Введение
Если не брать в расчёт металлообрабатывающие предприятия, относящиеся к добывающим отраслям (Газпром, Роснефть), то для большинства машиностроительных предприятий приобретение нового крупногабаритного и многофункционального станочного оборудования – задача на сегодняшний день практически недостижимая в связи со значительными затратами на покупку. По результатам обследования состояния парка станков на ряде предприятий Московской, Тульской, Ярославской, Калужской областей выясняется, что известные модификации группы горизонтально-расточных станков, такие как 2А622, 2А656, произведённые в конце 80-х годов прошлого столетия и ещё находящиеся в эксплуатации, отличаются в большинстве случаев достаточно хорошим состоянием кинематических и гидравлических узлов, но имеют практически неработоспособное электрооборудование и средства управления. Учитывая относительно небольшие затраты на модернизацию основного электрооборудования, отсчётно-измерительной системы и средств управления (не более 3 млн руб.), а также довольно короткий срок периода модернизации (в пределах двух месяцев), данное направление работы классически укладывается в тренд современных направлений по общей модернизации производства в России.Описание объекта модернизации
Горизонтально-расточные станки с подвижной передней стойкой и встроенным поворотным столом, имеющим продольное и поперечное перемещение, с навесной планшайбой и радиальным суппортом предназначены в основном для обработки крупных корпусных деталей. Универсальность станка и широкие функциональные возможности предопределяют наличие значительного спектра электротехнических устройств, обеспечивающих управление подвижными органами, визуализацию процесса обработки, реализацию предохранительных функций и технологических блокировок. Основными элементами электрооборудования станка являются шкаф управления (рис. 1) с двухсторонним обслуживанием и приводные электродвигатели.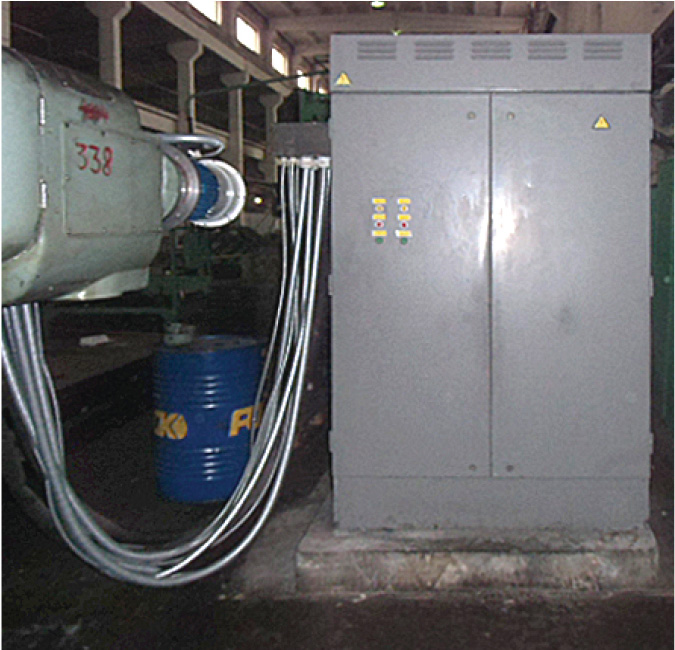
В целях наглядности и оценки функциональных связей всего электротехнического комплекса станка на рис. 2 показана структура электрооборудования и средств управления горизонтально-расточного станка 2А656РФ11 после проведения модернизации.
