Потребитель постоянно повышает требования к качеству желаемой продукции. Развитое общество повышает требования к качеству жизни. Производство развитых стран ужесточает требования к безопасности технологических процессов, причём крайне желательно ещё и одновременное снижение издержек производства. Как выполнить все эти требования? Каким образом создать условия для достойной жизни общества? Возможно, ответ на этот сложный вопрос лежит в сфере гибкого автоматизированного промышленного производства. К сфере промышленного производства, конечно, уже давно относятся и сельское хозяйство, и транспорт, и связь, и строительство.
Автоматизированное производство год от года повышает требования к точности контролируемых параметров, к стабильности и повторяемости параметров технологического процесса. В каких производствах были наилучшие геометрические точности, скажем, в XVIII – начале XIX века? Возможно, наиболее точные производства того времени были в ручном часовом ремесле, граничившем с искусством, в изготовлении ткацких станков и стрелкового оружия. Какого порядка были эти технологические (геометрические) точности? Вряд ли точнее 0,1 миллиметра.
А какие геометрические точности достигнуты сейчас, в начале XXI века, скажем, в производстве сверхбольших интегральных схем? Достигнуты точности 0,05…0,1 микрометра и лучше. Кажется, это не предел. Таким образом, за три века геометрические технологические точности возросли на три порядка. Этот пример иллюстрирует, как тесно связан уровень технологий с точностью массового производства. Отсюда, из технологичности и точности, получены доступность современных товаров, современное качество жизни.
Не во всех производствах начала XXI века требуются точности в десятые и сотые доли микрона. В сельском хозяйстве, производстве продуктов питания, в строительстве, производстве стройматериалов вполне достаточно точности 0,1 мм. В высокоскоростном транспорте, автомобилестроении, машиностроении, металлообработке уже требуются лучшие точности, порядка 0,01–0,001 мм. Кроме точности, конечно, значение имеют и диапазон измерений, их простота и надёжность и многие другие параметры измерительных устройств, датчиков.
