Введение
На обогатительных фабриках плотность пульпы измеряют, в основном, в продуктах измельчения – на сливе классификаторов рудных мельниц и сливе гидроциклонов второй стадии измельчения. В этих случаях плотность является показателем качества процесса измельчения. Кроме того, необходимость в измерении плотности возникает при создании расходомеров твёрдого в потоках пульпы на флотацию.
Несмотря на исключительную важность плотности как технологического параметра на современных фабриках фактически отсутствует её автоматический контроль. В некоторых случаях применяют гидростатические плотномеры, которые, как правило, ненадёжны в работе и отличаются большой погрешностью измерения. Однако обычно плотностный режим проверяют вручную методом кружечных замеров. Поскольку такие замеры производятся нечасто, данный параметр практически не контролируется в технологическом процессе.
В настоящее время повышаются требования к качеству производства, и сложившуюся ситуацию нужно менять.
Специалисты ООО «ASU Technology» при решении задачи автоматического контроля плотности слива гидроциклонов на медной обогатительной фабрике Алмалыкского ГМК пошли по пути создания системы контроля на основе современных высокоточных датчиков физических параметров и компьютерных технологий. В настоящей статье описывается разработанное техническое решение.
Предварительно проанализируем несколько известных технических решений (им посвящён следующий раздел статьи), а в первую очередь рассмотрим часто применяемый метод кружечных замеров плотности. Этот метод получил широкое распространение на фабриках, но, что характерно, никто не знает, какова его погрешность в конкретных условиях. Можно указать три основные погрешности: погрешность, связанная с представительностью отобранной пробы, погрешность отбора заданного объёма пульпы и погрешность взвешивания пробы. Кроме того, неизбежны другие погрешности. Например, плотность пульпы в технологической ёмкости или пульпопроводе является случайной функцией времени, поэтому появляется погрешность, определяемая продолжительностью процедуры пробоотбора. Наконец, измеряемая плотность уже через 5…10 минут может существенно измениться. Если бы мы захотели оценить суммарную погрешность кружечного замера, нам потребовалось бы сравнить этот замер с истинной плотностью в данный момент времени. Но поскольку истинная плотность в реальных производственных условиях неизвестна, то неизвестна и погрешность рассматриваемого метода.
Анализ известных плотномеров
Многие известные автоматические плотномеры, существенно отличающиеся друг от друга по конструктивным признакам, реализуют методы измерения, которые являются аналогами метода кружечных замеров плотности. Такими плотномерами являются гидростатические с одной и двумя трубками, весовые, поплавковые (буйковые), вакуумметрические и др.
Гидростатический плотномер с одной трубкой показан на рис. 1. В контролируемую жидкость 1 погружена на некоторую заданную глубину h открытая снизу трубка 2. Если соединить трубку с источником 3 сжатого воздуха и манометром 4, то из нижнего конца трубки начнут выходить пузырьки воздуха, а манометр покажет давление воздуха P, равное произведению удельного веса γ жидкости на глубину h:
Р = γ h.
Это давление называется гидростатическим [1]. В данной формуле если γ имеет размерность кгс/л, а уровень – мм, то давление будет выражаться в мм вод. ст. Следует заметить, что плотность кг/л и удельный вес кгс/л в условиях земного тяготения численно равны; по этой причине при расчётах, связанных с гидростатическим давлением и взвешиванием, удобнее оперировать понятием удельного веса жидкости вместо плотности.
Из этого основополагающего уравнения гидростатики можно определить удельный вес как отношение P/h. Если числитель и знаменатель данного отношения умножить на сечение отверстия трубки S, удельный вес жидкости будет определён как отношение веса жидкости к её объёму.
При кружечном замере плотности тоже делят вес пульпы на её объём.
Недостаток гидростатического плотномера с одной трубкой состоит в том, что в процессе измерения уровень h в технологической ёмкости может колебаться и даже небольшие изменения уровня могут вызвать недопустимую погрешность.
Данный недостаток не распространяется на гидростатический плотномер с двумя трубками, показанный на рис. 2. В этом плотномере трубки установлены на разной высоте от днища ёмкости. Расстояние между нижними концами трубок ∆h = const. Верхние торцы трубок снабжены штуцерами для подключения к дифференциальному манометру, который измеряет разность давлений ∆Р в трубках. Нетрудно доказать, что в этом случае
а колебания уровня жидкости не оказывают влияния на точность измерения [2, 3, 4]. При этом имеет место гидростатическое взвешивание объёма жидкости, заключённой между двумя горизонтальными плоскостями, проведёнными через нижние концы трубок.