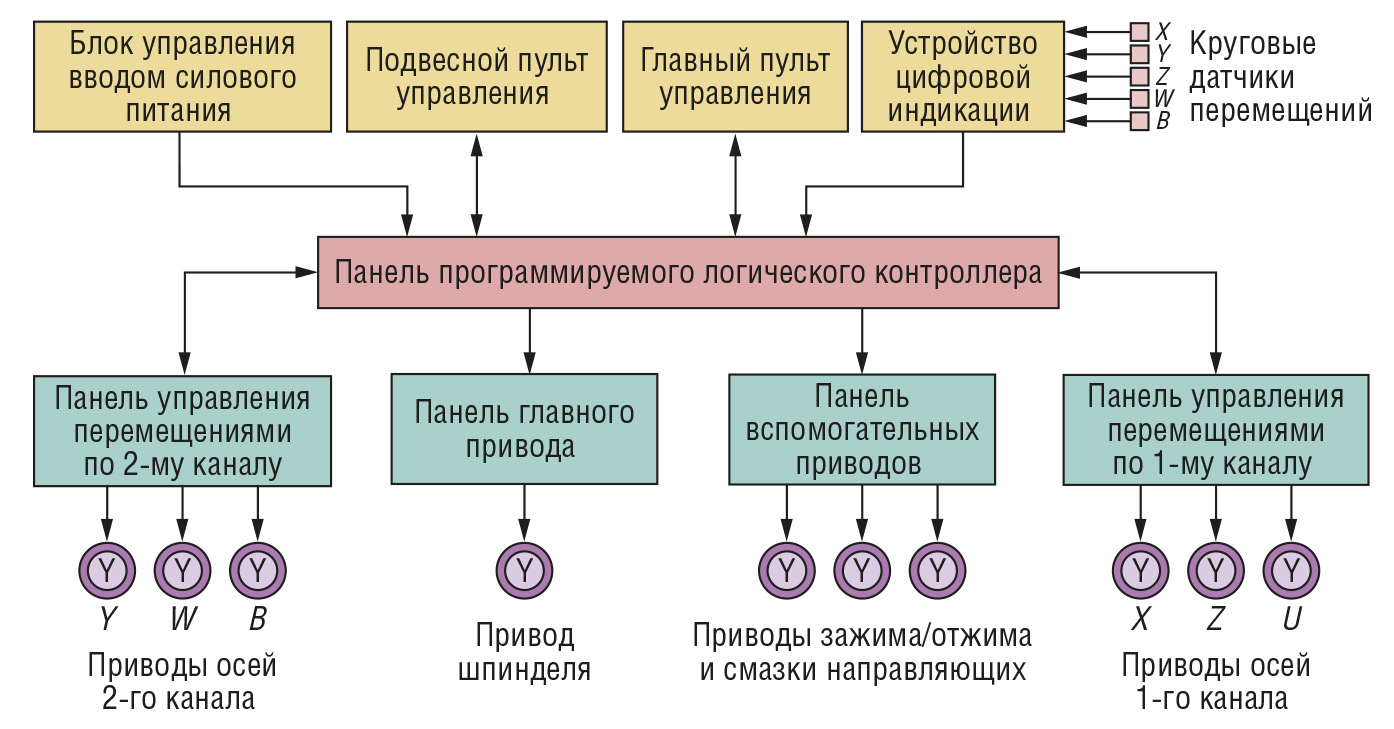
Условные обозначения: ось Х – поперечное перемещение стойки; ось Y – вертикальное перемещение шпиндельной бабки; ось Z – перемещение шпинделя; ось W – перемещение стола продольно; ось U – координата выдвигаемой пиноли; ось B – круговое вращение стола.
Основной перечень работ по модернизации включает:- замену по всем осям (X, Y, Z, W, U, B) приводных электродвигателей постоянного тока на специальные асинхронные электродвигатели с независимой системой вентиляции и энкодерами; работа сопровождалась созданием конструкции переходных фланцев для механического сопряжения вновь устанавливаемых приводных электродвигателей на штатные посадочные места;
- установку отсчётно-измерительной системы с реализацией функций контроля перемещения и программно-позиционного управления;
- полную модернизацию внутренних панелей шкафа управления с заменой практически всей элементной базы (программируемый логический контроллер вместо двух релейных блоков, преобразователи частоты взамен тиристорных преобразователей, бесконтактная коммутационная аппаратура для управления переключением скоростей шпинделя и т.д.);
- восстановление оборудования главного и подвесного пультов управления (задатчики установочных и рабочих перемещений, элементы индикации режимов работы и выбора осей);
- замену элементов отжима и контроля отжима осей X, Y, концевых выключателей ограничения перемещений и технологических блокировок, системы обеспечения смазки направляющих и т.д.