Для сокращения издержек автоматизированного (читай: почти безлюдного) производства весьма важны цена, срок службы измерительных устройств, датчиков, контролирующих технологические параметры.
Контроль длин, перемещений, габаритов, пройденного пути, дистанции до объекта, безопасного расстояния, контроль крайних положений в пространстве и т.д., то есть, в конечном счёте, контроль за движением является одной из самых важных и часто встречающихся задач автоматизации. Эти задачи автоматизации имеют практическое значение на любом современном производстве, поскольку с контролем расстояний связаны качество выпускаемой продукции, безопасность техпроцесса для персонала и окружающей среды.
Для решения задач контроля расстояния и движения компания Pepperl+Fuchs предлагает устройства для самых разных производств, точностей и условий окружающей среды.
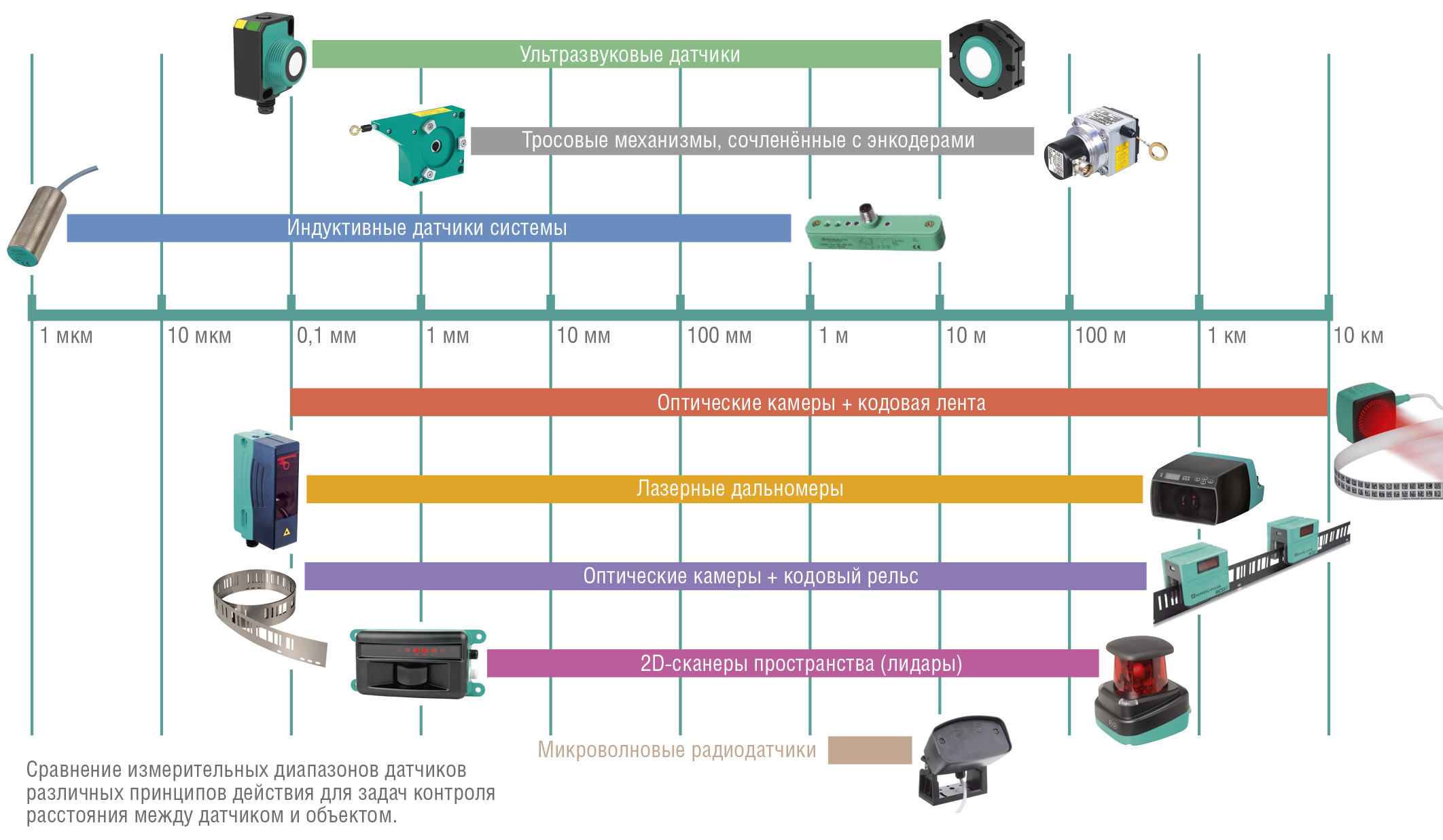
Совокупные возможности датчиков и систем компании Pepperl+Fuchs для контроля за движением показаны на рис. 1. С помощью датчиков компании можно контролировать зазоры, габариты, дистанции, расстояния от единиц микрон до десяти километров. Этот диапазон изображён на логарифмической шкале в центре рисунка, от 1 мкм до 10 км, что составляет 10 (!) порядков. Датчики работают на различных принципах действия, каждая группа датчиков имеет свои конструктивные особенности, свои достоинства и недостатки, которые определяют, в свою очередь, возможные применения.
Ультразвуковые датчики
Ультразвуковые датчики, или, в нашем случае, ультразвуковые датчики приближения измеряют дистанции эхолокационным методом. Чаще всего ультразвуковой излучатель и ультразвуковой приёмник расположены в одном корпусе (хотя у компании существуют и иные конструкции). Пьезоэлектрический излучатель создаёт ультразвуковой луч в направлении объекта. В качестве объектов могут выступать твёрдые и жидкие материалы достаточных размеров. Луч, достигнув объекта, отражается от него в направлении датчика. Пьезоэлектрический приёмник улавливает отражённый от объекта луч. Электронный преобразователь датчика измеряет время, затраченное лучом на движение в сторону объекта и назад. По известной скорости распространения ультразвукового луча в воздушной среде преобразователь датчика вычисляет дистанцию от датчика до объекта.
