведён на рис. 19.
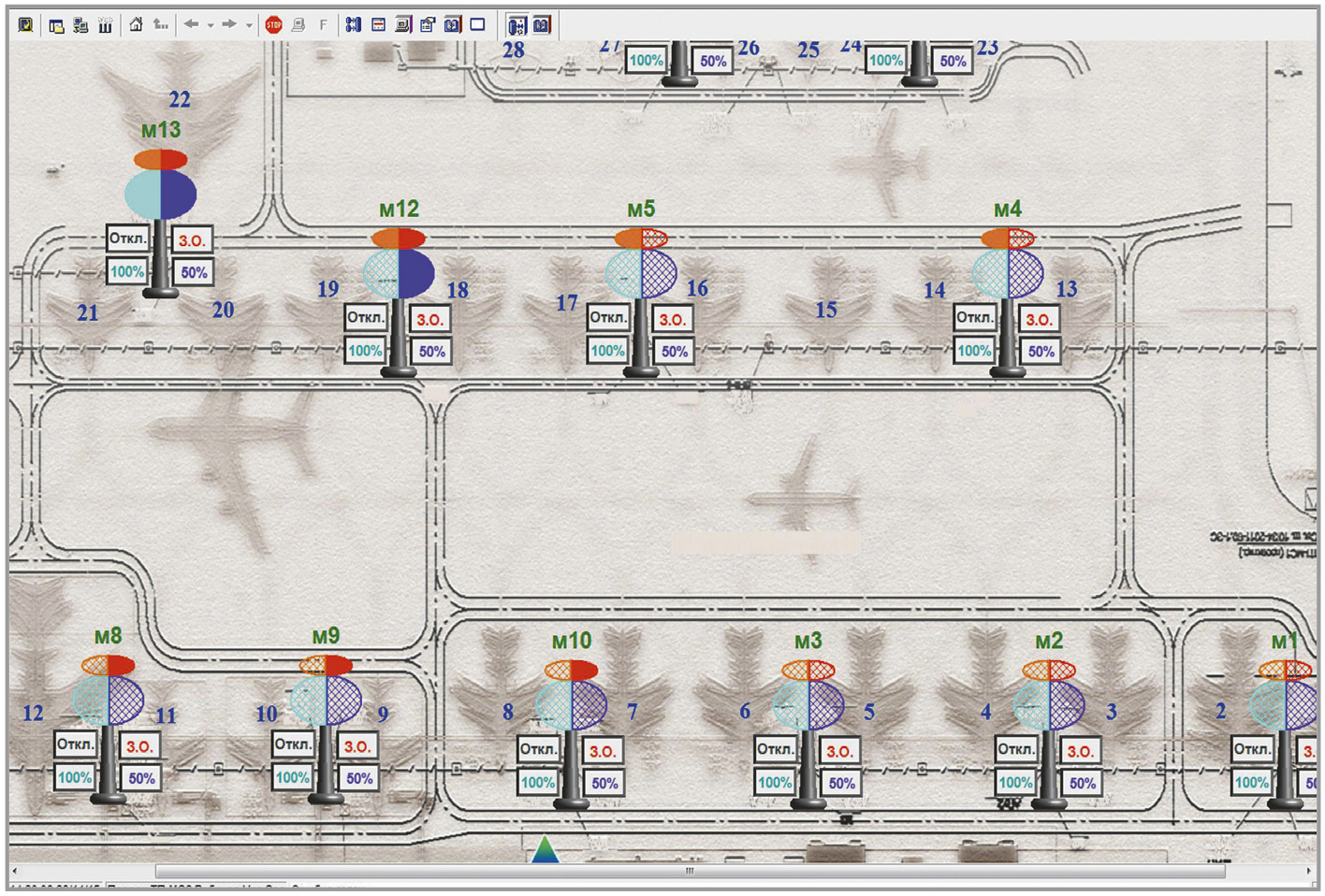
Используя приобретённый опыт, специалисты компании «Вьютек» в 2015 году приступили к реализации нового проекта модернизации аэродромной инфраструктуры. Его важной особенностью стало географическое расположение аэропорта в экологически чистом курортном регионе Кавказа.
По аналогии с предыдущим проектом принципы реконструкции системы рабочего и дежурного освещения перрона были применены и здесь, а техническим заданием заказчика уже было предусмотрено использование контроллеров WAGO I/O серии 750-81х. Предполагалось размещение оборудования WAGO /O в силовых шкафах трансформаторных подстанций, где контроллеры решали бы задачи:
- приёма управляющих сигналов на включение/отключение светильников мачт освещения от рабочей станции диспетчера по протоколу Modbus;
- формирования и передачи управляющих сигналов на выходные модули, коммутирующие силовую нагрузку;
- приёма сигнализации состояния светильников мачт освещения на входные модули;
- передачи сигнализации состояния светильников на рабочую станцию диспетчера по протоколу Modbus.
Разработку автоматизированного рабочего места диспетчера специалисты компании «Вьютек» выполнили с использованием SCADA-пакета Master-SCADA.
Заключение
Продукция компании WAGO на протяжении многих лет применяется в различных сферах автоматизации. Этот выбор обусловлен высоким уровнем производственного процесса, налаженного внутри компании, и активной политики в области освоения новых программных решений. Новый девиз компании ”We Innovate!”, который можно перевести как «Мы внедряем инновации!», в полной мере отражает стремление WAGO к применению новых технологий в своих продуктах. ●Авторы выражают благодарность за предоставленную информацию Захария В.О., Валиуллину Д.Р. (ООО «КИП-Сервис», Казань), Биктимирову А.М. (ООО «Вьютек», Казань), Николаеву М.В. (АНУ ПАО «Нефтеавтоматика», Альметьевск).
Литература
- А. Деркач, Р. Камалиев, В. Маценко. Примеры решений на базе сенсорных панелей Weintek для АСУ ТП и встраиваемых систем // Современные технологии автоматизации. – 2014. – № 3.
фирмы ПРОСОФТ
Телефон: (495) 234-0636
E-mail: info@prosoft.ru
Если вам понравился материал, кликните значок - вы поможете нам узнать, каким статьям и новостям следует отдавать предпочтение. Если вы хотите обсудить материал - не стесняйтесь оставлять свои комментарии : возможно, они будут полезны другим нашим читателям!