Недостатки плотномера с двумя трубками заключаются в том, что верхняя трубка может оголяться при колебаниях уровня, а нижняя трубка не должна устанавливаться в придонной области, так как рудные пульпы забивают её песком. Эти негативные факторы вынуждают уменьшать ∆h, что снижает точность измерения.
Весовой плотномер показан на рис. 3. Работа весового плотномера основана на непрерывном взвешивании участка трубы 1, заполненного жидкостью. Один конец трубы с помощью гибкого шланга 2 подключён к ёмкости с контролируемой жидкостью 3. Сливной конец соединён с весоизмерительным устройством 4. Здесь также делят вес жидкости на её объём в трубе, который остаётся неизменным в процессе измерения [2, 3, 4].
Недостаток весового плотномера состоит в том, что конец трубы, соединённый с гибким шлангом, не позволяет с высокой точностью определить вес пульпы. Кроме того, труба изнутри обрастает твёрдыми отложениями, что искажает результаты измерения веса пульпы и изначально зафиксированный объём внутри трубы. Помимо этого не всегда можно найти подходящее место для слива пульпы, прошедшей через прибор.
Поплавковый плотномер показан на рис. 4. Поплавок 1 полностью погружён в контролируемую жидкость. На поплавок действует выталкивающая сила, которая, как известно, равна весу жидкости, вытесненной им. Зная показание весоизмерителя 2 и объём поплавка, определяют удельный вес жидкости.
Недостатки поплавкового плотномера состоят в том, что твёрдые частицы пульпы, налипая на поплавок, увеличивают погрешность измерения. Надёжность работы таких плотномеров невелика.
Вакуумметрический плотномер показан на рис. 5. Открытый конец трубки 1 погружён в контролируемую жидкость, а другой конец подключён к источнику 2 заданного отрицательного (вакуумметрического) давления (разрежения). Датчик 3 измеряет величину заданного разрежения Р_. Можно доказать, что Р_= γ×h. Чем больше величина Р_ , тем на большую высоту h над уровнем жидкости в ёмкости 4 поднимается жидкость в трубке 1. Чем больше γ, тем на меньшую высоту поднимается жидкость. И в этом случае γ есть результат деления веса столба жидкости высотой h на объём этого столба [1].
Недостатки вакуумметрического плотномера связаны с тем, что это прибор периодического действия. Кроме того, он нуждается в источнике вакуумметрического давления. В то же время следует подчеркнуть, что он может работать при сравнительно невысоком уровне H жидкости в ёмкости и показания прибора не зависят от колебаний этого уровня.
Описание разработанной системы автоматического контроля плотности пульпы
ООО «ASU Technology» (г. Алмалык) разработало и внедрило систему автоматического контроля плотности пульпы, выгодно отличающуюся от рассмотренных решений по точности измерения и надёжности в работе. Задача состояла в том, что нужно было непрерывно и автоматически измерять плотность слива гидроциклонов второй стадии измельчения руды. Слив направляется в коробку объёмом 1,5 м3, а из неё – самотёком на флотацию. Эта коробка с пульпой представлялась авторам как «большая кружка» переменного объёма с пульпой переменной плотности. Задача решалась методами современных компьютерных технологий с применением новейших датчиков контроля физических параметров пульпы: уровня h пульпы в ёмкости и гидростатического давления Р [5]. Следует добавить, что контролируемая системой пульпа характеризуется негативными особенностями: открытой волнообразной поверхностью пульпы в ёмкости и аэрированностью, вызванной мощными струями потоков, входящих в ёмкость сверху и увлекающих за собой воздух. Воздух, диспергированный в объёме пульпы, как известно, для любого типа плотномера является помехой, порождающей дополнительную погрешность измерения.
Принципы построения системы
На рис. 6 показана установка датчиков системы.
Датчик 1 гидростатического давления Р выполнен в виде открытой снизу трубы, установленной в приёмную коробку 2 слива гидроциклона 3 с зазором 60 мм от днища коробки. Верхний торец трубы герметично закрыт. Импульсная трубка 4 соединяет внутреннюю полость трубы с преобразователем давления, размещённым в шкафу КИП (5). Пузырьки воздуха, присутствующие в пульпе, поступают в трубу снизу и вытесняют из неё пульпу. Труба полностью заполнена воздухом. Давление воздуха равно гидростатическому давлению пульпы на нижний срез трубы. Это давление Р равно γ×h. Если концентрация воздуха в пульпе небольшая, трубку подпитывают от источника сжатого воздуха. В нашем случае воздуха в пульпе достаточно, чтобы непрерывно поддерживать занятый воздухом объём. Первоначальное заполнение трубы воздухом, если она была заполнена пульпой, происходит приблизительно за 3 минуты.