Использованные программно-аппаратные средства управления и электропривода
При проведении модернизации была применена элементная база, которая широко применяется на территории Российской Федерации и поддерживается поставками развитой дистрибьютерской сети, а также характеризуется высоким качеством и эксплуатационной надёжностью.Приводная система выполнена на основе высокопроизводительных преобразователей частоты серии А1000 (Omron). В частности, в этом проекте использовано два комплектных частотно-регулируемых электропривода (ЧРП) мощностью 11 кВт, по одному на каждый канал (рис. 2), состоящих из преобразователя частоты CIMR-AC4A0031FAA и электродвигателей АДЧР132М2У3-1М3001-1-ТО2500-В3. Внешний вид встраиваемой в шкаф панели управления перемещением по первому и второму каналам представлен на рис. 3.
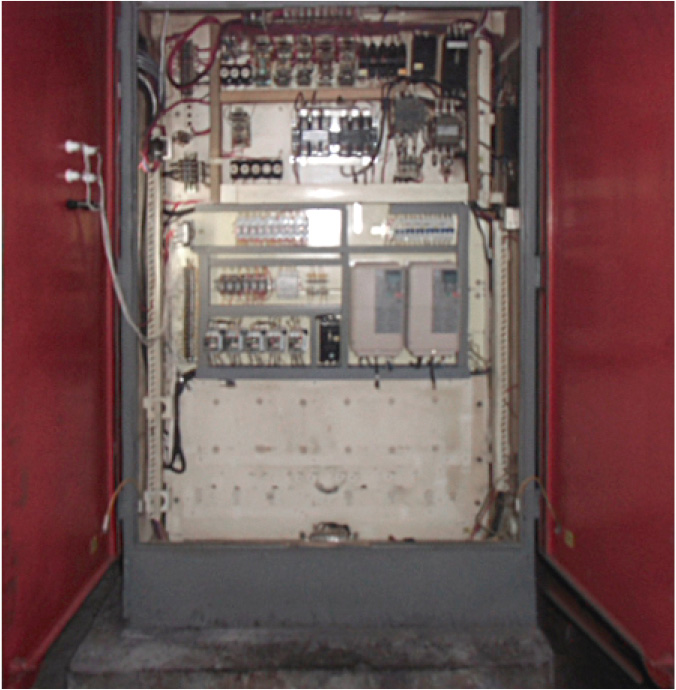
Панель программируемого логического контроллера (ПЛК) собрана на базе универсального промышленного контроллера S7-300 фирмы SIEMENS (рис. 4) и твердотельных реле Omron G3NA-D210B (рис. 5), которые обеспечивают связь модулей дискретного вывода с электроавтоматикой станка, в частности, с исполнительными устройствами (электромагнитными муфтами) распределения и подключения выбранных осей соответствующего канала к частотно-регулируемому электроприводу.