Разрешение ультразвуковых датчиков и их рабочие дистанции таковы, что ультразвуковые датчики компании работают в диапазонах расстояний от десятых долей миллиметра до 10 метров.
С выхода ультразвукового датчика снимается аналоговый сигнал или сигнал иного стандарта о расстоянии до объекта.
Важные достоинства ультразвуковых датчиков:
- распространению ультразвукового сигнала (а, значит, и обнаружению объекта) не препятствует воздушная среда с большим содержанием пыли, иных взвешенных частиц в воздухе. Ультразвуковой датчик, как правило, работоспособен в непрозрачной воздушной среде, работоспособен там, где любой оптический датчик уже не сможет работать;
- ультразвуковой луч (сигнал) хорошо отражается как от твёрдых, так и от жидких поверхностей, причём не имеют значения цветность, прозрачность и шероховатость отражательной поверхности объекта;
- если сравнить рабочие дистанции двух датчиков, ультразвукового и индуктивного, имеющих примерно одинаковые по размеру корпуса, то рабочие дистанции первого датчика будут в 20–50 раз больше, чем у второго.
Особенности ультразвуковых датчиков:
- датчик имеет определённую диаграмму направленности распространения ультразвукового сигнала – максимальная мощность сигнала излучается вдоль оси излучателя (датчика), значительно меньшая мощность сигнала излучается в направлениях, отличных от оси излучателя. Конструктивными приёмами при производстве датчиков удаётся существенным образом варьировать угол расхождения ультразвукового сигнала: в одних датчиках можно достичь очень узкого угла расхождения сигнала (сигнал будет своеобразным ультразвуковым щупом или указкой), в других датчиках можно получить очень широкий (в десятки градусов) угол расхождения сигнала, в третьих датчиках угол распространения луча может быть настроен пользователем для своей производственной задачи;
- ультразвуковой излучатель датчика вибрирует и не только на ультразвуковой частоте; это способствует самоочищению, некоторому стряхиванию пыли с приёмоизлучающей поверхности датчика;
- обычно ультразвуковые датчики работают на частотах от десятков до сотен килогерц. В силу физики процесса скорость распространения ультразвукового сигнала в воздушной среде не слишком велика, и должен быть период ожидания для приёма отражённого от объекта сигнала. По этим причинам удаётся достичь быстродействия ультразвуковых датчиков не лучше, чем десятки-сотни миллисекунд. Для контроля многих производственных технологических процессов этого вполне достаточно. Однако для некоторых быстротекущих процессов, для оперативных измерений указанного быстродействия может недоставать;
- по причине более сложной конструкции приёмопередающего узла ультразвукового датчика, чем, например, у индуктивного датчика, пока ультразвуковые датчики сто́ят заметно дороже индуктивных. Однако технологии ультразвуковых датчиков постоянно совершенствуются, растут объёмы их производства, и существуют прогнозы, по которым цены на эти датчики в течение 5–10 лет должны приблизиться к ценам индуктивных датчиков.
Некоторые ультразвуковые датчики компании Pepperl+Fuchs показаны на рис. 2, 3, 4 вместе с основными техническими характеристиками.