Ультразвуковой уровнемер 6 типа PROBE (Siemens Milltronics) установлен над ёмкостью и настроен на измерение уровня пульпы h, отсчитываемого от нижнего среза трубы 1 (от оси 0-0). Токовый сигнал уровнемера (4…20 мА) поступает в шкаф КИП (5).
Шкаф КИП
Внешний вид приборов шкафа КИП можно видеть на рис. 7.
Шкаф КИП содержит преобразователь датчика гидростатического давления РМС 131 (Endress+Hauser), модули аналогового ввода ADAM-4017 и микроконтроллера ADAM-4501, выпускаемые фирмой Advantech, блок питания DPP50-24 компании Lambda с выходным номиналом 24 В.
Блок-схема локального контроллера, образуемого перечисленными модулями ADAM с источником питания, приведена на рис. 8. К модулю аналогового ввода подключены токовые сигналы 4…20 мА от датчиков уровня и давления. От контроллера по интерфейсу RS-485 (или через Ethernet – вид связи зависит от расстояния) цифровой сигнал плотности поступает в компьютер АРМ оператора, на видеоустройстве которого средствами пакета GENESIS32 плотность визуализируется в виде числового значения, размещаемого на мнемосхеме гидроциклона.
Одновременно строится график изменения плотности во времени, на рис. 9 показан фрагмент этого графика.
Вывод расчётной формулы для γ
Казалось бы, расчётная формула очень проста: γ = P/h.
Однако она справедлива лишь в случае, если пульпа двухфазная (твёрдое+ жидкое). В нашем случае, как практически и всегда, промышленные пульпы в той или иной степени аэрированы, а следовательно, они трёхфазные (твёрдое+жидкое+газ).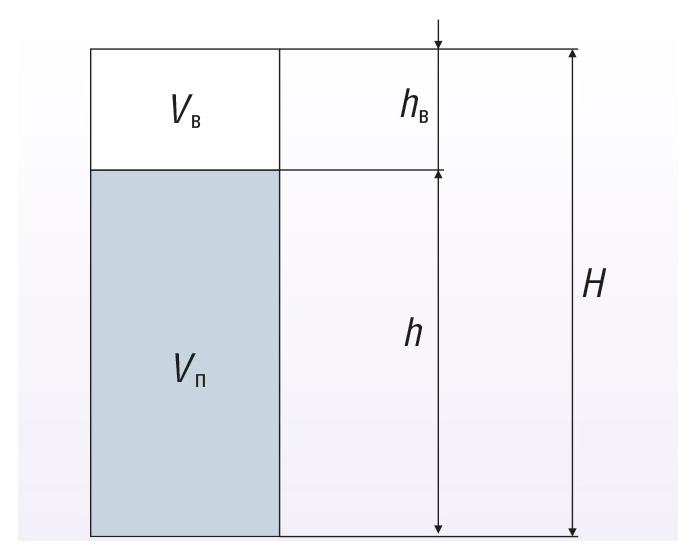
Обратимся к рис. 10, чтобы вывести формулу γ для трёхфазной пульпы. Допустим, мы наполнили сосуд аэрированной пульпой до верхнего края. Через некоторое время пузырьки газа улетучатся, и в сосуде останется деаэрированная пульпа. Пусть объём деаэрированной пульпы будет Vп. Тогда суммарный объём пузырьков будет Vв. Объёмная концентрация воздуха в пульпе, выраженная в долях единицы, будет равна:
Разделим числитель и знаменатель этого выражения на величину сечения сосуда. От деления Vп и Vв на величину сечения сосуда получим, соответственно, h – уровень деаэрированной пульпы в сосуде и hв – уровень воздуха. С учётом этого, а также обозначения уровня аэрированной пульпы как Н приведём выражение к следующему виду:
Отсюда h = H(1 – С). Действительно, при С = 0 имеем h = Н, а при С = 1 получим h = 0.
Таким образом, для трёхфазной пульпы расчётная формула будет такой:
Программирование
Программа системы написана на языке высокого уровня C++. Для связи с компьютером верхнего уровня (компьютером АРМ) используется протокол Modbus RTU.
Входные аналоговые сигналы, получаемые 50 раз в секунду, преобразуются в соответствующие им значения давления, измеряемые в мм вод. ст., и уровня – мм, фильтруются фильтром низких частот и сглаживаются методом скользящего среднего. Полученные средние значения за последние 4 секунды участвуют в расчёте текущей плотности пульпы, и к рассчитанному значению плотности опять применяется метод скользящего среднего. Полученное среднее значение плотности за последние 8–10 секунд передаётся для визуализации и архивирования в компьютер верхнего уровня.