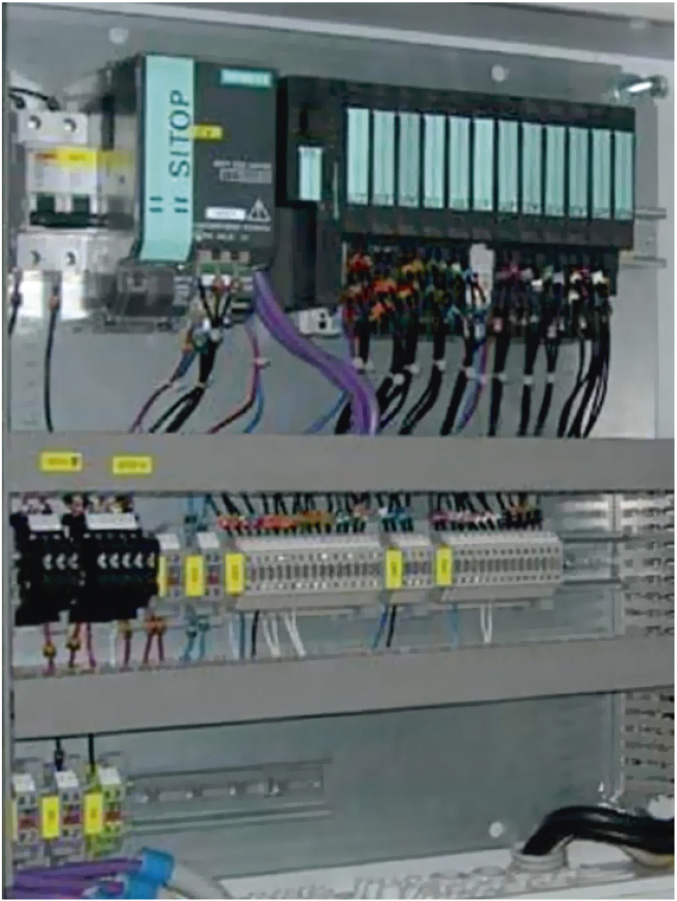
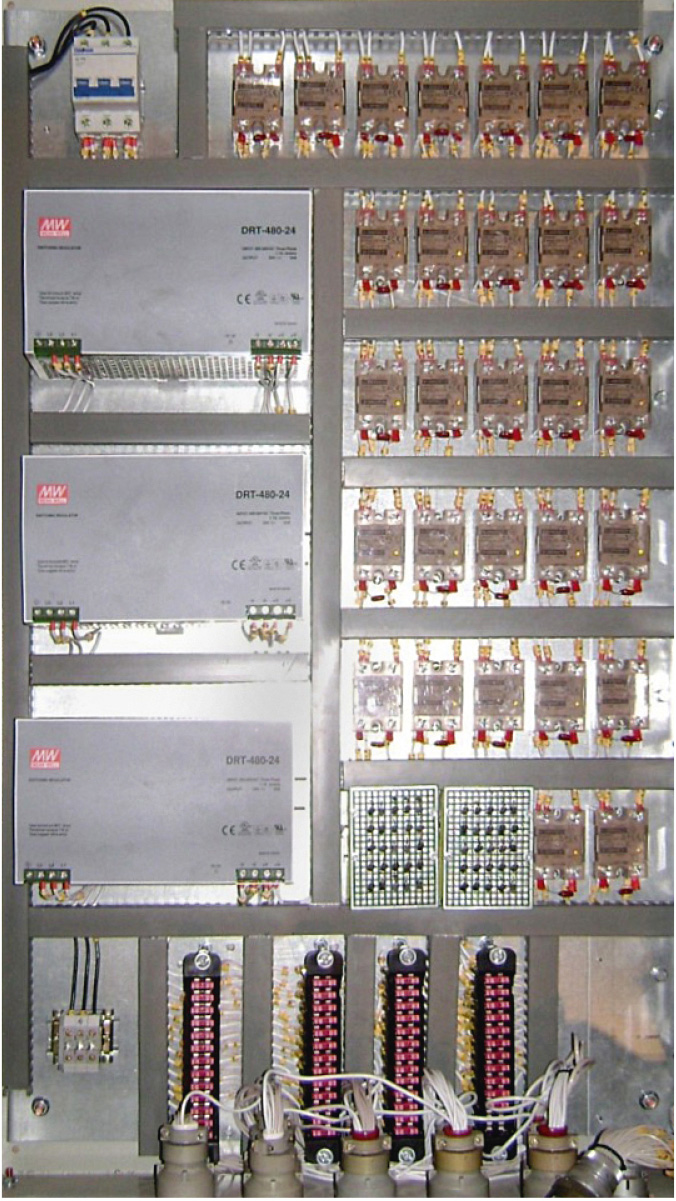
Конструктивно панель выполнена в виде двух отдельных блоков, которые устанавливаются на противоположной от панели управления перемещениями стороне шкафа (рис. 3). Выбор основной элементной базы вызван необходимостью обеспечения бесперебойной работы оборудования в связи со значительной загрузкой станка (16 часов работы в сутки с перерывом 1…1,5 часа), а также наличием потенциальной возможности приобретения при необходимости замены. Разработка и отладка управляющей программы производилась с помощью инструментальной среды SIMATIC STEP 7 Basic на языке LAD-диаграммы.
Следует упомянуть об устройстве цифровой индикации (УЦИ), обеспечивающей совместно с ЧРП выполнение таких функций, как:
- поддержка трёх систем отсчёта для каждой оси (абсолютной, относительной, оперативной), делающих станок с позиций оператора «зрячим»;
- ввод параметров управления движением по трём осям: X, Y, Z (координаты референтной метки, значений пяти уставок торможения, значений компенсаций люфта и систематической погрешности);
- позиционирование с выходом на заданную координату раздельно по каждой оси.