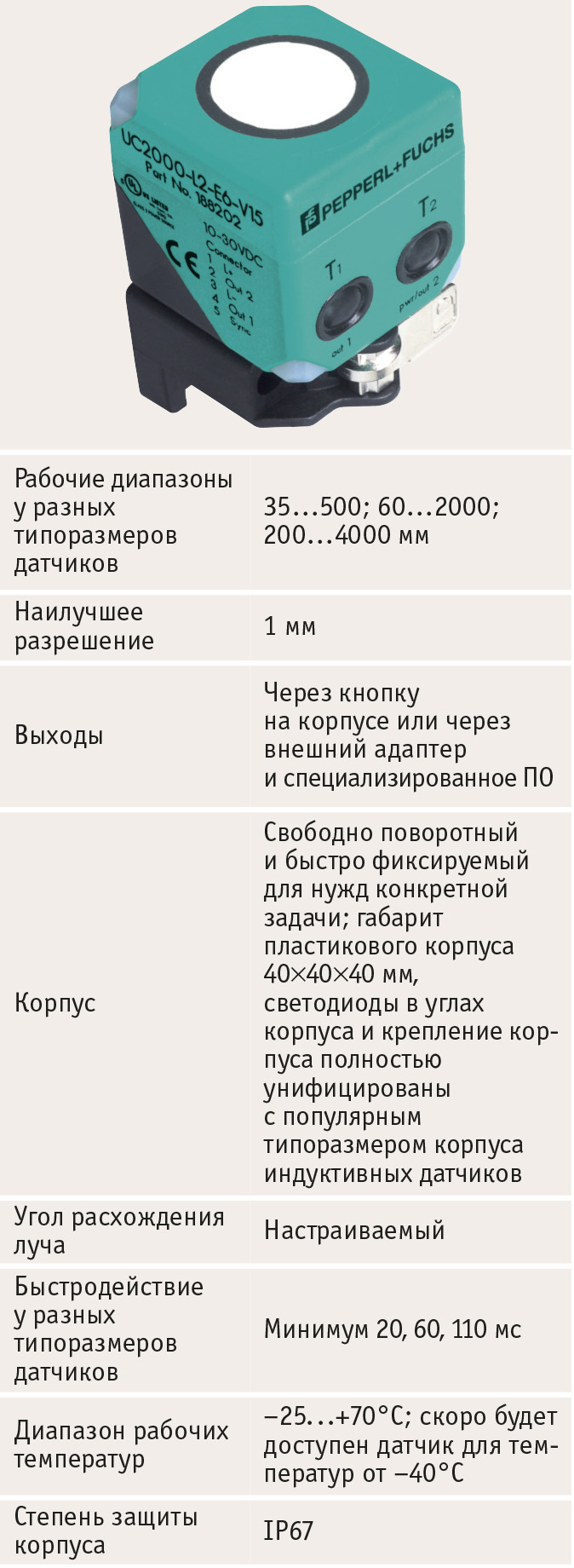
Некоторые применения ультразвуковых датчиков компании показаны на рис. 5, 6, 7, 8.
Тросовые механизмы, механически сочленяемые с энкодерами (датчиками угла поворота вала)
Тросовый механизм представляет собой подпружиненный барабан. На барабан наматывается в один слой относительно тонкий стальной трос. За счёт подпружиненного барабана для вытягивания (разматывания) троса требуется некоторое незначительное усилие, преодолевающее усилие пружины, а для наматывания троса усилия не требуются, трос наматывается на барабан сам за счёт встроенного пружинного механизма барабана. Таким образом, поступательные (линейные) перемещения наконечника троса механизм преобразует во вращения барабана. Если тросовый механизм сочленить с энкодером, то этим энкодером можно измерить вращение барабана, которое механически связано (с хорошей точностью прямо пропорционально) с поступательным движением наконечника троса.
Качество изготовления механических деталей, упругие свойства стального троса, длины тросов таковы, что пристыкованным энкодером можно измерить поступательные движения троса в диапазонах от десятых долей миллиметра до 60 метров. В свою очередь, энкодеры компании Pepperl+Fuchs поставляются работающими практически со всеми промышленными интерфейсами, в том числе с повсеместно распространённым аналоговым.
Для заказа доступны как отдельные тросовые механизмы, так и тросовые механизмы, сочленённые на заводе-изготовителе с энкодерами.
Достоинства тросовых механизмов: в устройствах применяется простой, понятный, визуально контролируемый способ преобразования линейного движения наконечника троса во вращение вала. Затем вращение вала измеряется энкодером. Надёжность такого способа измерения линейного движения весьма высока, но имеются особенности, продиктованные конструкцией узла.
Особенности тросовых механизмов:
- вне барабана, то есть в размотанном виде положение горизонтального троса в пространстве сопровождается провисанием троса. Это снижает точность измерений, особенно самых длинных перемещений. По этой причине тросовые механизмы применимы лишь в измерениях средней точности;
- в силу механической инерционности подвижных элементов тросового механизма такое устройство способно контролировать лишь не слишком быстрые перемещения;
- упругий, гибкий, прочный стальной трос – весьма надёжный элемент конструкции, он является составной частью измерительной системы.