В компьютере верхнего уровня используется Fastwel Modbus OPC Server для организации публикации текущих данных в локальной сети предприятия.
Для архивирования используется программа GENESIS32 TrendWorХ (компания Iconics). Получаемые значения плотности, уровня в технологической ёмкости и давления усредняются и записываются в базу данных 1 раз в 10 минут.
Оценка погрешности измерений
При значительном содержании воздуха в пульпе потребуется концентратомер и задача определения плотности деаэрированной пульпы станет проблематичной. В нашем случае концентратомера не было. С целью определения значения концентрации воздуха (C) для расчётной формулы были проведены исследования: отбирались пробы пульпы кружечным методом и одновременно средствами разработанной системы измерялись сигналы Р и Н. По результатам 118 измерений, выполненных в течение одной недели, было установлено среднее значение –С = 0,17.
Поскольку разброс значений концентраций относительно –С был небольшим, стало возможным принять расчётную формулу:
При кружечных измерениях взвешивается деаэрированная пульпа, поэтому в каждом измерении определялась концентрация С из формулы (1), в которой вместо γ подставлялся результат кружечного замера.
После определения среднего значения концентрации –С по результатам кружечных замеров и ввода этого значения в формулу для γ система выдаёт вычисленные значения плотности. При эпизодических проверках эти значения сравниваются с результатами кружечных замеров γк.
Естественно, что имеет место расхождение значений плотностей γ и γк, которое обусловлено случайными отклонениями текущих значений С от –С. Это расхождение значений плотностей является случайной величиной, характеризующейся дисперсией и средним квадратическим отклонением σ [6].
Наиболее точную оценку σ можно получить по результатам всё тех же 118 измерений, в ходе которых параллельно с каждым i-м кружечным замером (γкi) проводились измерения Pi и Hi средствами разработанной системы. На основе полученных значений Pi и Hi, а также принятого среднего значения концентрации воздуха –С по формуле (1) вычисляются значения γi, соответствующие показаниям системы, и подставляются в следующую формулу:
В результате вычислений было получено значение σ порядка 21 г/л. Такая ошибка в определении γ вполне допустима.
Начиная с декабря 2007 года и по настоящее время нами и фабрикой многократно и независимо проводились проверки системы с помощью кружечных замеров. Выводы: отклонения близки к 21 г/л, система работает удовлетворительно и по точности измерений, и по показателям эксплуатационной надёжности. В ходе эксплуатации установлен диапазон измерения плотности от 0,85 кг/л (аэрированная вода без руды) до 1,65 кг/л (соответствует нарушению технологии). Приведённая к данному диапазону среднеквадратическая погрешность измерения размером 21 г/л составляет всего 2,6%.
Заключение
Разработана, испытана и внедрена система автоматического контроля плотности продуктов измельчения и флотации руд.
Система разработана с применением современных технических средств и компьютерных технологий, отличается достаточной точностью измерения при простоте конструкции и высокой надёжности работы в тяжёлых условиях промышленной эксплуатации.
Получена формула для расчёта плотности трёхфазной пульпы, которая позволит создать систему для автоматического контроля как двухфазных, так и трёхфазных пульп. ●
Литература
-
Цыбин Л.А., Шанаев И.Ф. Гидравлика и насосы. – М. : Высшая школа, 1978. – С. 10–17.
-
Козин В.З., Троп А.Е., Комаров А.Я. Автоматизация производственных процессов на обогатительных фабриках. – М. : Недра, 1980. – С. 228–230.
-
Хан Г.А., Картушин В.П., Сорокер Л.В., Скрипчак Д.А. Автоматизация обогатительных фабрик. – М. : Недра, 1974. – С. 36–40.
-
Хан Г.А. Опробование и контроль технологических процессов обогащения. – М. : Недра, 1979. – С. 133–136.
-
Никитин А.В., Скрипчак Д.А., Семёнов М.А., Хан И.С., Заманов Г.С. АСУ ТП медно-молибденового участка медной обогатительной фабрики Алмалыкского ГМК // Современные технологии автоматизации. 2007. № 1. С. 30–36.
-
Вентцель Е.С. Теория вероятностей. – М. : Наука, 1969. – С. 377–385.
Авторы – сотрудники ООО «ASU Teсhnology»
Телефон: (+9987061) 484-95
E-mail: zamdir@asutechnology.uz
Если вам понравился материал, кликните значок - вы поможете нам узнать, каким статьям и новостям следует отдавать предпочтение. Если вы хотите обсудить материал - не стесняйтесь оставлять свои комментарии : возможно, они будут полезны другим нашим читателям!