Краткое описание функционирования системы управления станком
Как уже упоминалось, органом управления и координации работы всех агрегатов станка является панель ПЛК. В отличие от заводской системы управления модернизированный вариант позволяет:- повысить возможности диагностики и определения состояния всех без исключения элементов управления, контроля и блокировки, установленных непосредственно на станке, за счёт светодиодной визуализации дискретных входов ПЛК;
- оперативно производить проверку работоспособности исполнительных элементов схемы управления станка (электромагнитных муфт, золотников гидравлической схемы, вспомогательных электроприводов);
- эффективно контролировать функционирование цепей управления частотно-регулируемых электроприводов за счёт встроенных средств визуализации используемых инверторов А1000;
- значительно упростить процедуры настройки, функциональной диагностики и поиска неисправностей в приводных системах, применяя сервисные возможности инверторов А1000;
- снизить время поиска неисправностей в системе электроавтоматики станка за счёт наглядности и упрощения электрической схемы.
Использованные в проекте модернизации УЦИ отечественного производства ЛИР532 для координатных осей X, Y, Z и ЛИР522 для W, U, помимо основных функций, упомянутых ранее, реализуют функцию позиционирования, которая предназначена для перемещения подвижного органа в положение с заданными координатами (координатами позиционирования). Совместно с инициированной командой преобразователя частоты, реализующей фиксированный пробег электродвигателя при торможении от любой начальной частоты до полной остановки, УЦИ инициирует движение к координате позиционирования по каждой оси. При этом запуск функции позиционирования может осуществляться как с клавиатуры УЦИ, так и от внешнего сигнала, сформированного ПЛК панели управления станком.
В дополнение к сказанному с главного пульта управления имеется возможность обнуления текущей координаты с помощью кнопок «сброс» по каждой оси: X, Y, Z, W, B – при работе в относительной системе отсчёта.
Задание скорости перемещения подвижных органов осуществляется раздельно для установочных и рабочих перемещений аналоговым сигналом 0…20 мА, что даёт возможность не менять ранее установленное значение подачи при настроечно-регулировочных перемещениях.
Следует отметить, что несомненным достоинством модернизированной системы управления является применение высокоэффективного частотно-регулируемого электропривода с моделью трансвекторного (FOC – Fied Oriented Control) управления с замкнутым контуром (с датчиком обратной связи). Как уже упоминалось, в качестве инвертора используется преобразователь частоты серии А1000 производства Omron, позволяющий в рамках указанной базовой технологии управления добиваться беспрецедентно высоких характеристик привода подач, таких как:
- пусковой момент 200% от номинального при нулевой скорости;
- точность поддержания момента и скорости в пределах ±0,02%;
- диапазон регулирования 1:1500;
- перегрузка 150% от номинального выходного тока в течение не менее 1 минуты.
- повышения напряжения на шине постоянного тока инвертора;
- понижения напряжения на шине постоянного тока инвертора;
- перегрева тормозного резистора;
- опрокидывания ротора;
- замыкания силовой цепи на землю;
- перегрузки электродвигателя и преобразователя частоты;
- перегрева радиатора преобразователя частоты.
Заключение
Более чем 8-месячный срок эксплуатации модернизированного горизонтально-расточного станка 2А656РФ11 показал наличие достаточно серьёзного эксплуатационного ресурса и высокую надёжность работы установленного основного электротехнического оборудования. В течение указанного срока не было ни одного отказа по вине частотно-регулируемого электропривода, управляющего программируемого контроллера и устройства индикации. Эксплуатационный персонал в кратчайшее время приобрёл уверенные навыки работы с системой управления, особенно в части оперативного устранения неисправностей в электроавтоматике и вспомогательном электрооборудовании станка, оставшихся в заводском исполнении. ●E-mail: akis_tula@inbox.ru
Если вам понравился материал, кликните значок - вы поможете нам узнать, каким статьям и новостям следует отдавать предпочтение. Если вы хотите обсудить материал - не стесняйтесь оставлять свои комментарии : возможно, они будут полезны другим нашим читателям!