Однако в тяжёлых производственных условиях потребуется контролировать его исправность, по крайне мере визуально, а также необходимо содержать трос в достаточно чистом виде. Примеры тросовых механизмов вместе с их основными техническими характеристиками показаны на рис. 9 и 10.
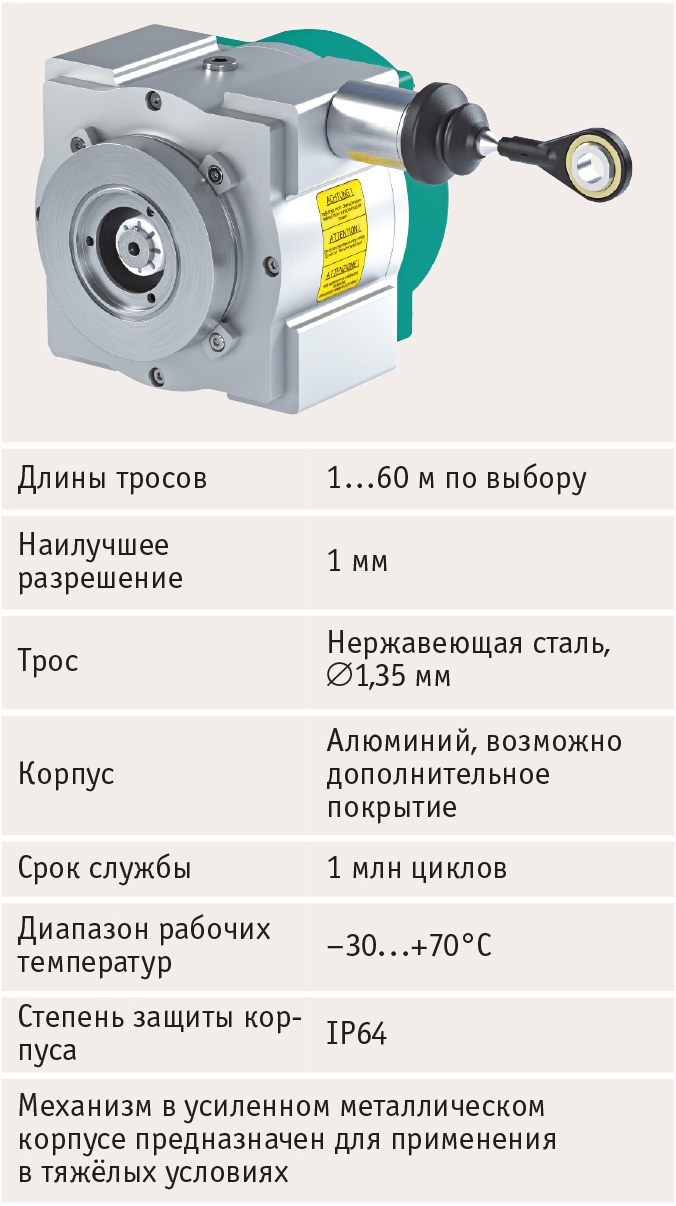
Примеры тросовых механизмов, сочленённых с энкодерами, показаны на рис. 11.
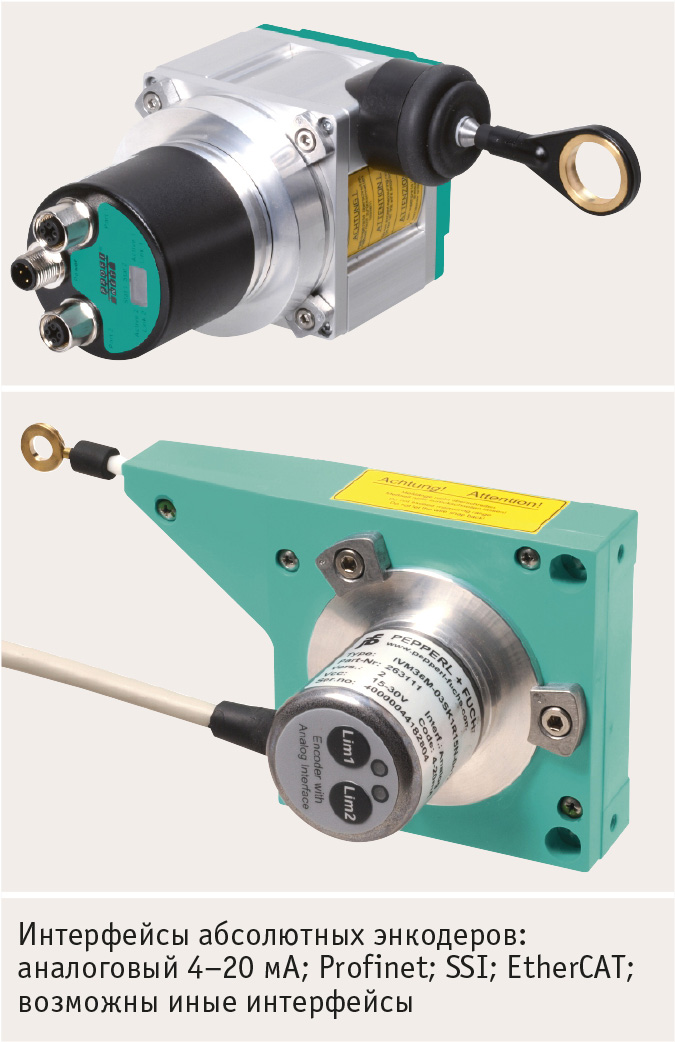
Применение тросового механизма для контроля перемещений механизмов на буровой установке проиллюстрировано рис. 12.
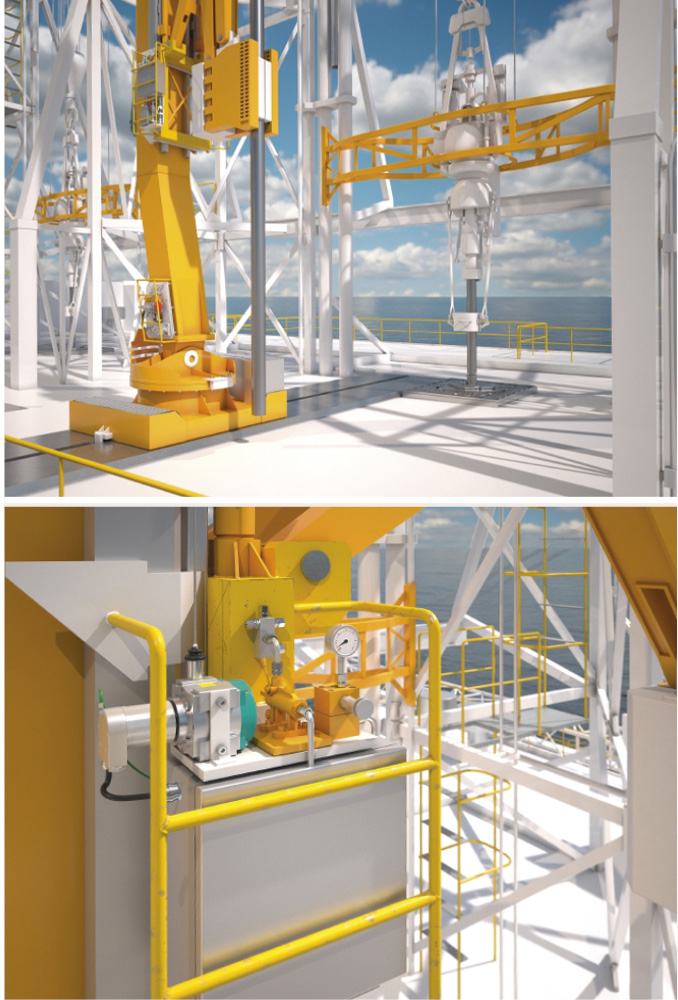
Устройства контроля расстояний иных принципов действия рассматриваются во второй части статьи. ●
Продолжение следует.